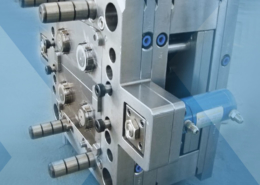
THE ROLE OF BACKPRESSURE IN INJECTION MOLDING - back injection molding
Author:gly Date: 2024-10-15
At the other end of the polyethylene spectrum, LDPE has many crystalline branches in its composition for an end product that is softer, more flexible and less brittle than the polyethylene materials with higher density ranges. LDPE and LLDPE are often used for lower temperature injection molding applications and will not withstand the high temperatures tolerated by HDPE.
The plastic is prepared in liquid form. In some cases the resin is naturally a liquid and in others a granular solid is liquefied by heat. The liquid plastic is poured into a closed mold and air bubbles are removed. The plastic is cured at room temperature or in an oven at low heat. The cured plastic is then removed from the mold.
Polyethylene plastic is the common choice for high-volume, low-cost injection molded applications. It can also be overmolded onto tubing for surface smoothness or roughness. Polyethylene is also used to produce sheeting for food wraps and plastic film. Interested in using this material for your project? Request a quote to get pricing.
A heated plug the size and shape of the inside of the article to be cast is dipped into a container of liquid plastisol. The mold is withdrawn at a given rate. The plastic immediately surrounding the mold adheres to it and solidifies. The slower the rate of withdrawal, the thicker will be the layer of plastic. After cure, the plastic is stripped from the mold.
A liquid plastisol is poured into a heated hollow mold which is the shape of the outside of the object to be made. The plastisol in immediate contact with the walls of the mold solidifies. The longer the plastic remains in the mold, the thicker will be the layer of plastic that solidifies. The excess plastic, still in the liquid form, is poured from the mold. After the plastic is cured the mold is opened and the part is removed.
Many products are made by casting rather than molding. In casting, the liquid is simply poured into the mold, rather than being forced in.
Within the broad industry of consumer goods, plastic injection molded polyethylene applications using grades from high density to low are found in many products, including:
High-density polyethylene injection molding results in products that are less flexible and stronger than products produced by injection molded lower-density polyethylene. With the fewest crystalline branches in its makeup, HDPE is defined with a density range of .941 to .960 g/cc. Although it has greater impact resistance, HDPE can sometimes be used in place of polypropylene, another commonly produced plastic found in commodity products.
As a group, polyethylene plastic is the most widely-used plastic in consumer goods. The range of polyethylene plastic materials is defined by density produced by crystalline branching within the material composition. The material grades include high-density polyethylene (HDPE), medium-density polyethylene plastic (MDPE) and low-density polyethylene (LDPE). Within the low-density polyethylene family, linear low-density polyethylene (LLDPE) is stronger and less flexible than LDPE.
A special application of casting commonly used for the manufacture of hollow articles is plastisol casting. There are several variations; dip casting, slush casting and rotational casting. All are based on the fact that a plastisol liquid form is solidified as it comes in contact with a heated surface.
While this material is a popular choice, under certain conditions, polyethylene can warp and suffer environmental stress fractures.
A predetermined amount of liquid plastisol is placed in a heated, closed, two-piece mold. The mold is then rotated, usually in two planes: this distributes the plastic against the walls of the mold in a thin even layer. As it comes in contact with the mold it solidifies. After the plastic is cured the mold is opened and the part removed.
The characteristics of plastic injection molded polyethylene differ by the grade selected with HDPE having the greatest strength and rigidity and LDPE showing the most softness and flexibility. Polyethylene is:
Both thermosets and thermoplastics may be cast. Commonly used materials for casting include acrylics, phenolics, polyesters and epoxies.
GETTING A QUOTE WITH LK-MOULD IS FREE AND SIMPLE.
FIND MORE OF OUR SERVICES:
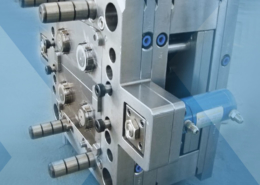
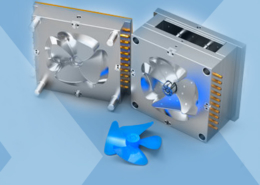
Plastic Molding

Rapid Prototyping
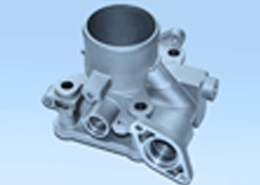
Pressure Die Casting
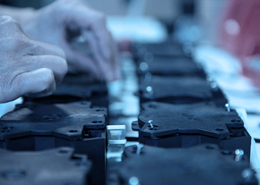
Parts Assembly
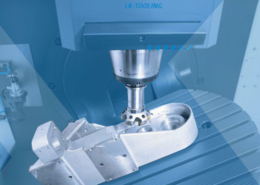