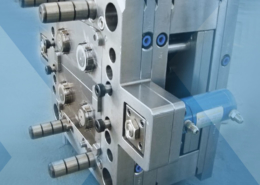
The Benefits of Two Shot Injection Molding - two shot injection molding
Author:gly Date: 2024-10-15
Ripley Dynamics is committed to providing cost-effective PVC moulding solutions without compromising on quality. Our 3D printing technology allows us to produce high-quality moulding at a fraction of the cost of traditional methods. Whether you need crown moulding, baseboard moulding, or any other type of PVC trim, we offer affordable options that fit your budget. Despite the lower cost, our PVC moulding is durable, easy to install, and resistant to moisture and pests. By choosing Ripley Dynamics, you can achieve the elegant and polished look you desire without breaking the bank. Our cost-effective PVC moulding is perfect for homeowners and businesses looking to enhance their spaces while staying within budget.
In the consumer goods industry, polypropylene is preferred for its strength and the ability to be molded. PP is used in small appliances like blenders and hairdryers because it offers impact strength and ease of molding. Polypropylene is safe and durable and it is used often in injection molding toys. Furthermore, polypropylene’s durability is also used in household products such as bins for storage and utensils in the kitchen.
PP Plastic Injection molding provides an advantage of mass production of identical plastic parts. High volumes- from a thousand to millions of identical parts can be produced at one time. Because the intended mold is reused several times in the part’s manufacturing process. This makes polypropylene injection molding another suitable option to meet the large demand and ensure that the products produced are of equal quality, simultaneously.
The extrusion die is a critical component in the process. It has to be designed to not allow the die to swell and control the flow of the material that is being extruded to achieve the desired quality of the final product.
Polypropylene is widely used in food packaging since it is safe and has a longer lifespan. Take-out containers and food storage products such as cups and containers are made from PP foam for thermal insulation and protection. PP material is used in making plastic cups and bottles for beverages and food products since the material does not react with moisture or chemical substances.
They include Homopolypropylene (PP-H) for rigidity, Random Copolymer Polypropylene (PP-R) for flexibility, and Block Copolymer Polypropylene (PP-B) for impact resistance.
Crown moulding PVC from Ripley Dynamics brings a touch of elegance to your home or office. Our 3D printed crown moulding offers the perfect combination of beauty and functionality, enhancing the transition between walls and ceilings. This type of moulding is ideal for adding a refined, classic look to living rooms, dining areas, and other spaces. Our crown moulding PVC is available in various styles and sizes, allowing you to choose the perfect design to complement your décor. In addition to its aesthetic benefits, our moulding is resistant to moisture and pests, ensuring it remains in pristine condition for years. With Ripley Dynamics, you can enjoy the timeless charm and durability of high-quality crown moulding PVC.
This article gives more information about polypropylene (PP) as an engineering plastic, including the different types available, the properties of the PP, and the complexities of the injection molding process. It also examines the challenges associated with selecting the right equipment, addressing issues related to product design, and discussing the fundamentals of mold design. In the same vein, the article discusses some of the major defects that are likely to occur during production and how to correct them.
Ripley Dynamics is your go-to source for architectural PVC moulding, ideal for both residential and commercial building projects. Our 3D printing capabilities allow us to create moulding that meets the specific requirements of architects and builders, offering versatility and precision. Architectural PVC moulding adds a refined touch to building exteriors and interiors, providing both decorative and structural benefits. We work closely with clients to develop custom solutions that enhance the design and integrity of their projects. With our focus on quality and innovation, Ripley Dynamics delivers PVC moulding that not only meets but exceeds industry standards, making us a trusted partner in the construction industry.
PP-B is a block copolymer polypropylene that has a block structure with ethylene thus making it have better impact strength and elasticity compared to PP-A. This type is applied in the automobile industry, in the manufacturing of shockproof packaging material and other heavy-duty consumer products. The automotive sector and protective packaging industries are ideal for PP-B because of its flexibility and damping properties in stressed applications.
When designing living hinges in polypropylene, it is good to work at a thickness of between 0.2 mm to 0.51 mm. For optimum performance, the radii should be wide and the hinge should have a flat shoulder. This design approach provides flexibility and strength to withstand the usage of the hinge when used several times.
To ensure the best PP material and injection molding production, it is wise to seek advice from an experienced supplier. An experienced provider can provide recommendations on the most suitable PP plastic injection moldings for your product’s functional requirements and the final product’s appearance, ensuring a successful project.
All in one service for new product development from part design, PCB design, prototyping, testing, mold/die/tooling making, massive production, assembly, inspection, and packing.
