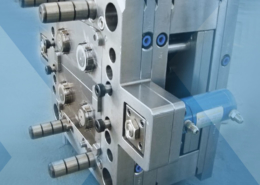
Top 10 Chinese Injection Molding Companies: Affordable ... - largest injection m
Author:gly Date: 2024-10-15
Resin pellets are loaded into a barrel where they will eventually be melted, compressed, and injected into the mold’s runner system. Hot resin is shot into the mold cavity through the gates and the part is molded. Ejector pins facilitate removal of the part from the mold where it falls into a loading bin. When the run is complete, parts (or the initial sample run) are boxed and shipped shortly thereafter.
Our helpful design aid demonstrates part features that are too thin or too thick, bad bosses, right and wrong ribs, and other considerations to be mindful of while designing parts for injection molding.
Based on the chart above, 3D printing is a much cheaper option for lower quantities due to the absence of high upfront mold tooling costs. As we reach 500 pieces and above, injection moulding starts becoming more cost-effective. At 10,000 pieces, the total cost of injection moulding is approximately $12,900 (around 99 cents per piece), while 3D printing costs $70,000 (around $7 per piece), making additive manufacturing five times more expensive.
This complete reference guide walks you through everything from quoting, design analysis, and shipment to best practices that ensure your model is optimized for molding.
We have wide selection of more than 100 thermoplastic and thermoset materials. And if you're looking for alternative material options, check out our guide to resin substitutes for ABS, PC, PP, and other commonly molded plastics.
With prototype injection mold tooling, also known as rapind tooling, you can test the part in the production intent material, understand how the part will work when manufactured in the production process, and it allows for low volume production runs to test the market.
Injection molding is a manufacturing process that consists of filling a metal mold cavity with liquid plastic resin, which then cools and forms a plastic part.
It's most often used for the manufacturing plastic parts at scale due to its low material waste and low cost per part. It’s an ideal manufacturing process for industries like medical devices, consumer products, and automotive.
The argument typically goes that the cost to deliver a 3D-printed part will always remain the same, regardless of whether you are producing 1 or 1000 units. However, this is not the case, as evident in the chart above. 3D printing technologies has advanced over the years. Nowadays, manufacturers like HLH Rapid with automation systems, streamline processes and larger industrial printers, now enable the production of larger quantities at lower unit costs.
Tough Black (Loctite Henkel 3843) and Ceramic-Filled (BASF 3280) are two new advanced photopolymer materials now available for 3D printing.
Tolerances: Typically, Protolabs can maintain a machining tolerance of +/- 0.003 in. (0.08mm) with an included resin tolerance that can be greater than but no less than +/- 0.002 in./in. (0.002mm/mm).
Additive manufacturing is slowly establishing itself as a viable production tool, and we’re increasingly seeing our clients utilize these benefits. However, this does not mean that additive manufacturing should be treated as a complete replacement for traditional manufacturing. For large-scale production, traditional methods still offer unmatched economies of scale.
When it comes to production methods, two processes, injection moulding and 3D printing are often compared. These two methods represent a classic debate of ‘old’ vs. ‘new’ in today’s manufacturing industry. While 3D printing has allowed for innovative design implementation within hours, plastic injection molding remains an industry standard for high-quality, reliable, large batch production.
