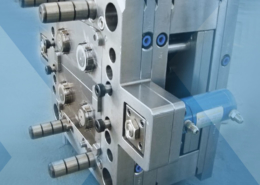
Top 30 Plastic Injection Molding Companies in The USA - 2024 - top injection mol
Author:gly Date: 2024-10-15
This is why choosing a supplier with exceptional skills is important. Excellent supplier quality scorecards established processes to prevent flash, flow lines, short-shots, and backup plans from increasing capacity as your company and your needs for two shot molding expansion are all things to look for.
The soft plastic is molded a second time after being first molded as hard plastic. The first time is transparent; the second time isn’t. The first molding is done with a high temperature plastic, while the double molding is done with a low-temperature plastic.
This is essential for producing solid surface cosmetics and a homogeneous mold. In single-shot injection molding, the melt can enter through the thickest part of the opening before flowing to the smaller areas, thanks to the gate’s placement.
The two shot injection molding technique is divided into two steps. The first involves an injection of resin into a mold, which is then cooled to create a solid object, much like traditional injection molding.
For intricate, multiple colors, and multi-material plastic goods, especially in high-volume manufacturing circumstances, two shot injection molding is the best plastic molding technique.
Materials like silicone and thermoplastics, nylon and thermoplastic elastomers, or stiff nylon and soft touch materials are a few examples of materials that can be blended successfully with this procedure.
Substance A is first injected into the cavity when the slider is in its expanded position during the injection molding process using the core toggle two shot mold. Then pulling the slider back to expose a new area of the cavity.
Take into account the two materials’ shrinking. Generally speaking, the material that is initially created affects shrinkage.
The method is also excellent for making soft handles for electrical equipment, air conditioning seals and gaskets, and non-slip surfaces. With this method, logos may be created that, unlike painted-on logos, would never fade.
In addition, the two shot molding process is applied in the automotive sector to make a wide range of products and parts. Other items made using the double shot process include lawn and garden tools and agricultural equipment.
The structure contains closed numeric or alphabetic characters like 0, 4, 8, A, B, D, and O. The secondary material can only easily enter the confined region when a seesaw construction is used, creating a lovely appearance.
In two shot injection molding, a first section is molded, and after it is complete, a second part is injected to create the molding’s final portion. Both pieces must be comparable (chemically) for the two shot molding process to be successful for bonding to take place.
For a strong molecular bond to be possible, your substrate and second-shot resin should ideally be chemically compatible. The longest leg or surface area is ideal for the joint between the two resins. The second shot is nearly impossible to remove by selecting the ideal materials and joint design.
You may create more useful, sophisticated elements using the two shot approach. Further, softer plastic may be mixed with hard plastic. The product has significantly greater integrity. Two-shot plastic molding products are often far more durable and shockproof.
Two different plastic resins are molded together in a single machining cycle during the double injection molding process, also known as dual shot, double shot, multi shot, and overmolding.
World Class Service – We listen to our customers, anticipate their needs, and seek to exceed their expectations prior to them having to ask.
People who are unfamiliar with two-shot injection molding might think it’s difficult. It does involve a second material and procedure, which adds another factor to component creation, but it’s relatively easy.
The remaining space is filled by moving the slider after material B is injected into the modified cavity through a different gate (above the middle nozzle).
With the first mold rotated out of the way and the second mold placed around the product so that the second compatible thermoplastic can be injected into the second mold, the two-step procedure only requires one machine cycle.
To form holes, snap features, and lengthy through-holes, the mold closes these places to prevent plastic flow into those locations.
A part made of hard material can be joined to a part made of soft material using two shot injection molding. In a two cavity mold, the procedure combines the molding of two components. It can significantly improve the product’s appeal in terms of feel, color, etc. There are many different design possibilities with two-shot molding.
Permit the first injection-molded part’s edge to be excessively large. This assures that the second injection will have a higher pressure.
The newly-molded object is transported to a second mold in the second stage using a rotating platen or a robotic arm. Depending on the design, the newly-molded part is then given a second injection of resin in, through, or around specific areas of the first mold.
