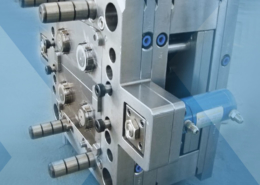
Sustainable materials for injection molding - molded plastic products
Author:gly Date: 2024-10-15
Recyclable plastic is also a good-quality plastic as it is good for the environment. Such a category of plastic does not leave hazardous footprints on the planet and can be used to serve many purposes. To ensure the safety of everything for the business it is essential to contract with the best dealer in this niche who is serving the same motive. The selection of the right materials is very important for integrating the customer’s trust in the product. And only an authentic supplier can help to figure this out altogether. Contact FOW Mould for all your injection molding queries and quotation.
These temperatures are maintained with precaution while executing the process of Injection Molding with heatproof plastic material. Plastics go under a lot of pressure to give the best output.
Polyetherimide Plastic is translucent plastic that is quite identical to PEEK in terms of properties such as high density and heat resistance. It is one of the most commonly used commercial thermoplastics.
The heat distribution channels should be placed at an equidistant level to ensure that the manufacturer does not spend more time cooling the parts to prepare for injecting or ejecting. The appropriate heat channels can catalyze the entire process of injection molding.
It uses the CNC molding technique which is a three-step process of inserting a specific shape of the objects, injecting molten material into molds, and leaving while it’s still hot so that the material could cool down and settle, which only gives a premium product.
The layers of plastic keep the wires protected. Although plastic is not a good conductor of electricity stimulation, it enables the flow of current inside the plugs, switches wires, and promotes good business.
It is a very rare case when a plastic material catches corrosion because these materials are very low maintenance unless not kept in appropriate conditions. Plastic materials such as high-density polyethylene are the first choice for industrial production.
This type of heat-resistant plastic has a good insulating capacity, and also high flexural strength. Furthermore, it can withstand extreme weather conditions as well. It is well known for having the highest melting point of other thermoplastics, which is 327 degrees Celsius.
The products obtained by 3D sampling include toys, chairs, automotive, and electronics but these are only very few products to name. FOW Mould has so many more things to offer such as heatproof plastic products that are water and corrosion-resistant.
Plastic is easily available in many forms. One of the popular forms of plastic polycarbonate is widely used by many manufacturing and assembly units to execute their operations. This versatile use of plastic has reached 311 million tons of global production for consumption directly or indirectly.
Nylon is a great example of lightweight material. It has a very low ignition probability and the weight of nylon is almost negligible under many circumstances which is why Nylon is used in packaging and binding material together.
The plastic helps hinder the leakage of currents from wires. Bakelite is the thermoplastic that is used by industries to make electric switches and electric wires that promotes the flow of current only under the wires.
Finding the right quality of plastic which serves the right purpose is not tough anymore. Different types of heat-resistant plastic have distinct properties, pros, and cons to look into. Therefore some of the most popular types of such plastic that are not only heat-resistant but also waterproof, and easily moldable have been mentioned below.
They are used for manufacturing water pipes and plumbing applications because they are in constant touch with water. If plastic is replaced by steel it will catch rust and corrosion within a couple of years and that is not good for the product’s longevity.
In the overmolding process, a finished molded component or a metal or other substrate is placed within the LSR mold during the LSR molding process. Once introduced, the mold closes and the LSR is molded around or over the presented substrate or component, integrating the two.
Moreover, they offer scalability to have a mass of supplies in hand. It is important to note here that these mass supplies are produced within budget to cater to the budget requirements of the distinct businesses as well.
When utilizing more than one material, the desirable characteristics from each of the materials can be realized – the rigidity of a thermoplastic or weight of a metal mass combined with the flexibility, sealing, or delicate features of an LSR.
Plastics are used in crafting aerospace because replacing metals with high-grade plastics helps reduce the weight of spacecraft materials. Polyetheretherketone is the plastic fiber that is used by Aerospace renowned organizations to ensure low temperature and atmospheric particles.
