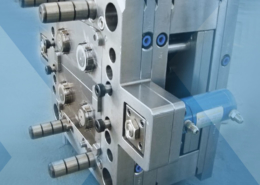
Unveiling the Versatility of Soft Plastic Injection Molds
Author:gly Date: 2024-06-08
Soft plastic injection molds represent a cornerstone of modern manufacturing, offering unparalleled versatility, precision, and efficiency in the production of a wide range of products. These molds enable the creation of complex, flexible components with intricate details and superior quality. In this article, we delve into the world of soft plastic injection molds, exploring their principles, applications, advantages, and future prospects.
Understanding Soft Plastic Injection Molds
Soft plastic injection molding is a specialized manufacturing process that involves injecting molten thermoplastic polymers into a mold cavity to produce flexible components. Unlike traditional injection molding, which typically uses rigid materials, soft plastic injection molding employs elastomeric or rubber-like materials that offer flexibility, resilience, and durability.
Principles of Operation
The soft plastic injection molding process begins with the preparation of thermoplastic pellets, which are melted and injected into a mold cavity under high pressure. The mold cavity is carefully designed to impart the desired shape, texture, and flexibility to the final product. After cooling and solidification, the molded part is ejected from the mold, ready for further processing or assembly.
Material Selection
Soft plastic injection molding supports a wide range of materials, including thermoplastic elastomers (TPE), thermoplastic polyurethanes (TPU), and silicone rubbers. Each material offers unique properties such as flexibility, hardness, and chemical resistance, allowing for tailored solutions to meet specific application requirements.
Process Optimization
Optimizing the soft plastic injection molding process involves fine-tuning various parameters such as temperature, pressure, injection speed, and cooling time. Advanced molding machines and control systems enable precise control over these parameters, ensuring consistent part quality and performance.
Applications Across Industries
Soft plastic injection molds find widespread use across diverse industries, catering to a variety of applications and market needs.
Medical Devices
In the medical field, soft plastic injection molding is utilized to produce components such as seals, gaskets, and flexible tubing for medical devices and equipment. The biocompatibility, sterilizability, and precision of soft plastic molds make them ideal for critical healthcare applications.
Consumer Products
Soft plastic injection molding is employed in the production of consumer products such as silicone phone cases, rubber grips, and flexible seals. These products benefit from the soft, tactile feel and shock-absorbing properties of soft plastic materials, enhancing user experience and product durability.
Automotive
In the automotive industry, soft plastic injection molds are used to create weather seals, gaskets, and vibration dampeners for vehicle interiors and exteriors. The ability to produce flexible, durable components with tight tolerances and complex geometries contributes to the comfort, safety, and performance of modern vehicles.
Advantages and Challenges
Soft plastic injection molding offers numerous advantages, but it also presents certain challenges that must be addressed.
Advantages
Flexibility
: Soft plastic injection molds enable the production of flexible, elastomeric components with varying degrees of hardness and softness.
Design Freedom
: The process allows for intricate part geometries, textures, and overmolding of multiple materials, expanding design possibilities.
Durability
: Soft plastic components exhibit excellent resilience, tear resistance, and chemical compatibility, ensuring long-term performance in demanding environments.
Challenges
Material Selection
: Choosing the right material for soft plastic injection molding requires consideration of factors such as hardness, elasticity, and environmental resistance.
Tooling Complexity
: Designing and fabricating molds for soft plastic injection molding can be complex and costly, particularly for parts with intricate geometries or overmolded features.
Process Control
: Achieving consistent part quality and performance requires precise control over molding parameters such as temperature, pressure, and cooling time, which can be challenging to maintain.
Future Perspectives
The future of soft plastic injection molding holds promise for innovation and advancement across various fronts.
Advanced Materials Development
Research and development efforts are focused on the development of novel soft plastic materials with enhanced properties such as biocompatibility, conductivity, and recyclability. These materials will enable the creation of next-generation soft plastic components for diverse applications.
Process Optimization and Automation
Advancements in molding machine technology, robotics, and automation will streamline the soft plastic injection molding process, reducing cycle times, minimizing waste, and improving efficiency. Smart manufacturing solutions and real-time monitoring systems will enhance process control and quality assurance.
Conclusion
In conclusion, soft plastic injection molds represent a versatile and indispensable technology in modern manufacturing, offering unparalleled flexibility, precision, and performance. As industries continue to demand innovative, high-quality products, the role of soft plastic injection molding will only grow in importance. By embracing technological advancements, materials innovation, and collaborative partnerships, the soft plastic injection molding industry is poised for continued growth and evolution in the years to come.
GETTING A QUOTE WITH LK-MOULD IS FREE AND SIMPLE.
FIND MORE OF OUR SERVICES:
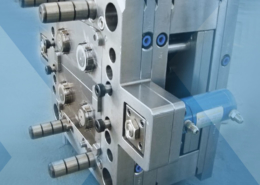
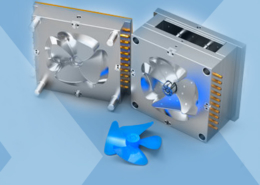
Plastic Molding

Rapid Prototyping
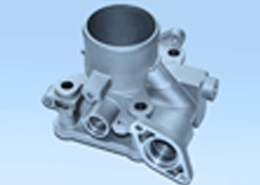
Pressure Die Casting
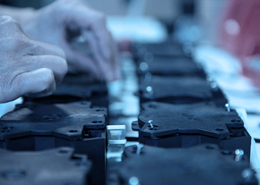
Parts Assembly
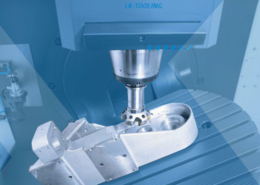