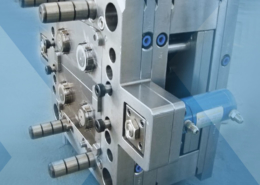
Top 10 Plastic Injection Molding Companies In China - top 10 injection molding c
Author:gly Date: 2024-10-15
As the leading large part injection molder in the United States, EnviroTech designs, engineers and produces large injection-molded polymer resin components. Our streamlined processes and in-house production facility allow us to complete massive production runs quickly and affordably.
We assist customers across virtually every sector and industry, including defense, mining, energy, oil and gas, agriculture, automotive, and deep-sea drilling rigs. We specialize in mold design, polymer resin engineering, mold optimization and troubleshooting, and custom injection molding of all types.
EnviroTech has over 50 years of experience and expertise in the injection molding space, optimizing part design for mold-ability and polymer resin engineering. With presses ranging from 850 – 2500 tons, and our experienced process control techniques that give us the ability to mold virtually any thermoplastic polymer resin and additive composition (see Polymer Resin Section), that opens the door to products for metal replacement and a wide range of industrial applications that were never before believed possible.
At EnviroTech Custom Injection Molders, we assist our customers with anything from the most diminutive part to the largest injection molded components. But, when working on substantial components – heavy, thick-walled or especially large – we have capabilities that you may not find elsewhere in the industry.
Plastics are also useful for heavy-duty packaging to protect construction materials or industrial equipment before it is put into use. Warning and other signage is also often made using plastic injection moulding techniques for maximum impact.
Our strict and exacting quality control processes allow us to provide consistently high-quality results without sacrificing time or economy. With our ability to customize injection molding solutions for our customers, you get the results you demand, time after time.
Use of plastic injection moulding products is commonplace in automotive manufacturing. Components are widely used in cars, vans and lorries, as well as other modes of transport such as boats and aeroplanes.
Our expansive facility operates around the clock to meet our customers’ needs. And, although we consistently meet the needs of our clients, we always strive to exceed their expectations.
The electronics sector uses plastic injection moulding products for several different applications This is because the finished products can be designed to highly bespoke specifications, with a huge choice of finishes, textures, shapes and colours. They offer good insulating properties too. Some uses for plastic injection moulding products in the electronics sector include smartphone and tablet components, battery casings, printed circuit boards and charging devices.
As with any manufacturing process, there are advantages and disadvantages to using plastic injection moulding to make required products. Advantages include the capability for large-scale production in a relatively short period of time, as well as the possibility of creating one-off prototypes using the same technique.
Uses for plastic injection moulding products across the medical and healthcare sectors is vast. Here, the materials are prized for their hygienic surfaces and ease of cleaning, their versatility and their resistance to bacteria and germs.
Plastic injection moulding products in the fast-moving textiles industry include tape strapping, plastics ropes and twines, sports clothing shoes and bags, sunglasses, watch straps, tote bags and beach shoes. The plastics offer good colour fastness, waterproofing and resistance to fading from UV rays from the sun or damage from bacteria mould and heavy usage when being worn, carried or used.
We offer a wide variety of polymer and engineering resin materials for you to choose from. We can recommend the best materials for your needs or, if necessary, we can work with our engineering resin manufacturing partners to design a material formulation just for you.
Examples of medical and healthcare products include syringes, vials, petri dishes, diagnostic devices and medication bottles. Also PPE, surgical equipment, implantable devices and stents.
As already mentioned, plastic injection moulding products can be found all over the world being used by most, if not all industries. Some examples of industries and how they use this type of products include:
Disadvantages include the fact that some polymers may be more difficult to recycle, making them a less environmentally-friendly option. There can be a higher initial cost setting up the machinery and designing bespoke moulds, plus the lead time can also be affected if the project is complex or intricate. Anything that introduces an undercut or locks the mould must be designed with extreme care.
The construction industry uses plastic injection moulded products for both large and small applications. So, they can be found inside heavy-duty machinery and furniture, as well as in decorative fixtures, fittings and tools.