It is a polymer with consistency unlike any thermoplastic but similar to a metal fiber which ensures the cooking vessels are made of heat-proof plastic.
Using semiconductors instead of steel and metals for making chips and wires is a real win for semiconductor manufacturers. Furthermore, thermoplastic is good for the long run and can be recycled without any hectic rotation.
Polytetrafluoroethylene is a very common plastic that is used to make good quality wires that don’t catch the heat and do not get tarnished by the touch of water. It is utilized in a lot of the manufacturing industries for making wires, cables, insulated transformers, surface coatings, and many such things which are largely used in mega-scale industries.
It is no lie that plastic is used in every industry in different forms or as distinct resources. Whether it is the packaging industry, manufacturing industry, raw material sourcing industry, electronics, transportation, or any bureau department, plastic is used in all. They are mainly used to ensure the smooth flow of operational machinery.
Two-shot injection molding is also called “2k molding” or co-injection molding. To successfully perform liquid silicone rubber two-shot molding, a specially designed co-injection molding machine is needed, and a mold builder and molder that are skilled and experienced in LSR processing to ensure accurate alignment and precision placement.
SIMTEC is proud to be a leader in the development of multi-injection molding technology. We’ve created and implemented technological approach to the integration of functions and materials, resulting in a proprietary multi-shot molding process that is unmatched in our industry.
Regardless of the industry, our liquid injection molding cells allow for the production of liquid silicone rubber parts or components that must withstand extreme conditions and make your products more effective. Industries and applications include:
Using plastic as a material for injection molding requires certain precautions and care. Although most manufacturers prefer high-quality metallic heat-resistant materials such as nickel or stainless steel, the use of plastic as a heat-resistant material has also become quite popular.
Multi-shot or multi-component injection molding is a collective term that refers to an injection molding process where two or more materials are molded in the same molding machine and within the same molding process. The result, an integrated molded component consisting of multiple materials and substrates.
In 2k LSR injection molding, there are two types of molds used: transfer molds and rotary molds. Using a transfer molding process, after the thermoplastic parts are molded, the molded parts are robotically removed from the mold and transferred up to the LSR mold for completion.
Polyetherketone is semi-crystallized and also the oldest member of the thermoplastic family. It is hard and stiff in consistency. Therefore, it is not easy to melt it down. PEEK is a denser chemical instructed plastic that is integrated with closely related molecules making the bond tough. Thus the products created from this type of plastic get tougher.
Aerospace apparatus are needed to be made with utmost sincerity hence, thermoplastic is considered the best because it caters to the minute detailings required for spacecraft products.
To ensure a better fulfillment of the business needs it is important to deal with the best suppliers who can not only meet the business expectations on time but also offer the best quality product at cheap rates.
Heat-resistant plastic is categorized under polymeric materials that can withstand high temperatures and up to and sometimes more than 300 degrees Fahrenheit without compromising on the physical or mechanical attributes.
However, it is important to note that PEI is relatively stronger and tougher than PEEK, which is why it is used in making electrical conductors, shields, and elevated thermals. It has been greatly used in making engines and aircraft, and carriers.
Contact us today to learn more about the many ways in which multi-injection molding can add value to your company’s manufacturing processes and applications.
Polyethylene and polypropylene are the two most commonly used plastic in pharmaceuticals. These two plastics are easy to mold and have low-density molecules to attain desired mm of thickness.
Polyetherketone doesn’t get any effect up to 170°C which makes it an ideal thermoplastic for industrial use. It can be considered the best alternative to metals. This is because it not only keeps the product durable but also adapts to harsh environments.
The benefits of using heat-resistant plastic materials are many. They are quite strong, decisive, and great for high-temperature conditions. This type of plastic material has a high melting point which enables them to not get melted easily.
One-time usable thermoplastics are utilized in many sectors too. They are easily available at cheap rates and fulfill distinct business requirements. Furthermore, they take the least space for occupancy that’s why thermoplastic is the first choice and an irreplaceable choice too.
