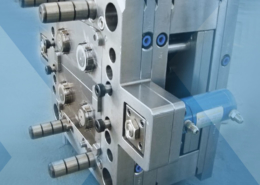
Rotational Molding - plastics rotational molding
Author:gly Date: 2024-10-15
IML is widely used in food and beverage packaging, medical and healthcare products, automotive and industrial parts, and consumer goods. Its efficiency, cost-effectiveness, and customizability make it suitable for various industries.
In mold labeling (IML) is revolutionizing the packaging industry, offering cost-effective, sustainable, and durable labeling solutions to industries like food and beverage, medical, and consumer goods. If you work with injection molding or blow molding, understanding IML Labeling's process and benefits can significantly impact your product's aesthetics and functionality.
In-mold labeling typically uses label materials like polypropylene or polystyrene, with a thickness ranging from 15 to 40 micrometers (µm).
Plastic Tooling Manufacturing has served customers since 1964, giving us many years of experience in the industry. You can rely on us for quality plastic products and services for your business.
Injection molding is the predominant process used in IML. While seemingly simple, this process requires precise control of various variables to ensure the quality of the plastic components produced. By understanding the process and its parameters thoroughly, manufacturers can find suitable plastic component suppliers more easily.
If you need custom plastic packaging made, we can get the job done. Our service include injection moulding, screen printing, pressure-sensitive labels, heat transfer labels and tool making. With our wide range of capabilities, we’re sure we can take care of your projects to your satisfaction. If you have questions or aren’t sure how we can help you, just ask.
IML containers are fully recyclable, making them eco-friendly. They do not require adhesives, reducing environmental impact and making them eligible for post-consumer recycled (PCR) products.
Grease Cartridges: Lubrication manufacturers and suppliers who are looking for high quality and reliable solutions to their packaging needs should look no further than Plastic Tooling Manufacturing. With over 50 years of experience in mould design and construction while also being responsible for the production of the first Grease Cartridges in Australia (450g variant). Produced locally in our Sydney factory you can be assured of competitive pricing, the highest quality and rapid delivery time frames. Fortunately, you are at the right place because Plastic Tooling Manufacturing can fulfil your requirements when it comes to plastic grease cartridges.
After most of the plastic is injected, pressure is applied for a specific duration, known as the "holding time." This time is crucial for ensuring proper plastic formation and tool packing. After cooling, the plastic conforms to the mold and bonds with the label.
Plastic Tubs/Buckets: Aside from multi-purpose grease cartridges, we also manufacture plastic tubs/buckets. We have many size options to suit your individual needs.
IML offers high-quality, customizable labels that elevate brand image and attract consumers. Its rapid design changes and full-color printing capabilities ensure products stand out on shelves, providing a competitive edge in the market.
If you would like to make an enquiry, please call us on (02) 9427 4455 or send an email to sales@plastictooling.com. Alternatively, you can reach us by filling out our online contact form and our friendly team will get back to you promptly. We look forward to hearing from you, and we hope to do business with you soon!
We provide ready-made products from our grease cartridge manufacturer, including tubs, buckets and cartridges. These products are leak-free, available in a variety of colours and made right here in Australia. Take a look at what we have to offer, and get in touch with us for more information.
At Plastic Tooling Manufacturing, we have top of the range machinery, assembly, and resources to mass-produce plastic products. Place your order today for 450g grease gun cartridges or plastic buckets, and we will manufacture these items as per your requirements.
Decoration On Plastic: The next step is decoration. A company that’s in the business of lubrication distribution or production needs to differentiate their range from others by using a grease container that’s appropriately decorated. At Plastic Tooling Manufacturing, we have just the right tools and resources to decorate our plastic products.
In mold labeling, also called in mold labels or IML, is a method that involves the placement of a pre-printed polypropylene label (decorative film) into a mold prior to the formation of the plastic container. It makes the label merge with the molten plastic, creating a single product with a durable, high-quality label integrated into the container's surface.
IML creates a durable bond that resists peeling, cracking, and fading, even in challenging conditions such as humidity, temperature fluctuations, or harsh environments. This durability ensures that the label remains intact throughout the product's lifespan, maintaining its appearance and functionality.
After holding and cooling, pins or plates expel the pieces from the tool. These parts fall to the machine's bottom, where they are collected on a conveyor belt or in a compartment. The finished product is now a plastic product with a printed label.
As the molten plastic reaches the end of the barrel, the gate, which controls the injection of plastic, closes. The screw advances, pulling a predetermined volume of plastic through and building pressure within, readying it for injection. The mold tool's two components are held tightly together under high pressure or clamp pressure.
We are the plastic tooling manufacturing specialists who can manufacture custom ordered products without any difficulty. Importantly, we can produce them in large quantities, to suit your needs. 400g Grease Cartridges 450g Grease Cartridges
In-mold labeling is a versatile, cost-effective, and sustainable solution for various industries. Understanding the benefits and process of IML can help you make informed decisions and achieve high-quality, visually appealing labeled products. If you're looking for an IML service, consider Huarong, a leading injection molding machine manufacturer with exceptional in-mold labeling capabilities. If you need in-mold labeling, please feel free to contact Huarong.
