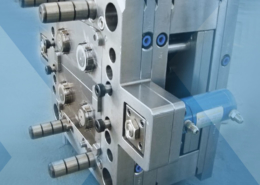
Top 10 Injection Mold Companies in Australia - injection mold fabrication
Author:gly Date: 2024-10-15
A Plus Plastics manufactures a diverse range of products, including automotive parts, consumer goods packaging, industrial containers, and building materials. The company leverages advanced automation and robotics in its production processes, significantly enhancing efficiency and precision.
Plasticut specializes in plastic fabrication and injection molding, with a strong emphasis on precision and quality in mold injection. Their core business involves the design, production, and supply of precision CNC machined plastic parts for industries such as medical, aerospace, and industrial machinery.
With a strong focus on innovative design and stringent quality control, B&C Plastics guarantees that each product meets the highest standards, fulfilling client needs and expectations.
B&C Plastics is a leading Australian plastic injection molding company specializing in the design, manufacture, and supply of custom plastic products. Their core business spans the entire process from concept design to final production, providing comprehensive end-to-end services to clients.
Known for handling complex molding projects, A Plus Plastics delivers high-quality, tailored solutions to meet various industry requirements. Their commitment to sustainability, innovation, and superior customer service ensures that each product not only meets but exceeds client expectations.
Amec Plastics is a leading company specializing in mold injection and plastic extrusion. Their core business involves the design, engineering, and production of custom plastic components and extruded profiles for a wide range of industries, including automotive, industrial, and construction.
Plastral is a leading company specializing in the distribution and fabrication of high-quality plastic materials, with a strong focus on mold injection. Their core business involves supplying plastic sheets, rods, and tubes, along with offering custom plastic fabrication services for a wide range of applications.
Romar Engineering specializes in advanced manufacturing solutions with a focus on mold injection. Their core business encompasses the design, development, and production of high-precision molds and plastic components for medical, aerospace, and industrial sectors.
Melro specializes in durable rotational molding, and ADDE uses advanced CAD/CAM technologies. Plasticut leads in CNC machining, and Plastral provides extensive material distribution and custom fabrication.
ACIS®, Autodesk Inventor®, CATIA® V5,Creo™ Parametric, IGES, Parasolid®, Pro/ENGINEER®,Siemens PLM Software’s NX™, SolidEdge®, SolidWorks®, STEP
Main Services: Specializes in the design and manufacturing of rotomoulded plastic products, including water tanks and custom mouldings, as well as injection moulding services.
Vacuum drying is the best means of drying nylon. Appropriate drying conditions are a temperature of 80-120°C and a vacuum pressure of 1013 hPa. Drying time should be 10 to 48 hours, depending on the pellet water content. Removing pellets from the dryer immediately after high-temperature drying and transferring the pellets to a container could result in oxidation or discoloration. Instead, reduce the temperature to below 70°C under vacuum before transferring the pellets. Figure 1.5 shows an example of a vacuum-drying curve for nylon.
Main Services: Offers plastic fabrication, injection moulding, and material supply services for industrial and commercial applications.
Specializing in the design, engineering, and production of precision molds and plastic components, ADDE serves diverse industries with expertise. Their products include intricate electronic device housings, sophisticated medical equipment parts, and high-quality consumer components.
Forme Technologies excels in creating intricate medical device components, precise automotive parts, and durable consumer goods. Utilizing advanced mold injection techniques and precision engineering, they ensure superior quality and consistency.
By integrating advanced mold injection processes, Romar Engineering consistently meets exacting client standards, showcasing superior craftsmanship and specialized capabilities. This dedication to excellence and innovation positions them as a leader in mold injection and advanced manufacturing.
Romar Engineering’s products include intricate medical device parts, critical aerospace components, and robust industrial machinery parts. Utilizing cutting-edge technologies like 3D printing and advanced mold injection techniques, they deliver innovative and high-quality products. Their expertise in mold design, commitment to continuous improvement, and rigorous quality control distinguish them in the industry.
Main Services: Provides high-quality plastic injection moulding services, product design and development, and precision toolmaking.
Nylon is a crystalline polymer that absorbs moisture, so be mindful of the following points when attempting to mold nylon.
