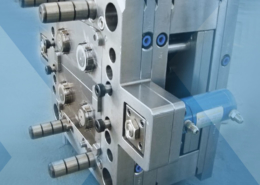
Texas Injection Molding: Houston Injection Molding Company ... - plastic mold ma
Author:gly Date: 2024-10-15
Discover how to enhance your mold design process with CAD/CAM software specifically tailored for the moldmaking industry. In part two of this webinar series, Cimatron will demonstrate how to intelligently design mold components, such as slides and lifters, using powerful CAD/CAM tools to accelerate the design process. Additionally, it will cover how to avoid errors and ensure design accuracy for ejector pins by checking clearance distances, calculating cutoff heights correctly, and thoroughly documenting all ejector components. Agenda: Slides Lifters Inserts Ejection pins and charts
Steps to improve data-driven decision-making and key features of a cloud-based system for mold monitoring and asset management.
Understanding plastic injection molding is crucial for professionals in manufacturing, design, and engineering. It’s a process that has implications for product development, cost management, and production efficiency.
The cost versus opportunity graph (see Figure 1) shows the value of ensuring the part drawing is critiqued early in the project.
Another area of focus is the adoption of energy-efficient practices. The injection molding process traditionally consumes a significant amount of energy, primarily for heating the plastic and operating the machinery. Advances in technology have led to the development of more energy-efficient machines and processes that reduce energy consumption and lower the carbon footprint of production.
Prototyping is a critical step in refining designs for injection molding. It allows for the testing and validation of design concepts before investing in expensive mold tooling. 3D printing, in particular, has revolutionized prototyping.
Making improvements, revisions and selections at the outset of a project offers the most significant potential to affect the final outcome, including the part cost.
In today’s fast-paced environment the mold designer must sometimes work in parallel with the customer by completing some of the mold design concepts while the part is still being finalized.
Material science is expected to advance, with the development of new polymers that offer improved properties or are more environmentally friendly. There might also be a shift towards more localized production models, facilitated by advancements in automation and 3D printing, reducing the need for extensive global supply chains.
Once the part design has been critiqued and revised accordingly, the customer must approve it. This step is critical and must never be skipped. Ideally, part approval should take place before a detailed mold design begins so that the mold designer can note any changes in the design and account for the corresponding change costs. However, in today’s fast-paced environment, the mold designer must sometimes work parallel with the customer by completing some of the mold design concept while the part is still being finalized. This approved part drawing, along with the details of the mold design (typically called the mold design order or order confirmation), can now be used to complete the mold design.
Engineers use properly preloaded bolts, blocks, springs and side-action cores to enhance functionality and reliability in various mechanical systems.
Looking to the future, sustainability will likely continue to be a significant trend in the industry. This might include increased use of recycled and bio-based materials, as well as continued efforts to reduce the energy consumption and carbon footprint of the molding process.
Plastic injection molding is a widely used manufacturing process, essential for producing a variety of products in numerous industries.
Intensive workshop teaches the process of mold maintenance to help put an end to the firefighting culture of many toolrooms.
Diamond compounds, with their varied grades, colors and base options, provide a comprehensive solution for mold builders in need of precise and superior polishing across diverse materials and applications.
Formnext Chicago is an industrial additive manufacturing expo taking place April 8-10, 2025 at McCormick Place in Chicago, Illinois. Formnext Chicago is the second in a series of Formnext events in the U.S. being produced by Mesago Messe Frankfurt, AMT – The Association For Manufacturing Technology, and Gardner Business Media (our publisher).
Answering the questions below will ensure that a proper review of the part takes place and that all critical aspects of the part design have been considered and approved by the customer, and are acceptable to the moldmaker.
In summary, plastic injection molding is a pivotal process in modern manufacturing, distinguished by its efficiency, versatility, and high-volume production capability. It involves injecting molten plastic into a mold to create diverse parts used in various industries. The process demands thoughtful design and prototyping to ensure the quality and functionality of the final product.
Understanding and facing the moldmaking industry’s obstacles to growth requires a strategy focused on increased profitability.
This webinar will provide an overview of new developments in hot runners, controllers, mold components, predesigned molds, process monitoring and mold maintenance equipment. These advancements are designed with the goals of lowering scrap rates, optimizing process temperatures and managing energy consumption. The solutions also aim to support productivity and may contribute to extending the operational lifespan of tooling equipment. Agenda: Innovative undercut and thread-forming components Predesign mold bases and plate control Melt delivery and control solutions Process monitoring and maintenance
Once the mold design concept has been agreed upon, and as engineering of the mold progresses, the opportunity to make conceptual changes or improvements diminishes and any costs associated with it will increase.
