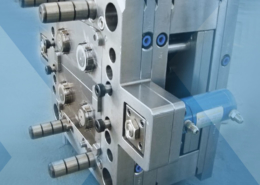
Star Rapid Company Overview, Contact Details & ... - star rapid injection moldin
Author:gly Date: 2024-10-15
The process for injection molding tooling isn’t that complicated. However, the process may vary depending on the products, materials, and specifications you want to meet.
As mentioned, mold plates are one of the molding tools used to produce plastic containers. You can use the number of mold plates to differentiate various plastic injection tools. They include the following:
The next process in the injection molding tooling involves producing several test parts and measuring the properties and dimensions of the molded plastics to see if they meet the required specifications and standards.
Ready to start learning more about automotive plastic molding processes and how they can contribute to better EV production? At Reliant Plastics, our depth of knowledge and hands-on experience are valuable assets to our partners – assets we’re ready to put to work for your next product. From prototyping to large-scale production, we offer key insights, guidance, and access to the manufacturing solutions that will support the electric vehicle industry today and tomorrow.
That’s before we even consider the resins suitable for heavy-duty use, capable of withstanding everyday wear and tear. Add in chemical and heat resistance, and finding plastic materials with the perfect profile for EV use cases is simple.
You can build your molding tools using aluminum or steel. However, aluminum isn’t the best option when producing high-tolerance plastic parts. You should, therefore, use it when making low-tolerant components only.
Generally, you’ll need sophisticated plastic injection molding tools to produce complex parts with added features like threads and undercuts. You may also require additional rotating mechanical gears in case of complex geometries.
The first stage in the injection molding process is the design creation and engineering. It involves creating a 3D CAD model of the injection mold and testing its performance, to see if it produces plastic parts with the desired shapes, sizes, and tolerance, using a simulation software.
It’s the entry point that allows the melted plastic to pass through from the injection unit. The entrance of the injection mold is called the sprue bushing. They connect to runners, tunnels connecting the sprue to the cavity image.
Now that you know your mold qualifies, you can use it for mass production. This involves filling the various mold cavities with the molten plastics and giving it enough time to cool and solidify, taking the mold shape.
After a slow start and a general reluctance among established automakers to embrace electric vehicles, the industry has kicked into high gear. No longer is Tesla the sole independent producer of electric vehicles; today, there are many prominent brand names, including Ford and Chevrolet, navigating the EV space. Even luxury brands, such as BMW, now offer all-electric vehicles.
Using injection molding for electric vehicles, automakers can tap into a flexible, scalable, and highly mature technology with international and domestic production capacity. Modern plastic molding processes remain cutting-edge, incorporating new techniques and technologies. Simultaneously, they provide a highly versatile solution for meeting many material needs within every electric vehicle.
The versatility of plastic injection molding is by far one of its biggest strengths for EV manufacturers. This process does not produce just one or two critical components. Instead, you can apply injection molding to many car parts. Molding suits everything from interior trim components on the dashboard to everyday touchpoints like the charging connector. Even with all the metal pins necessary inside a charging gun, advanced injection molding techniques ensure it is possible to create these assemblies quickly and efficiently.
The next step is to create a prototype mold to test the design. This helps you decide whether or not your model will give you the desired outcome. You can also use this stage to improve your mold design before it reaches the final stages.
The process doesn’t end with a single production. You must maintain the injection molding to ensure it continues producing the high quality products. This means repairing worn parts, making needed adjustments, and cleaning it from time to time.
The automotive industry moves rapidly to meet consumer demand and improve vehicle models from year to year. The world of electric vehicles moves even faster, especially with intense competition driving manufacturers to seek innovations wherever possible. Rapid prototyping, which is possible through injection molding, can swiftly propel projects toward achieving such critical milestones.
Tooling material selection is one of the most overlooked yet critical injection molding tooling designs. Your choice of material will significantly influence the lifespan of your injection mold tooling.
One of the primary ways to differentiate injection molding is by the number of mold cavities. There are three different types of injection molds under this category. They include the following:
The ejector mold or the B plate is the part of the injection molding tool that acts as the exit point through which plastic parts eject from the injection mold.
Here’s where you produce the actual mold. You can use various materials, like aluminum and steel, and techniques, such as electrical discharge machining (EDM), CNC machining, or 3D printing to produce the molds.
The overmolding process is simple. You start by molding the plastic products with a base-color material, ensuring you leave enough room to fit more plastic products with different colors.
The cavity image is an empty space in the injection mold that transforms the molten plastics to their desired shape and size.
Tools mold design, cavitation, and materials impact the plastic injection tooling tolerance. A simpler process is likely to get and maintain a tighter tolerance than complex parts because they can put tight tolerance at risk as there are other variables, such as the number of cavities, to consider.
