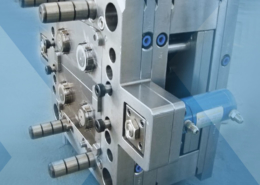
The Role of ABS in Injection Molding - abs moulding
Author:gly Date: 2024-10-15
Today, plastic injection molding is an environment-friendly process. The scrap plastic generated during the production process is reground and re-used. Hence, the process generates very little waste.
A highly skilled workforce and stringent quality standards ensure we consistently meet or exceed our customer’s expectations. Experienced molders include mold designers, toolmakers, plastics engineers, and fabricators. Some of them once served as lead engineer or project manager at a prestigious molding company like Accurate, with enough capability to meet all your tooling and molding needs.
One of the major advantages of using plastic injection molding for manufacturing parts is the ability to use different types of plastic simultaneously. This can be done with the help of co-injection molding, which takes away the worry about using a specific type of plastic.
The use of such advanced technology enables us to work fast without compromising quality. As a result, we manufacture about 400 mold sets in a year.
RYD Tooling has been in the mold making industry since 2006. During this period, our company has successfully worked on hundreds of injection mold projects for clients in various industries. We have gained vast experience in mold design and injection mold making through these project partnerships. They have also enriched our understanding of the injection mold requirements of different types of products. You can count on us to provide you with the right injection mold solutions.
Nanoplas brings innovative mold maintenance products to the plastic injection mold industry. Browse our selection of mold coatings, greases, cleaners & more!
Plastic injection molding is an automated process. A majority of the injection molding process is performed by machines and robotics which a sole operator can control and manage. Automation helps to reduce manufacturing costs, as the overheads are significantly reduced. Furthermore, with reduced labor force the overall cost of manufacturing the parts is reduced and this cost saving can easily be passed on to the customer.
RYD Tooling injection molds are made of steel. The type of steel that is used depends on the resin that will be used during the plastic injection molding process.
A bi injection molded structure is filled with resin using a plunger instead of the injection sprue that is used in ordinary injection molding.
Our factory is spread across 4,000sqm and divided into departments that specialize in different stages of the mold-making process. It is equipped with 11 high-precision CNC machines and 9 EDM machines. These machines are controlled using advanced computer systems and are, therefore, very accurate. We also recalibrate them regularly to prevent errors.
Our team of innovative designers develops injection mold designs based on the plastic part our client wishes to produce. We use high-precision CAD software to ensure every structural detail is captured in our mold designs.
Molds are used to form plastic parts during injection molding. This is done by injecting molten plastic resin into closed molds at high pressure and leaving it to cool and adapt the shape of the mold.
Large moldsare specially designed to form large plastic components like those used in the aeronautical and automotive industries.
Using injection molding also ensures the parts manufactured hardly require any work after the production. This is because the parts have more or less a finished appearance after they are ejected from the injection molds.
Our molds are designed to be durable and high-functioning. However, we understand that it is normal for tooling to develop faults. For this reason, we offer after-sale services to ensure our customers get the best user experience.
Once the injection molds have been designed to the customer’s specifications and the presses pre-programmed, the actual molding process is very quick compared to other methods of molding. Plastic injection molding process hardly takes times and this allows more parts to be manufactured from a single mold. The high production output rate makes plastic injection molding more cost effective and efficient. Typically, hot-runner ejection mold systems produce parts with more consistent quality and do so with faster cycle times, but it’s not as easy to change colors nor can hot runners accommodate some heat-sensitive polymers. Learn more about the key differences between hot-runner and cold-runner systems.
The injection molds are subjected to extremely high pressure. As a result the plastic within the molds is pressed harder against the mold compared to any other molding process. Due to this excessively high pressure, it is possible to add a large amount of details into the design of the part.
In addition to mold design and mold making, we offer comprehensive part design, 3D prototyping, and injection molding services. Each project is headed by a lead project manager who consults and updates the clients throughout the project.
Furthermore, automation allows for making precise and accurate injection molds. Computer aided design (CAD) and computer aided manufacturing (CAM) allow close tolerances during the making of the molds.
