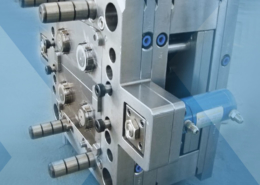
The Ultimate Guide to Nylon Plastic for Injection Molding - nylon injection mold
Author:gly Date: 2024-10-15
Outwater Industries offers a wide variety of color plastic angle mouldings. These corner trim mouldings are manufactured from high quality Styrene and PVC that provide many benefits. Styrene is cost effective and great for color matching, while PVC has a high impact strength and features resistance to chemical abrasion. These multifunctional color plastic angle corner moldings will stand up to high levels of everyday wear and tear and come in 60 and 90 degree angles. These specialty right angle mouldings also have a few styles that are available in both flexible and rigid forms. The flexible mouldings allow for curved installations on walls and other areas. These colored plastic moldings have a wide range of applications, including:
Our high-precision electric thermoplastic manufacturing capabilities deliver robust production with consistent quality output for virtually any product volume. Additionally, Sanner offers blow molding services at a number of its facilities.
Using fully automatic and robot-supported cleanroom production with minimal bioburden, Sanner can produce a range of devices for drug delivery and diagnostic applications. Sanner offers its CDMO customers molding activities in ISO Class 7 or 8 cleanrooms.
Our high-precision electric thermoplastic injection molding capabilities are designed to produce molded parts with shot weight accuracy and repeatability at low deviation to mean ratios for high-quality drug delivery, diagnostic, or medtech components.
All plastic angle mouldings are stocked in Outwater's East and West Coast facilities, making delivery and shipping faster and more convenient for every customer. Our in-house engineering allows for the production of custom extrusions to meet our customer's needs. If you're having difficulty finding the plastic extrusion profile you need, please contact our sales department.
Sanner CDMO can utilize its Babyplast micro-injection molding for prototypes, pilot series parts, providing material integrity even with small shot weights (0.1g).
Sanner’s mold tooling providers include some the world’s most advanced and well-established sources that can support virtually any tooling need. Sanner has been serving drug delivery, diagnostics, and medtech customers for over two decades with production processes and quality systems that are fully adapted to the requirements of the pharmaceutical and medical device industries. This includes our extensive injection molding capabilities from concept, design up to tool maintenance and optimization. We use our ISO Class 7 or 8 cleanrooms as well as unclassified spaces for molding activities, depending on the individual requirements, all operated under an ISO 13485 quality management system (QMS).
Our cleanroom molding facilities are capable of manufacturing packaging systems such as complex resealable pipettes, with pre-determined breaking points for dose opening, and thin-wall injection molded parts with exact wall thickness for tight device seals.
Outwater Industries offers a wide variety of color plastic angle mouldings. These corner trim mouldings are manufactured from high quality Styrene and PVC that provide many benefits. Styrene is cost effective and great for color matching, while PV...
Sanner offers 2K injection molding capabilities that is ideal for even the most complex molded parts. Sometimes called double injection, multi-material, or two shot molding, it is a specialized molding process that combines different thermoplastics (TP) in a single molding step. 2K molding can produce your complex drug delivery, diagnostic or medtech device parts for better handling characteristics and improved user-convenience.
Sanner’s CDMO tooling and molding services offer a range of precision molding technologies to develop and produce virtually any device or component for drug delivery, diagnostic, or medtech devices.
The Babyplast can also be operated under ISO Class 7 clean room conditions. Furthermore it is also possible to produce LSR parts in the prototype and Scale-up stage.
Sanner takes a scientific approach to designing, developing, and maintaining molds. Sanner’s tooling engineers can design, develop and maintain tooling for even the most complex devices or components. We start with our rigorous tool concepting process followed by mold flow simulation studies to assess material fill data. This data set allows our injection molding designers can better position mold gates, anticipate knit line locations and identify difficult to fill spots within the molds early in the process. All of this is done under the oversight of our metrology group to support component quality all the way through production. Critically, Sanner maintains its molding expertise in-house, with our own tool shop for more control and quicker turnaround in mold development and maintenance. Through scientific injection molding data analysis, Sanner‘s molding processes result in high-quality reproducible parts made by validated processes for CDMO customers.
Still headquartered in Germany, Sanner leverages its development expertise and best-in-class manufacturing capabilities to lead the market in desiccant closures and effervescent tablet packaging, and a sought-after provider of customized solutions for medical devices, diagnostics, pharmaceuticals, and consumer healthcare. To provide customers with a suite of leading, end-to-end services across drug delivery, diagnostics and medtech device sectors, Sanner recently acquired Springboard Pro, a leading device design and development consultancy based in Cambridge, U.K., and the U.S.-based CDMO Gilero, a specialist in medical design, development, manufacturing, assembly and packaging. Since 2021, Sanner Group has been backed by majority shareholder GHO Capital Partners LLP, a leading specialist healthcare investment advisor. Together, GHO and the fourth generation of the Sanner family will continue its successful growth to create intelligent healthcare solutions for a better quality of life.
HeadquartersSanner GmbH Schillerstr 76 64625 Bensheim GermanyTel.: +49(0)6251 938-0info@sanner-group.com
Sanner’s device CDMO teams bring extensive experience in processing a wide range of materials for different applications. Molded materials commonly utilized at Sanner include polypropylene (PP), high-density polyethylene (HDPE), all types of engineering plastics -, and various biobased materials with up to 64 cavities. Don’t hesitate to inquire if your device requires specialized materials.
GETTING A QUOTE WITH LK-MOULD IS FREE AND SIMPLE.
FIND MORE OF OUR SERVICES:
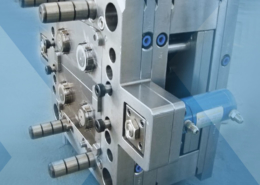
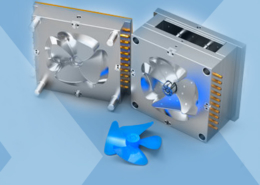
Plastic Molding

Rapid Prototyping
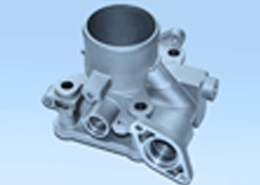
Pressure Die Casting
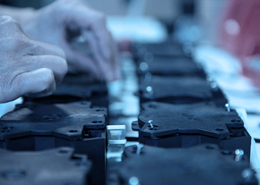
Parts Assembly
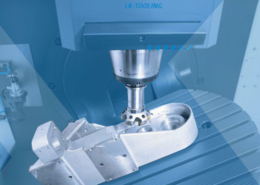