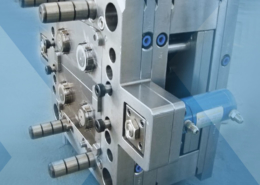
SOLIDWORKS Plastics Part & Injection Mold Analysis Software - injection molding
Author:gly Date: 2024-10-15
A: In polycarbonate injection molding, polycarbonate plastic is melted and injected into a mould to create different parts. It is widely used in making plastic parts that are durable and of high quality.
The software needed to print prototypes is often exclusive to the hardware utilized; nonetheless, the following list of CAD applications is used to produce models:
From my point of view when considering design flexibility and precision offered by polycarbonate injection molding there isn’t an outstanding material for complex detailed designs like this one.it may be observed, therefore that it could be employed in intricate details with great accuracy/ preciseness such as small molds used in automotive industry which require several molds before achieving quality output unlike those made from other materials such as aluminum steel among others whose melting point are very low thus requiring care when designing because poor designs may lead into damages during chilling process but using PC will minimize these challenges.I think this would benefit various industries including automotive manufacturing, electronics (i.e., cell phone covers), medical device production (i.e., catheter tubing), where high precision and accuracy are crucial. In conclusion, polycarbonate is a good choice for many complicated applications because it can make parts that are highly specific and durable.
After treatment of condensation polymerization, they are also referred to as thermosets and show the primary bond between molecular chains. In thermosetting materials, polymers undergo another process known as healing, which is triggered by heat, light, or other suitable radiation. Thermosetting polymers do not melt when heated; instead, they break down and do not reform when cooled. Thermosets cannot be recycled or converted back into their original component.
From my point of view polycarbonate injection molding plays an important part in consumer electronics production including gadgets such as phones. Thus this light yet durable material is commonly chosen for manufacturing different smartphone cases, tablets’ casings or laptop’s shells etc.. The ability to absorb shocks well makes them a favorite among gadget makers because these things are subjected daily wear hence might easily break down if not shielded inside them by hardwearing substances like this one. Besides this it possesses features that facilitate easy shaping into intricate forms especially when crafting sleek modern looking designs that appeal to end users. Hence it comes forth that what makes polycarbonate such an invaluable component in consumer electronics is the combination of reliability with flexibility plus aesthetical options which designers are given access here.
Polycarbonate is known for its exceptional strength and durability, which make it a good choice for molding. It has high impact resistance and does not crack or break under heavy loads. In addition, polycarbonate retains this property over a wide range of temperatures to ensure that the molded parts are reliable even under difficult conditions. However, it toughness and longevity leads to robust production pieces that can withstand heavy use while lengthening product life.
A: While looking for a reliable service provider specializing in injection molding using polycarbonate consider those with experience in polycarbonate processing, strong quality management systems, and positive customer feedback. It is important to ensure that your choice can handle this type of material better.
A: Polycarbonate has excellent qualities such as being transparent, high impact resistance, and stable thermal properties. These advantages have led to its use in production of robust and multipurpose molded parts.
Because larger parts take longer to print than smaller ones, the component volume also affects the cost of additive manufacturing. While some processes need a lot of labor and have high unit costs, other methods are significantly more productive and cost-effective.
The material greatly influences the quality of the prototype. Selecting components made via additive manufacturing may not be the best option if functional features are connected to unique material qualities, such as surface polish and durability. Following are a few examples of common plastic materials used in various industrial processes:
Type: Academic Journal Article Summary: Published in the Journal of Polymer Engineering, this peer-reviewed article explores recent advances in polycarbonate injection molding technology. The study delves into innovations in material formulations, process optimization, and the development of new additives that enhance the performance and durability of molded parts. The research includes case studies and experimental data, providing scientifically validated information on improving the efficiency and quality of polycarbonate injection molding. This source is particularly relevant for researchers, engineers, and industry professionals seeking cutting-edge knowledge and technical data.
Through the use of a plastic injection mold prototype, you may see a practically identical development of your finished product in reality. Many companies, including those in the automotive, electronic, healthcare, and packaging sectors, often use this strategy. It works effectively for items that need a lot of testing and certification.