The chemistry of the materials is crucial to take into account when deciding which ones to utilize for two-shot molding. While some materials bind imperfectly, others work well together and create a solid molecular adhesion.
A material compatibility table is reviewed to determine which polymers will cling to one another and which polymers are incompatible. Additionally, it eliminates the possibility of contamination, which is an issue when utilizing two different molds.
In addition, compared to producing an identical product or part using two different molding processes, the two shot molding procedure results in a much stronger bond. The ability to make multicolored plastic goods using the two-shot molding method is one of the process’ additional advantages over painting, which may lose its effectiveness over time.
Innovative and Creative – Our employees are the most valuable asset of the company and the only asset that has the ability to innovate and generate creative ideas to provide solutions to customer challenges. We will encourage teamwork, creative thinking, and innovation as a primary avenue to add value to our customers, reduce cost and improve quality.
Because the mold’s core and cavity do not need to be relocated, the core toggle multi shot molding procedure is the simplest. Alternatively, shifting the slider will alter the geometry of the mold cavity.
A broken hole is created as the needle rises at the edge of the sealed-off portion of the primary product. To drill the secondary material into the closed area from the broken hole, the needle is moved lower by the returning pin of the fractured plate during the double injection molding process.
The number of parts in a finished assembly is decreased using two shot injection molding, saving an average of USD$40K in development, engineering, and validation expenditures for each increased part number.
The plastic component is then forced out of the mold after hardening. Circulated in the same order as above to continue the molding.
An injection molding machine is used in the two shot molding process where two materials are “over molded” in one molding cycle. The amount of material injected into the molding cavity is referred to as a “shot.”
Our business strategy and operating plan is built upon People, Process Control, and Technology. We believe that by combining the best talent with proper technology to control the injection molding process we will manufacture consistent high quality parts for our customers. We also believe that culture is a strategic advantage and when we can foster an environment where people care for each other they will take care of the equipment, resin, customers and company.
Physical, mechanical, chemical, thermal, electrical, flammability, and UV resistance are all important considerations when selecting a material for your component. You’ll need to provide answers to a number of questions in order to focus your material selection, including:
With two shot molding, several components can be molded with a single tool, requiring less work to produce your parts and no post-molding welding or joining of the components.
Conduct an adhesion test before beginning manufacturing when the adhesive property of two compounds is unclear. When bonding is insufficient, fixes can be incorporated into the design, such as undercuts, grooves, or shoulders, to increase adhesion and lock the two compounds together.
The male model cavity glides under the influence of the motor as the mold is opened after one injection. A specified distance is used to align the mold with the master mold before the second injection molding process.
In order to create the first segment of the product, one material is first injected into a mold. A second injection of a secondary material compatible with the first follows this. There are several reasons why many businesses choose to produce plastics or polymers this way.
Following the formation of a molecular link between the two plastic resins, the multi-resin molded object is cooled and expelled.
Two-shot molding can be done using rotary platen, movable core, or overmold, among other options. The first two require two processes, two runner systems, and a second injection unit.
Texas Injection Molding provides custom plastic injection molding services for OEM manufacturing and consumer products. Located in Houston but also serving in Austin, San Antonio, and the S. E. United States, Texas Injection Molding provides product design assistance and engineering services for the development of plastic injection molded products. We offer decades of experience in processing commodity and custom engineered plastic resins and partner with the world’s leading resin manufacturers and custom compounders to bring solutions to complex plastic engineering applications. We strive to be known in the markets we serve as the best partner for custom plastic injection molding manufacturing services that operates to the highest ethical standards.
In these situations, the mold’s two halves seal against one another. Due to this, the sealing faces of the mold can open and close without colliding with one another. Three to five degrees should be the minimum draft angle. The longer the mold lives, the higher the clearing and the greater the draft.
A cutting-edge manufacturing technique called double injection, also known as two-material, two-shot molding, or two-K molding, is used to create intricate molded parts from two different materials.