Our company is known around the world as the industry leader in thick-walled injection molding. We have one of the largest shot capacities in the industry, allowing us to produce exceptional quality thick wall molding components that are void-free. We also design, engineer and manufacture large shot and thick-walled molds.
There are various methods of plastic processing available, including injection moulding, extrusion and blow moulding. The plastic injection moulding technique involves pouring melted plastics into a rigid mould, which is shaped to form the required part or component. Polymer pellets are fed into a hopper before being melted so that they can fit the mould. The mould is secured and the plastic left to cool and harden. The final product is then released and quality tested.
Our technology and sophisticated automation capabilities allow us to complete even the most massive thick wall molding production runs quickly without compromising quality output. Even complex components are no match for our experience and capability.
The food and drinks industry uses plastic injection moulded products for packaging such as trays, boxes, shrink wrap, bags and protective layers. They are lightweight, hygienic and can be hermetically sealed to keep the contents contamination-free. The versatility of the end products also make the plastics useful for rigid packaging, point of sale and advertising materials. Other things that can be packaged in this way include tobacco, electrical appliances, toys, clothing and electronic devices.
When you need the best heavy, large or thick wall molding services, call on the experts at EnviroTech for all your bulk and custom injection molding needs.
EnviroTech’s unique proprietary bulk injection molding process allows EnviroTech to manufacture and produce large thick-walled polymer components that are simply impossible for other injection molders.
Heavy injection molding uses a variety of space-age materials and additives to achieve the weight you need. Our processes ensure timely production and exacting standards of quality as well as the affordability you enjoy with standard injection molded products.
Multiple parts can also be created to accurate specifications and with precise uniformity. There is a vast choice of colours, designs and finishes available for excellent versatility. Materials used are readily available and offer good durability, strength and resistance to damage from UV rays, chemicals and general wear and tear.
Plastic injection moulded products can be made in a huge array of colours, finishes and polymers. The two main types of plastic materials used are polypropylene homopolymer and polypropylene copolymer. Each has different properties and benefits, including chemical and impact resistance, strength and stress crack resistance, high processability and durability. More information can be found here.
Plastic injection moulding products are used all over the world across multiple sectors. This is because they are versatile, hard-wearing and easy to design to highly accurate specifications. The plastic injection moulding process itself is efficient and effective, offering the capacity for large-scale production, as well as bespoke, one-off projects.
Using thermoplastics and polymer resins, EnviroTech has the ability to manufacture substantial components that have all the benefits of polymer injection molded parts – reduced cost, quick turnaround, minimal environmental impact – as well as the desired weight.
We have assembled a substantial collection of state-of-the-art equipment at our in-house design and production facility. Using cutting-edge technology and a half-century of experience, we have the ability to produce extremely large, heavy and thick-walled injection molded components.
GETTING A QUOTE WITH LK-MOULD IS FREE AND SIMPLE.
FIND MORE OF OUR SERVICES:
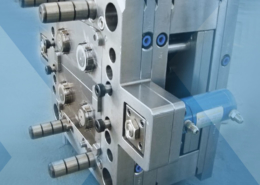
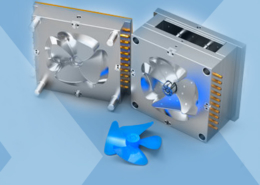
Plastic Molding

Rapid Prototyping
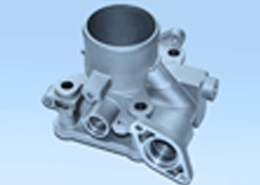
Pressure Die Casting
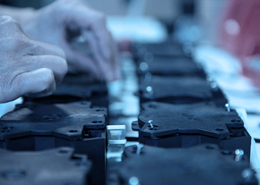
Parts Assembly
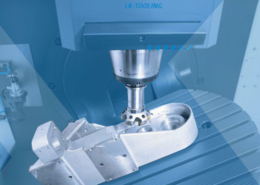