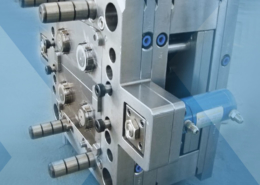
The Ultimate Guide to Prototype Injection Moulding - prototype injection molding
Author:gly Date: 2024-10-15
(2) The flow range of the melt is too long, and the flow resistance is too large – The parts that hinder the flow of the melt include the nozzle, the sprue, the runner, the gate, and the thin walls of a product. The flow resistance of the nozzle can be reduced by increasing the nozzle diameter / temperature, and using a nozzle with a small flow resistance.
Short shot refers to incomplete filling of a mold cavity which results in the production of an incomplete part due to the insufficient plastic fluidity. The main causes are the inappropriate injection pressure and speed (including excessive pressure loss caused by resistance), which are mainly affected by the following aspects:
(1) Poor plastic fluidity – If the plastic material doesn’t feature a great fluidity, it will solidify before reaching the furthest end of the cavity or flowing to the overflow tank, which often results in a short shot.
PMMA: Due to its higher stiffness and brittleness compared to ABS, PMMA parts may require careful handling during ejection to avoid stress-induced defects such as cracking or crazing. Proper mold release agents or ejector pin placement may be necessary to facilitate easy part removal. ABS: ABS parts are generally more forgiving in terms of ejection and handling, but care should still be taken to prevent part damage or distortion during demolding. Smooth ejection and part separation help maintain the integrity of the molded parts.
The process of injection molding for PMMA (Polymethyl Methacrylate) and ABS (Acrylonitrile Butadiene Styrene) involves similar steps but may differ in certain aspects due to the unique properties of each material. Here's a comparison of the injection molding process for PMMA and ABS:
(3) Poor venting. When filling the cavity, air is trapped to cause counter pressure. When the melt is injected into the cavity, the cavity is often closed by the melt in the very beginning, with air trapped in the unfilled local areas. Also, because the filling speed is too fast, sometimes there is not enough time for the air to be vented through the parting surface but compressed instead, resulting in partial unfilled areas in the cavity, thus short shot in the molded part.
(1) Insufficient injection molding capacity – This is caused by an overestimation of the capacity of the injection molding machine, which may also occur due to insufficient plasticizing capacity or insufficient injection volume. Among them, the insufficient plasticizing capability can be increased by extending the heating time, increasing the screw speed and raising the backpressure. If the injection volume is not high enough, the injection machine with a larger injection capacity can be used to solved the problem.
PMMA: PMMA is sensitive to moisture, so it requires thorough drying before processing to prevent defects such as bubbles, voids, or surface imperfections. Typically, PMMA pellets are dried in a desiccant dryer to reduce moisture content to acceptable levels. ABS: ABS is less sensitive to moisture compared to PMMA, but proper drying is still recommended to ensure optimal mechanical properties and surface finish. ABS pellets are also typically dried in a desiccant dryer before processing.
(1) Local short shot caused by the flow imbalance in each cavity of a multi-cavity mold – When the injection molding capacity of the injection molding machine is sufficient, this defect is mainly caused by the uneven flow in each gate, i.e., the mold cavities are not distributed in a balanced way.
PMMA: Due to its higher melt viscosity compared to ABS, PMMA typically requires higher processing temperatures and slower injection speeds to achieve optimal flow and minimize defects such as melt fracture, warping, or sink marks. The injection molding machine settings, including barrel temperature, injection pressure, and cooling time, need to be carefully adjusted to process PMMA effectively. ABS: ABS has lower melt viscosity and better flow properties compared to PMMA, allowing for faster injection speeds and shorter cycle times. The injection molding machine settings for ABS may involve lower barrel temperatures and higher injection speeds to optimize flow and fill the mold cavity efficiently.
In summary, while the basic principles of injection molding apply to both PMMA and ABS, the process parameters, mold design considerations, and handling techniques may vary to accommodate the specific properties and requirements of each material.
(1) Improper injection molding process – The low barrel temperature, slow injection speed, short injection time, and insufficient backpressure lead to a shortage of plastic.
During the product design process, the principle of uniform wall thickness must be followed. If it is impossible to maintain a uniform wall thickness, please change the mold design in a timely manner. Increase the number of runners or ribs in the area where the feeding is difficult, so as to avoid the defect of underfill caused by too-thin wall thickness.
(2) Oversupply of plastic – If too much plastic enters the barrel, the injection pressure is lost due to the compression of the pellets, thus reducing the pressure required to inject the melt from the nozzle, which is necessary for injection molding, resulting in insufficient injection pressure. The solution is to adjust the amount of feed, i.e., the amount of melt, and make the amount just right for the molding.
All in all, the reasons for short shot are multifaceted, which are also mutually restrictive and mutually influential. To reduce and correct such a defect, we need to make adjustments through an overall consideration of the relationship between these aspects, while making constant practice and accumulating experience continuously to quickly identify the causes of underfill, thereby reducing resource waste and improving product yield.
(3) Unstable production cycle – Frequent machine shutdown, and production inconsistent with the normal cycle make some plastics stay in the barrel for too long with reduced density and viscosity, thus resulting in plastic underfill.
In order to eliminate such defects, the melt / mold temperature, and the injection pressure / speed can be increased to allow the melt to reach the end of the cavity before solidifying. In such a case, a great plastic fluidity is of particular importance, so selecting the plastic with a better fluidity is also a solution. If the flow coverage is too long and the plastic cannot properly fill the injection molded part, it is recommended to change the gate location to reduce the plastic flow length.
PMMA: PMMA injection molds may require specific design considerations to accommodate its high shrinkage rate and minimize residual stresses in the molded parts. Proper mold venting is essential to prevent trapped air and ensure the quality of the surface finish. Cooling channels in the mold may need to be designed strategically to control cooling rates and minimize warpage. ABS: ABS injection molds may have similar design considerations as PMMA molds but may not require as much attention to shrinkage and residual stresses. Cooling channels are designed to efficiently remove heat from the mold, ensuring consistent part quality and minimizing cycle times.
(2) Try to evenly mix the recycled material and the raw material. Because the recycled pellets, as well as their density are relatively larger than the raw material, if the mixing is not uniform, the amount of the molten material is easily reduced, resulting in reduced injection volume accordingly.
GETTING A QUOTE WITH LK-MOULD IS FREE AND SIMPLE.
FIND MORE OF OUR SERVICES:
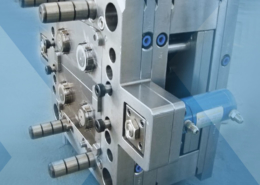
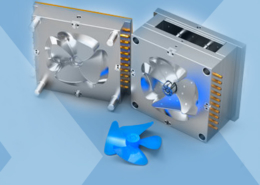
Plastic Molding

Rapid Prototyping
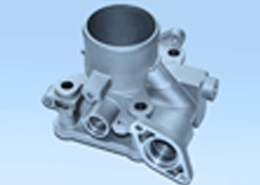
Pressure Die Casting
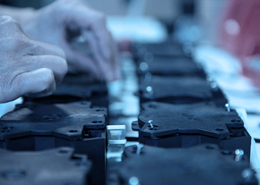
Parts Assembly
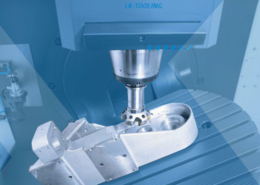