Maintaining the right injection pressure is essential to achieve quality in the process of polycarbonate injection molding. Injection pressure ranges recommended by leading sources from the top 3 Google websites usually vary between sixty and one hundred fifty megapascals. It helps in achieving complete mold filling while minimizing stress-induced defects.
Manufacturers can swiftly make a high-quality product thanks to injection molding. It works well for extremely small manufacturing runs. You don’t have to compromise product quality in the process of manufacturing. It helps you determine what you need for a full production run.
Since there are some methods to get the desired objective, each has its unique benefits and drawbacks that should be considered. How to choose the suitable one? Continue to read!
For various reasons, injection molding is known to be the best method of making polycarbonate components. One of them is that it allows the production of precise and detailed parts which are important especially in electronic and automotive industries. Moreover, this process is highly efficient as large numbers of parts can be produced uniformly with minimal wastage.
The injection molding machine is an important aspect of the injection process and it is a key factor in manufacturing high-quality polycarbonate parts. It basically blends mechanical together with hydraulic mechanisms to ensure accuracy and effectiveness. The machine consists of two main units: an injection unit and a clamping unit. In this case, the first one melts the polycarbonate material and injects it into a mold whereas the second holds this mold tightly throughout injection as well as cooling stages.
We hope that this article has given you a solid understanding of plastic rapid prototyping processes. It is crucial for both the manufacturer and the client to learn about the features, advantages, and usage of their product globally. By choosing the best prototyping method and service provider, we can improve our product in line with how quickly the world is changing.
Rapid prototyping is appropriate for plastic products that must have an exact dimension or fit. Engineers and product designers sometimes have to test the plastic prototype several times quickly to fulfill deadlines to attain perfection. As the name says, rapid prototyping has this benefit.
A product’s usability and popularity among customers are improved by strategically placing interface elements.Prototyping also helps to save a lot of time. Additionally, it facilitates the design creation process, and during the prototyping phase, it is easy to spot extraneous components that are best left out. The workload of the designer during the manufacturing process is greatly reduced by this technique, ultimately resulting in cost savings for the client.
This particular kind of plastic is the one that is most usually used. The key feature that sets them apart from thermosets is their capacity for several melt and solidification cycles. It can be heated to change its shape or geometric properties. The technique results in no chemical bonding, therefore, recycling or melting thermoplastics is a possibility.
Whether you’re a seasoned professional or a novice in the field, this post will provide you with valuable insights into the world of plastic prototype manufacturing and help you make informed decisions about which method to choose for your project.
With respect to quality and uniformity, performance of the injection molding system has huge impacts on. For example, by keeping accurate control over parameters like temperature, pressure and speed of injections, the molten polycarbonate will be distributed uniformly within the mold cavity. Moreover, these machines may also have automatic systems for monitoring or adjusting these parameters that make them more precise while minimizing chances of failure.
Optimizing the mold temperature and injection speed is an important step in the polycarbonate injection molding process. Maintaining ideal temperatures within the mold ranging from 80°C to 100°C is essential to ensure a uniform smooth surface finish and avoid defects like shrinkage or warping. It is also of significance to balance injection speed since fast one may cause excessive shear stress leading to incomplete filling up the mold or material degradation. These parameters, when properly regulated by manufacturers of polycarbonate parts can enhance mechanical performance as well as aesthetics thus enhancing efficiency and consistency throughout production.
When choosing a prototype option, cost is always an important factor to take into account. The quantity of prototype components needed is essential in determining the procedure since some prototyping methods are only financially viable for lesser numbers.
Some of the key advantages I see with polycarbonate injection molding are resistance to impact as well as sustained use in high temperature environments. The impact resistance of polycarbonate is unmatched ensuring a tough element necessary in products that undergo extensive demand and harsh conditions. For example, safety gears or electronic housings are immensely valuable if they can absorb and take severe impacts without breaking apart. Moreover, polycarbonate performs extraordinarily across broad temperature ranges: it maintains its properties even at extreme temperatures thus making it suitable for different applications depending on environment. In other words, the combination of temperature stability and impact resistance enhances endurance of materials produced from polycarbonates.