A connected software solution streamlines the moldmaking process by providing a unified source of design data, enhancing efficiency and reducing errors, with five key steps benefiting from this integration.
MoldMaking Technology addresses the complete lifecycle of the manufacture and maintenance of a mold—from design to first shot—by providing solutions and strategies to moldmaking professionals charged with designing, building and repairing molds. About Us
The following checklist can be used as a part drawing critique during the part design review meetings. Embedding a part design critique meeting into your mold design process can save thousands of dollars and weeks of mold build time.
A fully described plastic part is the most crucial information for a mold build project. An incomplete part drawing can create countless problems in the mold design process, waste a lot of precious time and cause numerous issues when the mold is completed and commissioned at the customer’s facility.
Another significant advancement is the development of smart molds equipped with sensors. These sensors provide real-time data on parameters like temperature and pressure, enabling better control and optimization of the molding process.
The need for data to track information and the history of the mold-building process is ever-increasing, and mold component solutions can help.
This method involves injecting molten plastic into a mold to create parts with precision and efficiency. The technique is notable for its ability to mass-produce items with consistency and high quality.
Once injected, the plastic cools and hardens, forming the desired part. The mold is then opened, and the part is ejected, ready for any further processing or finishing.
4. Is all geometry defined (radii, angles and so on)? Are complicated details called out in blowups and section views such that the part design is fully understood?
Steps to improve data-driven decision-making and key features of a cloud-based system for mold monitoring and asset management.
MoldMaking Technology Editorial Director Christina Fuges checks in with Bruce Cateon, an executive advisor at OASIC Consulting. Bruce started out in moldmaking, eventually becoming an industry consultant and taking time to work on his passion project the “Injection Mold Design Handbook” as a way of giving back to the industry that has given him so much. This episode is brought to you by ISCAR with New Ideas for Machining Intelligently.
Released earlier, this video remains a valuable recruitment tool and is being re-promoted in celebration of Manufacturing Day 2024.
Explore the standout articles of September, featuring innovations, expert insights, and strategies to boost efficiency and quality for your moldmaking needs.
It begins with melting plastic pellets or granules until they are liquefied. This molten plastic is then injected at high pressure into a metal mold.
6. Are there any sharp corners on the drawing? If possible, a minimum radius of 0.25 millimeter (0.010 inch) should be used on plastic parts. A radius of 0.8 millimeter (0.030 inch) is the minimum recommended radii as the stress concentration is mostly eliminated above this.
Smart sensors and sophisticated process and measurement data management are driving intelligent moldmaking to new heights.
While offering numerous benefits, it’s also important to consider the initial costs, design restrictions, and material limitations that come with this manufacturing method. The environmental impact of plastic production and disposal remains a significant concern, leading to efforts towards sustainability through recycling, the use of biodegradable materials, and energy-efficient practices.
In ISO 9001 quality management systems, the Management Representative (MR) plays a crucial role. While the 2015 version of ISO 9001 no longer mandates this position, having a trusted management member serve as an MR remains vital for streamlining operations and maintaining quality standards.
Utilizing helpful products and services for mold maintenance, repair and surface treatment (MRST) can save moldmakers time and money. Access more information about MRST in this exclusive, online-only content, including a suppliers list, products, services and more.
At the beginning of a mold build project, the customer may have only part samples, a CAD model or a 3D-printed model of the part they want to mold. While this may be advantageous to better visualize the product, it is absolutely necessary to have a complete detailed drawing of the product to minimize risk for all parties involved in the final decision. This drawing should show all features, tolerances and specifications. An example of a complete part drawing is shown in Figure 2.
Model-based definition replaces technical drawings to communicate precise product definitions between designers and manufacturers.
Identify pain points, tackle each one strategically and maintain flexibility to keep your moldmaking business on a path to growth.
While creating the plastic part drawing, the designer has the best opportunity to decide on the most suitable design for the mold and/or to make suggestions on how the product design might be modified to improve productivity and simplify the mold design; in turn, simplifying the mold design reduces mold costs.
With 3D printing, designers can quickly create prototypes that closely mimic the properties of injection-molded parts. This enables the identification and rectification of design flaws early in the development process. Prototyping also provides a tangible model for functional testing, ergonomics evaluation, and stakeholder feedback, ultimately leading to a more optimized and successful final product design.
12. Are locations where sinks may occur (like at the end of a rib) called out? Are thick-to-thin transitions designed correctly to reduce sinks?
