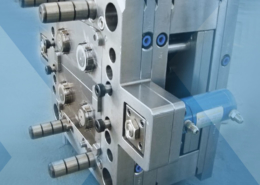
Torlon: Your Next Solution - torlon injection molding
Author:gly Date: 2024-10-15
Injection molding continues to evolve with trends and technologies that drive advancements in the field. These developments aim to improve manufacturing efficiency, enhance performance, and meet the increasing demands of the aerospace industry. The following are some of the most notable innovations:
Instead of manufacturing and assembling multiple components, injection molding can create a single part that performs the functions of several individual pieces. This consolidation simplifies the manufacturing process and reduces the number of features that need to be stocked, managed, and assembled.
Injection molding is highly efficient and automated, making it cost-effective for large-scale production. It minimizes labor costs and material waste since the process generates minimal scrap. It can also produce parts with high dimensional accuracy, reducing the need for secondary machining operations and further saving costs.
This article will explore the impact of aerospace injection molding on the industry. It will specifically highlight the innovative approaches that push the limits of aerospace engineering.
Advanced software allows engineers to simulate mold filling, cooling, and part shrinkage. This assists them in optimizing process parameters and identifying potential problems. Virtual modeling also aids in design validation, allowing for analysis of part performance and design optimization before physical production.
Injection molding is a manufacturing method in which molten material is injected into a mold cavity under high pressure. The material then hardens and takes the mold’s shape, resulting in a finished part. In the aerospace industry, injection molding produces high-quality aircraft and spacecraft parts. Silicone and plastic injection molding applications include interior and exterior structural components, brackets, panels, ducting, connectors, and housings.
ProMed has expertise in working with the full spectrum of silicones covering a wide range of properties and characteristics. We will assist in your material selection to help ensure all design requirements are met. Our manufacturing facilities and equipment are designed for a single purpose—to mold medical and implantable silicone, combination components, and bio-material grade plastics with uncompromising quality and service. We currently have four divisions that are located within two manufacturing sites. All are certified class 10,000 / ISO Class 7 cleanrooms.
Injection molding can achieve rapid production cycles, enabling quick turnaround times for large quantities of parts. It also facilitates rapid prototyping, which allows engineers to validate designs, make iterations, and perform functional tests before proceeding to full-scale production. This accelerates the development cycle and reduces time-to-market.
Aerospace injection molding offers several benefits, making it a preferred manufacturing method in the industry. Here are some of its advantages:
ProMed Molded Products is at the forefront of molding technology, utilizing state-of-the-art equipment and processes that leverage a wide range of materials to deliver superior results! An experienced technical team with deep injection molding expertise backs our commitment to excellence. We specialize in producing small, finely crafted silicone and plastic components.
ProMed was founded in 1989 to address an industry need for cleanroom manufacturing of silicone components, specifically those having a medical application. Over time, we broadened our product offerings to include assembly, micro-molding of highly engineered plastics, and combination products. We have garnered a reputation as the world benchmark of implantable silicone components and assemblies – and are one of few companies in the world to provide contract manufacturing of drug-eluting products. ProMed has expertise in working with the full spectrum of silicones covering a wide range of properties and characteristics. We will assist in your material selection to help ensure all design requirements are met. Our manufacturing facilities and equipment are designed for a single purpose—to mold medical and implantable silicone, combination components, and bio-material grade plastics with uncompromising quality and service. We currently have four divisions that are located within two manufacturing sites. All are certified class 10,000 / ISO Class 7 cleanrooms. We can identify the right manufacturing solution for any project. We have extensive experience in a wide range of injection molding techniques including: Automated Injection Molding Multi-cavity tooling Micro molds and micro molding Servo-controlled de-molding capabilities Insert molds, overmolds, and automation integration Transfer molding Compression molding Click here to see why ProMed is your silicone injection molding partner. Contact ProMed today at 763-331-3800 to discuss your next silicone injection molding project
Safety features guarantee the safety of operators on the hydraulic press. Make sure they are correctly installed before use:
The hydraulic press is equipped with a Jobsite Information Sheet which includes all the information necessary for the use of the machine in good safety conditions. It must be positioned in view of all operators using the hydraulic press.
Chemical variations and additives can expand the utility of silicone to include applications beyond structural components. Fluorosilicone is a variation of silicone that offers greater resistance to fuel, oil, and other harsh chemicals. Aerospace applications such as seals and o-rings for fuel systems take advantage of the unique properties of fluorosilicone. Conductive additives such as carbon black, carbon fiber, and carbon nanotubes can be mixed with silicone and fluorosilicone to facilitate flexible electrical connections, dissipate static charge, or provide electromagnetic shielding. Fluorosilicones and conductive silicones use the same injection molding process as standard material.