Type: Online Article Summary: This detailed article from Plastics Technology provides comprehensive guidelines on polycarbonate injection molding. It covers essential aspects such as material properties, processing parameters, and troubleshooting tips. The article also includes best practices for optimizing mold design, temperature control, and cycle times to achieve high-quality results. This source is highly valuable for both beginners and experienced professionals in the plastics industry, offering practical insights and expert recommendations for successful polycarbonate injection molding.
Additionally, prototyping is a crucial step in the creation of a product. A CAD model is a computer-generated illustration of your concept. Using a CAD model, you may evaluate how your prototype or model will fit together. It will also demonstrate how your product will work, which is more important.
A: Injection molding uses various classes of polycarbonates such as standard, optical, flame-retardant grades depending on application requirements. Each kind has unique attributes best fit for given injection molded parts.
By adding CAM software to the process, manufacturers can fully automate it. Plastic pieces may be machined at a reasonable price, and the whole process takes minimal time. CAD rendering is all you need to get started with CNC plastic prototyping.
A: Some cons associated with this process include expensive materials used for production purposes; environmental and other process variations sensitivity; strict need for temperature regulation among others. When not handled properly during moulding however , it may also suffer from stress cracking.
Numerous varieties of plastic are available for 3D printing, each with unique qualities that make it best suited for particular situations. The main categories of plastics used in 3D printing are described as follows:
To achieve optimum results in polycarbonate injection molding, several key process parameters must be accurately controlled:
One of the most expedient ways to produce plastic prototypes is through CNC precision machining. CNC machines use a range of cutting tools and cutter paths that are specially designed for the desired cut when carving a 3D model directly from a solid block of plastic.
Next, a two-part liquid material such as polyurethane or epoxy resin is poured into the mold cavity. The mold is placed in a vacuum chamber, where the air is removed, creating a vacuum that forces the liquid material into the mold’s cavities and ensures the part is free from air bubbles or voids.
Another great technique for making plastic prototype components swiftly is injection molding. The procedure begins with the construction of an aluminum or steel mold equipped with a runner system, a channel that allows molten plastic to flow to the chamber of the mold. The required plastic prototype is created by injecting molten plastic ingredients into the mold, allowing them to cool and solidifying them.
By carefully monitoring and adjusting the above parameters, I am able to make high-quality polycarbonate parts with excellent accuracy and lower defect rates.
This plastic CNC machining technique is incredibly adaptable and practical for a wide range of product sizes, complexity, and threaded features, and it is especially well-suited to prototypes that need to meet strict tolerance requirements.
The use of rapid prototyping technologies during the production process guarantees a high degree of precision and accuracy. It is fair to believe that design drawings of CAD software are quite accurate. Precision is a crucial component to take into account since it guarantees that your product will be produced consistently.
Additionally, a prototype using this technique will enable you to test every component you want. Additionally, it will serve as the basis for the succeeding mold that will be used for your whole manufacturing process.
Polycarbonate is a highly durable, transparent and versatile thermoplastic. It is amorphous in nature which makes it resistant to impact and its optical properties are great making it a good choice in various industries. It can also withstand high temperatures and is naturally fire retardant thus appealing to applications with stringent safety standards. Additionally, the material can be easily shaped hence making it ideal for injection molding processes that are intricate and precise. The fact that it has a combination of strength, transparency as well as thermal stability makes polycarbonate the preferred material for many types of products ranging from consumer electronics to automotive parts.
In certain cases, a quick prototyping industry will simply require an initial design to start the production process and create a computer model. OEMs (original equipment manufacturers) that want a high-quality prototype quickly and have the financial means to do so may consider using rapid prototyping.
In the medical field, polycarbonate injection molding is widely used because of its toughness, transparency, and compatibility with living tissue. For example, it can be used to make surgical tools, diagnostic units, blood oxygenators and IV parts. The strength of the plastic and its ability to withstand sterilization methods make it a good choice for reliable and safe medical devices. Importantly, its clearness allows observation of direct fluid flow which is significant in some types of diagnostic aids.