Ripley Dynamics is committed to providing high-quality PVC moulding solutions that cater to various needs and applications. Our expertise in 3D printing, combined with our dedication to customer satisfaction, ensures that we deliver products and services that enhance the value and appeal of your projects. Contact us today to learn more about how our PVC moulding services can benefit you.
PP-H, or homopolypropylene is the most used type of polypropylene, characterized by high rigidity and strength as a result of crystalline structure. It is commonly employed in uses where the material will be exposed to a lot of force, as it is with containers, auto parts, and more. PP-H has good chemical and heat resistance hence; it is used in products such as buckets and other household utensils. However, it is less flexible and therefore not as effective in more flexible applications.
Polypropylene pipes are used in plumbing and industrial practices since they are chemically inert and can be easily installed. PP plumbing pipes are used for both hot and cold water because of their strength and resistance to corrosion. In industrial applications, the use of polypropylene pipes is in chemical and waste handling systems, and the material is well endowed with the strength and capability of withstanding aggressive conditions.
Chair rail moulding PVC from Ripley Dynamics offers both functionality and style, protecting your walls while adding a decorative element to your space. Originally designed to prevent chairs from damaging walls, chair rail moulding now serves as a stylish design feature that can enhance the look of any room. Our 3D printed chair rail moulding PVC is available in a variety of designs, enabling you to choose the perfect match for your décor. This type of moulding can be used to create visual interest by dividing walls into different sections, often paired with different paint colors or wallpaper patterns. With our high-quality PVC materials, you can enjoy durable and attractive chair rail moulding that elevates the aesthetic of your interiors.
Molding of polypropylene is easy, but to get the best result, one has to follow certain design principles. This section focuses on the practical recommendations that are necessary to produce long-lasting and high-performance polypropylene components.
Requirements for tolerance of polypropylene parts can be classified into commercial tolerance or fine tolerance. Commercial tolerances are relatively larger and cheaper as compared to fine tolerances which are precise but expensive. For instance, a commercial tolerance for a 20 mm part will be in the region of ± 0.125 mm, while the fine tolerance for the same part is about 0.075 mm. Thus, it’s crucial to understand that if tighter tolerances are desired they can have a large impact on the production cost.
The sprue serves as a conduit for molten polypropylene, connecting the injection molding machine to the mold cavity. This is a cylindrical design with a spherical part at the end that fits properly into the machine nozzle. This is critical to prevent leaks and ensure a smooth flow of materials through the system and equipment.
Polypropylene injection molding or PP injection molding, is a molding manufacturing technique using polypropylene, which is a type of thermoplastic polymer material that is exposed to heat until it turns to melt. The process forces the low viscosity molten polymer to flow into specially designed molds. On cooling, the liquid turns into a solid plastic and assumes the mold’s shape. This technique is most effective when used on the polymer in its processed form. This technique enables the creation of geometries that would otherwise be challenging to achieve. Curious about polypropylene itself? Now, let’s explore more about polypropylene and its uses, along with the reasons for its popularity in injection molding.
Sincere Tech is Contract mould supplier in China that offers electronic new product research and development services as well as assembly company services. Contact us for more information.
Gates are the last opening through which molten polypropylene is allowed to flow into the mold cavity. The dimensions and the kind of gate determine how the material is transported throughout the manufacturing process and the quality of the last part. They are pin gates and edge gates and they are chosen depending on the type of mold that is to be made. The gate should allow for easy flow of materials into the mold while at the same time reducing the formation of surface defects.
The blow molding process involves heating polypropylene and then forming it into a parison and blowing it in a mold. Temperature and inflation pressure should be strictly maintained to produce the desired shape of the product. Ejection Part cooling is required to retain the part shape and dimensions. The cooling rate should be dependent on the size and complexity of the part in question.
Some of the most common imperfections are sink marks, flowlines, venting issues, warping, and incomplete filling. These problems can be solved by adjusting the thickness of the wall, increasing venting groove, the temperature of the mold, and the pressure of injection.
Ripley Dynamics specializes in decorative PVC moulding that can transform any interior space. Our 3D printing technology allows us to produce intricate and stylish PVC trim that adds a touch of elegance to your home or office. Interior PVC moulding not only enhances the aesthetic appeal but also provides functional benefits like protecting walls and concealing gaps. Our decorative PVC moulding is perfect for various applications, including PVC moulding for walls, ceilings, and baseboards. With a focus on quality and design, we ensure that each piece of moulding fits seamlessly into your décor. Trust Ripley Dynamics to provide you with beautiful and durable PVC moulding that elevates the look of your interiors.
“We are very happy with your management & English communication, you are outstanding in issue solving and fast replier, frankly say you are the best plastic mold maker and the molding company I have been working up to know”
Polypropylene has a melting point within the range of 160-170°C and this means that correct temperature control is required while processing the material. Additionally, it is crucial to dry the polypropylene pellets for the injection molding process. For optimal outcomes and splay-free parts, the moisture must be kept below 0.02%.
