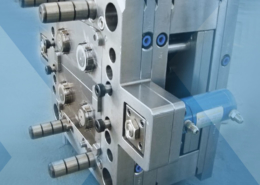
Top 10 Injection Molding Companies In Australia | MadeAria - injection companies
Author:gly Date: 2024-10-15
Short run injection molding does not significantly restrict resin requirements due to the mold material. It allows for utilizing a wide range of resins available in higher volume molding processes. Material selection plays a critical role in determining the final product's quality, durability, and performance. Factors such as environmental conditions and specific requirements need to be considered when choosing the appropriate material. By carefully selecting the right material and considering design limitations, companies can ensure that the chosen material meets all necessary requirements while remaining cost-effective.
HDPE, in its pellet form, can be a magnet for moisture. Before molding, it’s imperative to ensure the resin is dry. Moisture can lead to weak spots, compromising the product’s integrity. I’ve witnessed this firsthand and can’t stress enough the importance of thorough pre-drying.
In my years of experience, I’ve found HDPE’s chemical resistance to be quite impressive. The material, with its high density, resists corrosion and withstands many chemicals, making it a favorite for industrial applications. Imagine a knight in shining armor, unperturbed by the surroundings—that’s HDPE for you.
As a seasoned technician, I’ve seen how HDPE molding holds its own against other plastic resins. It emanates high tensile strength and low cost, giving it an edge over its cousins. In the world of injection molding, HDPE resin is like a reliable workhorse—consistent and trustworthy. It molds into an assortment of consumer products, displaying versatility that other plastics could only aspire for.
By leveraging our advanced products experienced team, and commitment to excellence, we aim to make your production processes more efficient, cost-effective, and responsive to market demands. Contact us today to explore how our short run injection molding products can empower your business to create precise, high-quality parts quickly and easily.
Short run injection molding finds application in various industries. Still, four key sectors stand out for reaping significant benefits from this manufacturing process: the automotive industry, the electronics industry, the medical device industry, and the packaging industry.
Too fast, and you risk trapping air; too slow, and you might not fill the mold completely. The dance with the injection molding machine is one of nuance and subtlety, with the right rhythm resulting in impeccable HDPE parts.
When considering short run injection molding solutions, several factors come into play. These include cost factors and budget considerations, design limitations, material selection, and the use of the right molding products.
The high strength and impact resistance of HDPE are tales of legend in our industry. From rugged playground equipment to durable storage containers, HDPE molding shapes these items with the promise of enduring wear and tear. The words “high strength” and “low cost” often don’t share the same sentence, yet HDPE melds these together harmoniously.
While HDPE’s advantages in the manufacturing process are undeniable, it’s essential to address the challenges that come with it.
And yet, amidst all its strength, HDPE moulding doesn’t turn a blind eye to our planet. Its recyclability is commendable. From milk jugs to detergent bottles, HDPE parts, once they’ve served their purpose, are reborn in the crucible of recycling. A commitment to the environment, one could say.
Step into any American household, and you’ll witness HDPE’s ubiquity. From milk crates to food storage containers, this versatile thermoplastic polymer seamlessly blends into our lives. HDPE plastic bottles, often overlooked, are silent testimonies to the material’s wide range of industries and applications.
Designing for HDPE injection molding is an art. The right wall thickness ensures structural integrity without wastage. There’s an old adage among us technicians: “Design is not just what it looks like. Design is how it works.” This rings true, especially when considering how uniform wall thickness can prevent sink marks and voids.
Designing with foresight, incorporating generous radii and draft angles, can make the ejection process smoother. An elegant curve not only enhances aesthetics but also adds to the structural strength, while draft angles prevent part sticking, ensuring the HDPE parts release effortlessly from the mold cavity.
Many companies struggle with finding efficient ways to produce high-quality components in small quantities. Traditional injection molding processes may not be suitable due to high tooling costs, extended lead times, and the need for large production volumes. These limitations often hinder the ability to respond quickly to market demands, leaving businesses at a disadvantage.
In the sprawling landscape of thermoplastic polymers, High Density Polyethylene, or HDPE moulding, stands as a titan. Its molecular architecture—a long chain of carbon atoms bonded to hydrogen—imbues it with properties that have ushered in a revolution across various industries. While discussing chemical compositions might seem like traversing a mundane path, HDPE surprises us with its simplicity and strength. It’s akin to the minimalism in an art masterpiece: unassuming yet profound.