To ensure high-quality, error-free polycarbonate parts that are efficiently made with precision, these technical parameters are necessary.
A: In the injection molding technique for polycarbonate, its plastic form is melted and pushed into a mold cavity through an injection molding machine. After that, it cools down and solidifies to get the final shape where it gets removed from the mold.
These steps are carefully regulated so as to produce good quality parts made of polycarbonate having excellent dimensional accuracy and surface finish.
A: These include mold temperature control parameters like screw barrel heat setting temperature cooling time at which material enters the mould at what speed injection should take place for optimum part quality. For instance determining necessary conditions required to achieve good product from polymers like PC.
Investing in an efficient and reliable injection molding machine not only improves production speed and consistency but also minimizes waste and operational costs. As a result, selecting right machinery and maintaining it properly are vital for successful polycarbonate injection moulding operations which make optimum outcomes attainable.
After checking the prototypes, the designer and client can more precisely assess the outcome. That’s why we need to make plastic prototypes.
This blog post aims to explore five different methods for manufacturing plastic prototypes, highlighting the advantages and limitations of each method.
What kind of technique and post-processing you need will depend on how accurately the final product must be produced. You should also think about how well your prototype compares to your finished product in terms of quality. Rapid plastic prototyping techniques provide prototype items with a high-quality surface finish.
Thanks to 3D printing, you may swiftly and effectively create parts for various applications. By using the appropriate 3D printing method and material combination, you may produce things with the desired mechanical properties, functional attributes, or aesthetics.
Vacuum casting involves first creating a master pattern of the desired part using 3D printing or CNC machining. This pattern is then used to make a silicone mold.
Vacuum casting would produce components that are almost comparable to those of injection molding and may be utilized without post-processing, but alternative procedures, like 3D printing, may require some post-processing time but are considerably more versatile for complex shapes.
The method of efficiently manufacturing products is called rapid prototyping. Rapid prototyping is a tool engineers and product designers use for all types of product development. It is a paid professional service.
Type: Manufacturer Website Summary: SABIC, a leading manufacturer of polycarbonate resins, offers a comprehensive technical data sheet and processing guide for their Lexan polycarbonate resin. The guide includes detailed information on material properties, recommended processing conditions, and application-specific considerations. It also provides tips on mold design, cooling systems, and post-processing techniques to achieve optimal results. As a direct source from a reputable manufacturer, this guide ensures accurate and industry-specific information for users involved in polycarbonate injection molding.
From my research on top three websites regarding injection molding, polycarbonate injection molding process entails some key steps. First, the polycarbonate raw material is fed into an injection molding machine where it heats up and melts. This molten material is then shot under pressure at very high speeds into a precisely formed mold cavity. The mold is normally cooled so that the polycarbonate solidifies into the shape desired. Once enough cooling has taken place, the molded part is ejected out of the mold. Parameters such as temperature control settings, injection pressure points and cooling periods are carefully regulated in order to produce quality parts without defects. By this method complex detailed components can be manufactured in large quantities with uniform accuracy
A: Among the many uses for which it can be applied include optical lenses, medical devices, automotive components, consumer goods, electronics housings etc. The implications of versatility and strength on polycarbonates for these industries is overwhelming.
Making prototypes before starting full-scale production of your items might be highly beneficial. The industrial sector has benefited from prototyping improvements by quickly producing plastic prototypes.
A: For information on Polycarbonates and Injection Moulding you may refer professional associations’ journals; manufacturers’ websites or industry’s technical resources. Industry conferences or workshops are also good sources of knowledge concerning new developments in Polycarbonate Injection Moulding Techniques.
From my experiences with polycarbonate injection molding processes, controlling wall thicknesses and melts temperatures are very fundamental. Making sure that there is an even wall thickness over the part eliminates issues such as sink marks, warpage, or uneven cooling that could affect its structural soundness or aesthetic appearance. An optimum thickness for polycarbonate components would be around 2.5 mm on this basis. Furthermore, it is important to monitor melt temperatures, maintaining them at between 250° C to 300° C so as to prevent thermal degradation of the melt flow’s consistency in order for material not lose its original properties through overheating. With these parameters under control, I am able to manufacture reliable high-quality polycarbonate parts that satisfy strict requirements of today’s consumer electronics industry.
