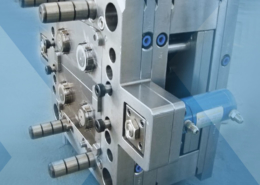
Structural Foam Molding - custom foam injection molding
Author:gly Date: 2024-10-15
Internet Explorer is no longer supported. Please switch to a current browser to be able to use engelglobal.com to its full extent.
Efficient all-electric production of thin-walled injection moulded parts - up to 50% less energy consumption compared to hybrid machines
Molten plastic flows into a mold through a sprue and fills cavities by way of runners and gates. Then, the mold is opened after cooling process and the ejector rod of the injection molding machine pushes the ejector plate of the mold to further eject moldings.
Why do we recommend optimising the injection moulding process? By comprehensively and critically evaluating the process and the production conditions, you define an efficient production flow for greater stability and performance.
Greiner Packaging reduces the wall thickness of food containers by a quarter with e-speed injection moulding machines from ENGEL. At the same time, efficiency is increased. Climate neutrality is the goal of the Austrian packaging manufacturer.
For the properties when reprocessed materials are used, please refer to "reprocessing capability" in the plastic data base.
The performance of electric injection units is constantly increasing. Even challenging applications such as the lid of a thin-walled container can now be produced on fully electric injection moulding machines.
Reprocessed materials are not solely used as materials for molding but usually used after blending with virgin pellets, since there is possibility of deterioration in various characteristics of the plastics because of the initial molding process. The maximum allowable limit for the ratio of reprocessed materials is about 30 %, because too high ratio of reprocessed materials may spoil the original properties of the plastics used.
Margarine tubs made of polypropylene are produced on our e-speed injection moulding machine with integrated in-mould labelling (IML).
The screw is rotated to melt plastic introduced from the hopper and to accumulate molten plastic in front of the screw ( to be called metering ) . After the required amount of molten plastic is accumulated, injection process is stared.
For the requirements of thin wall injection moulding, we have developed a clamping unit with an encapsulated five-point toggle lever. This not only ensures dry cycle times of well under two seconds, but also perfect cleanliness in the mould cavity. All moving elements, as well as the ejector, are sealed and prevent the formation of oil mist or dirt accumulation.
In the production of cartridges, the e-speed demonstrates uncompromising precision and maximum speed - even with complex components.
A high-performance injection unit for the e-motion enables the production of thin-wall packaging with a flow path to wall thickness ratio > 1:400.
Shortest cycle times require machinery with high dynamics. Large batch sizes mean continuous operation 24/7. Our service experts are like our machines - available to you round the clock. So that if the worst comes to the worst, production of thin-walled plastic parts can start up again quickly.
For the requirements of thin wall injection moulding, we have developed a clamping unit with an encapsulated five-point toggle lever. This not only ensures dry cycle times of well under two seconds, but also perfect cleanliness in the mould cavity. All moving elements, as well as the ejector, are sealed and prevent the formation of oil mist or dirt accumulation.
The position of change from speed control to pressure control is set at the point where either screw position or injection pressure reaches a certain fixed value.
Shortest cycle times require machinery with high dynamics. Large batch sizes mean continuous operation 24/7. Our service experts are like our machines - available to you round the clock. So that if the worst comes to the worst, production of thin-walled plastic parts can start up again quickly.
The method is suitable for the mass production of products with complicated shapes, and takes a large part in the area of plastic processing.
Internet Explorer is no longer supported. Please switch to a current browser to be able to use engelglobal.com to its full extent.
We use cookies on this website to ensure your user experience. Please click the button if you agree to the use of cookies. When you keep browsing this website, this will also mean that you are giving consent to the use of cookies.
The ongoing weight reduction of thin-walled packaging by reducing wall thickness is an ongoing topic in the packaging industry. This trend places increasing demands on injection moulding machines.
The hybrid injection moulding machine with hydraulic accumulator for thin-wall applications with the highest performance requirements
A molding consists of a sprue to introduce molten resin, a runner to lead it to cavities, and products. Since obtaining only one product by one shot is very inefficient, a mold is usually designed to have multiple cavities connected with a runner so that many products can be made by one shot.
A double-cavity mould for 1-litre buckets with reduced wall thickness and IML shows what our fastest hybrid packaging machine can do.
