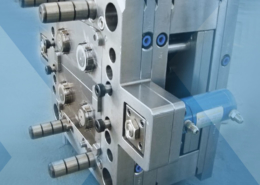
Thermoset Molding Capabilities - thermoset molding
Author:gly Date: 2024-10-15
Polyethylene injection molding offers a versatile and cost-effective solution for producing a wide range of customized plastic parts for various industries and applications.
Linear-low-density polyethylene (LLDPE) is a flexible and stretchable thermoplastic material that also offers puncture and impact resistance. Compared to LDPE, injection-molded LLDPE has greater chemical resistance, better mechanical characteristics at high and low temperatures, high surface gloss, and good resistance to cracking. It provides a barrier to water and has good stress cracking and impact resistance.
High-density polyethylene (HDPE) is a thermoplastic material that is commonly used in injection molding applications due to its unique properties. HDPE has a high strength-to-density ratio, making it a strong and durable material that can withstand impact and heavy loads. It also has good chemical resistance, making it suitable for use in applications where it may come into contact with chemicals or other corrosive substances.HDPE injection molding is a versatile and cost-effective process that can produce parts with a variety of shapes and sizes, making it suitable for many applications.
Polyethylene(PE) is a thermoplastic polymer that is formed by the polymerization of ethylene gas under high pressure and temperature, resulting in a high molecular weight material. The hardness and strength of different PE types vary, but injection molded polyethylene is typically used in parts that need to withstand pressure or strain. In addition, Polyethylene(PE) is a versatile material that can be made in various densities, from low-density polyethylene (LDPE) to high-density polyethylene (HDPE), and can be enhanced with a variety of additives. Polyethylene(PE) is lightweight, chemically resistant, electrically insulating, and inexpensive and easy to process. Polyethylene is commonly used in packaging, consumer products, construction and automotive applications.
Polyethylene injection molding is a manufacturing process used to produce custom plastic parts made from polyethylene material. The process typically involves the following steps:
Low-density polyethylene (LDPE) is a flexible thermoplastic material that maintains its structural integrity and has low water absorption. It remains flexible even at low temperatures and has good strength relative to its density, with the ability to withstand a significant amount of stretching before breaking. LDPE is odorless, sterile, and watertight, making it suitable for various applications. However, LDPE is susceptible to stress cracking and has lower strength and stiffness than other types of polyethylene. It also has limited resistance to mineral oils, oxidizing agents, and some hydrocarbons, and is highly flammable. As a result, it’s unsuitable for outdoor applications due to its poor resistance to UV light.
Polyethylene(PE) has different densities. PE with lower density types such as LDPE and LLDPE have lower crystallinity and higher flexibility, while higher density types such as MDPE and HDPE have higher crystallinity and stiffness. The level of crystallinity is also influenced by the molecular weight, which impacts both the material properties and the processing conditions. Each type of polyethylene has unique properties and benefits, allowing them to be used in various industries and applications.
Demonstrates a low friction coefficient similar to fluoropolymers and exhibits superior abrasion resistance to other polyolefins and engineering plastics.
UHMWPE is almost entirely inert, making it suitable for use in aggressive or corrosive environments at moderate temperatures. It remains resistant to many solvents at higher temperatures, although it may not be resistant to certain aromatic and halogenated hydrocarbons. The specific grade of UHMWPE determines the level of resistance to wear, chemicals, and impact that the material provides.
Despite its limitations, LDPE can be modified with specific additives to provide UV resistance or serve as an anti-static barrier for sensitive electronic components. LDPE is relatively easy to process during plastic injection molding, with a melt temperature ranging from 160°C to 260°C, and post-mold shrinkage between 1.5% and 3.5%. One of the applications for injection molded LDPE is hose fittings for water supplies.
Medium-density polyethylene (MDPE) is a durable thermoplastic material that offers high impact resistance and good chemical resistance. It has excellent shock and drop resistance and can withstand a wide range of chemicals, such as diesel fuels, acids, and oils. MDPE resins are stiffer than LDPE and LLDPE, but not as stiff as HDPE, making it a good “in-between” option.
Ultra-high molecular weight polyethylene (UHMWPE) is a thermoplastic material with exceptional mechanical properties, including high abrasion resistance and impact strength. Its low coefficient of friction also provides excellent abrasion and wear resistance. UHMWPE is commonly used in medical applications, specifically in the articulating surfaces of joint replacements, such as hip, knee, ankle, and shoulder surgery.