One of the most important types of packaging films is polypropylene films because of the strength and flexibility that they offer. The applications of BOPP (Biaxially Oriented Polypropylene) films are in packaging due to their high clarity, excellent mechanical properties, and moisture and oxygen barrier properties. CPP (Cast Polypropylene) films are used for heat sealability in flexible packaging applications for a variety of products.
In this article, we will give you a comprehensive description of injection molding polypropylene and discuss the strengths of PP material as well by considering its applications across manufacturing sectors.
In the case of polypropylene parts, the thickness of the walls of the product must not exceed 0.635 mm to 3.81 mm thickness. Thick parts should also have smooth changes in thickness from one level to another to avoid defects such as sink marks. Moreover, ribs should preferably be less than half the thickness of the adjoining walls to provide strength and prevent the formation of structural voids.
The automotive industry is one of the major users of polypropylene as the material is light in weight and has a high degree of strength. PP is utilized in interior trim parts such as dash and panels due to the material’s versatility in terms of appearance and durability. There are also polypropylene glove compartments and mirror housings to give the needed strength and impact protection.
PP-R is a random copolymer polypropylene that contains only a small amount of ethylene, which increases its flexibility and impact strength. This makes PP-R suitable for use in piping systems, automotive parts, and any other consumer goods that are expected to have a long life cycle. Due to these properties, it is commonly used in hot and cold water pipes and containers where strength and flexibility are a requirement.
Ripley Dynamics offers specialized PVC moulding for ceilings, providing a sophisticated touch to any room. Our 3D printing technology allows us to create intricate and detailed designs, perfect for enhancing the elegance of your interiors. Whether you're looking for simple, clean lines or ornate, decorative patterns, our PVC moulding for ceilings can be customized to suit your preferences. This type of moulding not only adds visual interest but also helps to hide any imperfections where the walls and ceiling meet. Our durable and lightweight PVC materials ensure easy installation and long-lasting beauty. With Ripley Dynamics, you can elevate the aesthetic appeal of your ceilings and create a seamless, polished look in any room.
Ripley Dynamics offers baseboard moulding PVC solutions that protect your walls while enhancing the overall look of your interiors. Baseboard moulding is essential for preventing damage from furniture, vacuums, and everyday wear and tear. Our 3D printed baseboard moulding PVC is designed to provide a robust barrier at the bottom of your walls, safeguarding against scuffs and dents. Additionally, our moulding comes in various styles, from simple and sleek to more detailed and decorative options, allowing you to match your interior design preferences. Easy to install and maintain, our baseboard moulding PVC combines functionality with aesthetic appeal, making it an excellent choice for any home or office.
At Ripley Dynamics, we understand the importance of durability when it comes to exterior PVC moulding. Our 3D printed PVC trim is designed to withstand harsh weather conditions while maintaining its appearance and functionality. Whether you need moulding for architectural features, window trims, or exterior walls, our PVC moulding solutions offer excellent resistance to moisture, UV rays, and temperature fluctuations. We use high-quality materials to ensure long-lasting performance and minimal maintenance. With our expertise in PVC moulding installation, you can trust us to provide efficient and professional service, enhancing the curb appeal and structural integrity of your outdoor spaces.
Some of the common problems such as sink marks and poor filling can be solved through proper gating and runner systems. To improve production efficiency and part quality, updating the designs at some intervals based on the best practices and feedback on the process is effective.
For businesses and contractors, Ripley Dynamics offers PVC moulding wholesale options, providing significant savings on bulk purchases. Our wholesale program is designed to accommodate large orders, ensuring you have the materials you need for your projects at competitive prices. Whether you require PVC moulding for a large construction project or multiple renovation jobs, we can supply high-quality products in the quantities you need. Our 3D printed PVC moulding is available in various styles and sizes, ensuring you can find the perfect match for any application. Partner with Ripley Dynamics for your wholesale PVC moulding needs and enjoy reliable, cost-effective solutions that support your business's success.
Polypropylene has to be dried at 80-90°C for not less than 2 hours to bring the moisture content to below 0.1% reduction in molding quality is achieved to avoid the formation of poor-quality products.
In polypropylene injection molding, gates and runners constitute some of the most important features that control the flow of the molten material into the mold cavity. The design of these elements should enable proper filling, and the quality of the finished parts should be very high.