One of the primary concerns with HDPE parts is their high coefficient of thermal expansion. As the injection molding process inherently generates heat, HDPE tends to expand. This expansion, when followed by cooling, can lead to warping or distortion, compromising the aesthetic integrity of the final product. It’s a dance of heat and shape, where the rhythm can sometimes go awry.
Utilizing the right molding products is crucial to enhance the short run injection molding process. Mold sealers are commonly used to fill in the microporosity of molds, resulting in an even finish on the molded parts. Mold release agents aid in easily releasing items from the mold after the molding process is complete. Mold cleaners help maintain the cleanliness and longevity of molds, ensuring optimal performance over multiple production cycles.
Diving into the economic canvas, HDPE injection molding stands out as an excellent choice due to its cost-effectiveness. Manufacturing products in large quantities using HDPE injection molding machines taps into economies of scale. It’s like watching a symphony of efficiency: HDPE plastic molding reduces labor costs while ensuring production efficiency.
By considering these factors and leveraging the benefits of short run injection molding, companies can achieve efficient and cost-effective production for their customized components prototypes.
Here's where short run injection molding offers a breath of fresh air. By leveraging advanced technologies and skilled expertise, short run injection molding provides a cost-effective and efficient solution for small-scale production. With reduced tooling costs, quick turnaround times, and the ability to produce quality parts in the thousands or even just a few hundred, short run injection molding empowers companies to respond swiftly to market demands, effectively manage product development, and seize opportunities.
The electronics industry benefits from short run injection molding through rapid prototyping and quick production of consumer electronics. This fast-paced process allows companies to test and validate product designs before committing to large-scale manufacturing. Unlike 3D prototyping, which often limit sample quantities, short run molding offers the ability to produce more samples in less time, providing greater flexibility for design iterations and improvements.
With a clear understanding of HDPE’s strengths and areas for improvement, we can better appreciate its role in various industries and applications.
Safety is paramount. HDPE’s vulnerability to high temperatures can be a concern, especially when exposed to flames. But, as with many materials, science offers a remedy. By incorporating flame retardants into the HDPE mold, we can significantly reduce its flammability, ensuring both the safety of the manufacturing process and the end product.
Short run injection molding refers to a manufacturing process that specializes in producing plastic parts in small quantities, typically ranging from a few hundred to a few thousand units. It offers a cost-effective solution for companies that require rapid prototyping, low-volume production, or customized components. In this process, a mold is created, and thermoplastic materials are injected into the mold cavity under high pressure. The mold is opened once the material cools and solidifies, and the finished part is ejected.
It’s frustrating to have a brilliant product idea or a new project that requires rapid prototyping or small-batch production, but not having the capability to produce the test product. The lengthy and costly tooling process associated with conventional injection molding can be a significant roadblock, hindering innovative product development and market entry. Production delays can result in missed opportunities and potential loss of customers and market share.
In the medical device industry, where stringent regulations and precision are paramount, short run injection molding accelerates the development process for medical devices. It enables cost-effective production of small-batch components, making it suitable for niche applications or specialized medical devices that require limited quantities. Short run molding ensures high quality and reliability while meeting tight timelines and maintaining compliance with regulatory standards.
Unlike many mold release brands, Stoner Molding Solutions formulates, manufactures, and distributes our own products. Check out our full line of mold releases, sealers, cleaners, rust preventatives, and lubricants. In stock products are ready to ship now!
HDPE, though a marvel, isn’t devoid of quirks. Shrinkage and warping are perennial challenges. But with intuition and experience, it’s possible to predict these behaviors. Design modifications and process adjustments can counteract these potential pitfalls, ensuring the end product remains true to its intended form.
In the automotive industry, short run injection molding plays a vital role in customizing parts for specific models. It enables manufacturers to produce limited quantities of high-quality components with precision, ensuring a perfect fit and finish. This top-tier quality is particularly valuable for luxury and exotic car manufacturers who offer high-end vehicles in limited numbers. By leveraging short run molding, they can maintain exceptional quality standards while meeting the demand for exclusivity.
The automotive sector, ever-evolving and always on the move, has embraced HDPE molding. Car components, molded with precision, take advantage of HDPE’s impact resistance and low thermal conductivity. This has paved the way for lighter vehicles, translating into improved fuel efficiency. A simple injection molded HDPE part can play a pivotal role in this vast machinery of movement.