When it comes to production methods, two processes, injection moulding and 3D printing are often compared. These two methods represent a classic debate of ‘old’ vs. ‘new’ in today’s manufacturing industry. While 3D printing has allowed for innovative design implementation within hours, plastic injection molding remains an industry standard for high-quality, reliable, large batch production.When comparing the two methods, cost is often the first topic that comes to mind: Which is cheaper, injection molding or 3D printing? It is crucial to determine when it is more economical to use injection molding over 3D printing, and vice versa. In this article, we will analyze the differences in per unit cost, total cost and advantages of using each process. 3D printing vs injection molding: cost comparisonThe cost of 3D printing versus injection moulding a part. For this example, we’ve taken an SLS printed and injection moulding PA+GF part that is 84.5mm x 80.0mm x 24.0mm in size with a standard deburr finish. *Please note that the chart is crafted based on the specific case mentioned. The cost per unit of your specific part may vary significantly based on factors such as size, geometry, complexity, material, post processing, and other considerations. For an accurate cost assessment of your part, we encourage you to get a rapid quote from our team at hlhrapid.com. Piece-part priceIn the case above, it is estimated that a mould would immediately cost the client $3,000 to have manufactured. Of course, this can vary depending on the size, complexity, and where the tool is manufactured.Based on the chart above, 3D printing is a much cheaper option for lower quantities due to the absence of high upfront mold tooling costs. As we reach 500 pieces and above, injection moulding starts becoming more cost-effective. At 10,000 pieces, the total cost of injection moulding is approximately $12,900 (around 99 cents per piece), while 3D printing costs $70,000 (around $7 per piece), making additive manufacturing five times more expensive. Setup and tooling considerationsIn injection moulding, every design modification or iteration usually demands the reworking of the mould, which can be costly and time consuming. Due to the nature of the process, significant changes may even require a completely new tool. This puts 3D printing at a notable advantage in this comparison. 3D printing allows you to update and change your design throughout the entire production process. Not only does it provide flexibility, but it is also a faster choice and more cost-effective option for small quantities. This makes additive manufacturing the perfect choice for prototyping and iterations. Scaling with 3D printingThe argument typically goes that the cost to deliver a 3D-printed part will always remain the same, regardless of whether you are producing 1 or 1000 units. However, this is not the case, as evident in the chart above. 3D printing technologies has advanced over the years. Nowadays, manufacturers like HLH Rapid with automation systems, streamline processes and larger industrial printers, now enable the production of larger quantities at lower unit costs.Additive manufacturing is slowly establishing itself as a viable production tool, and we’re increasingly seeing our clients utilize these benefits. However, this does not mean that additive manufacturing should be treated as a complete replacement for traditional manufacturing. For large-scale production, traditional methods still offer unmatched economies of scale. Prototyping with injection mouldingCan you prototype with injection moulding? At HLH Rapid, we use a single-cavity aluminum mold, known as a prototype injection mold tool, that can produce hundreds of parts. Nevertheless, project budgets are generally tight and deadlines are even tighter, so why would you invest the time and money needed to manufacture a prototype via injection molding? Why not go straight from your 3D printed prototype to production tooling? With prototype injection mold tooling, also known as rapind tooling, you can test the part in the production intent material, understand how the part will work when manufactured in the production process, and it allows for low volume production runs to test the market. 3D printing vs injection molding: which to chooseHLH Rapid has over 15 years of experience in 3D printing, injection molding, rapid tooling, and scaling from prototype quantities to product quantities. Request for an accurate quote from our team for multiple quantities to better understand which option is more cost-effective, when to justify high tooling costs, and which technology to use for your next rapid project.
While the molds themselves are similar, part quantities, lifetime maintenance, quality documentation, and pricing vary depending on which service option is chosen. The right one depends on your project needs.
*Please note that the chart is crafted based on the specific case mentioned. The cost per unit of your specific part may vary significantly based on factors such as size, geometry, complexity, material, post processing, and other considerations. For an accurate cost assessment of your part, we encourage you to get a rapid quote from our team at hlhrapid.com.
The manufacturing process for molded parts is complex. Before your parts are even molded, we're there to help you with comprehensive manufacturability feedback and consultative design services, so you can avoid mold design pitfalls before the resin hits the mold. From there, our production process is documented and optimized using scientific molding so you get high-quality parts consistently and reliably with every production run.
The cost of 3D printing versus injection moulding a part. For this example, we’ve taken an SLS printed and injection moulding PA+GF part that is 84.5mm x 80.0mm x 24.0mm in size with a standard deburr finish.
HLH Rapid has over 15 years of experience in 3D printing, injection molding, rapid tooling, and scaling from prototype quantities to product quantities. Request for an accurate quote from our team for multiple quantities to better understand which option is more cost-effective, when to justify high tooling costs, and which technology to use for your next rapid project.
Depending on your application's requirements, you can choose from the following when requesting an injection molding quote.
