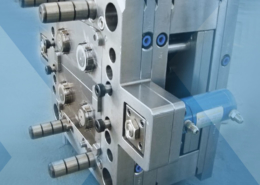
Soft Tooling — Polymer Additive Manufacturing Applied to ... - soft tooling for
Author:gly Date: 2024-10-15
By far, one of the primary benefits of injection molding is its ability to produce a large number of parts rapidly. Moreover, this makes the cost-per-part significantly cheaper.
One of the drawbacks of injection molding can be its inflexibility. Molds are expensive, and once you’ve created the mold for the part, you'll have to spend a significant amount of money to change them.
Other methods such as additive manufacturing, casting, and machining can help you reduce upfront costs. Although these methods still may require set up time, molds, or fixtures, the cost of those items may be lower than the injection mold tool. Companies can also amortize the cost of these upfront items, instead of considering them a capital expenditure.
Even with the drawbacks listed above, injection molding’s many significant benefits may still make it the best choice for aerospace companies. That said, there are some instances where you may want to consider other options.
Injection molding is a manufacturing process that injects molten plastic into a mold (which we often refer to as “tooling”) before rapidly cooling it to produce a large number of parts repeatedly and at low cost.
Their sophisticated product portfolio of Secure Base URL">injection moulding machine construction covers the entire spectrum of the plastics processing industry and meets the most diverse customer demands for the manufacture of mass and high-precision plastic products.
Thanks to its ability to produce a large number of parts at low costs with a variety of different materials, injection molding is a very popular manufacturing process for aerospace manufacturers. It can be used to make parts pretty much anywhere, from inside the cabin to the exterior of the plane.
With the ability to use a variety of different materials, injection molding is widely used not only in aerospace but in other industries as well.
That’s not to say the process doesn't have its drawbacks. With modern advancements in other processes like additive manufacturing, aerospace companies may want to consider other options depending on their circumstances.
The injection molding benefits for aerospace are very similar to the benefits of injection molding for other industries.
This is particularly important for steel tooling. There are other ways to get tooling for less, particularly by using aluminum tooling. However, the best aluminum tooling can usually get you around 20,000 parts. At that level, other 3D printing methods become a competitive alternative.
Injection molding can work with a wide variety of plastic materials, which is why it has so many different applications for aerospace parts. These materials include:
Suppliers, such as The Technology House (TTH), have helped aerospace companies produce injection molded parts for years, following AS9100 standards, and verifying material to assure the highest quality standards and repeatability.
At TTH, a lot of our work with aerospace part manufacturers revolves around interior cabin parts. That said, injection molding can be used for a variety of aerospace parts, from the interior to the exterior, and everywhere in between. Some common applications include:
Most organizations in aerospace will know whether or not they want to use injection molding for their part. Here are some reasons they may not want to choose injection molding:
The materials used for injection molding in aerospace will depend on the part, but there are a plethora of options to choose from, as you’ll see in the benefits below.
Switching to another material, even just an alternative grade, can be difficult in aerospace because of the regulations and testing required for parts and materials. This is already a tedious process, and if you need to change the tooling on top of this, it can increase expenses further.
To optimize their operation, many aerospace manufacturers combine multiple parts and materials into one part during the manufacturing process. Depending on the combined part, it may be difficult to use injection molding, and other 3D printing methods such as Carbon DLS may be more appropriate. At TTH, we’ve used Carbon to consolidate multiple parts into one and streamline our client’s operations.
To ensure you’re using the best process for you, this article is going to cover some of the primary injection molding benefits for aerospace companies, but also give you other options to consider depending on your circumstances.
You can acquire less expensive tooling for lower volumes, but the life of the tool is reduced compared to steel tooling.
Haitian has a solid foundation to take care of what customers really need. They have been sustainably developing their service team and service skills from learning from the past and accumulation of practical experience. They have a well-trained after-sales service team with excellent technical qualification and profound practical experience.
JavaScript seems to be disabled in your browser. For the best experience on our site, be sure to turn on Javascript in your browser.
However, it is still possible to combine parts and materials with injection molding. For example, TTH has manufactured armrests for the interior cabins of commercial aircraft. These armrests have a polycarbonate base that’s injection molded first. After that, the part receives another mold that injects an elastomer that binds to that polycarbonate base.
In a similar vein to the above, if you have complex and intricate parts, injection molding may not be the best for you. A 3D printing method may be better, as it can build intricate assemblies that are strong and durable.
At TTH, our integrated approach to design, prototyping, and production allows you to bring your concept to market faster and more cost-effectively. We focus on delivering products to your specific requirements, and we hold quality standards for ITAR (International Traffic in Arms Regulations), ISO 9001:2015+AS9100D, and Nadcap.
The injection molding process and many of the materials it uses have been around for over a century. It’s a manufacturing method that aerospace companies have tested and proven to be reliable.
TTH’s integrated approach to design, prototyping, and production allows you to bring your concept to market faster, more cost-effectively, than virtually anyone else.
Another aspect you should consider when building the tooling is the material. The tooling you create is designed to work with that specific material, and if you need to switch materials, you may need new tooling as well. As we’ve all learned over the past few years, supply chains can break, and the material you're using may not always be widely available.
With steel production tooling, you can get extremely tight tolerances as low as +/-0.001". This means you can produce a large number of parts with minimal variance in quality and/or dimensions.
GETTING A QUOTE WITH LK-MOULD IS FREE AND SIMPLE.
FIND MORE OF OUR SERVICES:
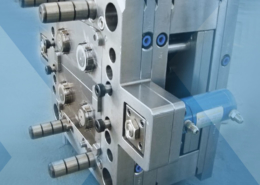
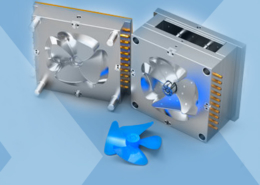
Plastic Molding

Rapid Prototyping
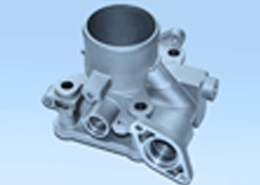
Pressure Die Casting
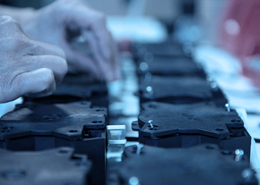
Parts Assembly
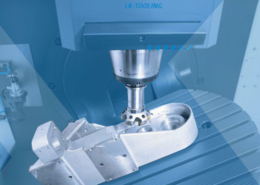