A pre-printed polypropylene label is taken by an in-mold label robotic arm and inserted into the mold. This ensures that the label is properly positioned for integration into the final product.
Thermoforming is slightly different from injection molding and blow molding. In thermoforming, manufacturers use heated plastic sheets that are formed into containers using a forming tool. The preprinted labels are incorporated into the plastic sheets during the forming process, resulting in labeled containers.
Depending on your requirements, you can order buckets of 250ml or 375ml, 500ml, 3L or 20L. More importantly, they are food safe and come with a screw cap and snap lid option. Plastic Tooling Manufacturing can supply these plastic buckets in any colour that you require.
Our team uses three techniques to decorate the plastic products that we manufacture in Sydney. These techniques are screen printing on plastic, adhesive and heat transfer labelling. You can choose whichever option best suits your requirements and budget when it comes to grease cartridge decorations. Screen Printing Adhesive Labels Heat Transfer Labels
Injection Moulding Specialists: The quickest and most cost-effective method to mass-produce plastic products is arguably the injection moulding technique. Be it grease gun cartridges, plastic buckets or other similar products, this technique yields fantastic results which are much cheaper than alternative methods.
Injection molding is the most widely used in-mold labeling method. This process uses an to mold thermoplastics or thermosetting polymers by injecting heated and liquefied plastics or polymers into a mold. The plastic takes its shape as it cools, and the label is seamlessly integrated into the final product. Injection molding is widely used for products like plastic containers, butter or ice cream tubs, skin cream packaging, plastic paint buckets, computer keyboards, and cell phone keypads.
In-mold label typically utilizes materials compatible with the injection molding process and can bond well with the molded product. The most commonly used materials for in-mold labeling are:
Welcome to Plastic Tooling Manufacturing Pty Ltd, your premier partner in plastic packaging solutions. With a passion for high quality plastic packaging and a commitment to provide the best customer support. Our extensive facilities, backed by decades of expertise, enable us to deliver packaging solutions that exceed your expectations. Discover the difference of working with a trusted partner who values quality, reliability and performance.
When using IML, consider your container requirements, container shape, container size, surface consistency, and printing location to ensure a successful labeling process.
When it comes to sevice delivery, we rank second to none. Our company has completed thousands of custom projects in Sydney since we started our business way back in 1964. Here are the top reasons why companies, distributors and small scale enterprises love working with us! We have an experienced team working at our site, enabling us to deliver high-quality plastic tooling manufacturing services in Sydney. You can talk to our customer service if you have any questions related to our plastic tooling manufacturing services. Plastic Tooling Manufacturing will provide you with a free quote for grease cartridges, plastic buckets and any other custom product you want.
IML simplifies labeling, reducing production costs and saving time. Its integration into the molding process eliminates extra steps, labor, and materials, boosting production efficiency and ensuring consistently high-quality labeled products.
Injection molding equipment can be powered by electricity or hydraulics. Raw thermoplastic pellets are fed into the machine's hopper and gradually fed into the machine's barrel. The screw rotates, progressively heating and melting the thermoplastic until it becomes molten.
The process of in-mold labeling is unlike traditional methods, where labels are applied after production, applying a label or design to a product during the manufacturing process. How does in-mold labeling work? There are several options. The top three IML techniques are injection molding, blow molding, and thermoforming.
Blow molding is the second most used technique for in mold labeling, especially for hollow plastic parts. In this process, manufacturers stretch or extrude a heated plastic mass to fit the shape of a mold. Air is then blown into the hollow tube to capture the mold's shape, resulting in a hollow plastic product with an integrated label. This method is commonly used for liquid containers like shampoo bottles, liquid soap containers, and containers for ketchup and sauces.
IML offers numerous benefits across industries, including increased branding options, cost-effectiveness, durability, and environment-friendly. It also helps prevent counterfeit products, ensuring product authenticity and security.
GETTING A QUOTE WITH LK-MOULD IS FREE AND SIMPLE.
FIND MORE OF OUR SERVICES:
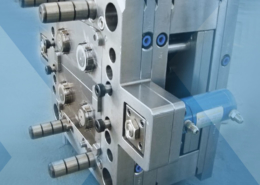
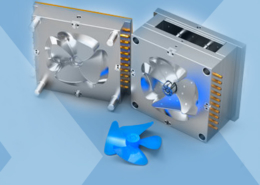
Plastic Molding

Rapid Prototyping
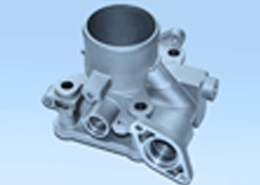
Pressure Die Casting
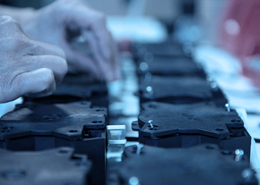
Parts Assembly
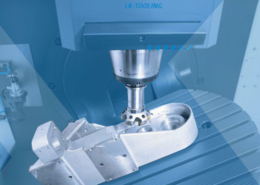