Injection molds are manufactured in separate parts that require assembly to form a complete mold. After production, we polish each part and evaluate it to ensure it is the right size and quality. The mold is then carefully assembled and tested for functionality.
RYD Tooling is an injection mold maker for numerous manufacturers of plastic injection molding parts across the world. Our clients operate in different sectors including the home appliance, electronic, and automotive industries among many others.
If you disable this cookie, we will not be able to save your preferences. This means that every time you visit this website you will need to enable or disable cookies again.
This website uses cookies so that we can provide you with the best user experience possible. Cookie information is stored in your browser and performs functions such as recognising you when you return to our website and helping our team to understand which sections of the website you find most interesting and useful.
RYD Tooling is well-versed in injection mold design and making for a variety of industrial applications. We utilize the latest techniques and machining equipment for efficient and precision mold manufacturing. Thorough analysis such as DFM, Mold Flow Analysis facilitates and expedites the production process, and enables the realization of your project.
Using the latest in technological equipment (EDM, multi axis CNC, and plastic injection molding machines), we are able to produce an injection mold with high quality and tight tolerance from simple to sophisticated design. Molds and parts produced by us have brought satisfaction to many clients from different industries like automotive, household appliances, electronic, furniture, aerospace, and other industrial markets.
In plastic injection molding, it is possible to use fillers in the injection molds. These filler reduce the density of the plastic while it being molded and also help in adding greater strength to the part after it has been molded. In fields where parts need to be strong and durable, plastic injection has an option that other molding processes do not offer.
Furthermore, due to high pressure during the molding process, complex and intricate shapes can easily be designed and manufactured which otherwise would have been too complicated and expensive to manufacture.
We obtain all our injection mold materials from vetted top-tier suppliers. We further require each supplier to provide certification documents to ascertain the authenticity of their materials. These stringent quality policies ensure that we deliver durable and reliable injection molds to our clients.
Once the mold design is approved, mold production begins. We use high-accuracy CNC and EDM machines and top-quality steel to manufacture precision molds. They have high tolerances and are reliable for long-term use. We also optimize them to be high-performing and cost-efficient.
Each product is covered under warranty for 5 years or its indicated life span. We provide replacement parts for repairs during the warranty period if the fault is not caused by negligent use. Our technicians respond to injection mold repair queries within 24 hours.
Plastic injection molding is extremely versatile method of producing parts and products. It is one of the preferred methods for manufacturing parts because it has multiple advantages over other methods of plastic molding. Not only is plastic injection molding simpler and more reliable, it is also extremely efficient. You should have no doubts about using this method to manufacture parts.
RYD Tooling design engineers analyze the accuracy and viability of each mold design using Mold Flow Analysis technology. They also evaluate its structure to determine whether it is optimized for the type of resin that will be used for injection molding.
GETTING A QUOTE WITH LK-MOULD IS FREE AND SIMPLE.
FIND MORE OF OUR SERVICES:
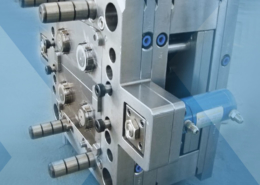
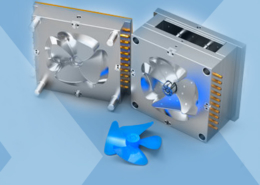
Plastic Molding

Rapid Prototyping
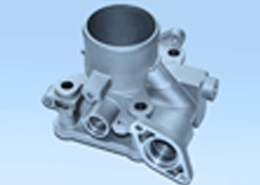
Pressure Die Casting
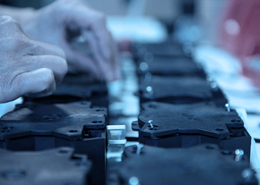
Parts Assembly
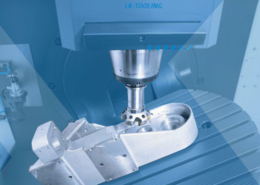