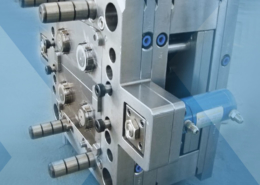
Top 10 Injection Molding Companies in China - chinese injection molding companie
Author:gly Date: 2024-10-15
7. **Quality Control:** The caps are inspected for quality and consistency to ensure they meet the desired specifications.
Since 1988, Advanced Plastiform, Inc., has been providing superior custom plastic molding and fabrication services to companies in North Carolina, South Carolina, Maryland, Georgia and Pennsylvania. Contact us to make an appointment Mon-Fri 8-5.
Overall, injection molding is a versatile and widely used method for producing plastic caps, and PLA is a suitable material choice for environmentally friendly and biodegradable cap applications.
Unlock the potential of HIPS - where proven success meets unmatched durability and precision in high-quality plastic manufacturing.
6. **Trimming and Finishing:** The caps may undergo additional processes, such as trimming excess material and adding any necessary finishing touches or features like threads for screw caps.
Yes, an injection molding machine can produce caps made from PLA (Polylactic Acid) plastic. Injection molding is a common manufacturing process used to produce a wide range of plastic parts and products, including caps and closures.
High impact polystyrene is affordable, versatile, and makes an excellent choice for many of the products we manufacture. With the best materials and innovative equipment and technology, we’re a leading plastics manufacturer, serving businesses across North Carolina, South Carolina, Pennsylvania, Maryland, Tennessee, Georgia, and Virginia.
2. **Melting:** The PLA material is fed into a heating chamber where it is melted at high temperatures. PLA has a relatively low melting point compared to some other plastics, which makes it suitable for injection molding.
At Advanced Plastiform, Inc. we work hard to provide our customers with durable, long-lasting plastics that offer the qualities they need while keeping lead times fast and prices low. In order to achieve the best results, we take care to match the most suitable thermoplastic to the project. One of those plastics we offer is high impact polystyrene, also known as HIPS.
4. **Cooling:** After injection, the mold is cooled rapidly to solidify the PLA. The cooling time can vary depending on the size and complexity of the cap.
3. **Injection:** Once the PLA material is molten, it is injected under high pressure into a mold cavity. The mold is designed to shape the melted PLA into the desired cap shape.
1. **Material Preparation:** PLA pellets or granules are loaded into a hopper attached to the injection molding machine. PLA is a biodegradable and biocompatible thermoplastic derived from renewable resources like cornstarch or sugarcane.
Once heated, HIPS is highly malleable, meaning high-impact polystyrene thermoforming is an excellent way to manufacture the plastics our customers need. To do this, large sheets of HIPS are heated and fitted over a custom tool. Then, to achieve the ideal shape and design, we use one of three methods to complete the thermoforming process.
It's worth noting that PLA has certain characteristics that may require specific considerations during the injection molding process. For example, PLA can be more brittle than some other plastics, so mold design and process parameters may need to be adjusted accordingly to prevent defects like warping or cracking. Additionally, PLA is sensitive to moisture, so proper storage of PLA pellets is important to maintain material integrity.
HIPS injection molding is ideal for small plastic parts and products, especially those needed in large quantities, or parts that need high levels of detail or variable thickness. While the tooling cost is higher with injection molding than thermoforming, we strive to deliver affordable tooling designs that, once created, can be used for additional orders in the future. This means that for high unit requirements, the per-unit cost is very low.
Vacuum forming is used for large plastic pieces that don’t need high levels of detail or sharp corners or edges. While it is the most basic method of thermoforming, it’s also quick and affordable. Once the plastic is heated and fitted to the tool, a powerful vacuum is fitted between the tool and the plastic, suctioning out all air from between the two and pulling the thermoplastic firmly against the tool, creating an accurate shape. HIPS vacuum forming is often used to produce refrigerator liners and boat hulls.
When defined edges, corners, and detailing is necessary, we use pressure forming. Like vacuum forming, we fit heated HIPS around a tool, but then, we use highly pressurized air to blast the plastic, pressing it firmly against the tool. Using air pressure uses three times the force of vacuum forming, creating a high level of detail. Pressure forming with HIPS is so precise, it can often be used in place of injection molding and is often used in creating automobile parts, including instrument panels and electronic equipment.
Twin sheet forming is the most complex high impact polystyrene thermoforming method. We heat two sheets of HIPS simultaneously, then fit and fuse them together. While it sounds simple, great care must be taken to make sure the two pieces are able to fuse together at the pressed points. This method is used to create hollow and double-walled industrial products. Gas cans and air ducts can be made by twin sheet forming HIPS.
While general-purpose polystyrene is lightweight, clear, and brittle, HIPS benefits from rubber additives to make it much more is much more flexible and improve its impact strength. Though it has an opaque appearance, it can be painted, labeled, and designed with ease.
Injection molding works by melting the high impact polystyrene into a liquid, then injecting it into the double-sided mold with extremely high pressure. Once it’s cooled and solid, the product is painted, labeled, or coated as needed.
GETTING A QUOTE WITH LK-MOULD IS FREE AND SIMPLE.
FIND MORE OF OUR SERVICES:
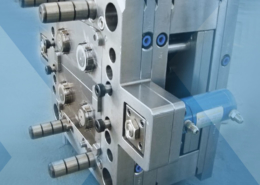
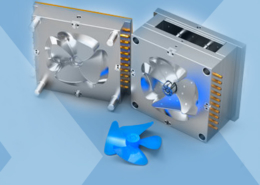
Plastic Molding

Rapid Prototyping
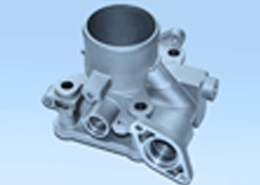
Pressure Die Casting
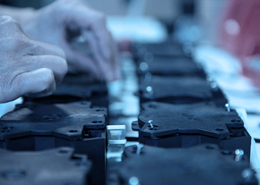
Parts Assembly
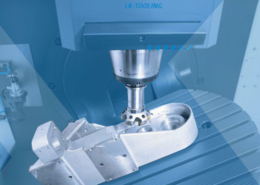