Molding condition means cylinder temperature, injection speed, mold temperature etc. set in a molding machine to obtain required moldings, and the number of combinations of conditions is innumerable. Depending on the conditions selected, the appearances, dimensions, and mechanical properties of the molded products change considerably.
The combination of the special ENGEL coinmelt process with a stack mould enables competitive unit costs with low energy consumption.
A mold is a hollow metal block into which molten plastic is injected to from a certain fixed shape. Although they are not illustrated in the figure shown below, actually there are many holes drilled in the block for temperature control by means of hot water, oil or heaters.
Injection molding machine is divided into 2 units i.e. a clamping unit and an injection unit. The functions of the clamping unit are opening and closing a die, and the ejection of products. There are 2 types of clamping methods, namely the toggle type shown in the figure below and the straight-hydraulic type in which a mold is directly opened and closed with a hydraulic cylinder.
Injection molding is a method to obtain molded products by injecting plastic materials molten by heat into a mold, and then cooling and solidifying them.
Water-cooled servo-electric drives make the injection moulding machine the optimum symbiosis of efficiency and maximum performance. Reproducible cycles thus ensure consistent part quality for your thin-walled plastic parts.
The standard molding conditions for our materials are shown below. Please click the mouse at the following names of plastics.
As a producer of plastic packaging, we find that ENGEL listens to us. Suggestions we make are incorporated into the development of the machines.
Sprues and runners among moldings are not products. These portions are sometimes discarded, but in other cases they are finely reground and reused as materials for molding. These materials are called reprocessed materials.
Water-cooled servo-electric drives make the injection moulding machine the optimum symbiosis of efficiency and maximum performance. Reproducible cycles thus ensure consistent part quality for your thin-walled plastic parts.
If the length of the runner to each cavity is different in this case, the cavities may not be filled simultaneously, so that dimensions, appearances or properties of the moldings are often different cavity by cavity. Therefore the runner is usually designed so as to have the same length from the sprue to each cavity.
We have developed dynamic and precise all-electric and hybrid injection units for the production of thin-walled plastic parts. Plasticising components developed for typical thin-wall injection moulding materials ensure high melt quality. Extra powerful servomotors and hydraulic accumulators guarantee reliable filling of the cavities even with extremely high flow path/wall thickness ratios and the shortest injection times.
We have developed dynamic and precise all-electric and hybrid injection units for the production of thin-walled plastic parts. Plasticising components developed for typical thin-wall injection moulding materials ensure high melt quality. Extra powerful servomotors and hydraulic accumulators guarantee reliable filling of the cavities even with extremely high flow path/wall thickness ratios and the shortest injection times.
While molten plastic is flowing in a mold, the machine controls the moving speed of the screw, or injection speed. On the other hand, it controls dwell pressure after molten plastic fills out cavities.
With over 20 years’ experience in thin wall injection moulding, we have designed two dynamic and high-precision powerhouses with our hybrid and fully electric machines e-speed and e-motion. They are especially suitable for applications with high to extreme flow-path to wall-thickness ratios. Thanks to iQ motion control, its powerful clamping unit offers up to 12% shorter dry cycle times at the touch of a button.
GETTING A QUOTE WITH LK-MOULD IS FREE AND SIMPLE.
FIND MORE OF OUR SERVICES:
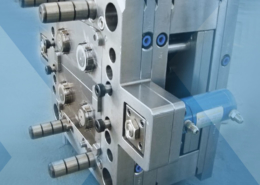
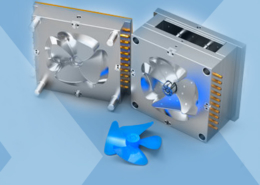
Plastic Molding

Rapid Prototyping
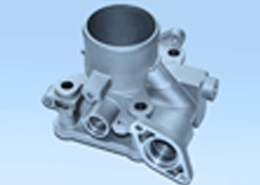
Pressure Die Casting
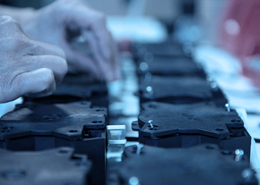
Parts Assembly
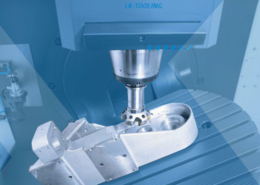