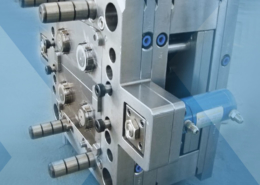
The Difference Between Normal and Medical Plastic ... - injection molding medica
Author:gly Date: 2024-10-15
Polymer - A substance that has a molecular structure consisting chiefly or entirely of a large number of similar units bonded together, e.g., many synthetic organic materials used as plastics and resins.
Once these new devices are produced, we assist our customers in transitioning the project into the production phase. Quality and customer satisfaction are our primary goals, and Aberdeen can work with both high and low quantity requirements with over 700 square feet of cleanroom injection molding space.
Multi-shot molding – A process where two or more plastic substances are injected into the mold to form a part. Toothbrushes are often manufactured using this technique.
Additives – These compounds are added to resins to improve the overall performance and appearance of finished products. A key trend in this area today is using additives that are made from organic materials such as eggshells, wood pulp, rice hulls or materials that improve the biodegradability of the plastic.
Over molding – A two-shot process, in which two plastic substances, are injected into a mold sequentially, usually a harder base material with a coating of softer material.
Masterbatch – A solid or liquid additive for plastic used for coloring plastics or imparting other properties to plastics.
Injection molding is a very common way to form plastic parts and components. Depending on the material, the parts can be very strict with their tolerances as well as easy to process. Injection molding is one of the most common types of forming plastics. It is used in a variety of industries and not just for medical injection molding. In fact, you probably have a wide variety of injection molded parts all around you and simply don't know it. Your basic pens, your keyboard, and even your phone have injection molded components in them.
Flash or burrs – A thin lip or protrusion beyond the body of the part that is generally caused by poor clamping force, improper mold design and/or mold damage.
We provide assistance throughout each stage of your program, from design recommendation through mold tooling fabrication, prototyping, first article approval, process validation, full scale production medical molding, and transfer of turnkey system to customer facilities if requested.
Blow molding – The process follows the basic steps found in glass blowing. A parison (heated plastic mass, generally a tube) is inflated by air. The air pushes the plastic against the mold cavity to form the desired shape. Once cooled, the plastic is ejected. This method is used to make plastic bottles.
Bridge tool – An injection mold that makes parts until the final tool is completed. These molds or tools are not meant to be production tools.
Flow marks - A wavy pattern or discoloration caused by a slow injection speed which allows the material to cool too quickly.
Delamination - This defect appears as a flaky surface layer on the part and is often caused by contamination or moisture in the resin pellets.
Flash gate – An alternative to a fan gate, which conveys the melted resins into a thinner gate section creating a linear melt flow into the cavity.
Alloy – A plastic alloy is a physical modification of an existing plastic to achieve higher performance and or functionality. These alloys are often used in the automobile industry and to replace metal parts.
In the medical field, we often see metal combined with the plastic part. This is called insert molding and is a very common practice for injection molders to do. You see this all over the medical arena from needles to EKG hook up leads and more.
Tie bars - Bars which provide structural support to the mold in the press. The spacing between the tie bars dictates the size of the mold that can be placed into the injection machine. The mold opens and closes riding on the tie bars.
Prime examples were molding non-communicating passageways through a plastic manifold, molding critical tolerance pacemaker components, and even molding around glass formations without breaking or cracking. Our advanced injection molding equipment makes even the most difficult projects possible.
Core - A protrusion or set of matching protrusions, which form the inner surface of a plastic part. They are often considered they “male” side of the part.
Aberdeen’s primary goal is total customer satisfaction for even your most challenging projects. Our company culture is one of honor, respect and service with the highest degree of competence and professionalism that you will find anywhere.
However, there are other types of plastics called thermosets that also can be used for injection molding, but the process is far different. These materials are most likely not going to be used for medical molding as they cannot be recycled as easily as the thermoplastic materials. Because of this, you don't see thermosets used as often as you do thermoplastics. A good example of a thermoset is your car tires. This is where they cannot be melted down and reshaped into something.
Posted by Kyle Coblentz | 02 / 19 / 14 0 Comments
Colorant – A pigment system, usually in pelletized form, powder or liquid, which is mixed with resin to produce the desired color.
Weld line - Also called a knit line, the juncture where two flow fronts meet and are unable to join together during the molding process. These lines usually occur around holes or obstructions and cause localized weak areas in the molded part.