A thorough plastic part design review ensures that you and your customer agree on the plastic part for the mold build project. Photo Credit: Haidlmair GmbH
Plastic injection molding is a manufacturing process used to produce parts by injecting molten plastic material into a mold.
As these innovations and trends continue to unfold, they will shape the future landscape of plastic injection molding, driving efficiency, sustainability, and innovation in this crucial sector of manufacturing.
Design plays a pivotal role in the success of plastic injection molding. A well-thought-out design not only ensures the functionality and aesthetics of the final product but also influences the efficiency of the manufacturing process.
MoldMaking Technology editorial director Christina Fuges checks in with Bruce Catoen, owner of OASIC Consulting on his passion project the “Injection Mold Design Handbook” as a way of giving back to the industry that has given him so much.
Figure 1. Cost and opportunity for change over the time of a mold build project. Photo Credit: Injection Mold Design Handbook.
Steel supplier discusses high thermal conductivity metal powders that also address the skills gaps via user-friendly materials and promote sustainability via durability and higher cycle counts.
A focus on electrode design and automation helps toolroom improve efficiency, reduce tooling costs and deliver higher quality products.
The field of plastic injection molding is constantly evolving, driven by technological advancements. Automation is playing an increasingly prominent role, with robotic arms and automated systems being integrated to increase efficiency and precision.
The moldmaking specialist, with help from its technology partner, Schoeller Allibert, will produce 20 injection molds for a reusable plastic packaging company.
Material Limitations: Although there is a wide range of materials available, each material has its constraints, such as melting temperature, strength, and flexibility. Some specialized materials may also increase the cost or complexity of the manufacturing process.
Understanding the nuances of plastic injection molding is crucial in the realm of modern manufacturing. It not only offers insights into how various products are made but also reveals the challenges and opportunities within this ever-evolving field. As industries continue to adapt and innovate, plastic injection molding will undoubtedly remain a central process, shaping the way we create and think about manufactured goods.
High Volume Production Capability: This process is ideal for high-volume production. With the capability to produce thousands or even millions of parts with the same mold, it is a cost-effective solution for large-scale manufacturing.
Join this webinar where Hexagon will explore how state-of-the-art CAD/CAM technology can drive your business forward. Learn how to optimize tool paths, enhance design accuracy and reduce lead times with advanced simulation. Discover the power of automation and real-time data for continuous improvement. Tailored for mold and die manufacturers, this session offers actionable insights to boost productivity and quality. Don’t miss this opportunity to gain a competitive edge in progressive die manufacturing. Agenda: Key challenges in progressive die manufacturing Optimizing tool paths Enhancing mold and die design accuracy Reducing lead times with simulation Automating processes for greater efficiency Leveraging real-time data for continuous improvement
Technological advancements such as automation, smart molds, and the integration of Industry 4.0 technologies are propelling the industry forward. Future trends suggest a continued focus on sustainability, material innovation, and the adoption of advanced data analytics.
Please place file(s) for transfer in the same folder and ZIP or RAR before attaching. Larger attachments can take a few minutes to transfer depending on your local internet speed :) For attachments over 20MB, click WeTransfer and send to info@HLHPrototypes.com.
When used for conformal cooling in plastic injection, 3D printing opens a wide range of design freedom. This design freedom enables designers to develop highly-efficient thermal regulation networks. However, this blessing also comes at the expense of not only higher manufacturing cost but also higher design cost as the designer could spend weeks to develop optimal cooling channels. This webinar will explore strategies and tools — including SimForm, a front-end thermal simulation app — to help tool designers and tooling managers maximize the benefits of 3D printing while minimizing manufacturing and design costs. Agenda: 3D printing applied to the plastic injection industry 3D printing pros and cons Tools and methods to facilitate the integration of 3D printing
Gerardo (Jerry) Miranda III, former global tooling manager for Oakley sunglasses, reshares his complete mold design checklist, an essential part of the product time and cost-to-market process.
After attending IMTS, it's clear that the integration of advanced technologies is ready to enhance precision, efficiency and automation in mold manufacturing processes. It’s a massive event, so here’s a glimpse of what the MMT team experienced firsthand.
Steel supplier discusses high thermal conductivity metal powders that also address the skills gaps via user-friendly materials and promote sustainability via durability and higher cycle counts.
21. For critical dimensions, will the dimension be left “steel-safe” for the first run so that the sizing can be adjusted?
Join MoldMaking Technology Editorial Director Christina Fuges as she gets the latest news on this mold builder's use of VR for mold design education.
After attending IMTS, it's clear that the integration of advanced technologies is ready to enhance precision, efficiency and automation in mold manufacturing processes. It’s a massive event, so here’s a glimpse of what the MMT team experienced firsthand.