Therefore it is important to check the high temp plastic properties before opting for it for manufacturing purposes. With more and more heat-resistant plastic materials being introduced, there are several considerations to be made before selecting a specific material for business requirements.
FOW Mould uses the best quality heat-resistant plastic to make molds for engineering, manufacturing, and mold assembly superset. And their best trait is they do not include any third party in this, FOW Mould uses injection molding of their own to make molds as per the expectation.
These chemicals are stored in cans to sustain the quality and properties of soothing for consumption and also to secure chemicals from reaction with moisture. These cans are made from heat-resistant and corrosion-resistant plastic which is essential for the chemical industry.
Polypropylene is plastic that is used by the automobile industry. It is a thermoplastic that can be easily molded by an injection molding technique, and the quality is up to the standards achieved with the virtue of heat resistance, corrosion resistance, and waterproofing. Polypropylene not only gives resistance against heat, water, and corrosion but also helps in noise cancellation and safety from road accidents.
They play a major role in different industries, especially as a compatible alternative to heat-resistant metals. Some of the beneficial properties of heat-resistant plastic have been mentioned below.
For product designers, the use of multiple materials in a single component allows for greater design flexibility to achieve complex part designs, desirable product features, and enhanced product performance.
Medical industries are more concerned and cautious about the use of plastic because they are going to be utilized directly by the patients. Hence they need the best quality hygiene and well-maintained plastic for surgical gives and syringes, insulin, tubes, and plastic bags. Thus plastic is used extensively by the medical industry because the medical industry maintains guidelines and is only used for one time.
With its high dielectric strength and chemical and flame resistance, PEI plastic is considered the best grade of plastic to be used for industrial and manufacturing purposes. It can bear heat temperatures up to 338 degrees. PEEK has a low water absorption rate. Therefore, it is a compatible choice when it comes to corrosion resistance and heat resistance.
Polyamide, also known as Nylon, is very popular for many uses. It is made from the injection molding technique. Polyamide is a flexible, water and heat-resistant plastic material. Its popular application includes in the textile industry, wherein nylon threads are used to make clothes. It does not react to the body or have any harmful traits.
Semiconductors appliances use plastic in a way to promote telecommunications equipment. In addition to these semiconductors and plastics are used in making chips, and pen drives, which allows these products to not get affected by the heat.
Furthermore, it is used in maintaining stability if dimensions balance the weight for carrying extraordinary operations. Vespel is suitable plastic for products where high-impact resistance and low-friction are needed. This heat-resistant plastic cannot be directly used in the injection molding process, but companies fabricate vespel for injection molding.
H is a code to determine the level of preserves that are used for specific temperatures and ascertain the degree of temperatures for the melting of plastic materials. H2 temperature ranges from 26°-40°C, and H3 temperatures range from 27-45°C.
With design flexibility, advanced technology and exceptional quality, there’s no better partner to manufacture your high volume Liquid Silicone components than SIMTEC. Contact us today to discuss your requirements.
SIMTEC has perfected their multi-shot LSR injection molding technology and is one of few with the expertise and quality results needed for complicated, critical component requirements. We are proud to be able to provide our customers with solutions that meet the product performance they need for their long-term, high volume programs, and deliver quality precision multi-material components, consistently.
The overmolding injection molding process is sometimes confused with or referred to as two-shot molding. Although similar because the finished component of both consist of a combination of two different materials or substrates, the manufacturing process and bonding is different. In the 2k molding process, the two materials are both chemically and physically integrated providing a superior bond compared to overmolding.
The chemical industry uses highly flammable and combustion solutions which need constant observation. But in mega industries, people are being replaced with plastic and this plastic is used to ensure the safety of chemicals.
Good-grade quality plastics like PEEK are a great source of dielectric strength and yet one of the most commonly used heat-resistant plastics. There are so many other polymers and thermoplastics, including PEEK, which are good insulators of electricity and keep the heat within the wires.
