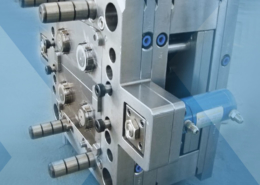
Top 6 Plastic Moulding Companies in Malaysia - kilang plastic injection moulding
Author:gly Date: 2024-10-15
Estimate the entire costs of setting up the injection molding business, including the equipment cost, tooling cost, factory cost, labor cost, etc. After estimation, decide on the price of the injection molded products to ensure that the costs are recovered by the revenue.
Seasky Medical serves you with medical injection molding solutions from design to tooling to material selection and manufacturing. Contact our specialized team and solve your problem now.
The market of plastic injection molding is relatively broad as injection molded products are produced for various industrial applications. The revenue of the injection molding business market in 2020 stood at USD 343.23 billion and reached USD 357.34 billion in 2021. As per the market estimations, the global injection molding plastics market is analyzed to thrive at USD 476.46 billion by 2028.
There are various injection molding machines, and almost all of them have automatic functions. Due to these automated machines, human labor assistance is not much required. Because of the less human labor, custom plastic molding can save money on labor expenses.
We manage the maintenance and repairs conducted according to the maintenance frequency decided for the shot count and the design and production history of injection molding dies and stamping dies as "die records." Our technicians that are well-versed in both injection molding dies and stamping dies maintain quality on a daily basis. Should a problem happen to occur, they can check the die records to go through the past history and changes.
With 3D scanner CMM from Keyence Corporation, we compare molded products at the prototype stage and CAD data with images to check for deviation and differences from the drawings. We also have coordinate measuring machines and Measuring microscopes, etc. measuring microscopes are also installed in our die manufacturing sites for on-the-spot checks.
There is evident growth in the global injection molding market that is linked to the growing demand for high-quality injection molded products. Acquiring the injection molded components from a reliable plastic injection molding manufacturer is highly beneficial due to the low cost and quick production.
The injection molding business is a great way to become environmentally conscious. The injection molding procedure leaves less scrap, and it is environmentally friendly. Even the excess plastic substance can be recycled and reused for making other plastic products.
Injection molding businesses will ensure that the business owners get enough profits. Since the demand for these products is increasing, the injection molding business will have more than enough clients, so the manufacturing process runs throughout the year. This way, it will be easy to earn more revenue.
When compared to various manufacturing methods, injection molding is known best due to its consistency. Due to the high-quality mold tooling, it is possible for businesses to produce exact parts for thousands of production cycles. Regardless of the design complexity, the business will be able to maintain the injection molded product consistency.
The injection molding procedure is only highly profitable in case of large-volume production. If the clients have ordered injection molding parts in small quantities, the molding business might not get much profit. This is because the mold design and tooling take up much of the budget.
It is to be noted that there are different types of injection molding methods, and choosing the proper method will ensure high profits. The most common injection molding methods are plastic injection molding, foam injection molding, liquid silicone injection molding, metal injection molding, and 3D printing. Depending on the type of products your business is planning to produce, it will be easy to pick the right injection molding method.
The injection molding procedure is compatible with various raw materials. The businesses can maintain stock of various substances, which makes it easier for material selection. There are many affordable and expensive raw materials as well.
The injection molding business is profitable because it has the capability to produce large quantities of products within a short time. In addition to that, complicated designs can be produced easily via injection molding due to the mold design and tooling. Another benefit is that the plastic molding company produces little to no waste, and the leftover plastic can be recycled.
When the injection molding procedure has started, making alterations to the design will be difficult and expensive. It is because a new mold design and tooling are required, which will require more time and adds additional expenses.
We start by checking the dimensions of the prototype, then check for internal defects such as voids and external problems such as glass fibers, short shots, sink marks, burning, and flash, which may occur due to the resin material/product shape. When performing die adjustment or changing conditions according to changes in the customer specifications, we are able to perform trial molding at our factory, which means that the new specifications can be quickly reflected in the molded product. We can then provide feedback on the status of product improvement. As customer assembly processes become more automated and higher precision is required for component units, we identify concerns before mass-production drawings/mass-production dies and conduct adequate prototype evaluations.
The manufacturing plant layout is vital to successfully start your molding business. The production factory should have enough space to fit all the injection molding equipment and a clean room injection molding facility as well. Make sure to design separate spaces for testing the molded products and storing the manufactured products.
The lead time of the injection molding procedure is relatively higher in comparison to other procedures. From product development, part design, material selection, mold tooling, sampling, and finally, manufacturing the products, the entire process will take several months. Due to the relatively long lead time, some people do not prefer injection molding businesses.
There are many raw plastic materials that are compatible with the injection molding process, such as acrylonitrile butadiene styrene, silicone, polypropylene, etc. However, it is better to only source medical-grade raw materials from reliable companies that guarantee the credibility of the materials.
