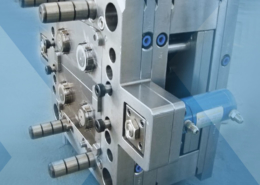
The best heat-resistant plastics for injection molding - injection moldable plas
Author:gly Date: 2024-10-15
This article was written by engineers from the BOYI team. Fuquan Chen is a professional engineer and technical expert with 20 years of experience in rapid prototyping, mold manufacturing, and plastic injection molding.
With state-of-the-art technology and a team of experienced professionals, we ensure that every step of the injection molding process is executed with precision and accuracy. We pride ourselves on delivering superior quality, fast turnaround times, and competitive pricing, making us the preferred choice for businesses seeking reliable injection molding solutions.
Patients benefit from the precision, quality and innovation Seaway Plastics brings to the table when meeting the unique specifications of every OEM engagement. To date, the company is helping OEMs to improve patient outcomes in the following areas:
Injection mold slide design is a crucial aspect of creating complex plastic parts. By understanding the working principles, considering key design factors, and adhering to best practices, manufacturers can produce high-quality, intricate parts efficiently and reliably.
Injection molding is a critical manufacturing process used to produce a wide range of plastic parts with high precision and efficiency. One of the key components in the design of injection molds is the slide mechanism, which is essential for creating complex geometries that cannot be achieved with a simple two-part mold.
With five manufacturing locations across the U.S. and the ability to work in close partnership with original equipment manufacturers (OEMs), Seaway Plastics creates end-to end solutions for the safe and cost-effective manufacturing of a broad range of precision medical components, devices and assemblies that are used throughout the medical, healthcare and life sciences sectors. Such products are used every day in clinical settings to support life-saving and life-improving medical procedures and other healthcare interventions that ensure optimal patient health outcomes.
Across numerous medical, life sciences and healthcare applications, Seaway Plastics works closely with OEMs to produce high-quality products that are used in the following applications:
Seaway Plastics has been a trusted manufacturer of high-quality components, products and assemblies for a variety of Class 1, 2 and 3 medical devices for more than four decades. To ensure a sterile manufacturing environment, its facilities have ISO 13485 Class 7 and 8 certified cleanrooms that prevent airborne contaminants as small as 0.3 and 0.5 microns, respectively, during molding and assembly operations. This ensures that finished products that are intended for use in medical, healthcare and life sciences applications meet all industry standards and regulatory requirements.
For any questions or inquiry about Mold manufacturing/Injection molding/Over molding/Insert Molding/Die casting , please contact one of our knowledgeable applications engineers at [email protected]
Medical injection molding using highly engineered materials is a proven option for creating precise industrial parts and complicated assemblies while keeping costs and risks low and quality and reliability high. Seaway Plastics has four decades of experience providing custom, end-to-end solutions to enable the manufacture of specialized products that are used during numerous diagnostic and life sciences applications.
The wedge locks the slider in place during the molding process and facilitates its movement during mold opening and closing. It usually interacts with cam pins or hydraulic cylinders to control the slider’s motion. The wedge ensures that the slider operates with precision and consistency, which is vital for producing complex geometries accurately.
Collectively, these benefits enhance reliability and reputational value — and can provide competitive advantage — for the OEM. For the healthcare professionals and patients who rely on such state-of-the-art products, the benefit of solid teamwork that consistently delivers high quality and reliability during manufacturing brings peace of mind.
Implant-delivery systems play a critical role in modern healthcare interventions, as they are used to support the accurate placement of therapeutic medical devices during surgical operations. OEMs that supply such specialty products to the surgical community must choose their manufacturing partners carefully to safeguard the integrity of the final products and enable optimal, consistent healthcare outcomes.
This type of guide pin, also designed for 2 or 3-part plates with thick plates and large mold cavities, may exhibit poor stability and processability. Despite having a similar length-to-diameter ratio of 1.5 or higher, these guide pins might not perform as well in maintaining alignment and smooth operation.
These guide pins are designed to provide excellent stability and a matte surface finish, making them ideal for molds with thin or clamped plates. Their design ensures precise alignment and smooth operation within the mold system.
The forming surface is the part of the slide that directly shapes the plastic part. It contains the negative geometry of the desired feature, such as an undercut or hole. The precision and finish of the forming surface are crucial for achieving high-quality molded parts.