The demand for miniaturized components in aerospace applications — such as sensors, connectors, and microfluidic devices — has led to the development of micro-injection molding. This technology enables producing tiny, precise, and intricate parts with dimensions in the micron range. It offers high repeatability, tight tolerances, and the ability to manufacture large volumes of miniature components.
ProMed was founded in 1989 to address an industry need for cleanroom manufacturing of silicone components, specifically those having a medical application. Over time, we broadened our product offerings to include assembly, micro-molding of highly engineered plastics, and combination products. We have garnered a reputation as the world benchmark of implantable silicone components and assemblies – and are one of few companies in the world to provide contract manufacturing of drug-eluting products.
In industry, we often find injection molding systems. This technology is more complex and requires advanced technical knowledge. An injection molding machine allows a high production rate and a precise quality of the produced parts. However, we made the choice of a hydraulic press because it is a machine which is, throughout the world, much more widespread, less expensive; therefore easier to obtain and to use.
The hydraulic press is a machine for shaping the molten plastic coming out of the Extruder or the Sheet oven. The hot viscous plastic material is placed in a mold fixed to the hydraulic press The jacks that compress it are activated and cause the molds to close. The pressurized plastic spreads around the mold until it cools and the plastic sets.
The hydraulic press is equipped with two plates, one is fixed and the other is mobile. Actuated by jacks, the movable plate guided by four columns approaches the fixed plate. The cylinders apply even pressure to the element between the plates. The molds installed on the hydraulic press usually consist of two shells (fixed part and moving part) which are strongly pressed. The pressure exerted by the hydraulic press distributes the hot plastic over the entire footprint of the mold.
Before any use, visually check the mechanical condition. Periodically check the condition of the equipment (see maintenance sheet).
Aircraft and spacecraft rely on interconnected components working together seamlessly. Consistency and reproducibility in injection molding are often achieved through rigorous control of temperature, pressure, cooling rates, and material properties. Once optimized and validated, these parameters can be replicated consistently throughout production.
The hydraulic press that we have on board is equipped with two large plates. These allow us to accommodate large molds, for example to make sheets.
The operators who interact with the hydraulic press must be aware of and respect the information relating to the use of the machine, the risks of using the machine, and the appropriate safety practices.
Why this choice? We have no choice but to add this machine into our production system due to its simplicity of design and use.
Multi-shot injection molding combines different materials to produce a single part in one machining cycle. This process enables the integration of dissimilar materials for enhanced functionality or aesthetic appeal. Overmolding involves molding one material over another component previously made from any compatible material, including silicone, plastic, and metal. This process enables additional properties such as increased grip or vibration dampening.
Click here to see why ProMed is your silicone injection molding partner. Contact ProMed today at 763-331-3800 to discuss your next silicone injection molding project
Preventive and corrective maintenance activities must only be carried out by a person trained for this purpose. Each intervention must be recorded in order to keep a history of the maintenance actions carried out.
Before carrying out any maintenance, adjustment or repair intervention requiring partial or complete dismantling of parts of the shredder, it is necessary to follow these protocols.
Additive manufacturing can create intricate geometries, internal channels, and lattice structures previously challenging to achieve through traditional injection molding methods. It offers greater design freedom and customization options, reducing material waste and lead times. It also allows for the rapid prototyping of complex aerospace components.
A work zone around the machine is defined by a marking on the ground. Access near the machine, whilst it is in operation, is permitted only to trained and equipped operators.
The injection molding process offers outstanding design flexibility, empowering the creation of highly complex shapes and intricate features. This versatility allows designers to integrate multiple functions into a single part, reducing assembly time and enhancing overall efficiency. Additionally, injection molding enables silicone overmolding onto plastic and metal parts, which has numerous applications in the aerospace industry.
We can identify the right manufacturing solution for any project. We have extensive experience in a wide range of injection molding techniques including:
GETTING A QUOTE WITH LK-MOULD IS FREE AND SIMPLE.
FIND MORE OF OUR SERVICES:
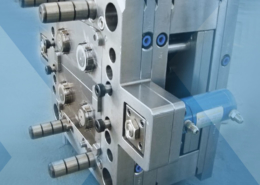
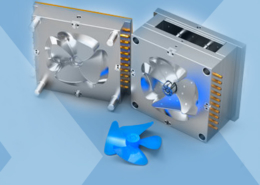
Plastic Molding

Rapid Prototyping
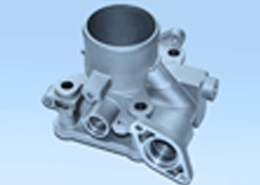
Pressure Die Casting
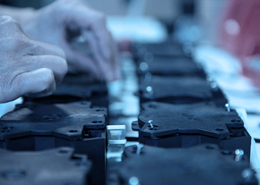
Parts Assembly
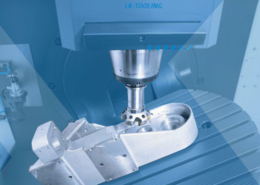