Our thermoplastic injection molding is a standard process involving an aluminum mold with no heating or cooling lines running through it, which means cycle times are a bit longer. As part of the scientific molding process, our molders independently optimize and monitor fill speed, hold pressure, and hold time, and periodically inspect part quality and cosmetics. During the molding process, we use an automated inline CMM to ensure dimensional accuracy, as well as generate a detailed process capability study and FAI report.
Our basic guidelines for plastic injection molding include important design considerations to help improve part moldability, enhance cosmetic appearance, and reduce overall production time. View our design guidelines page for more details.
Critical-to-quality (CTQ) dimensions you call out on models let us know what areas are most crucial to the success of your parts. Once the parts start molding, the process and samples are qualified using automated inline CMM technology, generating a detailed FAI and process capability study with no additional lead time.
Our digital factories create prototypes and low-volume parts fast, while our manufacturing network, offers advanced capabilities and volume pricing.
When comparing the two methods, cost is often the first topic that comes to mind: Which is cheaper, injection molding or 3D printing? It is crucial to determine when it is more economical to use injection molding over 3D printing, and vice versa. In this article, we will analyze the differences in per unit cost, total cost and advantages of using each process.
In the case above, it is estimated that a mould would immediately cost the client $3,000 to have manufactured. Of course, this can vary depending on the size, complexity, and where the tool is manufactured.
It has been very enlightening to us here at HP that we are able to get parts so rapidly out of the actual materials that we're going to use in the final production.
In injection moulding, every design modification or iteration usually demands the reworking of the mould, which can be costly and time consuming. Due to the nature of the process, significant changes may even require a completely new tool. This puts 3D printing at a notable advantage in this comparison.
Our plastic injection molding process produces custom prototypes and end-use production parts with lead times as fast as 1 day. We use aluminum molds that offer cost-efficient tooling and accelerated manufacturing cycles, and stock about 200 different thermoplastic resins.
Get machined parts anodized and chromate plated with our quick-turn finishing option. Eligible materials include aluminum 6061/6082 and 7075.
No one ever said that designing and manufacturing molded parts was easy. Our goal is to get you through it quickly and with quality parts. A good starting point is our Design for Moldability Toolkit.
Proto Labs, Inc. 5540 Pioneer Creek Dr. Maple Plain, MN 55359 United States P: 877-479-3680 F: 763-479-2679 E: [email protected]
Can you prototype with injection moulding? At HLH Rapid, we use a single-cavity aluminum mold, known as a prototype injection mold tool, that can produce hundreds of parts. Nevertheless, project budgets are generally tight and deadlines are even tighter, so why would you invest the time and money needed to manufacture a prototype via injection molding? Why not go straight from your 3D printed prototype to production tooling?
3D printing allows you to update and change your design throughout the entire production process. Not only does it provide flexibility, but it is also a faster choice and more cost-effective option for small quantities. This makes additive manufacturing the perfect choice for prototyping and iterations.
Want to learn more about injection molding? Sign up to receive a Design Cube. This physical aid demonstrates how to properly design features commonly found on molded parts.
GETTING A QUOTE WITH LK-MOULD IS FREE AND SIMPLE.
FIND MORE OF OUR SERVICES:
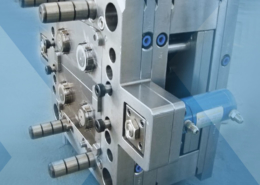
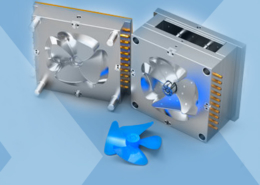
Plastic Molding

Rapid Prototyping
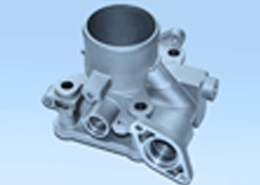
Pressure Die Casting
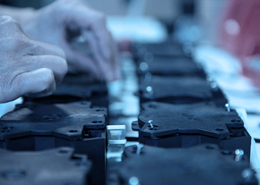
Parts Assembly
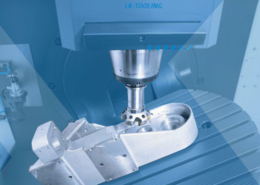