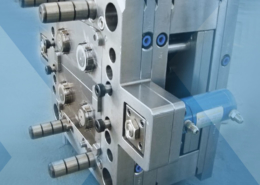
Scope of Plastic Injection Moulding Business: Overview - injection moulding busi
Author:gly Date: 2024-10-15
Founded in Guangdong, China in 2002. It has spread its wings all over the world. Specializing in the molding equipment manufacturing industry. Under the global management, Yizumi’s production bases are distributed at home and abroad, covering a total area of nearly 300,000 square meters, and now have more than 2,500 employees.
The Chen Hsong Group was established by Dr. Chen Chiang in 1958. Chen Hsong produces around 15,000 machines annually, approximately 1 machine sold in every 10 minutes, with a customer base covering more than 90 countries worldwide, including China, Taiwan, U.S.A., Canada, France, U.K., Germany, Turkey, India, Brazil, Argentina, Mexico and most S.E. Asian countries. Clamping force starts from 20 tons to 6,500 tons, with shot weight from 28g to 110kg.
Less expensive tooling not only saves on the initial production costs but also lowers the cost of design changes and modifications.
L.K. Group was founded in 1979, Hong Kong. After more than 20 years of development, it has now become a large enterprise group with assets exceeding 100 million yuan and the annual output value of several hundred million yuan. At present, the Group has established comprehensive product research, development, production, quality assurance, and service system, and has become one of the world’s largest manufacturers of hot chamber die casting machines.
Plastic Processing Machinery, Metal Processing Machinery, Mechanical Control Systems, CNC Milling Machines, Rubber and Plastics Processing
In 1997, the enterprise was transformed into a private enterprise. At present, it has become one of the top injection molding machine manufacturers in Zhejiang. Haida series injection molding machines designed and developed by the company are recognized and trusted by customers with stable quality after being put into the market.
Tederic Machinery is an intelligent injection molding machine manufacturer. Tederic has 4 overseas subsidiaries in Portugal, South Korea, Brazil and Mexico. More than 1000 employees all over the world.
The Group now has mainly covered five industries. And more than 70 subsidiaries at home and abroad. 2020 total output value of the Group exceeds 15 billion RMB, and its products and customers are located in more than 130 countries and regions around the world.
RIM is a thermoset manufacturing process where two liquid polymers are blended and then injected into a single heated mold. When the blended polymers hit the sides of the heated mold, they begin a chemical reaction that causes them to expand to fill the mold, then set into a solid part.
Because of the chemical reaction that takes place, RIM manufactured parts have a swirled, variable finish. If a RIM part is going to be visible in the final product, it needs to be painted.
Every project has an ideal process. If you’ve been considering RIM for anything beyond initial prototyping for your next custom plastic fabrication and plastic manufacturing project, we’d recommend that you look at the advantages of thermoforming before you make up your mind.
Thermoformed parts are completely recyclable. In fact, we can recycle the trimmings from all our thermoforming projects right here in the factory to be sent back to our suppliers, who reprocess them back into the thermoplastic sheet.
Our large part thermoforming capabilities allow us to make a single part of up to 10’x 18’. This means that we can consolidate what would be multiple RIM parts into a single large thermoformed part. There are a number of advantages to this type of part consolidation, including reduced part numbers, reduced inventory levels and less assembly time on the manufacturing floor. All these individual advantages combine for one big benefit: saving you money.
RIM is definitely an option worth considering as an alternative to prototyping, but when you move past prototyping into larger production runs there are several reasons to choose thermoforming over RIM.
Founded in 1955, one of the largest injection machine manufacturers in China. SOUND has two factories in Hang Zhou and Deqing. Three coordinate detection equipment and 70 sets advanced equipment imported from Japna, Italy.
Injection molding machine is an important plastic processing equipment. It is widely used for manufacturing a variety of parts, from the smallest components to entire body panels of cars. Advances in 3D printing. In 2018, the market size (sales) of injection molding machines in China reached 36.59 billion yuan, with a compound growth rate of 6.9% in the past five years, and is expected to maintain a compound growth rate of 5.6%, increasing to 48.06 billion yuan in 2023.
If you do decide to paint, you’ll have an easier time with thermoformed parts than with RIM, since a thermoformed part’s surface will accept paint more readily than a RIM part’s and less surface prep and less paint will be required to get a high-quality finish.
Founded in 1982, started to manufacture injection molding machines in Hong Kong China. It’s a core subsidiary of Datong Machinery Co., Ltd. It is a Sino-Hong Kong joint venture injection molding machine manufacturer that produces fully automatic injection molding machines and its auxiliary equipment. The is a core subsidiary of Datong Machinery Co., Ltd. It is a Sino-Hong Kong joint venture injection molding machine manufacturer that produces fully automatic injection molding machines and its auxiliary equipment.
In contrast, thermoformed parts can be molded in texture and color, allowing them to be aesthetically appealing without being painted.
We’ve listed four of the most common reasons here, and you can get more info from our RIM vs. Thermoforming comparison table.
To move from prototyping into larger quantity production, RIM manufacturing requires a 2-sided mold, similar to the molds used in injection molding. In contrast, thermoforming uses a single-sided mold. While RIM tooling is still cheaper than injection molding tooling, thermoforming tooling is significantly more affordable than either process, and allows you to get your product to market faster.
Hitcontrols is one of the finest suppliers, and is recognized as the market leader in hot runner accessories in China. Heating elements, hot runner controllers, sequential valve gate controllers, thermocouples. Moreover, build and sell professional and custom products to meet the needs of customers’ plastic injection moldings.
We’ve been getting a few questions recently about the process of Reaction Injection Molding, commonly referred to by its acronym, RIM.
According to the ranking of China Plastic Machinery Industry Association, the top 10 injection molding machine companies in China in 2020 are ranked according to their main business income as follows:
Borch Machinery Co., LTD (Borche), established in 2002, specializes in self developing, manufacturing and selling intelligent injection molding machines (IMM). Three manufacturing bases: Guangzhou headquarters with R&D and manufacturing base, Hangzhou plant and Guangzhou Intelligent manufacturing demonstration plant of Two-Platen machine.
In 1978, is the leading brand of injection molding machine in Taiwan. FCS was successfully transformed into plastic injection molding machine manufacturer. In addition to the original business of injection molding machine R & D, manufacturing and sales, since 2001, FCS also branches out into Magnet cable business, 3C optoelectronics and materials technology industry.
Founded in 1966, with over 50 years of growth, Haitian Group has developed into a large multinational company with total assets of over 10 billion.
GETTING A QUOTE WITH LK-MOULD IS FREE AND SIMPLE.
FIND MORE OF OUR SERVICES:
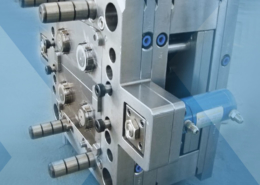
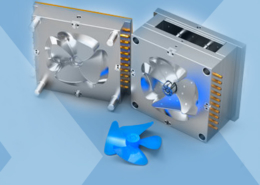
Plastic Molding

Rapid Prototyping
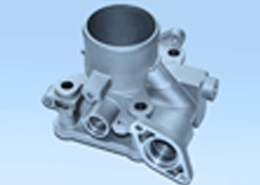
Pressure Die Casting
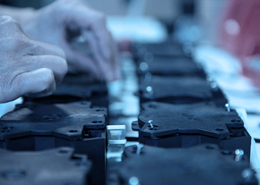
Parts Assembly
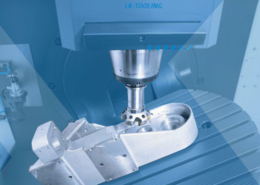