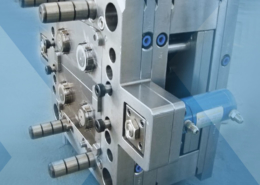
Supplier, company for plastic injection moulding & back ... - back injection mol
Author:gly Date: 2024-10-15
Using high-precision software to design molds with accurate core and cavity dimensions, we also consider requirements such as insert and double molding that are commonly used in the automotive motive industry. If our client intends to use such methods, we will tailor the mold design for them.
We take pride in being able to produce over 600 set molds in a year. This has garnered us a reputation for being able to fulfill any order, no matter how big it is. No matter how large the scale of the order, we are more than capable of fulfilling it.
Some other common materials used for injection molding include polycarbonate, nylon, acrylic, and polyoxymethylene. Each of these materials have their advantages and disadvantages, which is why, when determining which material to work with, you need to think of how the final product will be used. Will it need to be food-safe? Does it need to be heat tolerant? UV resistant? These are some of the things you need to consider before deciding which material to use.
Using 3D printing to analyze and modify automotive part samples is cost-efficient, fast, and allows for the production of multiple prototypes at the same time. Moreover, our 3D printers deliver high-quality prints that capture every design detail. This method is, however, only compatible with thermoplastic materials.
At FOW Mould, we use premium durable types of plastic to injection mold automotive parts. They include ABS, polypropylene, polyurethane, nylon, carbon fiber reinforced plastics, and polyethylene. Polypropylene car parts include cable insulations and polypropylene car bumpers while polyurethane is used to make suspension bushings and seat support. Our ABS plastic automotive parts are also popular in the industry.
When you give us confirmation for your specifications and molding designs, we will have our wide array of CNC machines to manufacture your mold design. With our computer controlled machining system, we can ensure only the best prototypes for your company.
Immould always adheres to a high standard of control. We follow the strictest quality control, and any plastic car parts that we distribute, are tested by our specialized team of experts. Rest assured, any product you get from Immould is of the best quality possible.
With updated software and all automated production processes, our machines are regularly maintained and recalibrated to enhance accuracy. These efforts help eliminate errors during design and injection molding processes because we understand how critical precision is when it comes to automotive assembly.
Choosing the right material for your project will help to streamline the process, improve your product’s performance, and reduce costs.
Plastic materials are ideal for some automotive parts like those found in vehicle interiors and car exteriors. They are smooth, user-friendly, and can be made to be sleek and stylish. In terms of functionality, the incorporation of plastic parts reduces the weight of automobiles because they are lighter than metal. It is also possible to bond them with other materials where firmer structures are required.
Once you know which material to use, you will be able to decide which material is best for your project. Specifically, you will need to choose between an amorphous plastic or a semi-crystalline plastic. The main difference between these two families of plastics is how they react to heat.
Amorphous materials shrink or expand less when heated or cooled because they don’t have a sharp melting point, making the process more forgiving and gradual. Unlike amorphous plastics, semi-crystalline plastics have a much sharper melting point and are known to expand or contract a great deal more when exposed to changing temperature extremes.
The application of the product will determine the material used. If a product needs to be transparent yet still durable, like an automobile headlight, polycarbonate would be a good choice. What if your product is a container, like a milk jug? Then polyethylene is the type of material you’ll want to use. Polyethylene is often used for food packaging because it is food safe and won’t leach chemicals.
By utilizing injection moulding for your plastic car parts, you are assured that you will be saving money. Just one injection mold could be used to create a myriad of parts. This means that you will save on both material and production costs.
Specialized in developing outstanding automotive injection molding solutions for a variety of industries, FOW Mould has over 40 years of experience in providing manufacturing solutions to companies. Each design, mold, or automotive part is designed for manufacturability as well as cost-efficient, and time-saving production.
Immould has been in the injection molding industry for years, and we are considered one of the best automotive plastic parts manufacturers in the world. Here are some of the key applications that we provide to the automotive industry.
Our design team designs automotive parts based on clients’ specifications and requirements. Upon completion, we evaluate and test every product design proposal. The analysis process is carried out by design and engineering experts in consultation with the client, which ensures that we deliver precise and high-performing parts
FOW Mould also has rich experience in automobile parts. For automobile molds, accuracy is the one thing that needs extra attention. All of our mold parts are processed by high precision machines, thus our injection molded parts are within a specific tolerance rate as our clients require.
ACIS®, Autodesk Inventor®, CATIA® V5,Creo™ Parametric, IGES, Parasolid®, Pro/ENGINEER®,Siemens PLM Software’s NX™, SolidEdge®, SolidWorks®, STEP
Using engineering-grade resins when injection molding automotive parts, we’re able to deliver high-performing structures like ABS plastic parts that are resistant to wear. We also achieve the surface finishes requested by clients. All procedures are performed and tested under the supervision of production experts.
Thermoplastics are plastics that melt when heated and make plastic injection molding possible. Most of the plastic products used today are created using thermoplastics because of how diverse this material is. Some thermoplastics are very sturdy and rigid, while others are flexible and rubber-like. Some are clear and others are opaque. It is this diversity that makes thermoplastics such an appealing material for manufacturers.
With our precise moulding methods, you could be assured that all your automotive plastic components are of the best quality possible. Immould makes it a priority that all the dimensions of your plastic car parts are as precise as possible.
