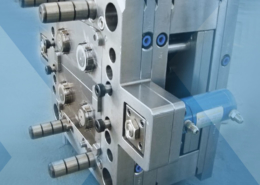
SMARTFLOW® FasTie® Quick Ejector Tie-In System - ejector rod injection molding
Author:gly Date: 2024-10-15
Released earlier, this video remains a valuable recruitment tool and is being re-promoted in celebration of Manufacturing Day 2024.
Discover how CAD/CAM functionality tailored for the mold industry can significantly enhance the mold design process. In part three of the webinar series, Cimatron will focus on designing waterlines and cooling components. It will demonstrate how CAD/CAM tools can verify drill line depths for water lines and baffles, ensure that minimum steel requirements are met while placing water lines, and provide a complete list of all baffle cutoff lengths. Additionally, it will explore how to confidently design runners and gates using CAD functionality specifically developed for these aspects of mold design. Agenda: Waterlines and verification Conformal cooling Baffles and charts Runners and gates
In ISO 9001 quality management systems, the Management Representative (MR) plays a crucial role. While the 2015 version of ISO 9001 no longer mandates this position, having a trusted management member serve as an MR remains vital for streamlining operations and maintaining quality standards.
Efficient cooling is essential to solidify the molten plastic within the mold cavity uniformly. Proper cooling strategies can mitigate warpage, reduce cycle times, and enhance part quality.
Advanced plastic injection molding necessitates a thorough understanding and optimization of process parameters. By carefully controlling injection speed, pressure, temperature, and cooling strategies, engineers can produce parts with impeccable dimensional accuracy and consistency.
IMTS 2024: Open Mind Technologies showcases its hyperMILL CAD/CAM software with enhancements to its toolpath capabilities, overall functionality and more.
After attending IMTS, it's clear that the integration of advanced technologies is ready to enhance precision, efficiency and automation in mold manufacturing processes. It’s a massive event, so here’s a glimpse of what the MMT team experienced firsthand.
The adoption of high precision plastic injection molding offers a multitude of benefits for engineers and manufacturers alike.
In precision injection molding, material selection is a pivotal aspect of achieving optimal part performance, dimensional accuracy, and quality. Engineers must carefully evaluate a plethora of material properties, including but not limited to mechanical strength, thermal stability, chemical resistance, and dimensional stability. High-performance engineering thermoplastics such as PEEK, ULTEM, and LCPs are often preferred for applications requiring exceptional mechanical properties and resistance to harsh environments. Furthermore, the selection of specialized materials with low shrinkage rates and minimal warpage tendencies is imperative to ensure dimensional stability and minimize post-processing requirements. Advanced additives and fillers, including glass fibers, carbon fibers, and nanocomposites, are judiciously incorporated to enhance material properties and tailor performance to specific application requirements. Through a comprehensive understanding of material science principles, coupled with rigorous testing and validation protocols, engineers can navigate the vast array of material options to select the most suitable candidate for precision injection molding applications, thereby ensuring the attainment of superior part quality and functionality. For more information, see our in-depth plastic injection molding material selection guide.
Join MoldMaking Technology Editorial Director Christina Fuges as she gets the latest news on this mold builder's use of VR for mold design education.
Engineers use properly preloaded bolts, blocks, springs and side-action cores to enhance functionality and reliability in various mechanical systems.
A focus on electrode design and automation helps toolroom improve efficiency, reduce tooling costs and deliver higher quality products.
The Kyocera MA90 milling insert series delivers high body rigidity with lower cutting forces in an effort to provide tough and reliable machining performance.
By harnessing cutting-edge technology and meticulous attention to detail, high precision plastic injection molding sets new standards in quality and performance. Precision injection molding refers to a specialized form of plastic injection molding characterized by exceptionally tight tolerances, high repeatability, and meticulous attention to detail in both the molding process and the resulting parts.
Steps to improve data-driven decision-making and key features of a cloud-based system for mold monitoring and asset management.
This method is typically employed for the production of components where dimensional accuracy, surface finish, and consistency are paramount—often in industries such as medical devices, automotive, electronics, and aerospace.
Smart sensors and sophisticated process and measurement data management are driving intelligent moldmaking to new heights.
MoldMaking Technology Editorial Director Christina Fuges sits down with Murphy Forsyth, GM – Injection Molding and Director Of Marketing for Zero Tolerance LLC in Clinton Township, MI.
The need for data to track information and the history of the mold-building process is ever-increasing, and mold component solutions can help.
Identify pain points, tackle each one strategically and maintain flexibility to keep your moldmaking business on a path to growth.
