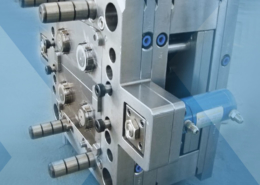
The best heat-resistant plastics for injection molding - heat molded plastic
Author:gly Date: 2024-10-15
We do quoting a little differently. When you request an injection molding quote, you'll not only receive accurate pricing, but also a manufacturing analysis—within just a few hours. Our online quoting platform also provides you with gate and ejector pin layouts and a price curve tool to help select the best tooling option for your project.
Aluminum moldsStandard lead times as fast as 7 daysTolerances of +/-0.003 in. plus resin tolerance (in./in.)Set-up fees apply to each run Consultative Design Services (CDS)Finishing OptionsNo minimum order quantities (MOQ)Quick-turn shipping in as fast as 1 day
Like any production process, plastic injection molding manufacturing can have problems and faults. Short shots, often known as "shorts," are one of the most typical quality concerns when the final product is incomplete because the mold did not entirely fill. This article will examine the most frequent causes of this issue and how plastics manufacturers can troubleshoot short shots to maintain high-quality and lean production.
No one ever said that designing and manufacturing molded parts was easy. Our goal is to get you through it quickly and with quality parts. A good starting point is our Design for Moldability Toolkit.
There are a variety of tools, procedures, and materials available for manufacturers to avoid short-shot defects. Four of the most tried-and-tested remedies are listed below:
Consult Flying Tiger today if your business is looking for a partner to co-create reliable, high-quality manufacturing outputs.
Yes, we offer a production tooling option called on-demand manufacturing. This tooling option provides several benefits: lower piece part price, multi-cavity capabilities, guaranteed tooling for the life of the project (we will cut a new tool if it wears out), and first article inspections.
Design for Manufacturing FeedbackEvery quote includes real-time pricing and design analysis. We evaluate your 3D CAD and help identify any features that may pose challenges during the molding process such as difficult to machine undercuts and insufficient draft.
Additionally, because the filling speed is excessively high, chances are that there is insufficient time to release the air via the separating surface.
Flow restrictions, hesitation of flow, and inadequate venting are all common short-shot defects due to inadequate mold design. Flow restrictions often come from the positioning, dimensions of runners and their gates, and how the molten plastic is poured into the mold.
Injection molding is plastic manufacturing process that can produce high quality parts at scale. It's typically used for low- to high-volume production but our aluminum tooling can also make prototyping runs economical.
We combine scientific (or decoupled) molding techniques, which optimize and lock in processing parameters to ensure part consistency—with extra attention paid to critical-to-quality dimensions using our proprietary automated CMM process. Plus, with every order you'll get:
Another potential reason is that the vacuum condition is not suitable for molds—Molds require a place for displaced air to escape, or they will develop air traps or poor venting.
Our digital factories create prototypes and low-volume parts fast, while our manufacturing network, offers advanced capabilities and volume pricing.
The secret to effective manufacturing and preventing either flow or pressure concerns is to match the right part with the proper molding machine.
Proto Labs, Inc. 5540 Pioneer Creek Dr. Maple Plain, MN 55359 United States P: 877-479-3680 F: 763-479-2679 E: [email protected]
We have wide selection of more than 100 thermoplastic and thermoset materials. And if you're looking for alternative material options, check out our guide to resin substitutes for ABS, PC, PP, and other commonly molded plastics.
The most frequent cause of failure to fill the mold is the appearance of something that interferes with the flow, and one of the leading candidates for flow issues is the type of plastic polymer itself.
In most cases, we can maintain a machining tolerance of +/- 0.003 in. (0.08mm) with an included resin tolerance that can be greater than but no less than +/- 0.002 in./in. (0.002mm/mm).
We have two unique offers to meet your needs wherever you are in the product lifecycle. Our prototype injection molding process helps you cut product development cycles by weeks—sometimes months—and bridge to production with injection-molded parts within days. Our On-demand Manufacturing process is designed to meet your production needs, and helps you qualify parts quickly to seamlessly transition into production with scientific molding, in-process CMM inspections with GD&T, and a full suite of secondary operations to make sure that your parts show up and perform as expected.
Overall, several factors can lead to the occurrence of short-shot defects, and they all have mutually limiting and influencing effects. Manufacturers must consider how these factors relate to one another, in order to devise a solution to reduce and correct short-shot defects. Note that It is often an ongoing process of monitoring and reviewing.
Therefore, beyond the choosing material, better control of mold and melt temperatures also aids in enhancing plastic flow. Flying Tiger offers a range of mold temperature controllers that help you achieve just that.
Overmolding and insert molding are two-part injection molding processes where one material is overlaid onto a second substrate part or metal insert to create a single component.
Make the move from prototyping to on-demand manufacturing for affordable, high-quality molded parts within days. Better yet, your prototyping tool is free once you shift to an on-demand manufacturing tool. Working with a single supplier that provides free design consultation services also massively speeds up the manufacturing process, allowing for greater supply chain flexibility, more consistent parts, and making qualification a breeze.
Poor venting happens when air is trapped during filling the cavity, creating counterpressure. When the melt is first injected into the hollow, under most circumstances, it immediately seals the cavity, trapping air in the remaining local spaces.