We have extensive experience in designing and injection molding interior and exterior plastic car parts. Our staff is well-trained in specialized techniques like insert molding and overmoulding which are essential in manufacturing plastic car parts with a strong durable structure. We also use premium plastic materials and cutting-edge technology to produce each part with flawless precision.
Dedicated to providing you with a hustle-free customer experience, we offer all the injection molding services you would need under one roof. Whether you need alternative materials, custom finishes, or different injection molding methods, we are fully capable of supplying your needs.
If you are interested in availing some of our injection moulding services, we are more than capable of providing you with an instant quote. This helps streamline the process, and makes all of our transactions more efficient.
FOW Mould is an ODM and OEM manufacturer of automotive plastic injection molding parts and automotive moulds. We work with bothsaloon and commercial automobile manufacturers to develop solutions that are suitable for their brands. Our designteam is experienced in creating comfortable, luxurious, and functional interior & exterior automotive parts and moulds within your budget. We also have professional auto engineering experts that ensure all the automotive injection molding solutions we offer are optimized for assembly.
These three thermoplastic materials are used all the time. They are cost-effective, durable, and can tolerate the stresses of constant use. You likely use products made from these three materials often, if not every day. For example, ABS is the thermoplastic used to make your keyboard and parts of your phone.
I’m making plastic pliers. mostly needle nose pliers. What material should I use, I don’t need strong heat or chemical resistance in the material used. They should not generate static charges, but they should be electrically non conductive.
A key advantage that our injection molding technology could grant you, is the quick production of prototypes. With our use of 3D printers and CNC machines, we are capable of producing your auto plastic parts prototypes in the shortest time possible.
Immould employs some of the best engineering experts to create a wide variety of designs. We utilize designing software to fulfill all of your mold specifications. Just give us your design, and we could have the design ready for you in no time.
We are injection molding designers and manufacturers for several leading automobile brands. Our factory facilities canproduce 900-1000 automotive molds and thousands of plastic injection molding automotive parts in a year. Our services are also diversified to cater to manufacturers of baby products, buckets, home appliances, and furniture among many others.
FOW Mould injection molding auto parts andproduction processes are certified by international regulatory bodies. Working with us would thus make your plastic auto partsindustry-compliant by default.
Here is a table of the most common thermoplastic materials used for injection molding with their unique features and most common applications.
The blog “Materials Used in Injection Molding” provides a comprehensive overview of the various materials suitable for injection molding processes. The author effectively discusses the properties and applications of common plastics, such as ABS, polypropylene, and polycarbonate, highlighting their strengths and limitations. This information is crucial for professionals in the industry who need to make informed decisions about material selection for specific applications. Thank you for sharing this valuable resource, and I look forward to more informative posts that delve deeper into material science and its impact on manufacturing!
Once we receive your specifications, we will have our team of highly skilled engineers to design your molds. With our molding technology, we will utilize our precision molding software to design molds that are as accurate and effective as possible.
CNC machining is applicable in producing prototypes made of more than one material. The machining tools are controlled by computer systems thereby guaranteeing high accuracy and high tolerances. While this prototyping method takes longer than 3D printing, it is more efficient in producing large parts.
Materials used in injection molding are plastics, specifically thermoplastics. There are hundreds of thermoplastics, but the most common thermoplastics used in injection molding are:
We make molds for automotive parts using durable high-grade steel. Our engineers further ensure that the core, cavity, and gate systems are properly structured to facilitate even distribution of resin. The mold structure is then tested for efficiency and to confirm that it has no structural flaws.
Do you need design-for-manufacturing (DFM) assistance? Or, are you ready for production? We have a full suite of services to offer and a lifetime mold guarantee.
Car manufacturers rely on plastic parts to make car interiors luxurious, appealing, and more comfortable. They also apply them as exterior components in lights, bumpers, and other parts because high-quality plastic is durable and weather-resistant.
When it comes to automotive injection molding you will need high-precision parts for the best performance possible. With our extensive injection molding service and overmolding options, we are capable of manufacturing the best molds for various automobile brands.
Once we get confirmation for your mold prototype, we will finish and assemble all your products. With our specialized injection molding technology, we are capable of creating a multitude of copies of your products, with little to no fuss or wasted material.
Before proceeding to the mold-making period, our engineers run analysis on the product design and mold design, preventing any possible mistakes.
GETTING A QUOTE WITH LK-MOULD IS FREE AND SIMPLE.
FIND MORE OF OUR SERVICES:
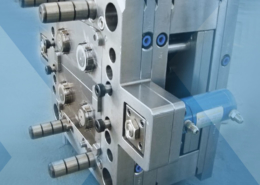
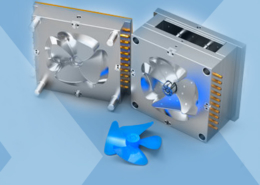
Plastic Molding

Rapid Prototyping
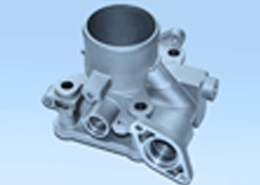
Pressure Die Casting
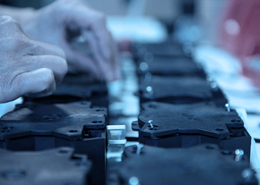
Parts Assembly
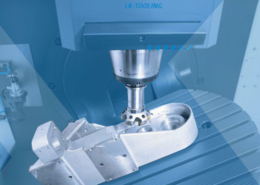