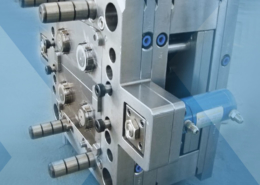
Thermoplastic Molding - thermoplastic molding
Author:gly Date: 2024-10-15
Thermoforming is a type of molding process that involves heating a plastic sheet of thermoplastic to a pliable forming temperature. A mold will then help the sheet form a particular shape, and a molding expert will trim it as necessary. This method also uses low pressures and can create 3D products from a 3D mold made from aluminum.
It’s the entry point that allows the melted plastic to pass through from the injection unit. The entrance of the injection mold is called the sprue bushing. They connect to runners, tunnels connecting the sprue to the cavity image.
Compression molding involves placing a heated plastic material into a heated mold and pressing it into a particular shape. This heating process, known as curing, allows the plastic to retain its strength. It is then followed by the cooling and trimming of the plastic before removal from the mold.
Different types of plastic molding suit diverse industry needs, each with unique features and benefits. By understanding the different molding processes and their common uses, you’ll be better positioned to choose a type that provides optimal performance for your product.
The 3D printing process involves having a printer lay sequential layers of a material such as polylactic acid, nylon, or polycarbonate to create a product. At The Plastek Group, we can print three different colors and create components with features like over-molding or a soft-touch finish. One of the main benefits of 3D printing is that it allows engineers to design plastic parts from their desks and make them a reality in hours.
Extrusion molding forms long, cylindrical plastic objects. This plastic molding process also differs from other molding types in that it uses a die instead of a mold to shape the product. The process involves squeezing hot, raw plastic through a custom-shaped die to get the desired shape. The extrusion machine includes a screw that feeds the plastic resin to the feeder. As it passes through the die, it creates a long, consistent shape, which is often tubular.
Similar to glass blowing, the blow molding process involves heating plastic and injecting air into the hot plastic until it expands to fill the mold and create the required shape. The mold then cools and hardens, and the machine ejects the part.
Generally, this injection molding tool can have single or multiple cavities, depending on your production volume. Single-cavity molds are called single-impression cavity molds, while those with multiple cavities are called multiple-impression cavity molds.
The small opening created when a mold opens is called a gate. Plastic enters the mold cavities through these openings. There are two main gate types found in injection molds. They include:
As mentioned, mold plates are one of the molding tools used to produce plastic containers. You can use the number of mold plates to differentiate various plastic injection tools. They include the following:
The next step is to create a prototype mold to test the design. This helps you decide whether or not your model will give you the desired outcome. You can also use this stage to improve your mold design before it reaches the final stages.
The overmolding process is simple. You start by molding the plastic products with a base-color material, ensuring you leave enough room to fit more plastic products with different colors.
Tooling material selection is one of the most overlooked yet critical injection molding tooling designs. Your choice of material will significantly influence the lifespan of your injection mold tooling.
Injection molding is commonly used for everything from large plastic car parts to small plastic bottle caps. This type of molding is especially ideal for creating high volumes of precise and high-quality parts at an affordable cost.
Here’s where you produce the actual mold. You can use various materials, like aluminum and steel, and techniques, such as electrical discharge machining (EDM), CNC machining, or 3D printing to produce the molds.
Rotational molding, or rotomolding, is ideal for producing larger hollow products or parts. The manufacturing process begins with placing liquid or powder resin into a metal mold and rotating it at high temperatures until the entire mold is coated with the resin. This constant rotation allows the resin to coat the mold evenly and create equal thickness throughout the product walls.
Given 3D printing’s flexibility, it’s a top choice for manufacturers in rapid prototyping, customization, and low-volume production scenarios. 3D printing also allows manufacturers to customize each item individually without incurring additional expenses, making it a cost-effective option for one-off or small-batch production needs.
The result is various plastic products like vehicle parts, containers, bottles, bottle caps, syringes, and more. Plastic molding offers numerous advantages, such as faster production, enhanced strength, and accurate complex part design. As a result, plastic molding is the preferred molding method for numerous business types and their applications.
Knowing the different types of plastic molding available can help you choose a method that aligns with your products’ needs. Would you like further assistance with understanding how to mold plastic and which molding process is best for you? The experts at The Plastek Group are happy to learn about your unique situation and determine the best fit for your goals.
Tools mold design, cavitation, and materials impact the plastic injection tooling tolerance. A simpler process is likely to get and maintain a tighter tolerance than complex parts because they can put tight tolerance at risk as there are other variables, such as the number of cavities, to consider.
To understand how it works, you must have basic knowledge of the injection molds tools, what they are, how they work, where to find them, and which injection molding tools are best for specific tasks.
The next process in the injection molding tooling involves producing several test parts and measuring the properties and dimensions of the molded plastics to see if they meet the required specifications and standards.
Generally, you’ll need sophisticated plastic injection molding tools to produce complex parts with added features like threads and undercuts. You may also require additional rotating mechanical gears in case of complex geometries.
Now that you know your mold qualifies, you can use it for mass production. This involves filling the various mold cavities with the molten plastics and giving it enough time to cool and solidify, taking the mold shape.
You can build your molding tools using aluminum or steel. However, aluminum isn’t the best option when producing high-tolerance plastic parts. You should, therefore, use it when making low-tolerant components only.
Rotomolding is one of the more economical molding options because you can reuse leftover plastic, reducing waste. You may use rotational molds for bulk containers, kayak hulls, recycling bins, storage tanks, and dog houses, among other products.
Injection molding is one of the most versatile and popular molding processes due to its capability to create parts with varying shapes and sizes. The injection molding process involves injecting molten plastic material into a metal mold at high pressure.