After opening the bag, nylon pellets will absorb moisture through exposure to the air. The rate of water absorption and the level of equilibrium water absorption are influenced by factors such as the type of nylon, the amount of reinforcement agents (such as glass fibers) added, the shape of the pellets and the air temperature and humidity. Figure 1.2 shows the relative humidity and atmospheric equilibrium water absorption for each nylon type. To find the equilibrium water absorption of reinforced nylons, discount the corresponding equilibrium water absorption value by the water-absorption rate of the reinforcement agent per weight percentage used. Figures 1.3 and 1.4 show the rate of water uptake in representative types of nylon pellets when exposed to the atmosphere. Based on these data, you can see the nylon pellets exhibit a fast rate of water uptake in hot and humid environments. If pellets have absorbed water beyond a certain threshold, using those pellets in a molding process could result in appearance problems such as silver streaking on the surface of the molded product and voids on the inside of the molded product, as well as sacrificed properties resulting from lower molecular weight. Water content of about 0.15% to 0.2% is preferred in nylon pellets used in injection molding. Take the following steps to ensure proper water content levels.
Compare quotes considering price, service, quality, and delivery time. Select the best-fit supplier and sign a detailed contract.
The company’s ability to customize products to specific client requirements showcases their expertise in mold manufacturing. With a professional design and engineering team, Melro delivers innovative and high-quality products, making them a trusted name in the industry.
Known for innovation and rigorous quality control, Forme Technologies delivers customized solutions tailored to client needs, positioning them as a leader in the plastic manufacturing industry.
Their commitment to innovation and quality assurance underscores their leadership in mold manufacturing, exemplifying superior craftsmanship and specialized capabilities.
Visit the factories, if possible, to understand their processes and meet with representatives to discuss project details and cooperation terms.
Maintain regular communication with the supplier, conduct quality inspections, and provide feedback upon project completion to ensure quality and establish future cooperation.
Main Services: Plastic Injection Moulding, 2 shot moulding (Over Moulding), Rapid Prototyping, CNC Machining, 3D Printing
Plastral’s product offerings include industrial components, signage materials, and construction plastics. Utilizing advanced fabrication techniques and technologies, Plastral ensures precision and consistency in every product.
A Plus Plastics is a premier Australian company specializing in the design and production of high-performance plastic components. Their core business includes offering comprehensive injection molding solutions that span from initial concept design to full-scale production.
The company’s ability to handle complex projects and provide customized solutions underscores their innovative approach and stringent quality control. By focusing on mold injection, Plasticut consistently sets industry standards, showcasing their superior craftsmanship and specialized capabilities. This commitment to excellence makes Plasticut a leader in the plastic fabrication and mold injection industry.
Toray nylon resin is manufactured under rigid quality control standards and packaged in sealed moisture-resistant bags. Therefore, pellets taken from the bag do not need to be pre-dried as long as the pellets are used immediately after opening the bag. As long as the bag is free of damage, the pellets should absorb virtually no moisture during storage. Please handle the pellet bags with care so as to prevent damage to the bag and avoid storing the bags in places with exceptionally high levels of humidity.
Amec Plastics stands out for their innovative approach and stringent quality control, providing customized solutions that meet specific client needs. Their expertise in mold injection and commitment to continuous improvement and customer satisfaction position Amec Plastics as a leader in the plastic manufacturing industry.
Figures 1.9 and 1.10 show drying curves achieved by dryers equipped with a dehumidifier. The dehumidifier removes moisture from the intake air. That dry air is then heated and circulated within the heater as hot air, constantly exposing the pellets to hot, dry air. This method is preferred, as it eliminates risks such as the seasonality referred to above. However, as always, be careful to avoid oxidation or discoloration. Furthermore, dehumidifiers have limited capacity to remove moisture, so remain vigilant in keeping pre-dried nylon pellets as dry as possible.
To recycle sprues, runners and other materials, the material to be recycled must be stored in dry conditions or dried appropriately before injection-molding. The properties of the recycled material will change as the material is subject to thermal history. Furthermore, in the case of reinforced materials, reinforcement agents may be damaged upon exposure to shearing force during the molding process. Generally, recycling results in diminished mechanical strength, while electrical, sliding, sintering and chemical resistance properties remain unchanged. Figures 1.11 and 1.12 show the change in properties in recycled non-reinforced nylon 6 and nylon 66. Similarly, Figures 1.13 through 1.22 show the same for recycled glass-fiber reinforced nylon 6 and nylon 66. See the following for detailed conditions used.
