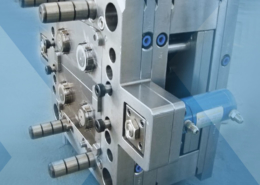
Things to Know About the Two Shot Molds - 2 shot injection molding
Author:gly Date: 2024-10-15
Upfront tooling costs. Injection molds are a huge investment, though one that typically pays for itself over a long service life. Urethane casts, on the other hand, usually can be produced for under $2,000 (as opposed to tens or hundreds of thousands of dollars for steel or other metal injection molds). We’ll talk more about differences in quantity and performance for each in the next point, but for now, understand that if you need to keep upfront costs low, urethane casting is the better choice.
Aluminum injection molds cannot be used for complex parts. Aluminum is a softer metal that can only be used for simple injection molded designs. Designs with complex geometry will need to be made with a steel mold. The steel is better able to handle complex designs and any thin walls in the design. Aluminum molds cannot handle thin walls or complex geometry because the metal is not as structurally strong as steel and will deform during the molding process. This is a universal limitation for all mold makers – not unique to the ICOMold by Fathom manufacturing process.
Aluminum molds have a limited manufacturing life span. Aluminum is a soft metal and cannot with stand the repeated pressure and temperature of the injection molding process. Aluminum molds will produce 3,000 to 10,000 cycles before needing to be replaced. Steel molds are more resilient and will produce 30,000 to 100,000 cycles before needing to be replaced or repaired.
Injection molding is a manufacturing process that uses a metal mold to manufacture large numbers of plastic parts. ICOMold by Fathom uses only high-strength steel when making plastic injection molds. Steel molds have several advantages over aluminum molds. Steel molds consistently produce a higher quality product when compared to aluminum molds. Steel molds are built to last — up to ten times longer than aluminum molds. Steel molds may have a higher up-front price but they can save significant time and money down the road.
Lead times. Tool steel injection molds require more intricate and extensive machining to create, and usually are not ready for several weeks — a typical lead time for a mold might be two months. Urethane casts, on the other hand, can be produced in less time, usually requiring just a 3D printed model to be produced and a soft mold to be created around it.
Looking at other specifics of the two processes, the materials used for molding vs. casting are typically different. Molds used for injection molding are typically created from a metal, such as hardened tool steel, or, for some lower volume applications, softer metals like aluminum. Casting molds, on the other hand, are usually made from materials such as silicone rubber. We’ll talk more about the impact of this difference in a bit.
Steel molds are much more durable and can last up to 100,000 cycles or more. While aluminum molds may be cheaper to machine, the steel mold will last ten times as long – producing parts long after the aluminum mold has been scrapped and replaced several times. The cost of machining a new aluminum mold after every 10,000 cycles will add up quickly.
Per-part cost vs. overall cost. When you’re looking the bottom line and ROI, per-part cost is a very useful benchmark to determine the efficiency of your process. In general, per-part costs for urethane casting will be higher than for injection molding, due primarily to the lower volume of parts created. Overall costs, however, are typically lower for urethane casting because of lower tooling and material costs.
As mentioned above, casting and molding are generally similar processes. The difference lies in the details, especially as they relate to manufacturing practices. Plastic injection molding is a process of using pressurized machinery to fill mold cavities. With casting, the material is generally poured into a mold rather than injected at high pressure. From there, we return to similarities: the heated, liquefied material is allowed to cool and harden, and is then ejected or released from the mold or cast.
Finally, let’s look at how tooling is manufactured for each process. Urethane casts are usually made by molding a 3D printed model of the finished part, whereas injection molding tools are machined via CNC grinding, milling and other processes.
Flash is what happens when the plastic injection material seeps into the mold seams during the injection process. The excess material will need to be removed in post-processing. This post-processing can be expensive depending on the amount of flash and the work required to remove it. Aluminum molds for injection molding are prone to flash. Aluminum is a soft metal and is therefore easier to deform and allow the injected material to leak out of the machined cavity. Steel is a harder material, which reduces the chance for flash. Steel molds will not deform as easily as an aluminum mold.
Injection molded material can impact the life expectancy of the tool. Aggressive materials like ASA/glass-filled Nylon and Ultem can reduce the lifespan of injection molds. Steel injection molds can be hardened through heat treatment to become extremely durable. The heat treatment will allow steel molds to handle the aggressive material without issue. Aluminum molds for injection molding cannot be hardened and will not be able to handle the high injection pressure and temperature required when injecting these aggressive materials.
Steel molds offer more options for surface finishes. The high-density nature of steel allows more texture selections. Custom, tall, or deep details in the tooling can be achieved by adding steel inserts. The number of surface finishes possible with an aluminum mold is limited and custom finishes are not available. The difference in available surface finishes is based on the mold material. This limitation affects all mold makers, not just ICOMold.
An aluminum mold will hold up for short part runs and is an ideal choice for small orders. However, steel molds are more durable and suited for extended manufacturing runs. Aluminum molds do not have the corrosion resistance or thermal stability found in steel molds. Steel molds are also better able to resist the constant wear and tear of the injection molding process. These characteristics allow the steel injection molds to achieve higher production cycles and withstand non-conformities in the product. Aluminum molds must be anodized or plated with nickel to reach the same level of hardness as steel molds. Anodizing and plating will increase the tooling cost and negate the benefit of using the less expensive aluminum to machine the mold.