There are several types of polyethylene that can be used in injection molding, each with its own properties and applications. The most common types include:
LLDPE has a structure similar to HDPE but with a higher softening point, greater strength, and relative breaking extension. It’s more difficult to process than LDPE and has a narrower temperature range for heat sealing, which is commonly used in packaging applications and industrial laboratories. Some of the applications for injection molded LLDPE include enclosures, caps, snap fits, and lids.
In summary, careful consideration of these factors can help ensure the successful processing of PE and the production of high-quality parts. Regular maintenance and calibration of equipment and molds are also essential for optimal processing results.
As a material that does not easily generate a squeaking noise even when combined with various packaging materials, it is ideal for automotive and OA component uses where quiet operation is required.
However, MDPE has poor resistance to UV light and solvents, which limits its use in outdoor applications and in contact with certain chemicals. Despite this limitation, MDPE injection molding remains a versatile and cost-effective process for producing a variety of customized plastic parts with superior mechanical properties for various industries and applications.
Polyethylene injection molding can be customized to produce parts of different sizes, shapes, and complexities. The process can also incorporate various additives and fillers to enhance the properties of the final product. The advantages of polyethylene injection molding include its ability to produce high-quality parts with tight tolerances and consistent dimensions. It also allows for mass production of parts at a relatively low cost compared to other manufacturing processes.
We offer a variety of manufacturing services: Rapid Prototyping, Tool Making, Injection Molding, Product Design and Development, CNC Machining and Metal Stamping. You can choose from a variety of plastics, silicone rubber, or metal for your product. Regardless of mass production or small batch customization, Sungplastic has always been committed to providing assured, efficient and more economical one-stop processing services for your projects.
Polyethylene injection molding offers many advantages and is an excellent choice for custom plastic parts. Sungplastic is your operating system for custom plastic parts, where you can quickly get quotes and learn about PE materials. Our injection molding experts understand the properties of each polyethylene plastic and also have experience molding LDPE, LLDPE, MDPE, HDPE and UHMWPE.
A:Yes, Sungplastic is a full-service injection molding company that provides a range of injection molding services, including thermoplastic(ABS, PC, PP and Nylon) injection molding, overmolding, insert molding and so on.
A: The geometry of the part, the amount of parts needed, your tooling budget and the application the part is being used for will all influence your decision to PE injection mold the part.
Polyethylene injection molding offers a range of benefits that make it a popular choice for the manufacturing of customized plastic parts for various industries and applications.
Sungplastic is a plastic product manufacturer with rich experience in injection molding. According to the different product development requirements, we flexibly adjust the manufacturing process to achieve high quality, high efficiency and more economical.
A:The time it takes to build a polyethylene injection mold can vary depending on several factors, such as the complexity of the part, the size of the mold, and the level of customization required. Generally, building a custom mold can take several weeks to several months.
Plastic Mold Manufacturing Plastic Injection MoldingRapid PrototypingCNC MachiningSheet Metal StampingPressure Die CastingSilicone & Rubber PartsSurface Finishing
GETTING A QUOTE WITH LK-MOULD IS FREE AND SIMPLE.
FIND MORE OF OUR SERVICES:
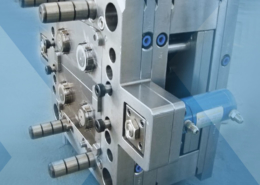
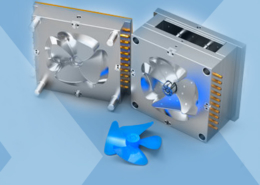
Plastic Molding

Rapid Prototyping
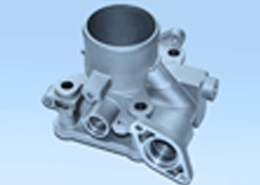
Pressure Die Casting
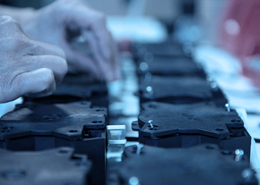
Parts Assembly
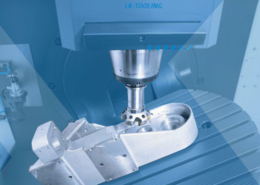