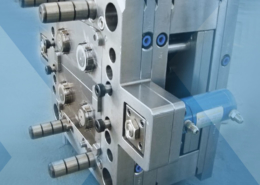
Rosti: Innovative injection moulding systems geared for the ... - rosti injectio
Author:gly Date: 2024-10-15
ABS (acrylonitrile butadiene styrene) injection molding is a standard way to make ABS plastic products. ABS is a strong and lightweight thermoplastic polymer thatâs easy to work with. The process involves adding molten ABS into a mold cavity and then removing it after it cools. Itâs a fast and useful method thatâs used to craft ABS products at an affordable cost. Itâs a popular go-to for household appliances, tools, and medical devices. Itâs used to make Lego bricks, computer keyboard keys, power tool housings, and power outlet fittings, and in the automotive sector, is used for dashboards, seat belt parts, door trim, and bumpers. Below is a picture of a part made with ABS injection molding
Scrap also depends on the plastic material being used for production. Thermoset materials like epoxy resin cannot be molten again once it is cured due to exposure to air. Any attempt to melt them will simply cause the plastic to burn. Thermoset material scrap is unfit for recycling or reusing for this reason.
Die casting is a great manufacturing process. This is a guide for buyers so finding the right factory in China is faster and more efficient
The mold closes once the machine cycle starts. Then the auger injects molten plastic in high pressure into the empty space of the mold, called the cavity. It just takes a few seconds to do this. There are coolants present around the mold to speed up the process of solidifying molten plastic. In as little as 60 seconds, the molten plastic obtains the desired shape.
Repeatability: Plastic injection molding machines can repeat the production of the same unit as many times as you want. That translates to having your second product identical to your first one, and the third identical to the second, and so on. Every business owner is concerned about brand image and consistency. Injection molding machines take care of that concern with this feature of repeatability. With all products made identical, there is little chance of faulty products going out to the consumers.
China Supplier - 7 Ways to Find a Reliable China Supplier - It can be difficult to navigate the seemingless endless clutter of suppliers and vendors in China. Here are our best tips to find the best supplier in China.
Plastic injection molding 101. This beginnerâs guide will walk you through the injection molding process step by step. Find out how you can make the most of plastic injection molding
Despite this simplicity in the fundamental process, this technology is highly efficient. The probability of error is minimal. Manufacturers and industrialists around the globe rely on injection molding to produce quality goods with consistency.
The basic mechanism of the technology is rather simple. At first, the machine injects molten plastic into a metal mold. Inside the mold, the liquid plastic eventually cools and hardens. Once the plastic is no longer molten, the metal mold separates into two, revealing the finished plastic product inside.
Sourcing Allies is a team of expert China sourcing agents that has helped western customers manufacture and source products from low-cost regions since 2006.
The intricacy of the parts you can make is only limited by a set of well-established DFM (design for manufacturing) guidelines that are created specifically for injection molding. It can make multi-featured, complex parts with metal inserts or overmolded soft-grip handholds, and you can easily add a range of colors (think: Lego bricks). This is all without the need for much human intervention, something that keeps labor costs to a minimum and also makes the parts more affordable for customers (obviously the cost and time required increase with the complexity of the part). ABS is easy to shape, recyclable, resistant to chemicals and heat, and has a low melting temperature. It wonât allow dirt to get in, but it doesnât do too well in UV light and prolonged outdoor exposure. To give it a little more power against the elements, it can be painted or electroplated with metal.
Almost any thermoplastic can work for injection molding. They can be filled with reinforcing additives like glass or carbon fiber fillers. You can also inject metals if itâs combined with a plastic filler, allowing the metal powder to flow through the mold. That said, additional sintering is needed for metal injection molding. The ABS injection molding process is the same as with most other thermoplastics. Resin pellets get fed into a hopper, where theyâre melted and injected into a mold using high pressure. Once itâs cooled and re-solidified, itâs removed from the mold. The simple and efficient process makes it perfect for high-volume production, and it creates very little waste, too.Â
Then the mold opens and the plastic structure is ejected. In just a minute or so, the machine successfully produces one unit of the product and is ready to go again.