B&C Plastics produces a wide range of products, including industrial components, consumer goods housings, medical device parts, and complex-shaped injection molded parts.
By integrating mold injection into their services, Plastral sets the benchmark for excellence in plastic fabrication, emphasizing their superior craftsmanship and specialized capabilities. This dedication to quality and innovation positions Plastral as a leader in the plastic fabrication and mold injection industry.
Main Services: Provides plastic injection moulding, product design and development, and precision toolmaking services for medical, automotive, and consumer products.
Clearly outline your product specifications, materials, quantity, budget, deadline, and quality requirements before searching for suppliers.
Aside from tensile breakdown elongation, the non-reinforced product maintains nearly 100% of its properties. Test samples show that the glass-fiber reinforced product retains at least 90% of its properties (with the exception of impact strength) when recycled material content does not exceed 20%. However, before using recycled materials, implement rigid controls on the recycled material and determine the appropriate recycled material content level based on sufficient consideration of the products' required properties. Furthermore, during the crushing process, fine particles from the cutter blade could contaminate the recycled material, so use particular caution in compact electrical component applications. Otherwise, fine particle contaminants could destabilize the molding process; be sure to remove the contaminants in such cases. Underwriters Laboratories Standard 746D states that UL-certified materials may contain in-process recycled material of up to 25% by weight. Products containing more than 25% recycled material are to be certified after confirmatory tests conducted by UL.
Romar Engineering and Forme Technologies excel in high-precision mold injection for medical and aerospace sectors. Amec Plastics combines mold injection with extrusion for industrial solutions, and Rapid Plastics Australia specializes in rotational molding for durable storage.
Australia’s manufacturing industry is robust and dynamic, with plastic injection moulding playing a crucial role. This advanced process is essential for producing a wide variety of plastic products, from everyday items to specialized industrial components.
Reach out to the shortlisted companies with your design drawings and request quotes. Inquire about additional services like design support and quality control.
Figure 1.6: Hot-air blow-drying conditions and equilibrium water absorption of nylon pellets (drying temperature: 80°C)
Conduct industry research to find Australian plastic injection molding companies. Read reviews and case studies, then create a shortlist of potential suppliers.
Their core business serves agricultural, industrial, and commercial sectors, producing durable water storage tanks, chemical storage containers, and custom-molded products. Utilizing advanced mold injection and rotational molding technologies, Rapid Plastics Australia ensures superior strength, consistency, and precision in their products.
Utilizing advanced precision injection molding technology, the company ensures consistency and high accuracy in every product. Additionally, B&C Plastics excels in rapid prototyping, swiftly turning concepts into physical models, thereby reducing product development cycles.
Main Services: Specializes in the design, tooling, and manufacturing of high-quality plastic injection-molded products, offering services such as custom molding, prototyping, and sub-assembly for various industries.
ADDE is a premier Australian firm renowned for its excellence in plastic injection molding, especially in Australian mold injection.
Evaluate the shortlisted companies based on experience, certifications, technology, production capacity, quality, service, and delivery timelines.
Utilizing advanced CAD/CAM technologies, ADDE ensures optimal performance and durability in their molds. Known for managing large-scale production and complex mold designs, ADDE offers bespoke solutions tailored to client needs.
Melro is a specialized Australian company renowned for its production of rotationally molded plastic products. Their core business focuses on the design, manufacture, and supply of high-strength, durable plastic solutions for various industrial applications.
Forme Technologies specializes in high-precision mold injection and plastic component manufacturing. Their core business provides comprehensive solutions from concept design to full-scale production for medical, automotive, and consumer product industries.
The company’s ability to deliver customized solutions tailored to specific industry needs highlights their innovative approach and commitment to quality.
These companies exemplify the best of Australian manufacturing capabilities, driving the industry forward and ensuring Australia’s position as a key player in the global manufacturing arena.
Australia’s injection molding industry features ten exemplary companies, each offering unique strengths. B&C Plastics excels in precision and rapid prototyping, while A Plus Plastics focuses on sustainable, automated solutions.
Main Services: Specializes in the design, manufacturing, and delivery of rotomoulded plastic products, including water tanks and custom mouldings.
