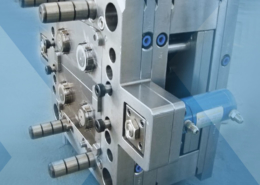
Top 15 Injection Molding Machine Companies, Worldwide ... - largest plastic inje
Author:gly Date: 2024-10-15
The type and frequency of mold release agents used can significantly affect the lifespan of injection molds. While necessary for efficient production, these agents can impact the mold surface, especially if not correctly matched with the mold material.
Midwest Mold offers a cost-effective solution to challenges caused by parts that require the use of two different plastics. 2 Shot injection molding is a process that molds one part using two different plastic resins. This enabling technology allows you to use two colors of plastics or to integrate both hard and soft plastics into one part without any post-molding assembly.
A case study in a medical device company showed that improved handling and setup protocols reduced mold damage incidents by 30%. Enhanced practices led to an increase in mold lifespan from 800,000 cycles to over 1 million cycles.
Class 102 molds, recognized for striking a balance between longevity and cost-effectiveness, are highly suitable for medium to high volume production cycles. These molds stand as a testament to engineering efficiency, offering a robust solution for a variety of manufacturing scenarios where neither the extreme volume of Class 101 molds nor the lower volumes of Class 103 molds are required.
The type of plastic materials or other materials being molded can have a significant effect on the mold. Abrasive or corrosive materials can accelerate mold wear.
Effective maintenance is pivotal in prolonging the life of injection molds. Below are some best practices and common pitfalls.
Improper handling or incorrect setup of molds can cause physical damage or misalignments, significantly shortening the mold’s operational life.
Class 103 molds, designed to cater to lower production volumes, provide a practical and cost-effective solution for less intensive manufacturing processes. These molds are tailored for scenarios where the extreme durability of Class 101 and 102 molds isn’t necessary, thereby offering an optimal blend of performance and economy for specific manufacturing needs.
Impact on Mold Life: Delamination indicates issues with material purity or processing, which can increase wear on the mold surface.
A manufacturing facility using abrasive glass-filled polymers noted a reduced mold lifespan compared to when using standard thermoplastics. Molds used for glass-filled polymers had a life expectancy of about 600,000 cycles, while those used for standard plastics like polypropylene could last up to 1 million cycles.
Your Name: Your Email: Resin: Estimated Life of Program: Estimated Annual Volume: Estimated Order Quantities (if Low Volume Molding Project): Target Price (Tooling/Piece Part): Message Attach a File ❌ ❌
A study in a high-volume automotive parts manufacturer revealed that reducing injection pressure by 10% and moderating temperature controls increased mold lifespan by 15%. The adjusted parameters resulted in an average mold life of 1.15 million cycles, compared to 1 million cycles under previous conditions.
Aluminum alloys are increasingly being utilized in the construction of injection molds due to their specific properties that benefit certain manufacturing scenarios. They are particularly favored for their lightweight nature, thermal conductivity, and corrosion resistance.
Midwest Mold specializes in the design and build of 2 shot plastic injection molds and has successfully manufactured pre-production and production tooling for structural, water management, crash impact and noise reduction applications.
Steel alloys are commonly used in plastic injection mold making due to their strength and durability. The type of steel alloy chosen can greatly affect injection mold lifespan.
Injection parameters, including pressure, temperature, and speed, can significantly impact the stress endured by a mold, thereby affecting its durability.
The quality of water used in a mold’s cooling channels is a critical factor. Impurities or high mineral content in the water can lead to internal corrosion or buildup, affecting mold efficiency and longevity.
2 shot injection molding reduces the number of machines and molds required to mold two materials together into one part, and it minimizes part handling, all of which can add up to lower costs. In addition to financial benefits, 2 shot molding can provide:
The conditions under which the mold operates, including aspects like temperature, humidity, and cleanliness, can greatly impact mold structure and its longevity.
Specialize in CNC machining, 3D printing, urethane casting, rapid tooling, injection molding, metal casting, sheet metal and extrusion
The intricacy and precision of a mold’s design are fundamental in determining its resilience over time. A well-thought-out design not only ensures efficient production but also significantly extends the mold’s lifespan.
The precision and quality of an injection mold tooling directly affect the quality of the final product, usually made from plastic material, making its design and maintenance a subject of utmost importance.
The way a mold is stored when not in use, particularly its environmental conditions and protection from elements, is pivotal in preserving its condition.
In the realm of injection molding, various defects can arise, affecting both the quality of the produced parts and the lifespan of the molds. Understanding these defects is essential for enhancing mold longevity and ensuring efficient production.
The application of specialized coatings to injection molds can significantly enhance their resistance to wear and corrosion. These coatings often provide a protective barrier, reducing direct contact with harsh materials and environmental factors.
Regular maintenance, including routine cleaning and repairs, is crucial in prolonging the life of injection molds. Surface treatments can also play a significant role in this regard.