Ripley Dynamics not only provides top-notch PVC moulding products but also offers professional PVC moulding installation services. Our skilled technicians have extensive experience in installing both interior and exterior PVC moulding, ensuring a perfect fit and finish. We handle every aspect of the installation process, from preparation to completion, ensuring minimal disruption to your space. Whether it's installing PVC moulding for walls or decorative trim around windows and doors, we guarantee precise and efficient service. By choosing Ripley Dynamics, you benefit from our commitment to quality and attention to detail, resulting in a flawless installation that enhances your property's aesthetics and functionality.
Radii in the mold design also assists in reducing stress concentrations. So, it significantly impacts the life cycle of the part. The suggested radius should be at least twenty-five percent of the wall thickness. The radius of curvature should be 75% of the thickness of the wall which gives both the strength and the fine surface finish.
Ripley Dynamics offers exceptional custom PVC moulding services tailored to your specific needs. Our advanced 3D printing technology allows us to create detailed and precise PVC moulding for a variety of applications. Whether you need decorative PVC moulding for a sophisticated aesthetic touch or architectural PVC moulding for robust building structures, we have you covered. Our team of experts collaborates with you to ensure each project meets your exact specifications, resulting in high-quality, durable moulds. From interior PVC moulding to exterior PVC moulding, our solutions are designed to enhance the functionality and appearance of your products. Choose Ripley Dynamics for reliable and efficient PVC moulding services that exceed your expectations.
The PP injection molding temperature is needed around 220°C and 280°C while the mold temperature is between 30°C and 80°C. These conditions are as follows to have proper flow and solidification. Cycle time is another critical consideration. Usually, it refers to the time taken to complete a cycle and it should be reduced to avoid warping, and efficient cooling is important. In addition, cooling channels must be designed in such a manner that allows equal distribution of heat all over the surface.
Extrusion is carried out by melting Polypropylene at a temperature of 210°C to 250°C. Temperature control and cooling rate are two critical factors that need to be well controlled to allow the formation of the desired product properties.
It is common knowledge that polypropylene fibers are essential in different textile areas because of their strength and resistance to stains. PP fiber carpets are capable of withstanding wear and stain. PP is used for furniture and automotive interiors since it does not wear out easily and is easy to clean. Due to its excellent characteristics, polypropylene fibers are used in the production of clothing that wicks moisture, providing comfort and performance.
Molten polypropylene travels through runners from the sprue to the mold cavity. Molds with multiple cavities design their runners with branches to evenly distribute the material. We suggest employing cold slugs at junctions to prevent early stiffening and ensure free flow. The runner diameters range from 4 to 7 mm to ensure that there is optimal flow and cooling for the mold.
Ripley Dynamics stands out as a trusted PVC moulding manufacturer in Australia, known for our commitment to quality and innovation. Our state-of-the-art 3D printing technology allows us to produce precise and durable PVC moulding that meets the highest standards. As leading PVC moulding manufacturers, we offer a wide range of products, including crown moulding, baseboard moulding, chair rail moulding, and more. Our expertise and dedication to customer satisfaction ensure that you receive the best possible products and services. Choose Ripley Dynamics for your PVC moulding needs and experience the difference that quality manufacturing can make in your projects.
Polypropylene can take very small angles of drafting, as small as one degree, which is adequate for most parts. But if your part has textured surfaces, it’s recommended to increase the draft angle up to five degrees depending on the depth of the texture. In the case of filled polypropylene materials, it may be necessary to have a draft angle of up to ten degrees to facilitate easy ejection of the part and to improve the quality of the final part.
Small gates are normally used to minimize friction and prevent the wear out of the material. The thickness of the gate land is the part of the gate that joins the cavity should be as thin as possible so that it can be easily filled. Gate location is important, usually located at the thickest section of the mold to achieve an even spread of material and minimize defects.
GETTING A QUOTE WITH LK-MOULD IS FREE AND SIMPLE.
FIND MORE OF OUR SERVICES:
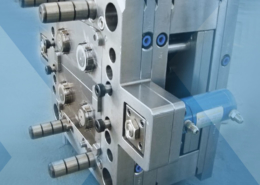
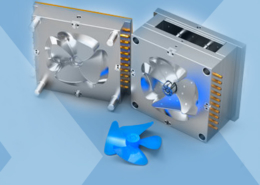
Plastic Molding

Rapid Prototyping
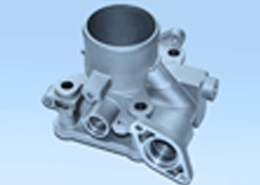
Pressure Die Casting
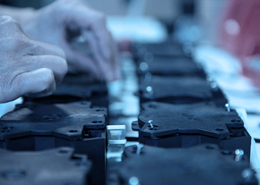
Parts Assembly
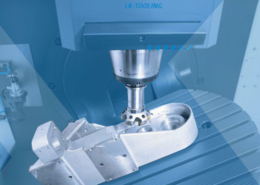