10. Are all potential pinch points to the flow of the molten plastic eliminated? For example, are all thick sections that may cause “race tracking” of molten plastic eliminated?
MoldMaking Technology Editorial Director Christina Fuges sits down with Murphy Forsyth, GM – Injection Molding and Director Of Marketing for Zero Tolerance LLC in Clinton Township, MI.
Spending extra time at the beginning of the mold design project to create a fully described part, which considers all aspects of the mold design, can save tens of thousands of dollars for the moldmaker, and hundreds of thousands of dollars for the molder and OEM.
After attending IMTS, it's clear that the integration of advanced technologies is ready to enhance precision, efficiency and automation in mold manufacturing processes. It’s a massive event, so here’s a glimpse of what the MMT team experienced firsthand.
Discover how CAD/CAM functionality tailored for the mold industry can significantly enhance the mold design process. In part three of the webinar series, Cimatron will focus on designing waterlines and cooling components. It will demonstrate how CAD/CAM tools can verify drill line depths for water lines and baffles, ensure that minimum steel requirements are met while placing water lines, and provide a complete list of all baffle cutoff lengths. Additionally, it will explore how to confidently design runners and gates using CAD functionality specifically developed for these aspects of mold design. Agenda: Waterlines and verification Conformal cooling Baffles and charts Runners and gates
11. Are horizontal sections (bottom/stack shoulder) 0.05 millimeters thicker to account for stack compression and ease of filling?
Versatility in Materials and Shapes: Plastic injection molding is compatible with a wide range of materials, including various thermoplastics and thermosetting polymers. This versatility allows manufacturers to choose materials based on the specific requirements of the product. Additionally, the process can produce complex shapes and designs, which might be challenging or impossible with other manufacturing methods.
1. Is the drawing a plastic part drawing or “steel part drawing?” Is this clearly marked on the part drawing? A steel part drawing is the plastic part with shrinkage dimensions applied, so that the mold designer does not need to add shrinkage. This is often used when the shrinkages are not uniform around the part
19. Is all required engraving shown on the part? For example, does the engraving need to be mirrored on the molding surface?
Design Restrictions: While injection molding allows for complexity in design, there are still limitations. For example, designs must accommodate the ejection of the part from the mold, and some intricate shapes might require complex and costly molds.
How-to, step-by-step instructions that take you from making the master pattern to making the mold and casting the plastic parts.
Efficiency and Speed: One of the most significant advantages of plastic injection molding is its ability to produce parts quickly. Once the mold is designed and created, the manufacturing process can produce a high volume of parts in a relatively short time. This efficiency is especially beneficial for large-scale production runs.
In response to environmental challenges, there are growing efforts to make plastic injection molding more sustainable. One of the key strategies is the recycling of plastic materials.
7. Are the parting lines and all split lines defined? Are all intentional mismatches between core and cavity shown and defined?
In this post, we will discuss five important aspects of plastic injection molding, providing insights into its workings, benefits, and challenges. This knowledge is vital for anyone involved in or interested in industrial manufacturing processes.
All successful mold build projects start with examining the part to be molded to ensure it is moldable and will meet the customers' production objectives.
What exactly does a hot runner do? If you’ve been in the injection molding industry for any length of time, you might think the answer is obvious, but it is not.
A wide range of thermoplastic and thermosetting polymers are used in plastic injection molding. Thermoplastics, like polyethylene (PE), polypropylene (PP), and polystyrene (PS), are popular due to their versatility and recyclability. They can be melted and molded repeatedly without altering their fundamental properties. Thermosetting plastics, such as epoxy and phenolic resins, harden permanently after being heated, making them suitable for high-heat applications. The choice of material depends on the intended use of the final product, cost considerations, and specific property requirements like strength, flexibility, or heat resistance.
8. Has a CAE flow analysis been conducted? Will the part fill and avoid any problematic weld lines and potential voids? Review the L/t ratio (length of flow/thickness) and confirm it is acceptable.
Furthermore, the integration of advanced data analytics and machine learning could lead to more predictive and adaptive manufacturing processes. These technologies can analyze vast amounts of data to predict issues, optimize production, and even adapt to changing conditions in real-time.
13. Is the gate position defined and an acceptable gate vestige called out? Usually, the acceptable vestige for a valve gate is flush with the molding surface or slightly into the molding surface to prevent interference. Normally acceptable vestiges are around 50–75% of the gate diameter if the gate is a hot tip. Is a dimple needed to hide the gate vestige?
Making improvements, revisions and selections at the outset of a project offers the most significant potential to affect the final outcome, including the part cost.
