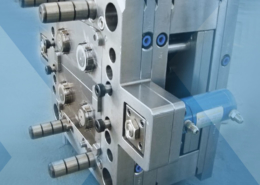
The outline of injection molding - shot mould
Author:gly Date: 2024-10-15
Injection molding tool steel is a carefully measured consideration in any custom injection molding project. Working with an experienced molder like Kaysun will provide balance in materials selection and give you the most value for your tooling dollar. Explore how to maximize your options in our white paper, 5 Key Considerations when Comparing Tooling Quotes.
The two shot process can also be accomplished with an indexing system (a roundtable rotating around a horizontal axis) with a primary and secondary station. While the first injection is accomplished at station number one, the second injection is accomplished at station number two. Each injection station is run by an independent injection unit. This allows injection speeds and pressures to be controlled for each material being utilized.
Eventually, H-13 tooling surfaces will become susceptible to corrosion brought about by chemically enhanced plastics, moisture, humidity and cooling water contamination.
Twin shot silicone rubber molding also allows manufacturers to take advantage of the best features of both materials and reduce costs because it reduces or eliminates post-molding assembly. The two-step process requires the use of only a single machine cycle because the mold incorporates both the thermoplastic and LSR injection. By consolidating multiple cycles to one, 2-shot molding lowers production costs and requires fewer operators, while producing more items per run.
The design and manufacture of steel tools are a considerable piece of a project’s budget. While a worthy investment, there are certain situations wherein tools designed using specialty materials may be appropriate.
If your injection molding project requires tight tolerances and high volumes, S-7 is the pre-hardened tool steel of choice.
420 stainless steel is relatively easy to machine unless hardened above 30 HRC. Also, if used in temperatures that exceed the relevant tempering temperature, mechanical properties are reduced.
Liquid silicone rubber is a versatile material that is used in countless applications in a variety of market sectors. One common use for LSR is in sealing applications due to its ability to maintain or return to its original shape despite repeated compression, its water repellant properties, and its thermal resistance. Some of the most significant advantages LSR has over thermoplastics include the following:
The most important aspect of two shot injection molding is the design of the tool. The tool must be designed to allow both stages of the part to be molded in the same tool to achieve maximum production efficiency. The design must consider two separate injection stages that can be rotated 180 degrees or oriented to allow a robot to transfer the components. In stage one, the substrate parts are molded and then rotated/transferred to the second stage to be over-molded.
However, the grade of injection molding tool steel chosen for production also has a major impact on project outcomes. Cycle times, part criteria, production volume, cost and maintenance expectations all must be factored in to align the steel with the need.
This article discusses the benefits of LSR as a material and the many advantages LSR two shot injection molding has over other common manufacturing methods.
LSR 2-Shot injection molding is also called multi-component injection molding, over-molding, and twin shot molding. LSR 2-shot molding consists of molding LSR directly onto a substrate (typically a thermoplastic) right after the substrate itself has been molded, using the same mold and injection molding machine. It is even possible to over-mold LSR onto LSR, with two separate durometers and colors. The benefit for manufacturers is the ability to integrate several functions, parts, and materials into one component — permanently fused.
Containing 13% chromium, 420 stainless steel is a high-quality tool steel that’s preferred for custom injection molding. The high carbon content provides:
In a time of limited resources and cost-cutting, budgets for new product design and development may also be limited. In some companies, the resources and experience necessary to successfully complete an LSR molding project are equally limited. SIMTEC is a leading provider of LSR 2-Shot injection molding services, and we can help you complete those projects successfully, economically and on time. Contact us today for more information about how SIMTEC can help you with your LSR 2-Shot injection molding needs.
LSR is often more expensive than other materials such as thermoplastics and HCR, but the value added from liquid silicone rubber far exceeds the initial investment — especially for fabricators of high-volume parts. LSR enables extended production runs with minimal labor and material waste. In fact, it’s possible to completely automate the process in which one operator can monitor and maintain multiple liquid injection molding machines simultaneously. This is a significant cost-saving benefit for manufacturers looking to increase process efficiency in the face of rising labor costs.
Custom injection molding projects are understandably focused on plastics selection. After all, the materials used to construct the parts have the greatest influence over quality and performance.
Overlooking this step or not properly understanding the interrelationship between the material being injection molded and the material doing the molding could be a costly error. Waste, defects, re-runs and line time can mount quickly.
During the second phase, another substrate part is being produced in the first position, resulting in a highly efficient, continuous cycle.
For all of its advantages, P-20 also has some challenges including not being able to meet ASTM-A681 minimums. Chiefly, it is best used with plastics that do not contain abrasives like glass fibers. There are also concerns around volume; P-20 that is not coated or surface-hardened will not stand up to high-volume production.
SIMTEC Silicone Parts is a producer of custom designed and manufactured LSR parts and LSR 2-Shot (LSR onto a substrate) components. LSR’s unique characteristics make it a good fit for a variety of industries and applications, and at SIMTEC we have produced billions of parts since our founding in 2002. While many injection molding companies started with plastic as the raw material and then expanded into LSR, SIMTEC was founded as a custom LSR parts manufacturer. We use our vast knowledge of LSR and the LSR two shot injection molding process to produce the highest quality parts for customers in a wide range of industries, including healthcare, automotive, industrial and electronic consumer products.
Tools made from specialty materials with high thermal conductivities can reduce overall production costs by about 25% compared to standard steel tools. If you’re interested in speeding up the cooling process of your next project, consider using tools made from specialty materials with high thermal conductivity, like MoldMAX®, aluminum or tungsten carbide.
The compression and transfer molding process, using plastic and high consistency rubber (HCR) as raw materials, was once the dominant manufacturing process in medical, aerospace, electrical, construction and industrial applications. In recent years, however, Liquid Silicone Rubber (LSR) 2-Shot injection molding has been the manufacturing process of choice across a range of industries for the fabrication of molded parts. The LSR 2-Shot molding process enables manufacturers to produce parts in a wide range of sizes and technical configurations, one of the many advantages 2-Shot injection molding has over compression and extrusion molding.
LSR 2-Shot injection molding is part of an overall growth story for the silicone elastomers market — the global market value of silicone elastomers was estimated to be $6.5 billion in 2013 and is projected to grow at a CAGR of about 9.28% between 2014 and 2019.
GETTING A QUOTE WITH LK-MOULD IS FREE AND SIMPLE.
FIND MORE OF OUR SERVICES:
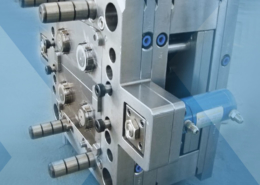
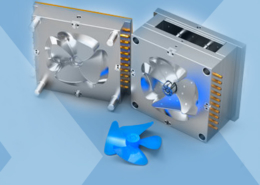
Plastic Molding

Rapid Prototyping
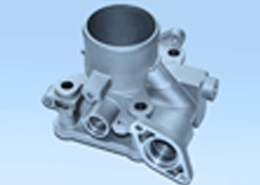
Pressure Die Casting
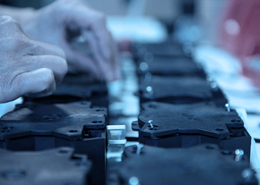
Parts Assembly
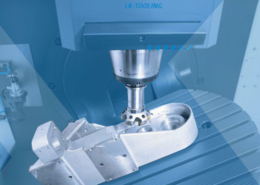