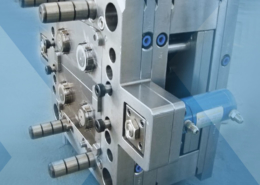
Soft tooling for just 1000 parts. Small production run. - soft tooling for injec
Author:gly Date: 2024-10-15
For more information on listing your equipment with Aaron contact Ricky Schmidt or click here for more information on our listing services.
We are out of stock of all Dies - Molds for Injection Molding Machines. We are always looking to buy high-quality, used Dies - Molds for Injection Molding Machines.
PMMA: Due to its higher melt viscosity compared to ABS, PMMA typically requires higher processing temperatures and slower injection speeds to achieve optimal flow and minimize defects such as melt fracture, warping, or sink marks. The injection molding machine settings, including barrel temperature, injection pressure, and cooling time, need to be carefully adjusted to process PMMA effectively. ABS: ABS has lower melt viscosity and better flow properties compared to PMMA, allowing for faster injection speeds and shorter cycle times. The injection molding machine settings for ABS may involve lower barrel temperatures and higher injection speeds to optimize flow and fill the mold cavity efficiently.
© Copyright Aaron Equipment Company , All Rights Reserved | Site Map
The process of injection molding for PMMA (Polymethyl Methacrylate) and ABS (Acrylonitrile Butadiene Styrene) involves similar steps but may differ in certain aspects due to the unique properties of each material. Here's a comparison of the injection molding process for PMMA and ABS:
Below is Aaron's inventory of unused and used dies and molds for injection molding machines. If you are looking to sell your used dies and molds for injection molding machine submit a request online or contact Erik Eichert at 630-238-7480.
PMMA: Due to its higher stiffness and brittleness compared to ABS, PMMA parts may require careful handling during ejection to avoid stress-induced defects such as cracking or crazing. Proper mold release agents or ejector pin placement may be necessary to facilitate easy part removal. ABS: ABS parts are generally more forgiving in terms of ejection and handling, but care should still be taken to prevent part damage or distortion during demolding. Smooth ejection and part separation help maintain the integrity of the molded parts.
PMMA: PMMA injection molds may require specific design considerations to accommodate its high shrinkage rate and minimize residual stresses in the molded parts. Proper mold venting is essential to prevent trapped air and ensure the quality of the surface finish. Cooling channels in the mold may need to be designed strategically to control cooling rates and minimize warpage. ABS: ABS injection molds may have similar design considerations as PMMA molds but may not require as much attention to shrinkage and residual stresses. Cooling channels are designed to efficiently remove heat from the mold, ensuring consistent part quality and minimizing cycle times.
PMMA: PMMA is sensitive to moisture, so it requires thorough drying before processing to prevent defects such as bubbles, voids, or surface imperfections. Typically, PMMA pellets are dried in a desiccant dryer to reduce moisture content to acceptable levels. ABS: ABS is less sensitive to moisture compared to PMMA, but proper drying is still recommended to ensure optimal mechanical properties and surface finish. ABS pellets are also typically dried in a desiccant dryer before processing.
Contact Information Phone: 630-350-2200 Toll Free: 1-800-49-AARON Email: [email protected]
In summary, while the basic principles of injection molding apply to both PMMA and ABS, the process parameters, mold design considerations, and handling techniques may vary to accommodate the specific properties and requirements of each material.
GETTING A QUOTE WITH LK-MOULD IS FREE AND SIMPLE.
FIND MORE OF OUR SERVICES:
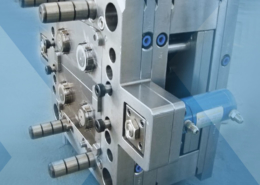
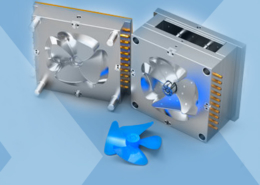
Plastic Molding

Rapid Prototyping
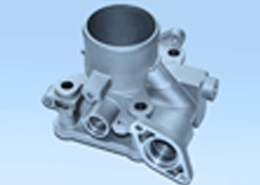
Pressure Die Casting
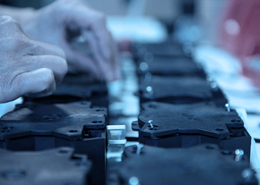
Parts Assembly
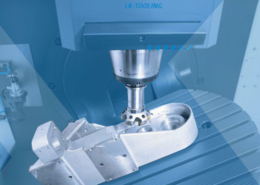