In two shot molding, the LSR and thermoplastic parts are both molded and combined during the same molding cycle. The molds for the LSR and thermoplastic parts share the same platen in the molding machine. Typically the mold for the LSR parts is on the top and the thermoplastics mold is on the bottom.
Polybenzimidazole is used by astronauts to make space suits and space shuttle materials, gloves, and also in aircraft wall fabrics, these special grade plastic is mainly used by special organizations for commercial purposes.
There are several benefits that can be achieved by choosing a multi-shot process versus a single-material part followed by assembly, heat staking, ultrasonic welding or other secondary process used to mechanically combine two or more substrates.
FOW Mould is a mold-making company that performs different molding activities, including injection molding. When a business trusts FOW Mould for making their molds and products they are leaving their trust to the skilled hands and authentic dealers who will definitely produce the best.
It is used in making valves, bearings, and more fabrication appliances because of its unbeatable strength and ultra-high vacuum power, and it’s healthy for the environment too.
Some of the primary features of heat-proof plastic material include resistance against chemicals, insulating properties, light-weighted yet durability, and many more. Based on these advantageous properties, this kind of plastic is used across different industries.
Two-shot LSR injection molding involves molding an LSR material and a second polymer in the same molding process. The second material can be either a compatible thermoplastic material or a different grade of LSR (different durometer or pigment). The two materials are molded during the same process and combined to form one integrated two-material component. This process is a two-shot injection molding process.
They have a great experience in mold design and have been producing durable and high-quality mold designs. Their exclusive designs not only lead to a smooth manufacturing process but also stands out from others. Be it a customized mold design or the one formulated by them, a durable mold design is guaranteed.
Injection molding is an integral technique, and FOW Mould does it within the boundaries of its plant by trial and error over many decades. FOW Mould aces its operations in injection molding by achieving the height of the standard.
FOW Mould is one of the first companies in China to use the 3D printing technique for samples. They use 3D printing in plastic prototyping and provide samples to their customers. These samples are used to illustrate the design of products to the clients.
PBI is also used to put the minimum weight hence it is a good material to replace glasses, metals, and steel products. It is good to know that thermoplastics are suitable for replacing those metals and gives an assurance of not catching the fire and work well with heat and water.
It ensures the safe flow of activities in not only electricity but every industry. Plastics do not have electrons which helps the copper wires to maintain the steady flow of electricity inside the walls of thermoplastic.
Good quality heat-resistant plastic has proven to be quite beneficial in several instances. Not only are these kinds of plastic heat resistant but also corrosion-resistant, and insulators that prevent any further damage.
Polyethylene is the widespread plastic that is used by every industry to pack commodities, protecting them from moisture in a humid atmosphere. The varying sizes of Polyethylene are being used widely for fulfilling different elements of industries.
Polybenzimidazole is a heat-resistant plastic that is known for not catching fire easily. It is a synthetic fiber and shows a wonderful tolerance to extreme heat temperature, and these qualities are to be used only for specific purposes.
In several parts, heat channels cannot be used or placed appropriately within the molds due to certain extensions. In such a scenario, the thermal pin can be a great choice. These pins can instantly transfer the heat from anywhere to the mold’s heating channels.
FOW Mould make their molds at the factory they own and it is one of the greatest advantages for mold-making companies to have their injection molding plant. FOW Mould company integrated many unique and efficient techniques in their operation to ensure the timely delivery of final products.
It can easily maintain the interior temperature without affecting the coolant pressure in the mold. These pins are a great choice for complex molds. However, it is significant to consider that there are no air gaps between the thermal pins, which might disrupt its functionalities.
The pharmaceutical industry uses plastic to pack and secure them from getting defective or sapped in warehouses. The pharmaceutical industry uses plastic for primary, secondary, and tertiary levels of packaging and storing them in racks.