Time is an essential factor when performing plastic prototyping. Post-processing and assembling parts from low-quality prototypes will take longer than from high-quality prototypes.
I believe that polycarbonate injection molding is a must for many automobile parts due to their high tensile strength, resistance to heat and reduced weightiness. This material is often employed in making headlamp lenses, interior items as well as other applications located under vehicle bonnet. These items have to withstand extreme temperatures and impacts without deteriorating since they have to meet strict safety requirements. These parts are also very flexible so as to suit any design ideas by engineers who always strive to improve both functionality and aesthetics of vehicles. Polycarbonate therefore becomes an important material in automotive industry due to its combination of durability and versatility.
Once filled, the mold should have a holding pressure between thirty megapascals and seventy megapascals so as to compensate for material shrinkage when it cools down and solidifies. This holding pressure need not exceed the initial injection pressur.
Businesses and entrepreneurs may benefit significantly from prototyping. It is a method of testing your concept before moving forward with large-scale manufacturing. Additionally, it enables the designer to present his idea to potential investors.
It’s essential, first and foremost, to choose a starting point for injection pressure that will be sufficiently high for completely filling a mould cavity. The data shows that it is advisable to start with a pressure of roughly seventy megapascals and then adjust depending on part quality and fill time. A low pressure can result in incomplete filling or short shots whereas excessive flash or stresses may occur if the pressure is too high.
GOLDSUPPLIER.COM expands globally, offering quality business opportunities, cost savings, convenience, and expertise in international trade. Trusted and recognized internationally.
In today’s fast-paced world, product development is becoming more competitive than ever. In order to stay ahead of the competition, engineers and designers must be able to produce high-quality plastic prototypes quickly and efficiently.
A: The PC injection moulding technology entails regulating temperature and pressure correctly to enable the complete melting and flow of polycarbonate material into molds. Also cooling and ejection are equally significant techniques to avoid defects as well as maintain product quality.
The process of CNC machining is subtractive. In other words, it entails removing material from an unfinished item. A milling machine is used to do CNC machining on plastic components. A milling machine has many axes that may be manipulated.
Therefore, if you are a skilled independent businessperson and can make a prototype by hand, it will only cost you in terms of time and materials.
The manufacturing industry is associated with the Polycarbonate injection molding; a process that produces durable and versatile plastic products. This guide provides an all-encompassing view of polycarbonate injection molding techniques, advantages, and applications. This complex field can be navigated by understanding basic properties of polycarbonate materials and complexities of the molding process, which are elaborated in this guide. Either you are a professional who has been doing this for some time or a beginner looking to improve on skills, this article is a great resource to master over polycarbonate injection molding. Essential elements of the process such as material selection, equipment requirements, common challenges, and practical tips for achieving optimal results are outlined in this text.
GETTING A QUOTE WITH LK-MOULD IS FREE AND SIMPLE.
FIND MORE OF OUR SERVICES:
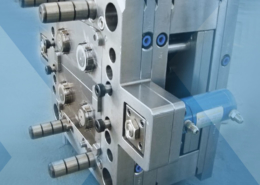
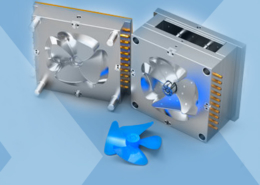
Plastic Molding

Rapid Prototyping
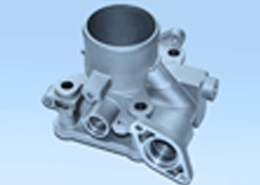
Pressure Die Casting
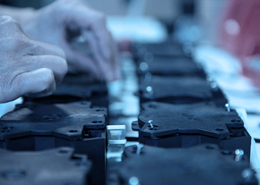
Parts Assembly
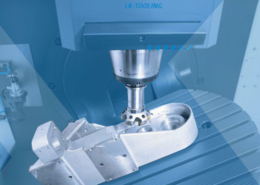