Looking to kick off your injection mold work? Pick ACO Mold! We’re all about using a bunch of different plastics for injection molding. Think HDPE, ABS, PP, PE—you name it. Got questions? Just hit us up. Our pros at ACO Mold are here to hook you up with everything you need, all in one place!
The packaging industry benefits from short run injection molding by enabling the creation of unique packaging designs for limited-edition products. It allows companies to meet specific packaging requirements for new product launches, ensuring eye-catching and functional packaging solutions. Short run molding provides the flexibility to produce a limited number of parts while keeping options open for future design changes or additions.
The industrial landscape is painted with HDPE’s footprints. From pipe thread protectors to industrial products that demand high strength and chemical resistance, HDPE moulding has found its niche. Reflecting upon the numerous projects I’ve worked on, HDPE’s adaptability to complex geometries and its compatibility with large-scale production never cease to amaze.
HDPE’s low surface energy makes it a bit of a lone wolf, resisting bonding with other materials. This characteristic can pose challenges in processes requiring adhesion, such as overmolding. However, every challenge has its solution. In this case, specialized adhesives designed explicitly for HDPE can bridge the bonding gap, ensuring a firm union between HDPE and other components.
The advantages and benefits of short-run injection molding are numerous. First, it allows for quick turnaround times, enabling companies to bring their products to market faster. This fast process is particularly advantageous for industries where time-to-market is crucial. Additionally, short run injection molding is a cost-effective solution, eliminating the need for expensive tooling and molds associated with larger production runs. Companies with limited budgets can benefit from this approach without compromising on quality. Furthermore, this process allows flexibility and agility in design iterations and product improvements, making it ideal for companies that value innovation and adaptability.
As I ponder the vast expanse of the injection molding world, HDPE emerges as a beacon of promise. Its versatility, coupled with its economic advantages, places it at the forefront of consumer and industrial applications. While challenges persist, the path forward for HDPE moulding is bright, fueled by innovation and an ever-growing demand. The tapestry of the past interwoven with the threads of the future makes HDPE molding an attractive option for generations to come.
Short run injection molding provides a game-changing solution for companies seeking efficient and cost-effective manufacturing processes for small-scale production. We have explored the numerous benefits of this innovative technique, from its ability to meet the demands of various industries to its flexibility in customization and rapid prototyping.
Short run injection molding offers cost advantages compared to larger production runs. Since fewer parts are required, less expensive mold materials such as aluminum or lower steel grades can be used, reducing tooling costs. With lower upfront costs, short run injection molding becomes accessible to a broader range of customers with smaller budgets. Additionally, adjustments and modifications can be made without significant financial commitments, and prototypes may require less finishing than in 3D printing, saving both time and cost.
Mastery over the injection molding machine parameters is paramount. Balancing the melt temperature, injection speed, and pressure can make all the difference between an average and an outstanding product. As they say, “The devil is in the details.”
Transitioning from the challenges, let’s delve into the myriad applications of HDPE, showcasing its versatility. But before that, here’s a table juxtaposing the advantages and challenges of HDPE:
Comparing it to its sibling, LDPE, HDPE is denser and possesses higher temperature resistance. From food storage containers to medical applications, HDPE parts have become the backbone of countless products. It’s remarkable how this versatile material effortlessly adapts to the shape of the mold, catering to a wide range of applications.
GETTING A QUOTE WITH LK-MOULD IS FREE AND SIMPLE.
FIND MORE OF OUR SERVICES:
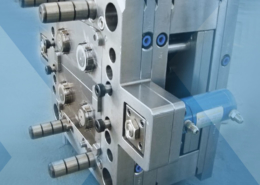
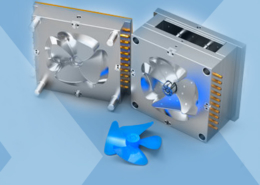
Plastic Molding

Rapid Prototyping
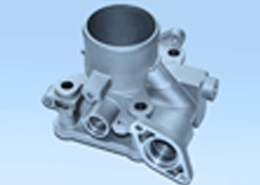
Pressure Die Casting
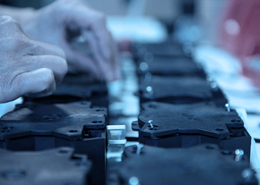
Parts Assembly
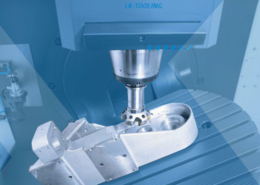