There are many variables that must be considered when choosing the right injection molding supplier for your business. Here are five key steps you can take to ensure the best decision for your company:
Melro’s product range includes large water storage tanks, chemical storage containers, and agricultural equipment. Utilizing advanced rotational molding technology, Melro ensures that each product is robust, reliable, and meets exacting standards.
The sector has experienced significant growth, with companies investing in state-of-the-art machinery and sustainable practices. Key applications include automotive, medical, food packaging, and consumer goods, offering efficiency, precision, flexibility, and sustainability.
Main Services: Specializes in CNC machining, plastic fabrication, and injection moulding services for various applications.
Main Services: Specializes in plastic injection moulding, tooling, and engineering services, providing high-quality and innovative solutions for a wide range of industries.
A hot-air dryer, a hopper dryer or either of these equipped with a dehumidifier can be used in hot-air blow-drying. The degree of drying achieved through hot-air blow-drying is determined by the pellet shape, initial and final water content, drying temperature and the temperature of and relative humidity of the dryer intake air. Figure 1.6 shows the relationship between the state of the dryer intake air and the pellet equilibrium water absorption after using a hot-air dryer on nylon pellets at 80°C. As you can see, the degree of drying achieved is determined by the absolute humidity (water content) of the dryer intake air. Ordinary hot-air dryers and hopper dryers intake air directly from the atmosphere. Therefore the degree of drying achieved is controlled by the relative humidity in the atmosphere, which could easily result in seasonal variance. Drying pellets already low in moisture content could result in higher moisture content, and it may be difficult to achieve sufficient drying in hot and humid environments. To achieve better drying, use a higher drying temperature and a longer drying time. However, note that the extent to which the drying temperature can be raised is limited by the risk of oxidation or discoloration when using high temperatures to perform hot-air blow-drying. Figure 1.7 shows the change in coloration of nylon pellets when hot-air blow-dried at different drying temperatures and durations. Using an ordinary hot-air blow dryer, the drying temperature should be no higher than 80-90°C to prevent oxidation or discoloration. Figure 1.8 shows the hot-air blow-drying curve of nylon pellets. As you can see, excessive water uptake prevents sufficient drying within a short period of time when drying at temperatures low enough to mitigate the risk of oxidation or discoloration.
Main Services: Specializes in silicone injection moulding, precision engineering, and advanced 3D printing for medical and industrial sectors.
The company is known for its innovative solutions, stringent quality control, and ability to deliver customized products tailored to specific client needs. Their expertise in mold injection and commitment to excellence make Rapid Plastics Australia a leader in the plastic manufacturing industry, setting benchmarks for quality and reliability.
Plasticut’s product range includes intricate medical device components, high-precision aerospace parts, and durable industrial machine components. Utilizing advanced CNC machining technology, Plasticut ensures exceptional accuracy and quality in their products.
Rapid Plastics Australia specializes in the design, production, and supply of high-quality rotationally molded plastic products, with a strong emphasis on mold injection techniques.
In this article, we highlight ten leading plastic injection moulding companies in Australia known for their innovation, quality, and exceptional customer service.
Amec Plastics is known for its ability to produce high-precision industrial components, durable automotive parts, and robust construction materials. By utilizing advanced mold injection techniques and state-of-the-art extrusion technologies, they ensure exceptional accuracy and quality in their products.
GETTING A QUOTE WITH LK-MOULD IS FREE AND SIMPLE.
FIND MORE OF OUR SERVICES:
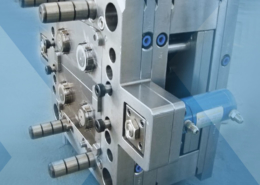
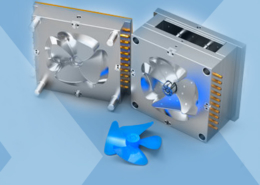
Plastic Molding

Rapid Prototyping
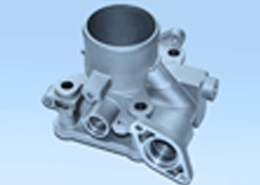
Pressure Die Casting
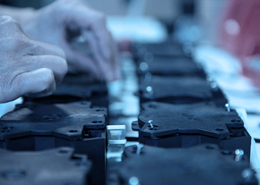
Parts Assembly
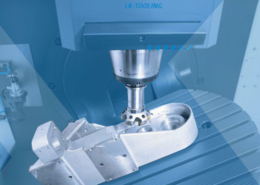