We conduct prior verification such as resin fluid analysis for mold conditions such as the gate position, resin injection pressure and filling time, and die temperature. We then determine the die structure upon comprehensively investigating the specifications, drawing requirements, and product shape received from the customer. The molding conditions are determined based on resin properties obtained in production history and past launch data such as resin fluidity, gas position and volume, and rate of contraction. Our molded products are produced from simple prototype dies according to customer evaluation and development steps.
The beginning expenses of molding die and equipment are rather expensive. Because of that, many people hesitate to start an injection molding business due to a lack of needed budget. Mold making is also another expensive task associated with injection molding. However, softer die substance is affordable but can not be used for large-scale production.
SeaskyMedical uses reliable medical-grade raw materials to produce parts and inspect manufactured products. At SeaskyMedical, large orders are processed quickly for a lower price. Make sure to contact SeaskyMedical to get small-scale or large-scale injection molded products. They provide injection molding service to both domestic and worldwide clients, can be your reliable molding partners.
The inspection jigs and tools used at our manufacturing sites are designed and produced in-house. We confirm that metal stamped inserts are non-faulty within the process, and if there is any indication of a fault such as deformation, we quickly identify and deal with it.
The market for injection molding products is on the rise, and the demand for injection molded parts is thriving rapidly. There are many industries where injection molded parts are being used, such as the medical industry, automotive industry, consumer electronics, pharmaceutical industry, telecommunication industry, food and beverage industry, construction industry, packaging industry, etc.
Planning to sell injection molded products? In that case, finding a reliable plastic injection molding manufacturer is essential. SeaskyMedical is a China-based medical plastic injection molding producer with more than 10 years of industrial experience and Class 8 clean room. This company offers a one-stop molding service, including part design, material selection, mold tooling, and quick production and supply.
Starting an injection molding business can seem challenging if one does not know where to begin or what things are needed. To make it easy for people to get into the injection molding business, here we have listed the common steps involved in beginning the injection molding business.
There are a wide variety of molding machines, such as CNC machining, EDMs, drilling and milling equipment, etc. The molding machines have different working mechanisms and are used for different purposes. Due to that, it is best to choose the proper machines that are compatible with the type of products the business will produce. Avoid picking cheaper molding machines, as they may stop working in a few months. Choose durable and good-quality equipment.
The mold tooling is a crucial part of ensuring that your molding company delivers precise, high-quality parts to the clients. It is highly recommended to hire mold design and tooling experts to handle the mold tooling requirements for your business.
Seasky Medical serves you with medical injection molding solutions from design to tooling to material selection and manufacturing. Contact our specialized team and solve your problem now.
Based on the total cavities in the molding tool, the injection molding procedure can create plenty of components in an hour. With the proper molding tool design and molding equipment, it is possible for businesses to consistently create high-quality parts with shorter lead times.
We consider die structure to minimize defects expected in mass-production from the stage of prototype dies, and utilize our design ability and die processing technologies we have cultivated over the years to design, manufacture, and assemble high quality injection molding dies and stamping dies.
The injection molded parts are made using high-quality medical-grade materials that are known for their sturdiness and long-lasting features. Due to that, injection molding medical devices last for a long period, stay durable, and can withstand heavy pressure and temperature. The molded products are highly used in applications that require impact resistance, pressure resistance, temperature resistance, etc.
The mold designers and tooling experts with enough experience can make the proper molds for your business. Therefore, it can become a little difficult to discover the right experts. In addition to that, hiring those skilled mold and tooling designers means one has to spend more money.
The present plastic injection molding businesses are producing a wide range of products for different industrial niches. For example, the various niches include the pharmaceutical field, medical device field, automotive field, telecommunication field, electronics, food and beverage industry, packaging industry, construction field, and many more. As there are many niches for injection molding, it is vital to choose a specific niche. This way, one can establish a medical device component manufacturer that is focused on producing molded parts for a particular industry.
GETTING A QUOTE WITH LK-MOULD IS FREE AND SIMPLE.
FIND MORE OF OUR SERVICES:
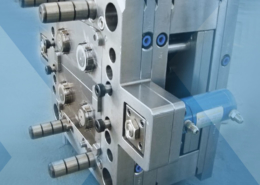
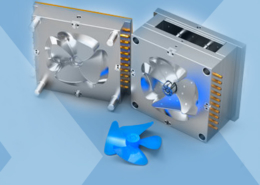
Plastic Molding

Rapid Prototyping
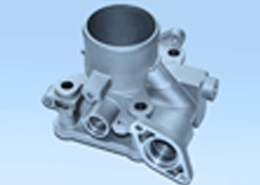
Pressure Die Casting
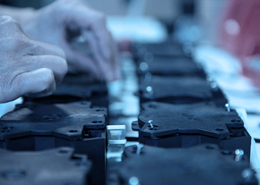
Parts Assembly
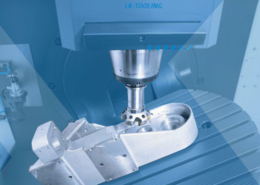