Liquid silicone rubber molding is a thermoset process that mixes a two-component compound together, which is then heat cured in the mold with a platinum catalyst to produce a final part.
No Minimum Order Quantities (MOQs)Procuring parts on demand, without MOQs, helps you manage market or demand volatility and provides a cost-effective source for bridge production, line-down emergencies, end-of-life production, or product customization.
Unmatched Lead TimesReduce your product development cycle by weeks—sometimes months—and bridge to production with injection-molded parts within days. Some injection molding orders can ship in as fast as 1 day.
Get machined parts anodized and chromate plated with our quick-turn finishing option. Eligible materials include aluminum 6061/6082 and 7075.
Injection molding is widely used for plastic part production in medical, consumer, and automotive industries. Typical parts include:
Therefore, it is squeezed instead, leaving some partially empty spaces in the cavity and shortening the shot of the molded item. To remove the air, the process must have vents built or ejection pins installed.
Injection Molding ExpertiseWe'll work with you throughout the course of your project to help you quickly move from prototyping to production, including finishing options and inspection reporting.
For instance, an oversized machine may have trouble controlling pressure if the shot size is less than 25% of its capacity, whereas an undersized machine will not have enough pressure or ram speed. Meanwhile, the barrel and mold wall should be heated to prevent the molded plastic from cooling too quickly.
Because of the initial capital investment in tooling, injection molding makes sense for higher volumes of parts. Our mold cost starts at $1,495 and will vary depending on part geometry and complexity. Other factors that will impact injection molding cost are lead times and material.
These holes frequently appear around the borders of the finished product or in areas where the mold wall is typically thin—these areas are the last places a mold would commonly fill.
Tough Black (Loctite Henkel 3843) and Ceramic-Filled (BASF 3280) are two new advanced photopolymer materials now available for 3D printing.
Manufacturers can immediately notice that the choice of material affects the flow or movement of the molten plastic inside the mold chamber in the mold cavity because it is a recurring factor in many problems.
With many accumulated years of experience with numerous domestic and foreign clients, Flying Tiger is confident in assisting corporate customers in quickly identifying the cause of short shots and other injection molding defects, thereby assisting in cutting down on resource waste and boosting product yield.
Short shots are one of the most frequent problems with plastic injection molding. There are numerous causes of them, but the primary ones are improper injection pressure and speed, including uncontrolled pressure loss brought on by resistance.
This complete reference guide walks you through everything from quoting, design analysis, and shipment to best practices that ensure your model is optimized for molding.
The imbalanced flow in each cavity of a multi-cavity mold can generate local short shots. But when the injection molding machine's capacity is adequate, this defect is primarily brought on by the uneven flow in each gate or the uneven distribution of the mold cavities.
A "short shot," as the name suggests, occurs when the mold-forming filling stops before the mold chamber is fully filled with the melt, leaving holes or thin sections and producing a defective product.
Plastic injection molding is a manufacturing process where resin in a barrel is heated to a molten state, then shot into a mold to form a final production-grade thermoplastic part.
Our helpful design aid demonstrates part features that are too thin or too thick, bad bosses, right and wrong ribs, and other considerations to be mindful of while designing parts for injection molding.
Nozzles, sprues, runners, gates, and thin product walls are among the parts that could obstruct melt flow. By raising the nozzle's diameter and temperature, besides utilizing a nozzle with a low flow resistance, the flow resistance of the nozzle can drop to the desired level.
Overall, it is crucial to comprehend the various varieties of plastic injection molding equipment and how varying sizes and types might be beneficial.
The production line might have a resin with a high viscosity measured by the Melt Flow Index (MFI), depending on the chosen material. MFI is a good starting point, even though it may not tell the complete story since there are two other factors of concern that may also be involved.
In plastic injection molding, a flow hesitation occurs when the flow slows down or stops due to variations in mold thickness. Inconsistent mold thickness causes the flow range of the melt to be too broad and its flow resistance to be excessive.
GETTING A QUOTE WITH LK-MOULD IS FREE AND SIMPLE.
FIND MORE OF OUR SERVICES:
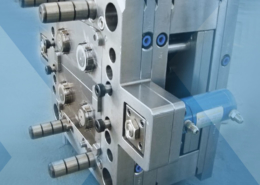
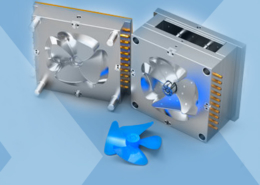
Plastic Molding

Rapid Prototyping
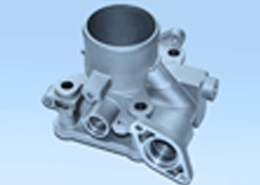
Pressure Die Casting
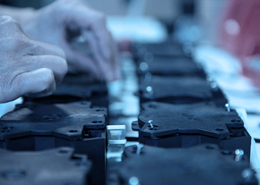
Parts Assembly
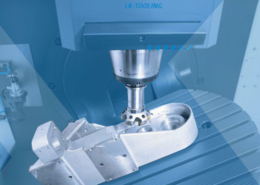