Vent – A channel from the mold cavity that allows gas and air to escape as resin is being injected into the cavity to prevent many types of defects from occurring.
EDM or electric discharge machining - A manufacturing process used to create molds, where the shape of the mold cavity is obtained by removing metal material using electrical discharges.
Medical injection molding is a manufacturing process that produces plastic medical devices and components. It involves melting plastic resin pellets and injecting the molten material into a mold to create a specific shape. This process allows for precise control over the product's size and shape and is subject to strict quality and regulatory standards.
Thermoplastic - A material that can be heated and cooled repeatedly without changing the material structure. Highly recyclable.
Hot-runner mold – Hot runner molds consist of 2 plates that are heated with a manifold system. The manifold sends the melted plastic to nozzles which fill the part cavities.
Compression molding - The name of this molding method says everything. A heated plastic material is placed in a heated mold and is then compressed into shape. The plastic can be in bulk but often comes in sheets. The heating process, called curing, insures the final part will maintain its integrity. This molding method is often used to make large objects such as automobile components.
Medical injection molding is a core technology of Aberdeen Technologies and represents a cutting edge solution to the manufacturing needs of healthcare companies who produce medical molded devices. As an insert molding manufacturer, we provide assistance to device manufacturers who approach us with new product concepts and ask us to mold parts for clinical trials and marketing evaluations.
Release agent – A compound, which is sprayed on the mold, or as an additive, molded into the part to help facilitate the release of the part.
Thermoset – A material, which when heated, is pressed or molded into a shape. The heating process changes the structure of these materials, and for this reason they cannot by re-heated.
Sometimes the components need to be manufactured separately and then assembled. This is very common in many cases and this can be done by hand or robot.
Prototype tool – Also called a soft tool, a preliminary mold built to produce prototype parts and used to make adjustments to the final production tool.
The most common types of materials used in medical insert molding are thermoplastics. These are materials that can be heated up into a molten state and pushed through a barrel into a mold. These molds can simply be open and shut type designs, which are what you would expect for, say a simple product such as a cake mold. Or they can be very complex with moving side parts called slides. Of course, the simpler the mold the better for maintenance and longevity. However, complex parts will need these complex designs in order to produce the desired part.
Blister – As the name says, this is a part defect which appears as a small bubble or blister on the surface of a part and it generally created by gas or air bubbles.
Degassing – Opening and closing of a mold to allow gas to escape. Trapped gas and/or air can cause parts defects such as blistering and bubbles.
Cold slug – A defect characterized by a small non-uniform area on the part caused by an improperly heated piece of plastic becoming attached to the part.
Annealing - Annealing is the heating and slow cooling of a plastic part which allows the polymer chains to recoil and relieve internal stresses.
Undercut – Can be a design flaw that results in an indentation or protrusion that inhibits the ejection of the part from the mold. Other times undercuts are designed into a mold to ensure a part holds onto the correct side of the mold.
The process is capable of making FDA approved medical devices that are both durable and reliable. This type of molding can also be used to make prototypes to send and get the much-needed FDA approval. Medical injection molding can be performed in a clean room and the components can be sterilized without harm as well. Let's take a look at injection molding.
GETTING A QUOTE WITH LK-MOULD IS FREE AND SIMPLE.
FIND MORE OF OUR SERVICES:
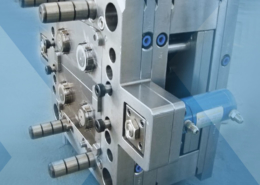
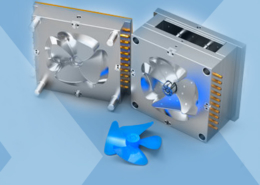
Plastic Molding

Rapid Prototyping
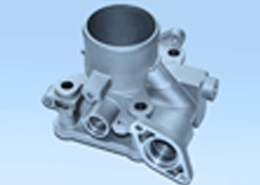
Pressure Die Casting
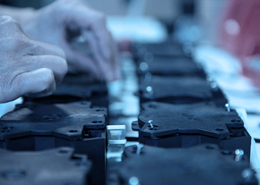
Parts Assembly
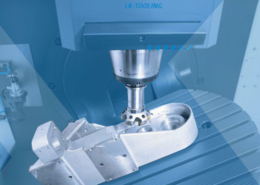