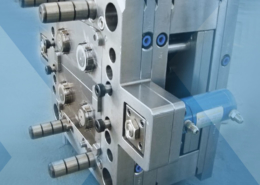
Exploring the World of Custom Molded Plastics
Author:gly Date: 2024-06-08
Custom molded plastics, a cornerstone of modern manufacturing, offer a plethora of applications across various industries. From automotive components to medical devices, these versatile materials have revolutionized the way products are designed and produced. This article aims to delve into the intricacies of custom molded plastics, providing readers with both a comprehensive understanding and an appreciation for their significance in contemporary manufacturing processes.
Understanding Custom Molded Plastics
Custom molded plastics refer to plastic parts that are manufactured using a molding process tailored to specific design requirements. Unlike standard plastic parts, which are mass-produced using predefined molds, custom molded plastics are uniquely crafted to meet the exact specifications of individual projects. This bespoke approach allows for greater flexibility in design, enabling manufacturers to create complex shapes and intricate features with precision.
Materials and Processes
The materials used in custom molded plastics vary depending on the desired properties of the final product. Thermoplastics, such as polyethylene and polycarbonate, are commonly employed due to their versatility, durability, and ease of processing. Thermosetting plastics, such as epoxy and phenolic resins, offer enhanced heat resistance and dimensional stability, making them ideal for high-temperature applications.
The molding process itself encompasses a range of techniques, including injection molding, compression molding, and blow molding. Injection molding, the most widely used method, involves injecting molten plastic into a mold cavity under high pressure. This process allows for rapid production of large volumes of parts with minimal waste, making it highly efficient and cost-effective.
Applications Across Industries
Custom molded plastics find applications across a diverse array of industries, including automotive, aerospace, electronics, healthcare, and consumer goods. In the automotive sector, these materials are utilized in interior components, exterior body panels, and under-the-hood parts, where they offer lightweight, durable alternatives to traditional metal counterparts. In the medical field, custom molded plastics play a crucial role in the production of surgical instruments, prosthetic devices, and diagnostic equipment, owing to their biocompatibility and sterilizability.
Advantages and Challenges
The adoption of custom molded plastics brings forth a multitude of advantages, including design flexibility, cost efficiency, and faster time-to-market. By customizing the material composition and molding process, manufacturers can tailor the properties of the final product to meet specific performance requirements, resulting in superior functionality and aesthetics. Moreover, the ability to produce intricate geometries with tight tolerances enables the realization of complex designs that would be impractical or impossible with other manufacturing methods.
However, the widespread use of custom molded plastics also presents certain challenges, such as material selection, tooling costs, and environmental considerations. Selecting the appropriate material for a given application requires careful consideration of factors such as mechanical properties, chemical resistance, and regulatory compliance. Furthermore, the initial investment in tooling and equipment can be substantial, particularly for small-scale production runs. Additionally, the disposal and recycling of plastic waste pose environmental concerns, necessitating the development of sustainable practices and alternative materials.
Conclusion
In conclusion, custom molded plastics represent a cornerstone of modern manufacturing, offering unparalleled versatility, customization, and efficiency. From automotive components to medical devices, these materials have revolutionized the way products are designed, produced, and utilized across various industries. By understanding the intricacies of custom molded plastics, manufacturers can harness their potential to create innovative solutions that meet the evolving needs of the market. As we continue to explore new materials, processes, and applications, the future of custom molded plastics remains promising, paving the way for further advancements in manufacturing technology and product design.
GETTING A QUOTE WITH LK-MOULD IS FREE AND SIMPLE.
FIND MORE OF OUR SERVICES:
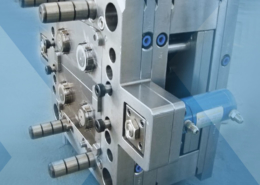
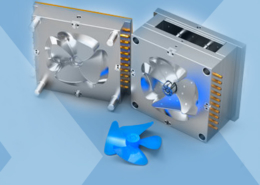
Plastic Molding

Rapid Prototyping
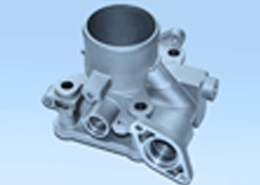
Pressure Die Casting
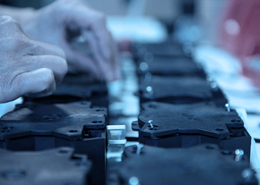
Parts Assembly
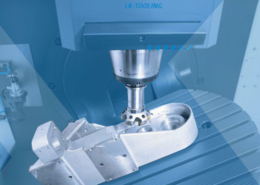