Comparing the benefits and drawbacks of two different manufacturing processes can be one of the best ways to illustrate the importance of proper process selection for a project. Urethane casting vs. plastic injection molding, for instance — two processes that are, on the surface, relatively similar — can yield vastly different results depending on your requirements and expectations. To start, let’s look at the difference between casting and molding.
Aluminum cannot be used as the injection molded material. The manufacturing process of metal injection molding does exist, however, aluminum cannot be injected molded. ICOMold by Fathom specializes in injection molding custom plastic parts. ICOMold can also manufacture custom metal parts with Computer Numerical Control (CNC) machining. As part of the Fathom manufacturing network, ICOMold will work to match customers to manufacturers in order to meet their specific aluminum machining needs.
Material costs. The production-quality plastics typically used in injection molding will require a greater expenditure than the urethanes used in urethane casting. If you require only a prototype or a run of a few pieces, you’re likely better off choosing urethane casting. For longer runs, or applications where certain material properties are critical to the performance of the part, you’ll need to choose the appropriate plastic for your needs.
Now that we know some differences between the two processes, we can look more closely at their implications. From there, we can see the optimal situations to make use of each.
Aside from the materials used to create a mold or a cast, the materials that are suited to each process are different, as well. Injection molding will typically use production-grade plastics such as PVC, ABS, polycarbonate and others. Casting is better suited for materials that can mimic the qualities of these plastics at low volumes, like urethanes.
ICOMold’s fast-turn, low-cost, high-value injection molding enhanced by joining Fathom’s manufacturing platform. Learn More
Quantity and production volume. If you’re looking for a mold for prototypes or low-volume runs, or you need to produce only a few parts at a time, a urethane mold is the better choice. For high-volume production quantities, the quality and lifespan of a tool steel mold will generally yield the better return on investment. Hand in hand with the point above, it’s best to weigh your production volume needs against the amount of investment you’re willing and able to make at your stage of product development.
In terms of quantities, injection molding tooling usually features a large number of cavities in each mold, resulting in higher quantities produced from each cycle. The nature of casting means that typically only a few (or as few as one) pieces are produced at once.
Preparation and education are two of the best ways to maximize your bottom line and the efficiency of your product development and production processes. Knowing what to expect at each step of the way is a highly effective tool in making informed choices — the types of choices that lead to a successful product. Understanding that one process is usually not inherently “better” than another, but may be better for your specific needs, is a key component of that knowledge — and we hope that this overview has helped you understand how to make those distinctions.
Steel molds can be modified and repaired after initial tooling. Aluminum molds cannot be changed or repaired if there is a problem with the initial design. Steel molds can be modified with welding. If a part re-design requires less plastic in an area, and therefore, more steel in that area of the injection mold tooling, the steel mold can be modified. This is not the case with aluminum. Consider using a steel mold if there is any chance your part may undergo design revisions that will require modifications. Steel molds can also be repaired in some instances. This will save customers thousands of dollars by simply repairing the mold instead of machining a new mold. The ability to repair a mold will depend on the tooling. Not all steel molds will be able to be repaired.
Aluminum can be used to make molds for the injection molding process. Aluminum is an affordable material that is easy to work with and has many applications. However, aluminum molds, while slightly cheaper to produce, are considered inferior to steel molds. ICOMold by Fathom uses only high-strength steel to manufacture injection molds.
An aluminum injection mold will last 3,000 to 10,000 cycles. Each cycle represents the mold closing, the mold being filled, the mold opening, and the part being ejected. If the mold has a single cavity, customers can expect to get up to 10,000 parts from an aluminum mold.
Development stage suitability. Between urethane casting and injection molding, there is no one “superior process.” Each one is, however, better suited for a different stage of your product’s development. For prototyping, urethane casting will almost always be the better choice, unless there is a specific need to use injection molding and a particular material at the prototype stage. Often, it will be cost prohibitive to iterate by modifying an injection molding tool, so a different process will almost always be a more cost-effective choice. For high-volume production runs, the durability and quality of tool steel molds cannot be mimicked by other materials or processes. In quantities of 100,000 and up, you simply will not see the ROI with another process that you will with a steel mold, and will begin encountering repair and replacement costs much sooner.
GETTING A QUOTE WITH LK-MOULD IS FREE AND SIMPLE.
FIND MORE OF OUR SERVICES:
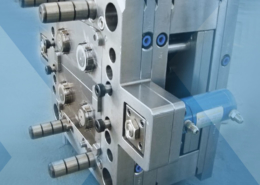
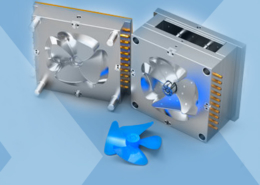
Plastic Molding

Rapid Prototyping
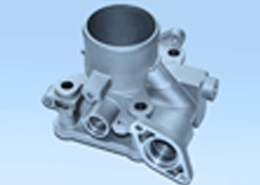
Pressure Die Casting
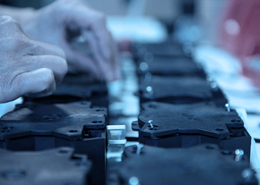
Parts Assembly
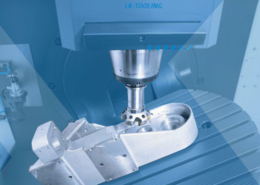