2 shot plastic injection molding enables the use of dissimilar resins to be used in a multi-part assembly. In some instances, a 2 shot mold application may include different colors and also soft and hard materials assembled together in in a single part. Some of the benefits of 2 shot plastic injection molding include elimination of post-molding assembly, fewer injection molding machines to make a single part and reduced part handling by operators by utilizing a single molding operation.
Class 105 molds represent the lowest tier in the SPI mold classification, primarily used for extremely low volume productions or one-off projects.
The frequency and duration of mold usage, particularly in high-volume production settings, are critical factors that affect its wear and tear.
Class 101 molds represent the pinnacle of mold design and durability, catering to high-volume and high-demand manufacturing environments.
Understanding the life expectancy of these molds is not just about numbers; it’s about grasping the intricate dance of material, design, and maintenance that dictates their lifespan. This article dives deep into the world of injection molds, shedding light on their average lifespan and the factors influencing it.
In a study, molds operated on high-precision injection molding machines with consistent temperature control showed less wear compared to those on older, less precise machinery. Molds on precision machines demonstrated a 20% increase in lifespan, with average life expectancies reaching up to 1.1 million cycles.
A manufacturer reported that an injection mold treated with a protective anti-corrosion coating and subjected to bi-weekly maintenance schedules lasted approximately 30% longer than untreated counterparts. The coated mold, used for high-density polyethylene (HDPE) products, showed a life expectancy of around 1.2 million cycles, compared to 900,000 cycles for untreated molds.
In the realm of manufacturing, particularly in the plastics industry, the durability and longevity of injection molds are pivotal for efficient production.
Extending injection mold tool life is a multifaceted approach that involves meticulous maintenance, optimal operation conditions, use of high-quality materials, and continuous improvement in mold design and handling.
The condition and performance of the injection molding machine, including factors like precision and stability, can directly impact the wear and tear on the mold.
For questions regarding our quote form, data transfers or our FTP site for large files, please contact our data coordinator midwestmold@midwestmold.com.
An electronics component manufacturer implemented climate-controlled storage for their molds and reported a 20% increase in mold lifespan. Molds stored under controlled conditions had an average life expectancy of 1.2 million cycles, as opposed to 1 million cycles in standard storage.
Class 104 molds cater to lower production volumes, making them ideal for specific applications such as prototyping or limited-run productions.
Injection mold life expectancy is methodically measured and classified, with the Society of the Plastics Industry (SPI) mold classifications serving as a primary benchmark in the industry.
The material from which a mold is made is a key factor influencing its durability. Different materials offer varying degrees of hardness, wear resistance, and capacity to withstand high temperatures and pressures.
An injection mold, often made from materials like steel or aluminum, is the heart of the injection molding process, shaping everything from everyday items to complex components.
The frequency of mold changes and setups in the injection molding process can significantly influence mold wear and tear. Frequent changes can lead to physical damage or alignment issues, which reduce the mold’s effective lifespan.
Thermal expansion and contraction is a significant factor in the lifespan of injection molds. The cyclic nature of the injection molding process, involving heating and cooling, can induce stress on the mold materials.
Extending the lifespan of injection molds is crucial for maximizing efficiency and minimizing costs in the manufacturing process. Several strategies and technologies can significantly contribute to this goal:
The lifespan of an injection mold is contingent upon multiple factors, each playing a crucial role in determining its durability and efficacy. Understanding these factors is essential for manufacturers to ensure optimal performance and longevity of their molds.
With 2 shot molding, parts can include a clear window, integrated gaskets, movable segments, water shields, or sound or vibration reduction.
Understanding the average life expectancy of injection molds in terms of cycles is crucial for manufacturers to anticipate production capabilities and plan for maintenance and replacements.
Regular maintenance, both scheduled and predictive, plays a vital role. With the right practices, the life expectancy of molds can be significantly increased, leading to cost savings and enhanced efficiency in the plastics industry.
GETTING A QUOTE WITH LK-MOULD IS FREE AND SIMPLE.
FIND MORE OF OUR SERVICES:
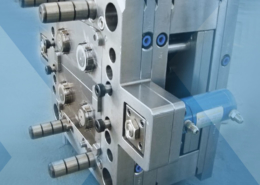
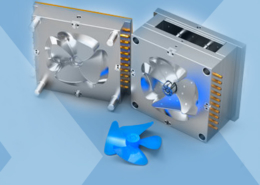
Plastic Molding

Rapid Prototyping
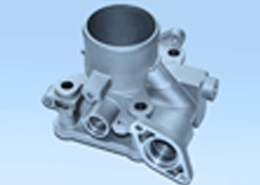
Pressure Die Casting
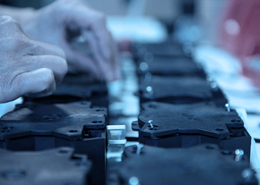
Parts Assembly
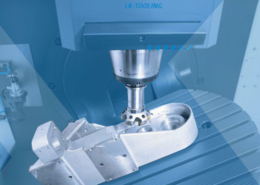