Another way to differentiate the plastic injection molding tools is through their feeding system, a collection of channels, including the runners, gates, and sprues, which direct the molten plastic into the mold cavity.
An injection mold or A plate is a machined tool used in the plastic injection molding process. It molds the molten plastics into finished plastic goods.
The first stage in the injection molding process is the design creation and engineering. It involves creating a 3D CAD model of the injection mold and testing its performance, to see if it produces plastic parts with the desired shapes, sizes, and tolerance, using a simulation software.
Depending on the product, the thermoplastic used in thermoforming will have varying thicknesses, materials, colors, and finishes. Professionals use thin-gauge thermoforming to manufacture containers, trays, lids, disposable cups, and similar products. Thick-gauge thermoforming is suitable for products like refrigerator liners and vehicle beds.
The ejector mold or the B plate is the part of the injection molding tool that acts as the exit point through which plastic parts eject from the injection mold.
Manufacturing companies offer different plastic molding options that are ideal for a range of industries, including personal care supplies, health and beauty products, home care items, pharmaceutical and nutraceutical products, and food and beverage items. This guide explores the different types of plastic molding processes and their common uses to help you determine the right molding manufacturing for your product or packaging.
The process for injection molding tooling isn’t that complicated. However, the process may vary depending on the products, materials, and specifications you want to meet.
Some examples of products created through blow molding include plastic bottles, watering cans, storage containers, fuel tanks, and plastic drums. Blow molding is also a popular technique used in the pharmaceutical and nutraceutical industries and health and beauty industries — it can form containers, bottles, and small medical and single-serve vials. The process is fast, allowing you to produce many pieces in one day.
There are various methods of plastic molding, from injection molding for high accuracy to rotational molding for larger hollow products. By understanding how different plastic products are molded, you can select a molding process that satisfies the unique demands of your product or services.
Plastic injection molding or injection molding is the production of plastic parts in large quantities using injection molding machines.
When the molten plastic molds, the clamping unit slides the B plate from the injection mold creating an exit point and pushing the plastic products out of the injection molds using ejector pins.
There are many types of injection mold you could use for your plastic injection molding process, but two-plate molding is the most used.
One of the primary ways to differentiate injection molding is by the number of mold cavities. There are three different types of injection molds under this category. They include the following:
Explore our plastic manufacturing capabilities today. To see how we can fulfill your plastic product and packing needs, contact one of our experts.
Overmolding is the process through which the injection mold forms multiple layers around a single product. It does this by re-introducing the injection molded parts into the mold.
Products formed with extrusion molding typically need to be the same shape along the length of the item. For this reason, companies mainly use it to create long and hollow products like straws, hoses, plastic decking, PVC piping, and plastic gutters. Some manufacturers may even create varying continuous shapes like U-sections, L-sections, T-sections, and circular sections.
The cavity image is an empty space in the injection mold that transforms the molten plastics to their desired shape and size.
Now that you know how plastic injection molding tools work, you can start your project. It’s a pretty straightforward process to create plastic containers in large quantities within a reasonable time frame. It’s also affordable and will help you produce quality pieces within the shortest time possible.
Finding the best manufacturing company for your custom injection molding process may be a little challenging. You must know the questions to ask and the response you need.
For the best results, you must ensure the molding company you work with has high-performance molding machines and high cavitation single face and stack molds. This equipment allows for the most effective and accurate injection molding process.
Blow molding is the process of making hollow, thin-walled plastic parts. This molding approach is often beneficial when the shape of your product is important and you need uniform wall thickness.
The Plastek Group is a world-class manufacturing company for plastic injection and blow molding packaging, among many other value-added services. Our process involves understanding your project, analyzing the best way to meet your functionality and cost requirements, developing a manufacturable concept using cutting-edge software and other innovative tools, and creating the final working model.
The process doesn’t end with a single production. You must maintain the injection molding to ensure it continues producing the high quality products. This means repairing worn parts, making needed adjustments, and cleaning it from time to time.
Compression molding is mainly useful for companies requiring strong, highly durable products. This process is ideal for automotive parts. Other valuable uses include creating sturdy plastic parts for household appliances, body armor, and clothing fasteners.
Molding involves placing liquid or pliable material into a rigid frame or mold cavity to form a particular shape. The manufacturing process uses pressure and heat to fill the cavity and pressurize the material until it solidifies. In plastic molding, manufacturers use polymers like polypropylene or polyethylene in pellet, granule, liquid, or powder forms.
GETTING A QUOTE WITH LK-MOULD IS FREE AND SIMPLE.
FIND MORE OF OUR SERVICES:
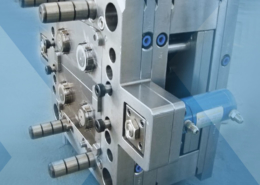
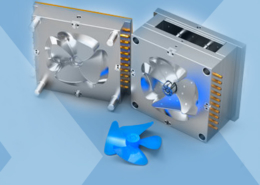
Plastic Molding

Rapid Prototyping
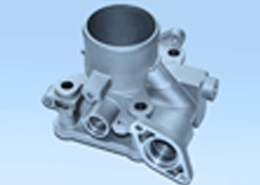
Pressure Die Casting
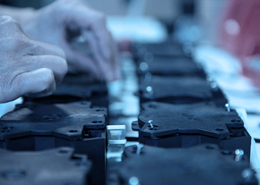
Parts Assembly
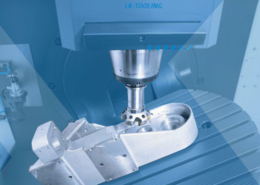