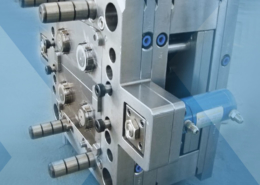
High Precision Injection Molding: Revolutionizing Manufacturing
Author:gly Date: 2024-06-08
In the realm of manufacturing, precision is paramount. High precision injection molding stands as a beacon of innovation in this regard. This article delves into the intricacies of high precision injection molding, its applications, advantages, challenges, and future prospects, aiming to captivate readers with its significance and potential.
Introduction
High precision injection molding, an advanced manufacturing technique, involves injecting molten material into a mold cavity with high speed and pressure. The process yields intricate and accurate components used across diverse industries, from automotive to medical.
Precision Engineering
Engineering Excellence
High precision molding demands meticulous engineering. Tolerances as tight as microns are achievable, ensuring the exact replication of mold designs. Advanced software and simulation techniques aid in optimizing mold flow and part design, enhancing precision further.
Tooling Perfection
Central to precision molding is tooling. CNC-machined molds crafted from premium materials guarantee dimensional stability and longevity. Advanced surface treatments minimize friction and wear, ensuring consistent and high-quality output over extended production runs.
Material Science
Material Selection
Choosing the right material is critical in precision molding. Engineering-grade thermoplastics offer a balance of strength, flexibility, and heat resistance, ideal for demanding applications. Specialty materials like liquid silicone rubber (LSR) cater to the medical and electronics industries, offering biocompatibility and exceptional electrical properties.
Material Handling
Maintaining material integrity throughout the molding process is vital. Automated material handling systems ensure precise dosing and mixing, minimizing variations in material properties. Tight control over material temperature and viscosity guarantees uniform flow and part consistency.
Process Optimization
Injection Control
Precision hinges on injection control. Advanced servo-driven injection systems provide unparalleled speed and accuracy, facilitating precise material dosing and cavity filling. Closed-loop feedback mechanisms adjust process parameters in real-time, compensating for fluctuations in material viscosity and environmental conditions.
Quality Assurance
Ensuring product quality is non-negotiable. Inline inspection systems employ vision technology to scrutinize parts for defects with unparalleled accuracy. Statistical process control (SPC) methodologies monitor key process parameters, enabling proactive intervention to prevent defects before they occur.
Applications and Advantages
Industry Applications
High precision injection molding finds applications in a myriad of industries, including automotive, aerospace, electronics, and healthcare. From intricate automotive components to miniature medical devices, the technology enables the realization of complex designs with unmatched accuracy and repeatability.
Advantages
The advantages of high precision injection molding are manifold. Reduced material wastage, shorter production cycles, and enhanced part quality translate to significant cost savings and competitive advantages. Furthermore, the ability to manufacture complex geometries and micro-features opens doors to innovative product designs and functionalities.
Challenges and Future Directions
Challenges
Despite its merits, precision molding presents challenges. Complexity in mold design and fabrication, coupled with the need for stringent process control, can pose barriers to entry for some manufacturers. Moreover, the demand for even tighter tolerances and higher part complexities necessitates continuous innovation in materials, processes, and equipment.
Future Directions
Looking ahead, the future of high precision injection molding appears promising. Advancements in material science, additive manufacturing, and industry 4.0 technologies hold the key to further enhancing precision, efficiency, and sustainability in manufacturing. Collaborative research efforts and knowledge sharing will play pivotal roles in driving the industry forward.
Conclusion
In conclusion, high precision injection molding epitomizes the pinnacle of manufacturing excellence. Its ability to produce intricate components with unparalleled accuracy and efficiency underscores its significance across industries. Embracing precision molding opens doors to innovation, cost savings, and competitive advantages, propelling manufacturing into a new era of possibilities. As we continue to push the boundaries of what is achievable, high precision injection molding remains at the forefront of technological innovation, shaping the future of manufacturing.
GETTING A QUOTE WITH LK-MOULD IS FREE AND SIMPLE.
FIND MORE OF OUR SERVICES:
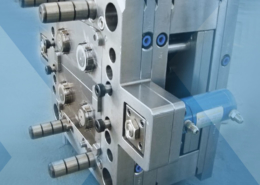
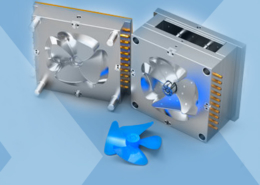
Plastic Molding

Rapid Prototyping
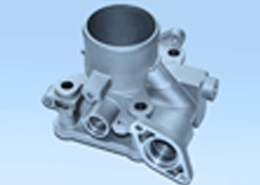
Pressure Die Casting
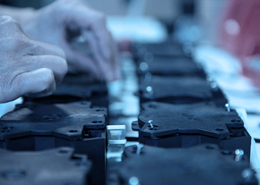
Parts Assembly
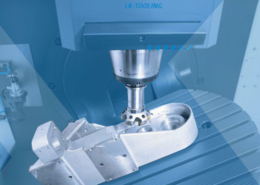