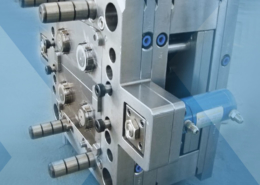
Sustainable materials for injection molding - products made with injection mould
Author:gly Date: 2024-10-15
HDPE injection material is used in the production of covers, cases, plastic pallets, kitchen items, toys and many other products and this is a high density polyethylene material. With the injection molding, the HDPE takes every shape. Since the values of temperatures and pressure value depending on the product, it can be widely used.
The ‘prototype mold’, or ‘rapid plastic injection tooling’ is based on the same principle as series plastic injection molds, but has a simplified and accelerated design. It is also not intended for long-term use. The use of a common mold base and aluminum for the molding parts makes it possible to reduce investment costs and machining time. Production of the prototyping mold takes between 2 and 4 weeks and is 40 to 60% less expensive than a traditional mold. The cost and design time of the mold depends on the shape complexity of the part to be molded. After a complete analysis of your plastic parts, our design office creates the tooling plan of your mold. We then start its production according to your specifications.
In rapid prototyping, the use of a prototype mold for plastic injection, therefore, makes it possible to obtain small series using the right material at a lower cost and in reduced time. It is a very good solution for testing your concept quickly and cheaply. There is no need to sacrifice the quality of the final part. You, therefore, obtain reliable information (mechanical, geometric, assembly and industrialization) on the final parts as well as the subsequent production of a series injection mold.
Injection molding means that the HDPE plastic is shaped by pressure in a heated mold. It is a very fast production method and the labor cost is low. It is popular with the production of smooth surface products in the production of complicated parts. Since we are working with a large number of injection equipment, our company is a competent company that fulfills the needs with the most affordable prices.
We have started our journey in 2012 to facilitate our customers’ lives and to offer many opportunities that would enrich your lives. Over time, we have developed ourselves and have succeeded in becoming a respectable, reliable and global company in the petrochemical sector, after increasing our resources and enhancing our product range.
In the HDPE production market, the products that are produced with injection molding technique constitute 30% of total production. HDPE injection products, which are used in many areas, lead the market since they provide many advantages. The melting of HDPE by the heat and shaping it in the injection machine is the most common method for producing plastic materials. The process consists of closing, injection, ironing, cooling, mold opening and removal from the mould. Every stage is performed automatically and the finished part is removed from the mold during the extraction process.
Thank you for your comment. Best format would be : STP / IGS / XT. I you could provide one of these please we could quote your project.
Thank you for your comment. We would only need the CAD design of the toothbrush, CAD design of mold would be done by us. On of our project manager will reach to you by email to have more information about you injection molding project.
This process consists of injecting a molten polymer (thermoplastic material) into the prototype tooling under high pressure. The plastic material is then cooled and solidifies, taking on the shape of your part. This prototyping technique allows the use of a very large range of ‘right material’ resins. The overmolding of metal inserts and the production of parts incorporating two materials is possible.
This technique allows the production of small series that are close to reality. The applications of plastic injection molding are very varied. They are particularly useful in the automotive, packaging, medical, and electronics sectors.
Cases, cowlings and hulls are examples of parts that we produce very regularly. In a field that requires many tests and certificates, such as the medical sector, the plastic injection can satisfy the regulatory requirements and constraints. (Find out more on our page about standards.)
Our rapid plastic injection molding solutions are specially adapted to the production of prototypes and small series of plastic parts (from 100 to 1000+ parts). Inspired by traditional molding techniques, we inject your plastic parts using an aluminum prototype mold (or rapid tooling). The results achieved with this technique are equivalent to series molds. The robustness, mechanical properties and industrialization information are identical.
Hello, I have 3D drawings for a project. I would like a quote for injection molding or your prototype mold system. Thank you
The design of our injection rapid tooling is based on a standard ‘mold base’ frame and interchangeable aluminum core and cavity inserts. This reduces the investment costs and production times inherent in plastic injection. This is our rapid production technique which is the most expensive. However, it makes it possible to obtain functional parts made from the ‘right material’. They can be marketed or used in transition production.
Thank you for you comment. We would need you specifications to advice and quote you : CAD files, volume required, material etc.
In general, HDPE injection has 700-2000 kgf / cm² pressure, 160-250ºC temperature and 10-30 seconds production time. There are different injection devices that produce many products including the smallest parts, and the largest plastic parts. The hot runner system is used in injection molding for reducing the need for the material, labor and machine capacity.
GETTING A QUOTE WITH LK-MOULD IS FREE AND SIMPLE.
FIND MORE OF OUR SERVICES:
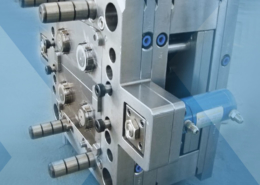
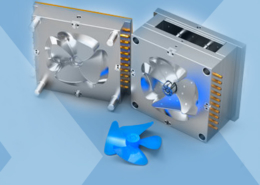
Plastic Molding

Rapid Prototyping
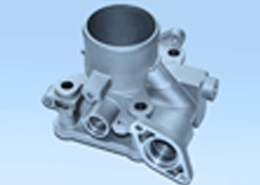
Pressure Die Casting
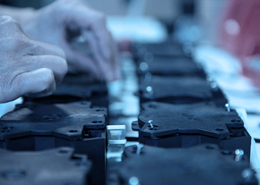
Parts Assembly
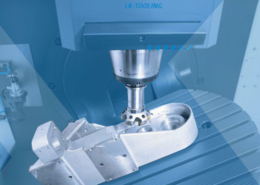