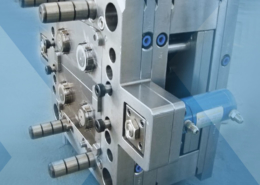
Top 10 Mould Manufacturing Companies in India - plastic molds and moldings pvt l
Author:gly Date: 2024-10-15
The simple answer is that making a successful injection mould tool is a hugely complex undertaking that require a lot of thought, planning, expertise and labour. The higher the complexity, the more expensive the cost of your mould will be. In this section, we break down the main factors that make up and impact the cost of an injection mould tool.
Huarong's innovative approach to two-platen machine design has resulted in several patents that optimize machine efficiency and performance. Their patented technologies include the Suspended Tie-bar Bearing Module, Patented Inner Supporting Sliding Module, Patented Moving Platen Positioning Device, and Optional Patented Tie-bar Disassemble Function, which won the prestigious Taiwan Excellence Award.
Several factors must be considered when deciding whether your part requires a large-ton machine. These factors include size, material, and safety considerations. Experts recommend adding a 10% safety factor to the clamping force calculation to accommodate potential defects. Key considerations to consider are part size and complexity, material type, projected annual volume, quality requirements, mold design, and seeking expert consultation.
Calculating the cost of your plastic injection moulding projectHow much will your injection moulding project cost? Upload your 3D drawings to our site contact form and include any project details like quantity, material or surface finish. Our team will get back to you with a quote which outlines the injection mould tool cost, the cost per part and total cost.
Several mould design decisions, such as side pull actions, number of cavities, texturing, multi-material shots, tight tolerances, engraving, undercut features, inserts, etc. will also significantly add to tooling costs. While costly, these design decisions may be a necessity or beneficial in the later stages of the process.
Various complex elements are made and assembled together using a range of manual and automated processes to form the injection mould or mould tool to guarantee a reliable and repeatable injection moulding process. These components are shaped to tight tolerances using specialist machinery, including CNC machining and EDM (electrical discharge machining), which significantly adds to the cost.
Gas-assisted injection molding (GAIM) is a technique that uses an inert gas, typically nitrogen, to help with the injection molding process. In GAIM, the gas is injected through air holes in the mold or the nozzle of the injection machine into the molten plastic within the mold, creating hollow sections in the part. This assists in pushing the molten plastic into the mold cavities, ensuring uniform filling and reducing internal stresses. By incorporating gas-assisted injection molding into their processes, manufacturers can achieve higher efficiency, better product quality, and reduced production costs, making it a valuable technique in large-part injection molding.
Large-part injection molding, also known as large-tonnage injection molding, shares similarities with standard injection molding but requires higher-tonnage injection molding machines (500 tons or more) to manage the increased clamping force needed for larger surface areas. Understanding the differences helps in selecting the right equipment and processes.
Injection moulds are subject to thousands of pounds of pressure every cycle and high levels of heat. As such, the moulds need to be made from strong, durable materials that can withstand the harsh operating conditions without deforming. These moulds are often made from different grades of steel or aluminium.
These machines offer cost-effectiveness, space efficiency, energy efficiency, suitability for large mold sizes, and flexibility in mold configurations. They have a smaller footprint than three-platen machines, making them ideal for limited-space environments.
Choosing the right material is crucial for the success of large part injection molding. Commonly used materials include:
The choice of material for the mould will likely depend on the number of parts to be produced. The more parts to be produced, the better and more expensive grade of steel should be used.
How much will your injection moulding project cost? Upload your 3D drawings to our site contact form and include any project details like quantity, material or surface finish. Our team will get back to you with a quote which outlines the injection mould tool cost, the cost per part and total cost.
Once the tooling process is complete, it’s important to note that injection moulding is an almost entirely automated process, compared to other forms of manufacturing methods. Hence allowing for an efficient and economical method of producing higher volumes of plastic parts — making the expensive initial injection mould cost highly worthwhile.
Large-part injection molding is a sophisticated manufacturing process for creating precision large-scale plastic components. This article delves into the details of this process, exploring various techniques, materials, and industry applications.
Cost is always a major consideration when you’re choosing the best manufacturing process for creating your plastic products. Unlike other manufacturing process like 3D printing and CNC machining, injection moulding requires a mould (tool) to make the parts, which involves a significantly higher start-up cost. The tool can cost from $10,000 or less to $100,000 depending on the material, size, complexity, and other factors, which can be a pretty big commitment.