Although the procedure is simple to grasp, mastering it is challenging. Even the tiniest errors can result in significant financial losses because of the high levels of technical competence and attention to detail required, especially in high-volume manufacturing circumstances.
Texas Injection Molding offers in-house tooling design and engineering support for new injection molds and has both in-house and outside plastic mold building resources to provide cost effective solutions to new tooling. Our in-house tooling group provides routine preventative tooling maintenance and tooling repairs to keep customer production running on-time.
Product makers prefer two shot injection molding for a variety of applications, including automotive interior parts, medical equipment, tools, and toys. It enables manufacturers to mix a multitude of components and hues to produce a robust and aesthetically pleasing product.
Integrity – We will be known in the industries we serve as a company that fulfills our commitments and operates to high ethical standards.
The mold, which can hold more materials, is only seen here with the two materials. Depending on how much material is utilized, the rotating platen can be rotated by 90°, 120°, or 180°. A specific injection machine is also required to produce the necessary rotation on the core side.
Although the tool’s price increases when a slider is added to the mold, it can still be significantly less expensive than rotating platen or rotary shaft molds. Sadly, it is unable to make intricate, multicolored plastic pieces.
Two shot molded parts are utilized in almost every industry, from consumer goods to construction, but they are most frequently used in situations needing the following:
Choosing and ending up with the proper mold structure is essential to save on costs and ascertain quality. Here are some types of two shot molding structures:
The method produces more products each run for less money and requires fewer workers to produce the completed product since it uses a single machine cycle rather than multiple machine cycles. Additionally, it guarantees a solid binding between the materials, eliminating the need for later assembly.
Plastic polymers are utilized in a range of production processes, such as extrusion, compression thermoset molding, and two shot injection molding. While each is a feasible manufacturing method, many plastics manufacturers use this method due to several advantages.
During the two shot injection molding, we carefully control the injection of numerous materials, including two distinct types of resin, into a single, multi-chambered mold using a highly specialized and automated technique.
The melted resin enters the mold chamber through a gate channel when using injection molding. To achieve the ideal part proportions and aesthetic look while preventing warping, the type of gate, design, and location must be taken into account.
Even when a high-level chemical bond may be achieved, we highly advise using an appropriate mechanical bond if bonding is important to your application.
With one side moving up, the other side moving down, and so on, the slab structure is made up of two sides rotating around the center. Most keyboard mold designs with numbers and letters use the seesaw structure.
An Adventure to Live – We will continuously evaluate business opportunities and seek to realize those opportunities that provide great value to the customer, inspire the organization, and provide great satisfaction to the organization when realized.
The latter often uses two different molds, one for each material, but can also be carried out using just one mold, two runner systems, and manual or automated pick-and-place part transfer.
On the centerline of the platen, which parallels the axis of rotation, the mold core plate has two identical cores that are mirror images of one another. Two cavities with various geometries are included in the cavity plate attached to the fixed platen.
GETTING A QUOTE WITH LK-MOULD IS FREE AND SIMPLE.
FIND MORE OF OUR SERVICES:
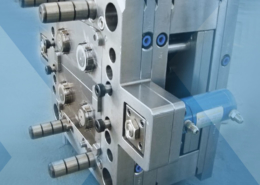
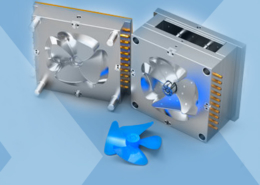
Plastic Molding

Rapid Prototyping
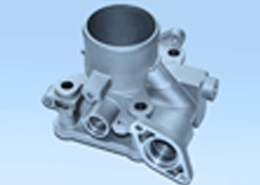
Pressure Die Casting
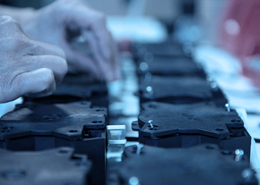
Parts Assembly
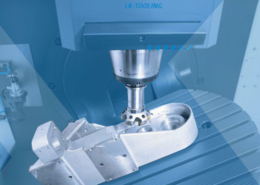