Low scrap rates: A traditional CNC machining would cut off a huge chunk of the original plastic sheet or block fed to it. That leads to the problem of growing scrap rates. All of that waste plastic has to be recycled, reused, or disposed of. Any of these options incur an additional cost, apart from the manufacturing cost itself. Injection mold machines do a great job at reducing scrap. It would in turn save money that would otherwise be spent on proper management of the scrap. Wastage occurs in these machines only in case of malfunction or defects. The gate location, sprue and runners of the machines do produce some scrap, but it is considerably less than what CNC machining would do. Sometimes there is also loss due to leakage from the metal moldâs cavity. Technologies like 3D printing, however, produce even less (or none) scrap.
The content appearing on this webpage is for informational purposes only. Xometry makes no representation or warranty of any kind, be it expressed or implied, as to the accuracy, completeness, or validity of the information. Any performance parameters, geometric tolerances, specific design features, quality and types of materials, or processes should not be inferred to represent what will be delivered by third-party suppliers or manufacturers through Xometryâs network. Buyers seeking quotes for parts are responsible for defining the specific requirements for those parts. Please refer to our terms and conditions for more information.
ABSâs viscosity increases when heated past its plasticizing temperature (unlike most other amorphous plastics), so it needs to be kept at or below that temperature for good results, especially when it comes to molding thin-walled components. Aside from an increase in viscosity, higher temperatures can chemically degrade ABS, if kept well above the plasticizing temperature. The plastic could also warp if it cools unevenly, but this can be prevented by using a mold with evenly spaced cooling channels. It could also shrink unevenly during cooling, creating sunken areas on the surface, if the temperature is too high or the injection pressure isnât sufficient. Again, these marks (known as sink marks) can be avoided if you use a mold with a high gate pressure.
The machine is made up of four main parts: an injection unit, a clamping unit, the control, and the base. To start the process, a barrel containing an internal screw-shaped device is fed with small plastic pellets. The screw-shaped device, known as the auger, feeds the plastic to the barrel by rotating the plastic at a high force. The body of the barrel is fitted with heater bands, which effectively melts the plastic.
Different finishes: Whether your product needs a smooth finish or a rough one, it can be easily done in an injection molding machine. By default, most machines produce products that have a very smooth finish. The good news is that you can alter the type of finish you desire without any additional operation. These machines also have the ability to produce unique finishes, like engravings or patterns. No matter what type of finish you want: shiny, rough, matte, it can all be done in the same machine, with the same efficiency and accuracy.
Control over color: Injection molding machines can infuse whatever color you want to your product. It is even possible to get two or more colors in a single product. You can achieve this with the use of two-shot or overmolding techniques. For plastic products aimed at children, like toys, having control over color determines the success of the product to a great extent.
Complex designs: Many complex designs can be produced without any secondary operation in a molding machine. It is achieved by using unscrewing features and core pulls. By eliminating the need for secondary operations, you can save money on the overall production cost. The designs can be parts with threads and side holes, and the molding machine will deliver the exact same product, finished with all the complexities, right out of the machine.
To conclude this brief guide on plastic injection molding, we can safely say that it is one of the breakthrough technologies of our generation. It has enabled the mass production of quality goods on an unprecedented scale. Every field of production employs this technology to get their work done effectively and efficiently. So if you are a manufacturer or industrialist wondering how to take your business to the next level, setting up a plastic molding machine is a safe and reliable option. With the development in all fields of technology, it can also be safely assumed that plastic molding machines will only get better and even more efficient with time.
Xometry provides a wide range of manufacturing capabilities, including CNC machining, 3D printing, injection molding, laser cutting, and sheet metal fabrication. Get your instant quote today.
In 1872, an American inventor named John Wesley Hyatt patented this technology for manufacturing plastic billiard balls instead of Ivory ones. His product did not become a success, but ultimately his technology did. Technology has skyrocketed from that point. Initially, it was used to produce simple plastic equipment like balls and buttons. Today, the same technology powers all fields, from medicine to automobiles to electronics. It would be hard to imagine the things we see around us everyday the same way if this technology did not exist. Before delving into why and how this method became so popular and effective, letâs see how plastic injection molding works.
Quality control in China can be difficult. Here are some real and on-the-ground insights on quality in the Chinese manufacturing sector.
The technology of injecting plastic into a mold is used in every industry to some extent. That leads us to the question of why it got so popular in the first place.