By reusing post-consumer or post-industrial plastics, manufacturers can reduce waste and lower the demand for virgin materials. Additionally, there is an increasing use of biodegradable materials. These materials, derived from renewable sources, can break down naturally over time, mitigating the impact of plastic waste.
Discover how to enhance your mold design process with the right CAD/CAM tool for parting and cavity design. This webinar will explore CAD/CAM capabilities including how hybrid solid/surface modeling can streamline workflow and improve accuracy. Learn how to confidently tackle parting, runoff, and shutoff, ensuring precision and efficiency in your designs. Agenda: Part analysis QuickSplit techniques Parting and runoff strategies Shutoff solutions
Join MoldMaking Technology Editorial Director Christina Fuges as she gets the latest news on this mold builder's use of VR for mold design education.
By the time the project reaches completion, the opportunity to make changes is low, and any costs could add up to 150 times the cost of a change in the design phase!
15. Do the parts need to stack and de-nest? If so, is the stacking height shown, and is there a diagram showing the stacking of the parts?
If you would like to learn more practical tips and guidelines for good mold design, visit hanserpublications.com or Amazon.
A water-based, eco-friendly plastic mold cleaning system helps Rankine-Hinman Manufacturing restore flow rates and avoid big-ticket failures on complex and costly molds.
The production and disposal of plastic products have significant environmental implications. Plastic waste, particularly from single-use products, contributes to pollution and poses a threat to marine life and ecosystems. The production process itself can be resource-intensive, often involving the consumption of fossil fuels and the emission of greenhouse gases. These environmental concerns have brought a renewed focus on sustainability within the plastic injection molding industry.
It’s easy to imagine the advantages automation offers the moldmaking process, but it's challenging to change one’s mindset, develop a plan and invest.
After attending IMTS, it's clear that the integration of advanced technologies is ready to enhance precision, efficiency and automation in mold manufacturing processes. It’s a massive event, so here’s a glimpse of what the MMT team experienced firsthand.
Proper design can minimize material usage, reduce cycle times, and prevent defects. It’s crucial to consider factors like wall thickness, rib design, and gate location during the design stage to optimize the molding process and the quality of the final product.
Initial Costs and Tooling: The initial cost of creating a mold for injection molding can be quite high. This includes the cost of design, material for the mold, and the machining process. Therefore, it’s more economical for large production runs where the initial investment can be spread over a larger number of parts.
Additive manufacturing, commonly known as 3D printing, is also influencing injection molding. It offers new possibilities in mold design, allowing for the creation of molds with complex geometries that were previously challenging or too costly to produce.
In ISO 9001 quality management systems, the Management Representative (MR) plays a crucial role. While the 2015 version of ISO 9001 no longer mandates this position, having a trusted management member serve as an MR remains vital for streamlining operations and maintaining quality standards.
In addition, the rise of Industry 4.0 technologies, such as the Internet of Things (IoT) and Artificial Intelligence (AI), is leading to more connected and intelligent manufacturing environments. These technologies enable predictive maintenance, process optimization, and enhanced quality control.
Spending the time to critique and carefully evaluate the part before creating a mold design is always a good use of time. If a problem is caught and corrected during the part design review, it can save up to 100 times the cost to resolve the problem at the end of the project. A thorough plastic part design review represents just a small fraction of the time required to design and manufacture the mold, and it ensures that you and your customer have an agreed plastic part for the mold build project.
GETTING A QUOTE WITH LK-MOULD IS FREE AND SIMPLE.
FIND MORE OF OUR SERVICES:
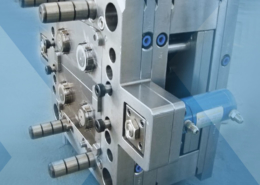
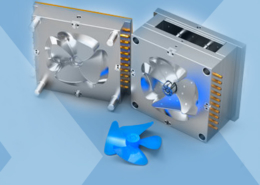
Plastic Molding

Rapid Prototyping
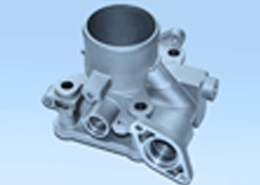
Pressure Die Casting
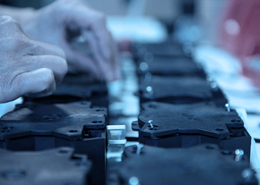
Parts Assembly
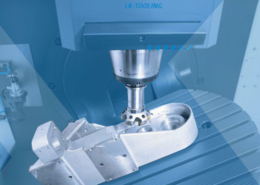