Discover how to enhance your mold design process with CAD/CAM software specifically tailored for the moldmaking industry. In part two of this webinar series, Cimatron will demonstrate how to intelligently design mold components, such as slides and lifters, using powerful CAD/CAM tools to accelerate the design process. Additionally, it will cover how to avoid errors and ensure design accuracy for ejector pins by checking clearance distances, calculating cutoff heights correctly, and thoroughly documenting all ejector components. Agenda: Slides Lifters Inserts Ejection pins and charts
MoldMaking Technology addresses the complete lifecycle of the manufacture and maintenance of a mold—from design to first shot—by providing solutions and strategies to moldmaking professionals charged with designing, building and repairing molds. About Us
Achieving high precision in plastic injection molding demands meticulous optimization of process parameters. Engineers must meticulously fine-tune injection speed, pressure control, temperature management, and cooling strategies to ensure the production of accurate and dimensionally stable parts.
When used for conformal cooling in plastic injection, 3D printing opens a wide range of design freedom. This design freedom enables designers to develop highly-efficient thermal regulation networks. However, this blessing also comes at the expense of not only higher manufacturing cost but also higher design cost as the designer could spend weeks to develop optimal cooling channels. This webinar will explore strategies and tools — including SimForm, a front-end thermal simulation app — to help tool designers and tooling managers maximize the benefits of 3D printing while minimizing manufacturing and design costs. Agenda: 3D printing applied to the plastic injection industry 3D printing pros and cons Tools and methods to facilitate the integration of 3D printing
Shrinkage can pose significant issues in high precision injection molding, particularly when fabricating intricate or dimensionally critical components. Understanding and mitigating shrinkage effects are paramount to achieving precise part dimensions and geometries. Various factors influence shrinkage, including material properties, mold design, processing parameters, and part geometry. Thermoplastics exhibit shrinkage during cooling after injection, with each material having its unique shrinkage behavior. Accurate prediction and compensation for shrinkage require comprehensive material characterization and advanced simulation tools. Mold design considerations, such as gate location, cooling channel layout, and part orientation, play a crucial role in controlling shrinkage-induced distortions. Additionally, post-molding processes such as annealing and stress-relieving treatments may be employed to minimize residual stresses and further enhance dimensional stability in high precision applications.
IMTS 2024: Features such as advanced collision protection and greater operational functionality make Heidenhain’s TNC7 CNC control platform critical for mold builders, who often face multi-surface machining.
Precise pressure control is essential to ensure uniform filling of the mold cavity and prevent defects like sink marks, warpage, or short shots. Pressure requirements vary depending on the material, part geometry, and mold design.
After attending IMTS, it's clear that the integration of advanced technologies is ready to enhance precision, efficiency and automation in mold manufacturing processes. It’s a massive event, so here’s a glimpse of what the MMT team experienced firsthand.
Swiss Steel USA’s E 40 K Superclean offers benefits for a more efficient manufacturing processes in terms of production efficiency and component service life.
Explore the standout articles of September, featuring innovations, expert insights, and strategies to boost efficiency and quality for your moldmaking needs.
Understanding and facing the moldmaking industry’s obstacles to growth requires a strategy focused on increased profitability.
After attending IMTS, it's clear that the integration of advanced technologies is ready to enhance precision, efficiency and automation in mold manufacturing processes. It’s a massive event, so here’s a glimpse of what the MMT team experienced firsthand.
In the realm of high-precision plastic injection molding, the integration of automation technologies has become indispensable for optimizing efficiency, consistency, and repeatability in production processes. Automation solutions encompass a spectrum of sophisticated systems, including robotic part handling, automated mold changeovers, and real-time monitoring and control systems. Robotics play a pivotal role in streamlining material handling tasks, from inserting inserts or overmolding components to swiftly removing finished parts from the mold. Automated mold changeovers dramatically reduce downtime by facilitating rapid mold swaps, enabling seamless transitions between production runs and minimizing setup times. Real-time monitoring and control systems leverage sensors and data analytics to monitor key process parameters such as temperature, pressure, and part dimensions, enabling proactive adjustments to ensure adherence to tight tolerances and quality standards. The seamless integration of automation technologies not only enhances productivity and throughput but also mitigates human error, ultimately empowering design engineers to achieve unparalleled levels of precision and consistency in plastic injection molding operations.
Temperature plays a critical role in plastic injection molding, influencing material flow, viscosity, and part properties. Precise temperature management throughout the process is imperative for high precision parts.
Injection molding machine supplier APSX-PIM now offers a comprehensive desktop FIM package using Nexa3D’s technology to 3D print molds, design parts.
In ISO 9001 quality management systems, the Management Representative (MR) plays a crucial role. While the 2015 version of ISO 9001 no longer mandates this position, having a trusted management member serve as an MR remains vital for streamlining operations and maintaining quality standards.
