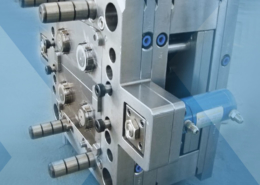
The role of injection molding in sustainable production for ... - sustainable in
Author:gly Date: 2024-10-15
VDI is an international standard for mould texturing of matte surfaces. It is mainly processed by Electrical Discharge Machining (EDM) when mould machining.
The same report points to the main drivers as a rise in the number of aircraft manufactured, increasing demand for lightweight components and growing demand for plastics in several aerospace applications. However, the high cost of fabrication and a limited range of material options are hampering the market.
“There are numerous advantages associated with ultra, high performance, and engineered polymers,” says Tim Miller, Technical Manager at Trelleborg Sealing Solutions. “These advantages include lighter weight, inherent flame resistance, excellent impact resistance, and low moisture absorption. More and more traditionally metal parts are being replaced with plastics and this trend will continue as the industry looks for lighter weight and more cost-effective solutions.
If you select a custom finish in the Instant Quoting Engine it will require manual review. Manual quoting usually takes 1-2 business days.
THE AEROSPACE INDUSTRY is continuing to evolve and there is a long-term trend toward using more engineered injection molded and machined parts in aircraft. According to Stratistics MRC the global aerospace plastics market accounted for 12.32 billion USD in 2017 and is predicted to reach 26.79 billion USD by 2026; an annual growth rate of 9%*.
The site is one of a few locations globally that is certified to injection mold parts from Torlon® PAI. By adding Torlon® to our aerospace material portfolio we are able to support a wider range of applications in the industry. The properties of the Torlon® material make it ideally suited to high-heat, load bearing applications, such as in engines, where reliable performance over time is critical.
The Trelleborg Sealing Solutions manufacturing facility in Denver, Colorado, U.S., is certified as an injection molder for ultra-high performance Torlon® polyamide-imide (PAI) polymer.
PEI (Ultem) is a thermoplastic polyimide. With a strong environmental resistance, this material is highly stiff and stable. It is rigid and retains its strength at high temperatures. It is resistant to heat and creep and has excellent electrical properties. It is flame retardant. It is typically used in engine components, temperature sensors, electronics and medical devices.
To counter that limitation, injection molding represents an effective and efficient option for production of plastic components. Sometimes thought of as weak, the latest plastic innovations in terms of materials and processes, mean that even structural metal parts can be replaced with injection molded alternatives.
GETTING A QUOTE WITH LK-MOULD IS FREE AND SIMPLE.
FIND MORE OF OUR SERVICES:
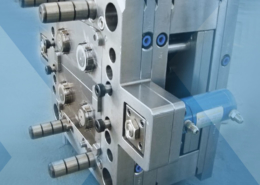
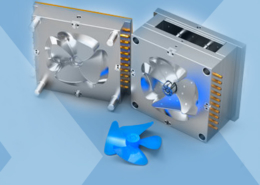
Plastic Molding

Rapid Prototyping
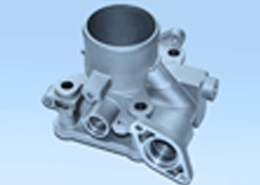
Pressure Die Casting
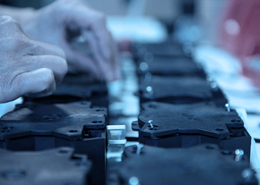
Parts Assembly
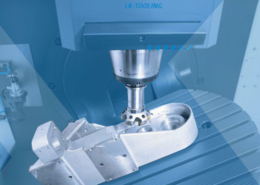