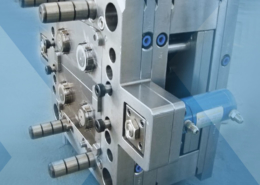
Exploring the Intricacies of Bobbin Molding
Author:gly Date: 2024-06-08
Bobbin molding, a specialized subset of injection molding, holds a unique place in the realm of manufacturing, particularly in the production of components for electrical and electronic applications. In this comprehensive analysis, we delve into the intricacies of bobbin molding, shedding light on its processes, applications, advancements, and future prospects.
Introduction
Introduction to Bobbin Molding
Bobbin molding is a manufacturing process used to produce cylindrical or spool-shaped plastic components known as bobbins. These bobbins serve various functions in electrical and electronic devices, such as holding and organizing wires, cables, or other components. The process involves injecting molten plastic material into a mold cavity, where it solidifies to form the desired shape of the bobbin.
Process Overview
Process Steps
The bobbin molding process consists of several key steps, beginning with the preparation of the mold and the selection of suitable plastic resin. Once the mold is prepared, the resin is heated to a precise temperature and injected into the mold cavity under high pressure. After cooling and solidification, the molded bobbin is ejected from the mold, trimmed, and finished as necessary.
Mold Design and Tooling
The design of the mold plays a crucial role in the success of bobbin molding operations. Mold engineers must consider factors such as part geometry, material flow, cooling efficiency, and parting line design to optimize mold performance and ensure consistent quality. Advanced tooling techniques, such as multi-cavity molds and hot runner systems, help maximize productivity and minimize cycle times.
Material Selection and Properties
Material Considerations
The choice of plastic resin is critical in bobbin molding, as it directly impacts the performance, durability, and cost-effectiveness of the final product. Engineers must select materials with properties tailored to the specific requirements of the application, such as temperature resistance, electrical insulation, chemical compatibility, and mechanical strength.
Advanced Materials and Additives
Advancements in polymer science have led to the development of specialized engineering thermoplastics tailored for bobbin molding applications. Materials with enhanced properties, such as flame retardancy, UV stability, and dimensional stability, are increasingly in demand for high-performance electronic devices. Additives such as glass fibers, fillers, and conductive additives further enhance material properties to meet stringent performance requirements.
Applications and Industries
Electrical and Electronic Applications
Bobbins find widespread use in electrical and electronic devices across various industries, including telecommunications, automotive, aerospace, and consumer electronics. They serve as essential components in transformers, inductors, solenoids, relays, motors, and other electromechanical systems, providing structural support, insulation, and winding space for conductive elements.
Medical and Industrial Applications
In addition to electronics, bobbin molding is also employed in medical devices, industrial equipment, and automation systems. Bobbins are used in applications such as medical sensors, fluid handling systems, actuators, and sensor enclosures, where precision, reliability, and performance are paramount.
Advancements and Future Outlook
Technological Innovations
Technological advancements continue to drive innovation in bobbin molding, enabling manufacturers to produce increasingly complex and precise components with greater efficiency and reliability. Innovations in mold design, material science, process automation, and quality control are poised to further enhance the capabilities and versatility of bobbin molding in the years to come.
Future Trends and Opportunities
Looking ahead, the future of bobbin molding holds promise for further advancements in materials, processes, and applications. Emerging trends such as miniaturization, wireless connectivity, and the Internet of Things (IoT) are driving demand for smaller, lighter, and more sophisticated electronic devices, creating new opportunities for bobbin manufacturers to innovate and collaborate across industries.
Conclusion
In conclusion, bobbin molding stands as a versatile and indispensable manufacturing process, serving a wide range of industries and applications with precision-engineered plastic components. Through meticulous process control, material selection, and technological innovation, bobbin manufacturers continue to push the boundaries of what is possible, driving progress and shaping the future of electrical and electronic devices. As we embark on the next phase of technological evolution, the role of bobbin molding in enabling innovation, efficiency, and reliability will only continue to grow, paving the way for a more connected, sustainable, and electrified world.
GETTING A QUOTE WITH LK-MOULD IS FREE AND SIMPLE.
FIND MORE OF OUR SERVICES:
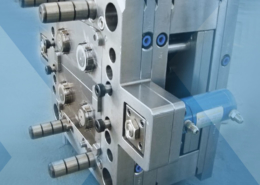
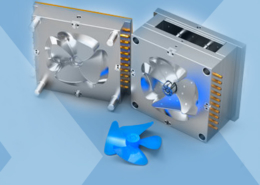
Plastic Molding

Rapid Prototyping
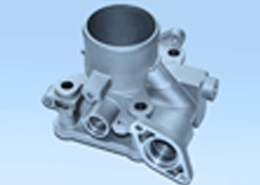
Pressure Die Casting
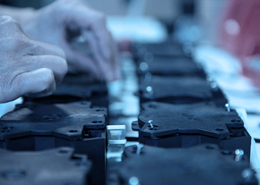
Parts Assembly
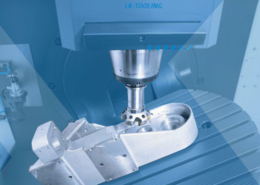