Steel supplier discusses high thermal conductivity metal powders that also address the skills gaps via user-friendly materials and promote sustainability via durability and higher cycle counts.
Join MoldMaking Technology Editorial Director Christina Fuges as she gets the latest news on this mold builder's use of VR for mold design education.
Injection speed refers to the velocity at which molten plastic is forced into the mold cavity. For high precision parts, a controlled and consistent injection speed is paramount. Rapid injection can induce turbulence and result in uneven filling, leading to variations in dimensions and surface defects.
In ISO 9001 quality management systems, the Management Representative (MR) plays a crucial role. While the 2015 version of ISO 9001 no longer mandates this position, having a trusted management member serve as an MR remains vital for streamlining operations and maintaining quality standards.
A connected software solution streamlines the moldmaking process by providing a unified source of design data, enhancing efficiency and reducing errors, with five key steps benefiting from this integration.
A water-based, eco-friendly plastic mold cleaning system helps Rankine-Hinman Manufacturing restore flow rates and avoid big-ticket failures on complex and costly molds.
High precision plastic injection molding offers unparalleled accuracy, consistency, and performance in the production of complex components. While it presents challenges and requires careful consideration of various factors, the benefits it brings in terms of quality, performance, and innovation make it indispensable in today's competitive manufacturing landscape. By embracing high precision molding, OEMs can elevate their designs and propel their projects to new heights.
Join this webinar where Hexagon will explore how state-of-the-art CAD/CAM technology can drive your business forward. Learn how to optimize tool paths, enhance design accuracy and reduce lead times with advanced simulation. Discover the power of automation and real-time data for continuous improvement. Tailored for mold and die manufacturers, this session offers actionable insights to boost productivity and quality. Don’t miss this opportunity to gain a competitive edge in progressive die manufacturing. Agenda: Key challenges in progressive die manufacturing Optimizing tool paths Enhancing mold and die design accuracy Reducing lead times with simulation Automating processes for greater efficiency Leveraging real-time data for continuous improvement
Diamond compounds, with their varied grades, colors and base options, provide a comprehensive solution for mold builders in need of precise and superior polishing across diverse materials and applications.
Here are some simple solutions for pushed-back or bent pins, pushed-back inserts, high amp deterioration, loose or broken latches and missing or loose ground wire connections.
Formnext Chicago is an industrial additive manufacturing expo taking place April 8-10, 2025 at McCormick Place in Chicago, Illinois. Formnext Chicago is the second in a series of Formnext events in the U.S. being produced by Mesago Messe Frankfurt, AMT – The Association For Manufacturing Technology, and Gardner Business Media (our publisher).
What exactly does a hot runner do? If you’ve been in the injection molding industry for any length of time, you might think the answer is obvious, but it is not.
It’s easy to imagine the advantages automation offers the moldmaking process, but it's challenging to change one’s mindset, develop a plan and invest.
While conventional injection molding processes have revolutionized manufacturing, high precision molding takes it to the next level. The key distinction lies in the meticulous control and refinement of every aspect of the molding process. Unlike conventional plastic injection molding services, which may suffice for less demanding applications, high precision molding requires stringent adherence to precise parameters, including tighter tolerances, superior material selection, and optimized processing conditions. These exacting standards ensure the production of components with unparalleled accuracy and consistency, catering to the most demanding engineering applications.
Steel supplier discusses high thermal conductivity metal powders that also address the skills gaps via user-friendly materials and promote sustainability via durability and higher cycle counts.
Recently, I reposted on LinkedIn the results of an informal survey we conducted, which revealed a shortage of skilled mold designers. It quickly gained a lot of traction. Given the response, I thought I'd summarize the feedback and keep the conversation going.
High precision injection molding relies on state-of-the-art equipment capable of delivering exceptional repeatability, accuracy, and process control. Precision injection molding machines feature advanced servo-hydraulic or all-electric drive systems, providing precise control over injection speed, pressure, and position. These machines are equipped with high-resolution linear encoders and closed-loop feedback systems to ensure consistent part quality and dimensional accuracy. Mold temperature control is critical in precision molding, facilitated by advanced hot runner systems or precise thermal control units (TCUs) for maintaining uniform mold temperatures. Additionally, precision injection molding equipment often integrates real-time monitoring and process optimization capabilities through advanced software and connectivity solutions. This enables continuous process monitoring, data analysis, and adjustment to ensure optimal performance and part quality.
After attending IMTS, it's clear that the integration of advanced technologies is ready to enhance precision, efficiency and automation in mold manufacturing processes. It’s a massive event, so here’s a glimpse of what the MMT team experienced firsthand.
Steps to improve data-driven decision-making and key features of a cloud-based system for mold monitoring and asset management.