Owing to its excellence FOW Mould has become popular for the molding services they provide. At FOW Mould, they offer high-scale injection molding techniques so that businesses can count on FOW Mould without giving it a second thought. They will ensure to deliver of the best quality product through rapid prototyping to ensure the least possible production days.
The material of the mold used can play a major role in the production of the final product. Opt for a high-temperature, heat-resistant material to ensure better longevity. If the mold material is not too heat resistant, consider adding more cooling channels to maintain a balance in the molding process.
Polyamide is also used in making pipes, ropes, and gears for adventures like mountain climbing or river rafting. Nylon rope is preferred by mountaineers, and gears are also used by them to attain safety at high altitudes. However, nylon should be excluded from general purposes like carrying and storing food items.
FOW Mould company has been fulfilling their client’s business needs efficiently for a long time which makes them one the best suppliers for plastic and injection molding. FOW Mould handles its operation very professionally which is why it has big market capture in China. They provide services such as producing heat-resistant plastic molds and using good thermoplastic for mold making. They bridge the gap between the imaginary product and the final one.
Selecting the appropriate kind of plastic to fulfill the purpose and attain efficiency is important. However, it takes a little detail to understand which kind of plastic should be used and when. Good quality is the one which has material that is heat resistant plastic, not easily breakable, and does not harm well-being.
A similar amount of heating and cooling fluid should be used in the process. This enables lowering or raising the temperature levels of the mold instantly whenever required.
In the case of connectors, covers, valves, and others components that use a seal, when produced as a multi-material component the product’s performance is enhanced. A superior chemical bond is achieved, the seal fits perfectly, remains in-place and eliminates seal rollover or displacement that can occur with loose seals added during a secondary assembly process.
ACIS®, Autodesk Inventor®, CATIA® V5,Creo™ Parametric, IGES, Parasolid®, Pro/ENGINEER®,Siemens PLM Software’s NX™, SolidEdge®, SolidWorks®, STEP
Cheap lightweight plastic sheets are prepared with heat-resistant plastics hence they are used extensively by industries in packaging and other operations. These plastics are not only used for their fire and heat-resistant properties but also because they are very light in weight. This further facilitates easy carrying and transportation.
Our advanced molds and molding capabilities enable us to fulfill even the most complex design requirements — without sacrificing quality, durability or aesthetic appeal. What’s more, we support our multi-shot injection process with a full complement of value-added services for our customers, such as design support and prototyping on the front end, and value-added inline secondary processes at the end for a full portfolio of services.
Vespel is also more like Polybenzimidazole. It is a good conductor of electricity and performs extremely well under high temperatures. Vespel is used in aerospace, air forces, and merchant ships for executing many functions.
Therefore it is important to discover some consumer-durable and consumer-friendly plastics in this article and how they are made, and the best supplier for sourcing thermoplastic molding supplies.
GETTING A QUOTE WITH LK-MOULD IS FREE AND SIMPLE.
FIND MORE OF OUR SERVICES:
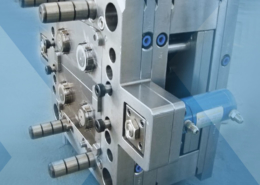
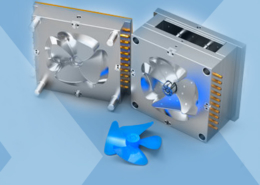
Plastic Molding

Rapid Prototyping
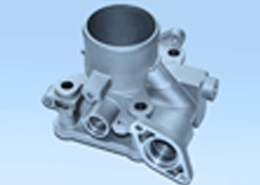
Pressure Die Casting
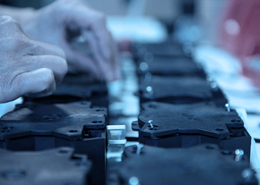
Parts Assembly
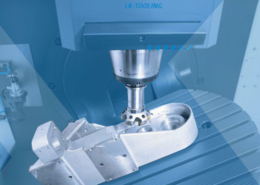