Cost is always a major consideration when you’re choosing the best manufacturing process for creating your plastic products. Unlike other manufacturing process like 3D printing and CNC machining, injection moulding requires a mould (tool) to make the parts, which involves a significantly higher start-up cost. The tool can cost from $10,000 or less to $100,000 depending on the material, size, complexity, and other factors, which can be a pretty big commitment. So why are injection moulds so expensive?The simple answer is that making a successful injection mould tool is a hugely complex undertaking that require a lot of thought, planning, expertise and labour. The higher the complexity, the more expensive the cost of your mould will be. In this section, we break down the main factors that make up and impact the cost of an injection mould tool. 1. Material CostInjection moulds are subject to thousands of pounds of pressure every cycle and high levels of heat. As such, the moulds need to be made from strong, durable materials that can withstand the harsh operating conditions without deforming. These moulds are often made from different grades of steel or aluminium. The choice of material for the mould will likely depend on the number of parts to be produced. The more parts to be produced, the better and more expensive grade of steel should be used. 2. Mould ConstructionVarious complex elements are made and assembled together using a range of manual and automated processes to form the injection mould or mould tool to guarantee a reliable and repeatable injection moulding process. These components are shaped to tight tolerances using specialist machinery, including CNC machining and EDM (electrical discharge machining), which significantly adds to the cost. 3. Mould Complexity & AestheticsSeveral mould design decisions, such as side pull actions, number of cavities, texturing, multi-material shots, tight tolerances, engraving, undercut features, inserts, etc. will also significantly add to tooling costs. While costly, these design decisions may be a necessity or beneficial in the later stages of the process. 4. Labour CostsDon’t forget to factor in labour costs. Designing, creating and assembling injection moulds is a labour-intensive and complex process that takes time and skill to do correctly. Injection mould builders and designers are highly trained specialists that don’t come cheap. If you cheap out on this, you might have to pay for the costs later on. Is injection moulding actually expensive?Once the tooling process is complete, it’s important to note that injection moulding is an almost entirely automated process, compared to other forms of manufacturing methods. Hence allowing for an efficient and economical method of producing higher volumes of plastic parts — making the expensive initial injection mould cost highly worthwhile.In fact, plastic injection moulding is often found to be one of the cheapest manufacturing processes when taking into consideration the total manufacturing cost for projects involving higher volumes. Read the full cost comparison of injection moulding versus 3D printing. Is it possible to get inexpensive injection moulds?For smaller production runs or niche markets, the high cost of traditional injection moulding tools often made from hardened steel, which can cost several tens of thousands of dollars, may not be justifiable. In such scenarios, rapid tooling can be a more cost-effective alternative. There are several forms of rapid tooling: Aluminum Tooling: Aluminum moulds are cheaper and faster to produce than steel moulds. They are suitable for producing a few thousand parts, making them ideal for low-volume production and prototyping.Soft Steel Tooling: Softer steels can be used to create moulds at a lower cost than fully hardened steels. These moulds can still handle a reasonable production volume but are less durable than hardened steel moulds.3D Printed Moulds: Advances in 3D printing technology allow for the creation of moulds directly from CAD models. Though not as durable or precise as aluminium or steel moulds, they can be useful for quick prototyping and very low-volume production. Read the full guide to rapid tooling in injection moulding.
The two-platen injection molding machine is ideal for medium—and large-sized machines. It features a unique design with two platens holding the mold halves during injection. Unlike traditional three-platen machines, this design is compact and efficient, ensuring precision and efficiency in molding large plastic products.
Large-tonnage injection molding machines are vital for producing large parts. These machines, rated by their clamping force, ensure the mold halves remain securely closed during injection. Proper tonnage calculation is crucial to prevent defects and ensure high-quality output.
Next news : Success Stories: How Elevate South African Manufacturer's Manufacturing Capabilities with Cutting-edge Two-platen Machine
For smaller production runs or niche markets, the high cost of traditional injection moulding tools often made from hardened steel, which can cost several tens of thousands of dollars, may not be justifiable. In such scenarios, rapid tooling can be a more cost-effective alternative. There are several forms of rapid tooling:
Don’t forget to factor in labour costs. Designing, creating and assembling injection moulds is a labour-intensive and complex process that takes time and skill to do correctly. Injection mould builders and designers are highly trained specialists that don’t come cheap. If you cheap out on this, you might have to pay for the costs later on.
Large part injection molding is an indispensable process in modern manufacturing, offering numerous benefits across various industries. By understanding the techniques, machinery, and materials involved, businesses can enhance their production capabilities and achieve superior product quality. As the leading plastic injection molding machine manufacturer, Huarong is committed to providing all our clients with precision, custom plastic injection molding services that deliver premium quality components. If you have any further questions or machine needs, please don't hesitate to contact Huarong.
In fact, plastic injection moulding is often found to be one of the cheapest manufacturing processes when taking into consideration the total manufacturing cost for projects involving higher volumes. Read the full cost comparison of injection moulding versus 3D printing.
Large-part injection molding finds extensive applications across various industries, offering unparalleled advantages in producing oversized plastic components.
GETTING A QUOTE WITH LK-MOULD IS FREE AND SIMPLE.
FIND MORE OF OUR SERVICES:
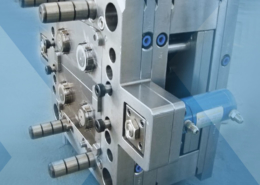
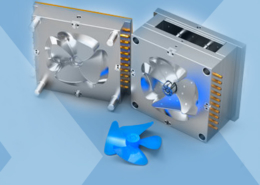
Plastic Molding

Rapid Prototyping
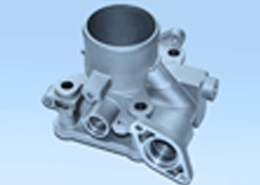
Pressure Die Casting
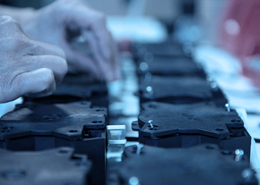
Parts Assembly
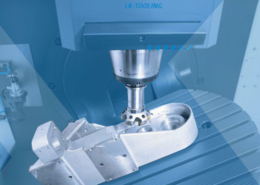