Seaway Plastics brings precision, quality and innovation to every customer relationship. Examples of the types of specialized diagnostic products that are used to inform and support healthcare diagnosis and treatment decision making include (but are not limited to):
The press block secures the slider in place during the injection phase, ensuring it does not shift under the pressure of the molten plastic. Once the mold opens, the press block releases the slider, allowing it to retract and enable part ejection. This component is crucial for maintaining the integrity of the molded features during the process.
Providing a full range of services that enable the manufacturing of complex products for these high-stakes applications, Seaway Plastics works closely with OEMs and CDMOs to select the most appropriate material from a broad array of medical-grade plastics and silicone and provides a complete range of engineering and medical injection molding services. Each of Seaway Plastics’ facilities is ISO-13485 certified and offers comprehensive process-validation services to ensure that all operations meet the prevailing quality and regulatory requirements.
Distinguishing between injection mold slides and injection mold lifters can be perplexing. Let’s navigate through their contrasting characteristics to shed light on their distinct roles and functionalities in injection molding processes.
Cam pin slides are the most prevalent type of slide action in injection molding. These slides utilize an angled guide pin, which withdraws from an angled hole inside the slider body. Key features and functions include:
The wedge locks the slider in place during the molding process and facilitates its movement during mold opening and closing. It usually interacts with cam pins or hydraulic cylinders to control the slider’s motion. The wedge ensures that the slider operates with precision and consistency, which is vital for producing complex geometries accurately.
Partner with BOYI for your next injection molding project and experience the difference that precision and efficiency can make. Contact us today to learn more about our services and how we can help bring your vision to life.
The guide pin also prevents displacement of inserts when they are used. For optimal performance, the guide pin should be positioned 15 to 25 mm above the product. Additionally, the slider guide pin, located 10 to 15 mm below the mold guide pin, directs the movement of the slide, ensuring it operates correctly.
In this case, a slider mechanism is needed. Before injection molding, pull the slider horizontally to ensure smooth demolding. So, the slider is a component within the mold structure that can move along the axis of the mold. It is usually used to adjust the opening height of the mold and assist in demolding and other functions.
Hydraulic slides are employed when cam pins might exert excessive pressure on the gibs, which control the slide’s linear motion. These slides use hydraulic cylinders to move the slide, offering several benefits:
Seaway Plastics has four decades of experience and a proven track record engineering, manufacturing and assembling high-purity medical devices that are designed for disposable, single-use applications.
Safety measures, such as implementing limit switches for ejection under slide details and ensuring proper locking mechanisms, are essential to prevent accidents and ensure operator safety. Regular training and adherence to safety protocols are also crucial for safe operation.
An injection mold slider is a component used in injection molds to create features like undercuts, holes, or grooves in molded parts. Its role is to facilitate the ejection of the molded part from the mold cavity by moving laterally to release the part from the mold.
By partnering with Seaway Plastics to streamline all steps in the complex manufacturing process, OEMs are able to be more competitive, safeguard their own brand reputation and focus on meeting the needs of their end customers — healthcare professionals treating patients in hospitals, physician practices and other clinical settings. Ultimately, this team effort is critical to support the shared end objective — which is to support and enable optimal health outcomes for patients.
There are many important advantages to selecting a manufacturing partner that is able to take ownership of every step in the process in-house — from engineering services to prototyping to fully validated production — without the need to involve additional partners or create multiple outsourcing arrangements. Specifically, for OEMs, the demonstrable advantages such a tightly integrated approach include:
In injection molding, it is common to encounter parts with various intricate features such as grooves, holes, or undercut structures. Normally, during the injection molding process, once the parts are molded, the core and cavity must separate, and ejector pins are used to remove the part from the mold. However, when parts have undercuts, holes, or grooves, they prevent the core and cavity from separating normally.
The ability to produce precise surgical robotic tools and assemblies that meet all of the rigorous engineering and regulatory specifications is another way in which both Seaway Plastics and its OEM customers are supporting surgeons and other medical practitioners in their quest to guarantee accuracy and repeatability during surgical procedures — thereby enhancing patient safety and overall health outcomes.
For any questions or inquiries regarding rapid prototyping, CNC machining, sheet metal fabrication, or vacuum casting, please contact coco at [email protected].
The development and use of surgical robotic devices and platforms continue to revolutionize how lifesaving and life-enhancing surgeries are performed. Such devices are complex mechanical assemblies with many parts, all of which have extremely exacting engineering requirements and zero tolerance for deviation.