In relation to the actual injection molding process, thereâs a high initial investment for the machinery (which is why itâs better suited for high-volume production), and a minimum part quantity is needed to break even on mold costs. In addition, some may find the DFMâs rules a little limiting when it comes to more creative designs. These standards were created to improve part quality and consistency, as well as cover things like wall thickness limits, the location of reinforcing features (like ribs), and the best hole location/size.
Thermoplastic material, on the other hand, can be recycled and reused. It can be molten again even after it has already been melted and solidified before. Often this recycling takes place within the factory. By scraping waste out of the sprues and runners and injecting it back to the machine, wastage is reduced to a great degree. The recycled material is termed re-grind. It is generally of inferior quality than the plastic that has not been reused. Regrind material is generally used for those units that do not require high-quality, robust material. One production unit can also accumulate a substantial amount of regrind and sell to some other unit that produces goods with inferior material. Overall, plastic injection moulding does a better job than other production technologies in terms of time, money, and resource management.
ABS injection molding is a common manufacturing process that involves injecting molten plastic into a mold cavity under high pressure and temperature. This technique is used in the automotive, consumer products, and construction industries for producing various components and products. Weâll cover the definition, uses, process, and techniques involved with ABS injection molding below, but for a brief recap, take a look at our short video below:
One of the major reasons is the technologyâs efficiency. When units can be produced in under 60 seconds, a few hours of application of the machine yields hundreds of units of the product. As more and more units are produced, the initial cost of setting up the machine is met in a very short time. After that point, the profit generation goes up by leaps and bounds. While saving time and money are the primary reasons this technology has garnered widespread popularity and dependency, there are some other reasons as well.
The average cost of these projects is generally $1,000-$20,000. The ROI also depends on the size of the manufacturing unit. The scale of the production unit and revenue are directly proportional. With a high scale of production, the cost of the machine is covered up in a short time. With low scale production, the time needed increases. The complexity of the design, material used, part size and quantities of production are the factors upon which the initial cost of setting up the machine depends.
Ever wondered how mass production units produce hundreds of thousands of pieces of the same part over and over, with exact precision every time? It is made possible by a technology called plastic injection molding. All those plastic caps, phone cases, keyboards that you use have been manufactured by some type of plastic injection molding. Due to its high efficiency and accuracy, plastic injection molding is one of the vital components of modern industrial production technology. If you are already curious about how all those components, both little and big, are manufactured by the millions with absolute accuracy, the intricacies of the technology will capture you even more. Letâs find out more about how this technology works.
Getting a perfect design before your machine starts production is very important. A faulty design will result in huge losses and unsatisfactory products. That is the main aspect of injection molding which needs a big investment. Designing and prototyping the part and the mold tool incurs a heavy cost. The Return of Investment, however, covers up for the cost if the prototypes are designed to perfection. Designing the tools and the prototypes requires a considerable amount of time and money, and that keeps some manufacturers away from using these machines. Owing to the complexity of some of these designs, only experienced engineers can manufacture them. Cost of hiring skilled technicians increases in this scenario. If this one time investment is not a hindrance, an injection molding machine makes up for the investment in a very short time.
GETTING A QUOTE WITH LK-MOULD IS FREE AND SIMPLE.
FIND MORE OF OUR SERVICES:
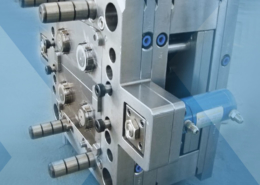
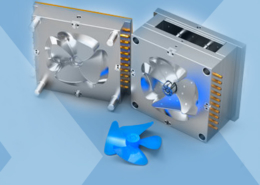
Plastic Molding

Rapid Prototyping
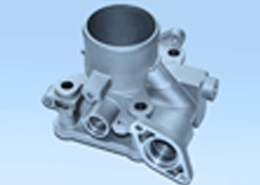
Pressure Die Casting
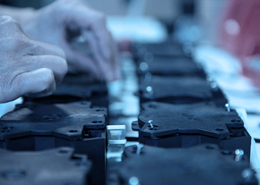
Parts Assembly
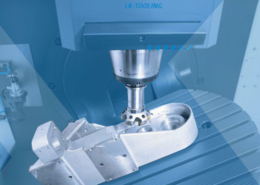