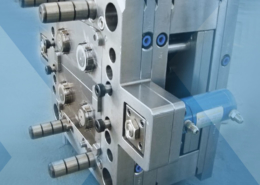
Structural Foam Plastic Injection Molding FAQs - structural foam injection moldi
Author:gly Date: 2024-10-15
In short, the USA and others are leveraging the moment and getting some quality plastic injection molds out of China. Check the references and make sure you call non-competing companies to mitigate your risks. Also hire people that project managed these types of injection mold suppliers to deliver exactly what you ordered.
The ‘prototype mold’, or ‘rapid plastic injection tooling’ is based on the same principle as series plastic injection molds, but has a simplified and accelerated design. It is also not intended for long-term use. The use of a common mold base and aluminum for the molding parts makes it possible to reduce investment costs and machining time. Production of the prototyping mold takes between 2 and 4 weeks and is 40 to 60% less expensive than a traditional mold. The cost and design time of the mold depends on the shape complexity of the part to be molded. After a complete analysis of your plastic parts, our design office creates the tooling plan of your mold. We then start its production according to your specifications.
China has a wide variety of skill sets available from high end to the lowest low. The culture is open to interpretation when the plastic injection mold shop decides how to design the cavitation structures. I suggest having your own injection mold tooling expert and engineering determine the way the cavities function. I also suggest having certifications on hand for all the steel used in the plastic injection molds. This would include all receipts and traceability documentation. There are different levels of quality in China for steel and you made have a variety of heat transfer issues associated with it.
Our rapid plastic injection molding solutions are specially adapted to the production of prototypes and small series of plastic parts (from 100 to 1000+ parts). Inspired by traditional molding techniques, we inject your plastic parts using an aluminum prototype mold (or rapid tooling). The results achieved with this technique are equivalent to series molds. The robustness, mechanical properties and industrialization information are identical.
In rapid prototyping, the use of a prototype mold for plastic injection, therefore, makes it possible to obtain small series using the right material at a lower cost and in reduced time. It is a very good solution for testing your concept quickly and cheaply. There is no need to sacrifice the quality of the final part. You, therefore, obtain reliable information (mechanical, geometric, assembly and industrialization) on the final parts as well as the subsequent production of a series injection mold.
Only one thing made me sleep at night when I have millions of dollars and tight performance timelines. I made the circuit of visitations to the engineering groups, tooling fab shops (all of them including 3rd tier) and plastic molding shops. There is nothing worse than have a several hundred thousand dollar injection molds crash and burn passing the 1000 shot mark. It leaves a mental on you when it happens.
Hello, I have 3D drawings for a project. I would like a quote for injection molding or your prototype mold system. Thank you
Thank you for your comment. We would only need the CAD design of the toothbrush, CAD design of mold would be done by us. On of our project manager will reach to you by email to have more information about you injection molding project.
The design of our injection rapid tooling is based on a standard ‘mold base’ frame and interchangeable aluminum core and cavity inserts. This reduces the investment costs and production times inherent in plastic injection. This is our rapid production technique which is the most expensive. However, it makes it possible to obtain functional parts made from the ‘right material’. They can be marketed or used in transition production.
This technique allows the production of small series that are close to reality. The applications of plastic injection molding are very varied. They are particularly useful in the automotive, packaging, medical, and electronics sectors.
Thank you for you comment. We would need you specifications to advice and quote you : CAD files, volume required, material etc.
This process consists of injecting a molten polymer (thermoplastic material) into the prototype tooling under high pressure. The plastic material is then cooled and solidifies, taking on the shape of your part. This prototyping technique allows the use of a very large range of ‘right material’ resins. The overmolding of metal inserts and the production of parts incorporating two materials is possible.
Thank you for your comment. Best format would be : STP / IGS / XT. I you could provide one of these please we could quote your project.
I suggest anyone sourcing plastic injection mold tooling in Low Cost Countries to make the visit, send a watch dog or anything else to mitigate potential issues. I sourced plenty of plastic injection mold tooling in Low Cost and High Cost countries in Asia during my career with a Japanese owned company.
Cases, cowlings and hulls are examples of parts that we produce very regularly. In a field that requires many tests and certificates, such as the medical sector, the plastic injection can satisfy the regulatory requirements and constraints. (Find out more on our page about standards.)
GETTING A QUOTE WITH LK-MOULD IS FREE AND SIMPLE.
FIND MORE OF OUR SERVICES:
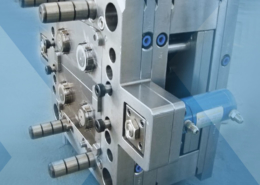
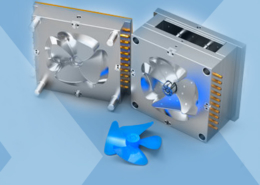
Plastic Molding

Rapid Prototyping
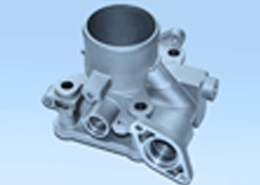
Pressure Die Casting
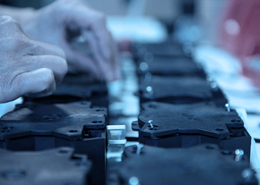
Parts Assembly
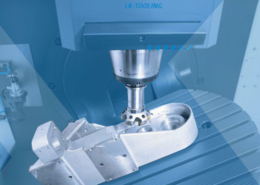