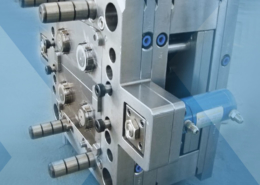
Styrolution PS 5801 - HIPS - hips injection molding
Author:gly Date: 2024-10-15
Medical OEMs are tasked with providing consistent, high-performance solutions to the challenges posed by a variety of complex applications. Partnering with a custom injection molder that has the experience, knowledge, technical expertise, and certifications needed to adhere to the exacting standards of the medical industry is imperative.Not every molder is qualified, but those who are — like Kaysun — can move your business forward with confidence.
RJG Inc. is a training, technology, and consulting company that specializes in the injection molding industry. They offer training courses around the globe, including Master Molder I and II, Systematic Molding, Injection Molding Essentials, and more.[1] They also offer CoPilot, a process control system that allows for data extraction of plastic conditions inside the mold using pressure sensors, transducers and strain gauges. The company is responsible for pioneering DECOUPLED MOLDING® techniques which have since become industry standard.[2][3][4][5][6]
As medical device design evolves to provide ever-improving healthcare outcomes, manufacturers are partnering with full-service, experienced custom injection molders to gain increased design freedom and process efficiencies.Partnering with Kaysun — one of the few injection molders in the country to hold MedAccred Plastics accreditation — is a consistent value-add from part and tooling design through material selection and process control. It empowers many medical OEMs to address issues before they impact production or the bottom line.
Medical device performance is largely dependent on the characteristics of the materials used and application needs such as strength, flexibility, transparency, biocompatibility, safety-enhancing microbe resistance, and temperature and chemical resistance. With thousands of engineered materials to choose from, it's important to work with experts in medical device injection molding.
The rapid advancement of the medical industry necessitates constant innovation and complexity in medical device design. Smaller sizes, more intricate geometries, progressive functionalities, and portability are among the greatest needs in today’s medical equipment — and among the biggest challenges for design and engineering teams.
“Kaysun exceeded our expectations in all areas. They made a complex, gigantic program easy from an engineering standpoint. Working with the Kaysun engineering team is like a hot knife through butter.”
Leveraging the experience and knowledge of medical injection molders during the design phase of complex applications can help overcome the unique challenges of medical injection molding and improve outcomes.
MedAccred is a Performance Review Institute medical device industry-managed supply chain oversight program dedicated to reducing patient safety risk. It focuses on critical manufacturing processes compliance and device quality and consistency.
Kaysun is experienced with medical product design, production, and assembly. We are ISO 13485:2016 certified and MedAccred Plastics accredited.
In 1985, Rod Groleau started a training and consulting company (then named RJG Associates, Inc.), where he developed techniques for retrieving data for plastic conditions inside the mold, previous to this only data from the molding machine itself was used for processing techniques. By 1999, the company developed controls allowing for different "stages" of molding and the "DART" (Data Acquisition and Retrieval with Transducers) system, which allowed for data to be retrieved by personal computers. In 1998, the company began offering Master molder certifications, a training program of robust scientific techniques which is highly valuable to employers in the industry.[7][8][9][10] Since then, the company has continued to develop further innovations that have a major impact on the industry.[11][12]
Portable medical devices are a mainstay in hospitals, emergency vehicles, and outpatient environments. The devices must remain accurate and functional; however, drops, bumps, and excessive vibration are inevitable as equipment is transported from place to place.Overmolding is a proven solution for shock and vibration reduction, sound dampening, electrical insulation, improved chemical/UV resistance, effective oxygen and moisture barrier protection, and color infusion.
Kaysun has carried the MedAccred Plastics accreditation since 2020, demonstrating our ongoing commitment to excellence and assuring medical OEMs of an unparalleled benchmark of production and quality standards.
Earning accreditation is a rigorous process, and only a small fraction of medical injection molding companies receive the distinction.
GETTING A QUOTE WITH LK-MOULD IS FREE AND SIMPLE.
FIND MORE OF OUR SERVICES:
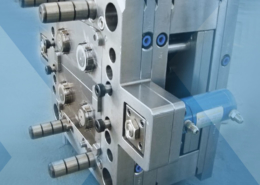
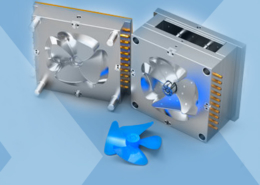
Plastic Molding

Rapid Prototyping
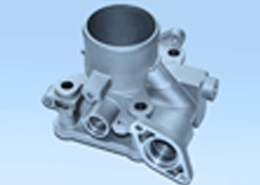
Pressure Die Casting
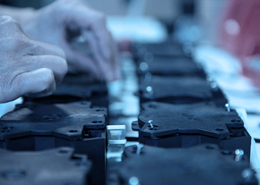
Parts Assembly
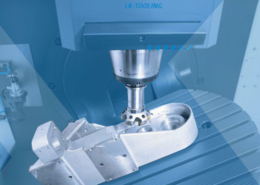