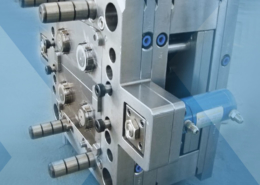
The Process of Creating a Plastic Prototype - prototype and plastic mold
Author:gly Date: 2024-10-15
Typical of part requirements for acrylic applications is the high degree of optical clarity and light transmittance afforded by these molding compounds. Light transmittance is 92%, which is comparable to optical quality glass. These optically clear plastics withstand exposure to UV radiation and will not discolor or fade when exposed to light. Acrylic material is also readily available in translucent and opaque colors that can be formed using the plastic injection molding process. Molding metal inserts into acrylic, commonly referred to as insert molding, is routinely performed at Rebling.
Do you have plastic injection needs?Well, you’re in the right place. Plastic injection moulding and tool making and design are just some of the services that we offer.
Our experience in moulding engineering thermoplastics is very well recognized here in Australia. Through knowledge gained by over 40 years building our business in this industry, we are confident of the quality of the advice that we provide. This confidence is important because choosing the right type of materials can often be very critical to a product’s success.
After you make the finalised decisions on the design and materials of the plastic part you want, the first step to getting the part plastic moulded is to build the mould.
Anchor Plastics is an Australian owned and operated company that specialises in Plastic Injection Moulding. We are dedicated to providing you, the client, with excellent service, high quality products, and low overall costs. We are also capable of meeting each client’s demanding lead time requirements, as we have 17 plastic injection moulding machines. Our machines range in size from 25 tons all the way up to 550 tons. These machines are running 24 hours a day, 5 days out of the week, moulding items ranging in weight from 1 gram to 2.2 kilograms. So, we are essentially always running the machines and working hard to make sure that we have your product finished in the most efficient and effective way and time that we possibly can.
Acrylic is one of the clear plastic molding materials the Rebling team is experienced at. Rebling has plastic injection molded acrylic for a variety of applications including lighting equipment, housewares and medical devices. If you are interested in acrylic molding, let’s first examine what acrylic material is. Acrylics are synthetic plastic materials that contain at least one derivative of acrylic acid. Acrylic material was first created in 1843 and patented nearly 100 years later by German chemist Otto Rohm The most common acrylic plastic is polymethyl methacrylate (PMMA).
Plastic injection moulding is the preferred manufacturing process when you want or need to make hundreds or thousands of the same plastic part. This process involves heating small plastic beads at a high temperature until they reach a liquid or near liquid state, and then injecting that material under pressure into the cavity of a metal mould.
Belonging to the class of amorphous thermoplastics, Acrylic possesses predictable material shrinkage values. Close tolerances are readily achievable with this material when using the plastic injection molding process at Rebling. High flow formulations necessary for molding thin-walled, difficult to fill parts are utilized by Rebling.
Design and manufacturing of tools is an important part of many industries. By creating the perfect tool, companies can improve their production efficiency and output.
In addition to the glass-like optical qualities of acrylic, the material is also noted for its resistance to ultraviolet and fluorescent lighting effects, excellent weatherability, and resistance to scratching. Several grades of acrylic material are suitable for food contact use, and because it is odorless and tasteless, it is used in applications such as refrigerator drawers and food storage containers. These molding compounds resist water, alkaline solutions, and weak acids but are dissolved by most organic solvents such as strong hydrocarbons, esters, and ketones.
Acrylic material has a Tensile Strength in the range of 8000-10,000 psi; a Flexural Modulus in the range of 425,000 psi and a Heat Deflection Temperature of over 210°F for some heat resistant grades.
Acrylic can be decorated using pad printing, hot stamping, and silk screening processes. Rebling has joined plastic injection moldings using both ultrasonic welding and solvent welding techniques. Machining operations; such as drilling, threading, tapping, routing, and turning; are additional services provided by Rebling on this material and other clear plastic injection molding materials.
Do you have a question or need further information about our injection moulding / custom moulding service? Complete the form below and one of our consultants will get in touch with you.
Copolymerizing acrylic with other monomers can alter its properties. For example, the addition of ABS significantly improves impact strength. When acrylic is blended with polycarbonate, the resulting impact strength of the copolymer is higher than polycarbonate by itself. The impact strength of acrylic and its copolymers decreases, however, as the ambient temperature decreases.
You may be wondering what types of industries need the services of a plastic moulding manufacturer such as Anchor Plastics. Well, the answer is: plenty of them, and even some that you wouldn’t think of. We mould the components needed for many of the well-known products in many sectors of Australian industry. Electrical, lighting, swimming pools, water filtration, hospitality, furniture, building, electronic, automotive, housewares, and scientific are just a few examples of some of the many industries that we supply the components for.
At Anchor Plastics, all of our products are always assembled and packaged to the highest standards and are thoroughly tested before they are packed and sent to our customers.
This process, the building of the mould as well as the finished product, is one that requires great precision and the use of specialist design software (CAD and CAM) and metal working equipment. The cost of this process varies depending on a number of factors, such as:
This is a very common question. Another one that you should ask yourself after you ask that one is whether or not you need parts made, and how else you would go about accomplishing that if not by plastic injection moulding.
Prior to issuing a final acrylic molding design, Rebling’s team will review your part design and offer suggestions to ensure that the end product meets the design intent.
Acrylic molding can sometimes be complicated. Acrylic is somewhat notch sensitive, so sharp edges should be avoided. Wherever possible, outside and inside corners should include a radius to minimize this notch sensitivity. The metal inserts used in insert molding should avoid sharp corners and edges to minimize the notch sensitivity of this material. Undercuts or entrapments should be avoided since they would break or fracture during part ejection. When necessary for part function, these features need to be incorporated through the use of slides in the mold which can increase the mold cost significantly.
GETTING A QUOTE WITH LK-MOULD IS FREE AND SIMPLE.
FIND MORE OF OUR SERVICES:
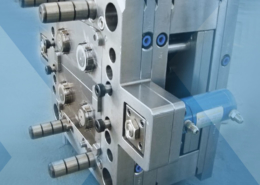
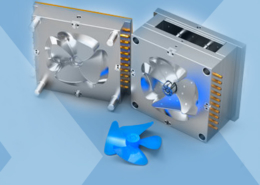
Plastic Molding

Rapid Prototyping
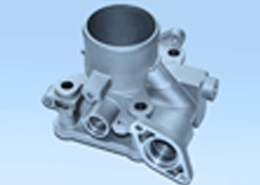
Pressure Die Casting
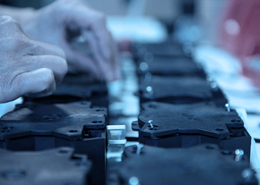
Parts Assembly
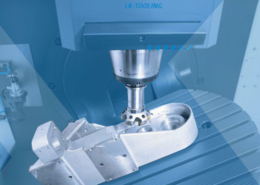