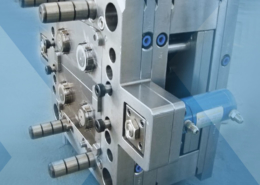
Exploring the World of Hard Plastic Molds
Author:gly Date: 2024-06-08
Introduction
Hard plastic molds stand at the forefront of modern manufacturing, embodying precision, efficiency, and versatility. These molds serve as the backbone of numerous industries, from automotive to consumer goods, revolutionizing the production process and driving innovation. In this article, we delve into the realm of hard plastic molds, uncovering their significance, functionality, and impact across various sectors.
The Anatomy of Hard Plastic Molds
Hard plastic molds are meticulously crafted structures, typically composed of durable materials such as steel or aluminum. Their intricate design facilitates the formation of complex shapes with unparalleled accuracy. Each mold undergoes rigorous engineering processes, including CAD modeling and CNC machining, to ensure precise replication of desired products.
Precision Engineering
Precision is the hallmark of hard plastic molds, enabling manufacturers to achieve consistent output and high product quality. Advanced machining techniques, such as EDM (Electrical Discharge Machining) and CNC (Computer Numerical Control) milling, are employed to create intricate features and fine details with micron-level accuracy.
Material Selection
The choice of material for hard plastic molds is critical to their performance and longevity. Factors such as thermal conductivity, wear resistance, and machinability are carefully considered during the selection process. High-grade steels, such as P20 and H13, are commonly preferred for their excellent thermal stability and mechanical properties.
Surface Finishing
Surface finish plays a pivotal role in mold performance, affecting part quality and cycle time. Techniques such as polishing, texturing, and coating are employed to enhance surface properties and minimize defects. A meticulously finished mold surface ensures smooth demolding and reduces the need for secondary operations.
Applications Across Industries
Hard plastic molds find widespread application across diverse industries, revolutionizing manufacturing processes and enabling the production of intricate components and products.
Automotive Industry
In the automotive sector, hard plastic molds play a crucial role in the fabrication of interior and exterior components, ranging from dashboard panels to bumper covers. Their ability to withstand high temperatures and repetitive molding cycles makes them ideal for mass production in automotive manufacturing plants.
Consumer Electronics
The consumer electronics industry relies on hard plastic molds for the production of casings, enclosures, and components for smartphones, laptops, and household appliances. These molds enable manufacturers to meet stringent design requirements while ensuring durability and aesthetic appeal.
Medical Devices
In the medical sector, hard plastic molds are instrumental in the production of precision components for medical devices and equipment. From syringe barrels to surgical instruments, these molds enable the manufacturing of sterile and biocompatible parts that meet regulatory standards.
Advancements and Future Trends
The field of hard plastic molds continues to evolve, driven by advancements in materials, technology, and manufacturing processes. Future trends such as additive manufacturing, multi-material molding, and smart tooling are poised to further enhance the capabilities and efficiency of hard plastic mold production.
Additive Manufacturing
Additive manufacturing, also known as 3D printing, holds immense potential for the fabrication of hard plastic molds with complex geometries and internal channels. This emerging technology offers greater design freedom and shorter lead times, revolutionizing the traditional mold-making process.
Multi-material Molding
The demand for multi-material components is on the rise, driven by the need for enhanced functionality and aesthetics. Hard plastic molds capable of accommodating multiple resins in a single shot are gaining traction, enabling the production of integrated assemblies with varying properties.
Smart Tooling
Advancements in sensor technology and data analytics are paving the way for smart tooling solutions in hard plastic mold manufacturing. Real-time monitoring of temperature, pressure, and cavity fill allows for proactive maintenance and optimization of production processes, leading to improved quality and efficiency.
Conclusion
In conclusion, hard plastic molds represent a cornerstone of modern manufacturing, enabling the production of intricate components and products across various industries. With precision engineering, advanced materials, and continuous innovation, these molds drive efficiency, quality, and competitiveness in today's global market. As we embrace future advancements and trends, the role of hard plastic molds will continue to expand, shaping the way we design, produce, and interact with the world around us.
GETTING A QUOTE WITH LK-MOULD IS FREE AND SIMPLE.
FIND MORE OF OUR SERVICES:
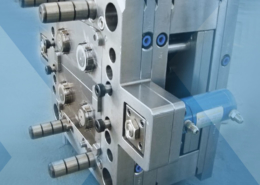
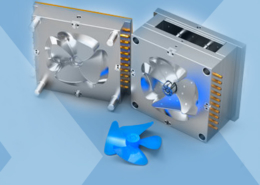
Plastic Molding

Rapid Prototyping
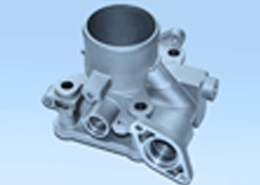
Pressure Die Casting
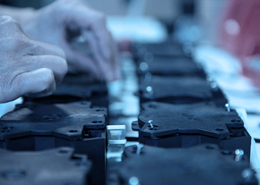
Parts Assembly
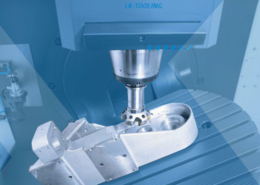