Within the realm of medical products that are used to support the health journey of patients managing respiratory conditions, examples include:
These guide pins are used for molds with 2 or 3-part plates, thick plates, and large mold cavities. They feature a length-to-diameter ratio of 1.5 or higher, ensuring sufficient length to maintain alignment despite the mold’s thickness and size.
To enable end-to-end project management for complex manufacturing projects, Seaway Plastics is able to manage each of these critical steps:
Proper cooling helps prevent warping and ensures the dimensional stability of molded parts. Injection mold sliders with sufficient cooling channels can help maintain consistent part quality and reduce the risk of defects.
Seaway Plastics brings precision, quality and innovation to every customer relationship. Recent examples of the types of specialized products produced for OEMs in this sector include (but are not limited to):
The wear plate is a protective layer that reduces friction and wear between the slide and the mold. It extends the lifespan of the slide by preventing direct contact between moving parts, thereby minimizing wear and tear. Wear plates are usually made from materials with high hardness and low friction coefficients.
OEMs that partner with Seaway Plastics to produce single-use disposable medical devices for use throughout the medical, healthcare and life sciences sectors gain peace of mind and reliability, knowing their manufacturing partner can handle the project from start to finish, from DFM all the way through final product manufacturing, assembly and validation.
Seaway Plastics offers a deep bench of DFM, tooling and injection molding expertise, and experience working with the broadest array of highly engineered materials. This supports the cost-effective, reliable precision manufacturing of many specialized parts, components and final products that are used to support medical, healthcare and life sciences applications.
Different types of slide actions are used depending on the specific requirements of the molding process. The most common types of slide actions include cam pin slides and hydraulic slides, each offering distinct advantages and applications.
At BOYI, we’re dedicated to delivering unparalleled precision and efficiency in every injection molding project. As a leading provider of injection molding services, we specialize in bringing your ideas to life with exceptional quality and attention to detail.
Affordable high precision plastic molds and machined parts available for any order size | Contact our experts or engineers now for a quote!
Their detailed working mechanism involves several stages, each critical for ensuring the smooth operation of the molding process. Here’s an in-depth look at the working mechanism of injection molding sliders:
The slide body is the main structural element of the slide mechanism. It holds the forming surfaces and other components, transferring the mechanical forces required for the slide’s movement. The body must be robust and made from durable materials to withstand the repeated stress and high temperatures of the injection molding process.
Injection mold sliders typically consist of a guide pin, slider body, forming surface, press block, wear plate, wedge, and locking mechanism. These components work together to facilitate the sliding action and ejection of molded parts.
With access to the most appropriate, state-of-the-art thermoplastic and thermoset options, Seaway Plastics helps OEMs to select the right materials — those that will deliver the specific suite of performance characteristics that are required by the finished parts, products or assemblies. Our customers have the opportunity to choose from a wide range of highly engineered materials, including but not limited to:
The slide mechanism consists of several key components, each playing a specific role in ensuring smooth and efficient operation. Here is a look at the main components of an injection mold slide:
The guide pin ensures precise alignment and movement of the slide within the mold. It guides the slide along a defined path, maintaining the correct positioning and orientation during the mold’s opening and closing cycles.
GETTING A QUOTE WITH LK-MOULD IS FREE AND SIMPLE.
FIND MORE OF OUR SERVICES:
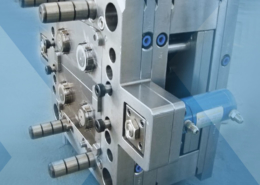
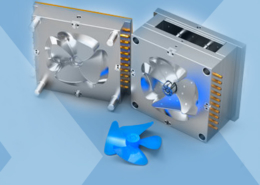
Plastic Molding

Rapid Prototyping
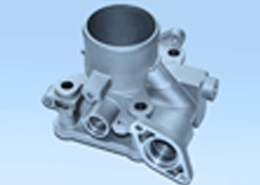
Pressure Die Casting
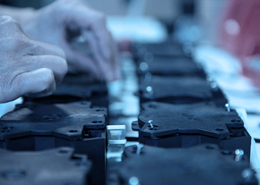
Parts Assembly
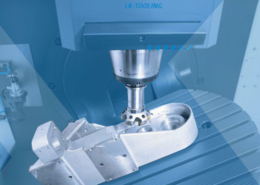