With so many potential areas to apply molding of components for the electrical sector, the right partner makes a difference.
The most suitable injection molding partners can help you build a highly resilient supply chain to meet the most extensive needs. The repeatable nature of injection molding means you can see hundreds of thousands of product outputs from one extended production run. That level of volume keeps all the parts you need close at hand for the assembly line. Investing in the capacity for large-scale production and the necessary inventory warehousing now means EV makers can also guard against future supply chain disruptions.
There are many types of injection mold you could use for your plastic injection molding process, but two-plate molding is the most used.
Generally, this injection molding tool can have single or multiple cavities, depending on your production volume. Single-cavity molds are called single-impression cavity molds, while those with multiple cavities are called multiple-impression cavity molds.
The convenience, versatility, speed, and scale of injection molding processes make this manufacturing method an obvious choice for supporting today’s EV needs. However, another fundamental reason to choose plastics is that their material properties perfectly suit electric vehicles. Much lighter than comparable parts made in metal, plastic lowers overall vehicle weight substantially and thus contributes to an extended range on a single charge.
An injection mold or A plate is a machined tool used in the plastic injection molding process. It molds the molten plastics into finished plastic goods.
Contact Reliant Plastics for a quote or to get more information on what you can achieve in plastic with Reliant for vehicle manufacturing.
Even components that must withstand extreme conditions, from a corrosive chemical environment to high heat levels, can be produced through injection molding. Molding of components for the electrical sector could yield critical improvements, too. Future battery compartment redesigns could rely on molding for more robust housing or efficient storage designs. Adding this capability to your technology lineup today ensures broad access to critical parts.
Rapid prototyping allows for ideas from the drawing board to be put into tangible materials; test proofs of concepts to be run on shorter timelines, opening the door to rapid iteration. With this technology, you can create a part design ready for full-scale production and inclusion into an EV sooner rather than later.
Finding the best manufacturing company for your custom injection molding process may be a little challenging. You must know the questions to ask and the response you need.
Plastic injection molding or injection molding is the production of plastic parts in large quantities using injection molding machines.
To understand how it works, you must have basic knowledge of the injection molds tools, what they are, how they work, where to find them, and which injection molding tools are best for specific tasks.
With this growing movement to adopt EV worldwide, the sector — already a vigorous, multibillion-dollar industry — seems poised to explode even more in size and value over the next decade. With this pace of change, massive growth in consumer demand, and increase in the number of players, there are genuine concerns about achieving reliable production. Sourcing suitable materials to continue growing and satisfying customers requires a serious heavy-lift effort. The EV industry must embrace several technologies, chief among them plastic injection molding for the automotive industry.
Another way to differentiate the plastic injection molding tools is through their feeding system, a collection of channels, including the runners, gates, and sprues, which direct the molten plastic into the mold cavity.
Now that you know how plastic injection molding tools work, you can start your project. It’s a pretty straightforward process to create plastic containers in large quantities within a reasonable time frame. It’s also affordable and will help you produce quality pieces within the shortest time possible.
Overmolding is the process through which the injection mold forms multiple layers around a single product. It does this by re-introducing the injection molded parts into the mold.
The small opening created when a mold opens is called a gate. Plastic enters the mold cavities through these openings. There are two main gate types found in injection molds. They include:
When the molten plastic molds, the clamping unit slides the B plate from the injection mold creating an exit point and pushing the plastic products out of the injection molds using ejector pins.
GETTING A QUOTE WITH LK-MOULD IS FREE AND SIMPLE.
FIND MORE OF OUR SERVICES:
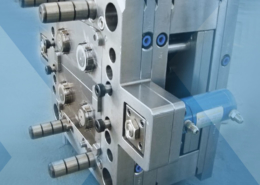
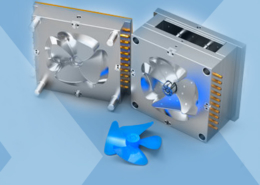
Plastic Molding

Rapid Prototyping
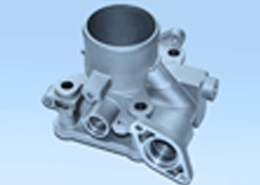
Pressure Die Casting
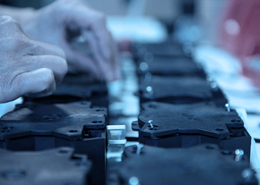
Parts Assembly
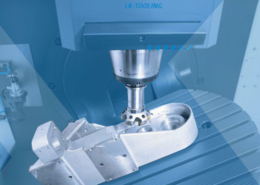