Discover how to enhance your mold design process with the right CAD/CAM tool for parting and cavity design. This webinar will explore CAD/CAM capabilities including how hybrid solid/surface modeling can streamline workflow and improve accuracy. Learn how to confidently tackle parting, runoff, and shutoff, ensuring precision and efficiency in your designs. Agenda: Part analysis QuickSplit techniques Parting and runoff strategies Shutoff solutions
NMG has more than 85 years of experience partnering with organizations to bring their industrial, IoT, lighting, medical, telecommunications, consumer, and aerospace products to life. We solve your most complex challenges in engineering design, manufacturing, and supply chain management.
After attending IMTS, it's clear that the integration of advanced technologies is ready to enhance precision, efficiency and automation in mold manufacturing processes. It’s a massive event, so here’s a glimpse of what the MMT team experienced firsthand.
This webinar will provide an overview of new developments in hot runners, controllers, mold components, predesigned molds, process monitoring and mold maintenance equipment. These advancements are designed with the goals of lowering scrap rates, optimizing process temperatures and managing energy consumption. The solutions also aim to support productivity and may contribute to extending the operational lifespan of tooling equipment. Agenda: Innovative undercut and thread-forming components Predesign mold bases and plate control Melt delivery and control solutions Process monitoring and maintenance
NPE2024: The University of Massachusetts Lowell extends an invitation to its Alumni and Friends Reception to university alumni and industry professionals, highlights successful programs giving hands-on manufacturing experience.
Hasco’s hot runner plug and socket inserts reduce wiring times. Via the elimination of time-consuming screwing operations during wiring in the wiring box, cable assembly can be carried out in just a few seconds.
Quality Tool and Die team discusses the journey from a small automotive tool shop to a diversified full-service moldmaking and plastic production facility.
Precision mold design entails meticulous attention to detail, encompassing extremely detailed thought as to gate type andplacement, parting line definition, core and cavity construction, cooling system optimization, and surface finish requirements. Utilizing advanced CAD/CAM software and simulation tools, engineers meticulously craft mold designs with optimized flow paths, uniform cooling channels, and minimized residual stresses to ensure flawless part replication. Moreover, the selection of high-grade tool steels, surface coatings, and advanced machining techniques further enhances mold durability, wear resistance, and longevity. Through a synthesis of cutting-edge technology, rigorous analysis, and deep domain expertise, precision injection mold design empowers engineers to realize the most demanding geometries and tolerances, facilitating the production of components across diverse industries with unparalleled precision and consistency. Let's explore the critical aspects of precision mold design and fabrication.
Gerardo (Jerry) Miranda III, former global tooling manager for Oakley sunglasses, reshares his complete mold design checklist, an essential part of the product time and cost-to-market process.
Barnes Molding Solutions highlights its side gate nozzles which offer customers good ease of use and reliability, even with challenging plastics.
The Walter USA Tiger·tec Gold grade WSM37G is most effective for machining blind-hole and through-hole threads in hard steel, stainless steel, cast iron and heat-resistant super alloys.
By incorporating advanced design techniques, leveraging state-of-the-art fabrication processes, and fostering a culture of collaboration and continuous improvement, design engineers can create molds that enable the production of complex, dimensionally accurate parts with unparalleled precision and consistency.
Precision injection molding involves the use of advanced equipment, tightly controlled process parameters, and high-quality molds to achieve precise control over material flow, cooling rates, and part ejection. Achieving high precision in injection molding necessitates a blend of advanced strategies and techniques tailored to meet exacting requirements. The resulting parts exhibit minimal variation in dimensions and properties, meeting stringent quality requirements and often requiring minimal or no post-processing.
GETTING A QUOTE WITH LK-MOULD IS FREE AND SIMPLE.
FIND MORE OF OUR SERVICES:
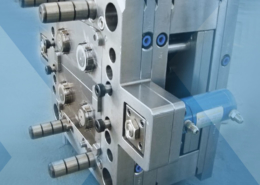
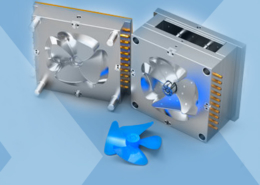
Plastic Molding

Rapid Prototyping
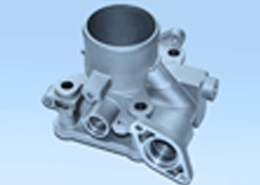
Pressure Die Casting
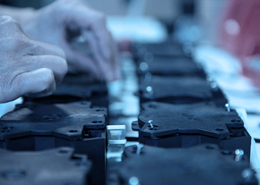
Parts Assembly
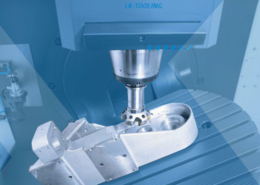