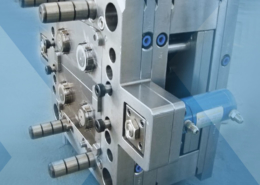
Top Third Party Injection Manufacturers ... - injection manufacturers
Author:gly Date: 2024-10-15
PlasTech Molding Solutions, formerly R.E.C. Manufacturing Corporation, specializes in custom injection molding with over 70 years of experience. Their expert staff, with a combined experience of over 100 years, excels in developing high-performance products, including thin-wall complex geometry applications. The company operates a modern 40,000 square foot facility with multiple clean rooms and a range of injection molding machines. PlasTech Molding Solutions is ISO 9001 certified, ITAR registered, and prioritizes customer service, engineering, production, and quality assurance. They offer a variety of services to meet the needs of both existing businesses and new product development.
Regular maintenance and inspections of injection molding equipment play a significant role in workplace safety. Machines should be routinely checked for signs of wear, damage, or other issues that could lead to malfunctions or accidents. Scheduled maintenance helps ensure that all components are operating correctly and can prevent unexpected breakdowns. Inspection routines should include checking electrical systems, hydraulic lines, and safety guards. By keeping machinery in top condition, we can maintain a safer and more reliable production environment.
Understanding and implementing safety measures in plastic injection molding is crucial for protecting workers and ensuring effective operations. From wearing appropriate PPE to conducting thorough training and maintenance, each step minimizes risks and enhances safety. Keeping these practices in mind helps create a secure environment where everyone can work efficiently and confidently.
Proper handling of materials is another fundamental safety practice. Workers should be trained to move and store raw materials safely to avoid spills and injuries. It’s crucial to follow guidelines for lifting heavy bags of plastic pellets or other materials to prevent back injuries. When dealing with chemicals or additives, using appropriate containers and labeling can help avoid mishandling and accidents. Keeping the work area clean and organized also contributes to a safer environment. Safe handling practices ensure that materials are used efficiently and safely, reducing potential hazards in the workplace.
Proper training and safety drills form the backbone of a safe workplace. Employees should receive comprehensive training on operating machines, handling materials, and following emergency procedures. New hires must be thoroughly educated before beginning their duties, and ongoing training sessions ensure that all staff remain current on safety protocols. Conducting regular safety drills helps reinforce training and prepare employees for real-life emergencies. A well-trained workforce is essential for minimizing risks and maintaining a safe and productive workplace.
Wearing the right personal protective equipment (PPE) is vital in plastic injection molding. Workers should always wear safety glasses to protect their eyes from debris and possible splashes of hot material. Heat-resistant gloves are essential, as they shield hands from high temperatures encountered during the process. Additionally, wearing long sleeves and pants made of non-flammable materials can offer extra protection. Ear protection is also a good idea in noisy environments to prevent hearing damage. Using PPE correctly helps reduce the risk of injuries and keeps workers safe on the job.
Implementing these essential safety tips is a proactive way to safeguard your molding processes. For more guidance and support about custom injection molding, contact Sound View Plastics today and let us help you maintain a safe, efficient workplace.
PlasTech Molding Solutions operates from a single location at 50 mellen street, hopedale, massachusetts 01747, united states.
Having a clear understanding of both basic and advanced safety tips can prevent accidents and keep operations running smoothly. Fundamental practices include wearing the right gear, properly handling materials, and ensuring machine guards are in place. Additionally, workplace-specific measures like regular maintenance and thorough employee training boost overall safety.
PlasTech Molding Solutions uses a variety of equipment, including Horizontal injection molding machines (29 machines ranging from 22 tons to 310 tons).
Sound View Plastics brings over 30 years of diverse experience to the plastics industry. We’re prepared to assist you with part, assembly, and product designs to complete your next injection molding project. Our robust industry network, trusted quality processes, and tool development can help your business be more efficient. Sound View is ready to be your partner in plastics.
The headquarters of PlasTech Molding Solutions are located in 50 mellen street, hopedale, massachusetts 01747, united states.
Safety in plastic injection molding is crucial for protecting workers and ensuring efficient production. Due to the high temperatures and heavy machinery involved, taking appropriate safety measures is essential. From using personal protective equipment to knowing emergency shutdown procedures, each step helps create a safe working environment.
PlasTech Molding Solutions, formerly R.E.C. Manufacturing Corporation, specializes in custom injection molding with over 70 years of experience. Their expert staff, with a combined experience of over 100 years, excels in developing high-performance products, including thin-wall complex geometry applications. The company operates a modern 40,000 square foot facility with multiple clean rooms and a range of injection molding machines. PlasTech Molding Solutions is ISO 9001 certified, ITAR registered, and prioritizes customer service, engineering, production, and quality assurance. They offer a variety of services to meet the needs of both existing businesses and new product development.
Machine guarding is a crucial part of safety in plastic injection molding. Guards on the machines prevent workers from coming into contact with moving parts. These guards should always be in place and never removed during operation. It’s important for operators to check that all safety guards are secured before starting the machine. Regular inspections can ensure that guards are functioning properly and haven’t been tampered with. Good machine guarding practices help prevent accidents and make the workplace safer.
By focusing on these safety aspects, companies can safeguard their employees and maintain high standards of productivity. Keeping everyone informed and prepared is key to successful plastic injection molding.
Knowing how to quickly and safely shut down machinery in an emergency is essential in any plastic injection molding facility. Emergency shutdown procedures should be clearly outlined and accessible to all employees. Specific buttons or levers on the machines can immediately stop operations if a hazardous situation arises. Regular drills and training on emergency shutdowns ensure that workers can act swiftly and correctly when needed. This proactive approach can prevent accidents and reduce the severity of any incidents, making the workplace safer for everyone.
GETTING A QUOTE WITH LK-MOULD IS FREE AND SIMPLE.
FIND MORE OF OUR SERVICES:
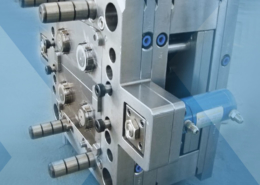
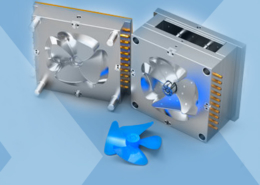
Plastic Molding

Rapid Prototyping
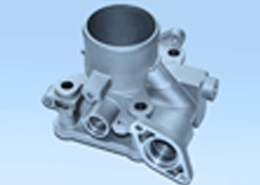
Pressure Die Casting
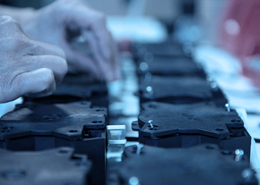
Parts Assembly
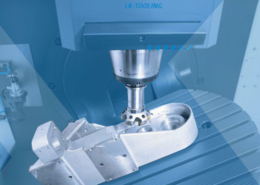