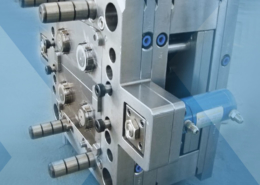
Recommended 15 China Injection Molding Companies - best plastic injection moldin
Author:gly Date: 2024-10-15
Our Promise - From “Conception to Completion” of your product, we will always operate with integrity and pursue the best interests of our customers.
In order to improve productivity and ensure product quality, the basic principle of injection molding cooling systems design is to ensure uniform cooling of plastic parts. Please pay attention to the following points when designing:
Water-cooling systems operate by circulating cold water through channels within the mold. This water absorbs heat from the mold, reducing the temperature of the plastic material. It works on the principle of conduction, where heat transfers from the hot mold to the cooler water. It is an ideal cooling system for intricate molds and materials sensitive to temperature changes.
We service our customers throughout Australia and overseas, we are known throughout Victoria and have become respected in our local business community by proudly serving our customers with integrity and true customer service in plastic injection moulding and fibre extrusion.
Sink marks are depressions or dimples on the surface of the molded part. They are caused by uneven cooling, where thicker sections of the part cool more slowly than thinner sections, resulting in the surface sinking inwards.
A well-designed injection molding cooling systems can significantly shorten molding time, improve injection molding productivity, and reduce costs. However, an improperly designed cooling system will lengthen the molding time and increase costs; uneven cooling will further cause various defects of plastic products. Here are some common cooling-related defects in injection molding:
Thermal pins are fluid-filled cylinders placed in cooling channels. They draw heat away from the mold by cycling between gas and liquid phases. As the gas cools, it condenses into a liquid, repeating the process. Thermal pins are highly effective at heat conduction, provided there are no air gaps between the pin and the mold.
Warping occurs when the part cools unevenly, causing it to deform or bend. This defect is often seen in parts with varying wall thicknesses or inadequate cooling channels.
Please note: In cooling systems, the “water” used is actually a mix of fluids. The cooling tower blends water with a biocide to combat microbial growth. In the lines near the injection mold, water combines with ethylene glycol to prevent rust formation.
Air-cooling systems function by using fans or blowers to dissipate heat from the mold’s surface. Unlike water-cooling systems, they rely on convection, where hot air is replaced by cooler air, gradually lowering the mold’s temperature.
There are two standard methods for injection molding machine cooling systems: air cooling system and water cooling system.
Bubblers are tubes inserted into drilled holes to connect coolant channels. They allow coolant to flow from one channel, bubble up through the tube, and then return to another channel. This mechanism increases surface exposure to coolant and is particularly useful for areas that lack milled or drilled channels. Bubblers play a crucial role, particularly when dealing with laminar flows, same as baffles, they introduce turbulence into the coolant’s path to enhance heat dissipation.
Air cooling is a practical choice for molds with simpler designs and materials less sensitive to temperature fluctuations. While it offers cost-effective advantages and ease of installation, it falls short in terms of efficient heat absorption and precise temperature control when compared to water-cooled systems.
During molding, the high-temperature plastic melt is filled into the cavity through the gate. The mold temperature is high near the gate and the temperature at the end of the material flow is low. Set the cooling water inlet near the gate so that the overall flow direction of the cooling water and the material flow direction in the cavity tend to be the same (the water and materials are parallel), and the cooling is relatively uniform.
Blisters are raised or bubble-like defects on the surface of the part. They occur when air or gas is trapped within the material due to insufficient cooling, causing it to expand and form blisters.
Conformal cooling revolutionizes injection molding, particularly for complex parts. It introduces cooling channels that closely match the intricate geometry of these parts. This approach ensures consistent cooling, even in challenging-to-reach areas of the mold.
We are also custom injection moulders and extruders and manufacture for all your project requirements to add value to your value stream.
Couple that with flexibility, quality and competitive prices, and it’s no surprise that we have a very loyal customer base.
Jetting happens when the material flows too quickly into the mold, causing it to cool rapidly upon contact with the mold surface. This can result in visible streaks or lines on the part’s surface.
This method involves creating cooling channels in the mold tool through standard techniques like drilling or milling. These channels are typically straight but may include features like baffles or bubblers. Traditional cooling is most suitable for parts with simpler geometries, ensuring effective cooling throughout the entire part.
The injection mold structure and design directly influence various aspects of the final product, including its dimensional accuracy, surface finish,
Compared with an air cooling system, a water cooling system has exceptional heat absorption and temperature control, and it is an ideal cooling system for intricate molds and materials sensitive to temperature changes. However, it needs higher initial setup and maintenance costs compared to an air cooling system.
The distance between the hole wall and the mold cavity should be appropriate, generally greater than 10mm, and 12~15mm is commonly used. When the wall thickness of the plastic part is uneven, the cooling water channel in the thick wall should be appropriately close to the mold cavity.
In injection molding, regardless of the cooling channel type within the mold, there’s a risk of part defects when certain areas of the mold stay too hot and are far from the cooling channels. To address this challenge and create a more efficient cooling system around the molded part, designers employ specific features known as bafflers, bubblers, and thermal pins.
Some of these products include Plastic plant pots, Gardening pots, Native tree tubes, and Plastic crates that are sold online as packs or wholesale to nurseries throughout Australia.
The injection molding cooling systems is a vital aspect of the manufacturing process, impacting product quality and efficiency. Understanding the methods and designs for effective injection molding cooling systems is essential for successful mold design. At Zhongde, we offer extensive expertise in cooling methods and mold design techniques. Our experienced team is ready to collaborate with you to optimize your injection molding projects for production efficiency and quality. Whether you’re seeking advice on technology options, materials, or project development, we’re here to assist you.
Injection molding flow marks are a common injection molding defect. While flow marks generally do not influence the structural integrity
Reasonably set the arrangement of cooling water channels to reduce the temperature difference between inlet and outlet water. The arrangement of cooling water holes must be reasonable. The cooling water channel should be arranged according to the shape of the mold cavity as much as possible. The shape of the plastic part is different, and the position of the cooling water channel is also different.
To prevent these cooling-related defects, it’s crucial to design and implement an effective injection molding cooling system, optimize cooling channel placement, and monitor and control cooling parameters during the injection molding process.
Danbar Plastics is Regional Victoria`s Premier Plastic Custom Moulders. Danbar Plastics is a custom plastic injection moulder and plastic extruder. We are also a manufacturer of our own plastic moulded products for the Horticulture, Nursery products, Viticulture, Furniture, Sporting, Construction, Automotive, Food, and Brush Fibre Industries. Danbar Plastics Custom Injection Moulders provide their plastic injection products and services to companies throughout Australia and overseas.
Have you ever noticed a whitening phenomenon in PVC product whitening? Some of your transparent PVC products, like shower curtains
Baffles are blade-like metal plates within cooling channels. They divert coolant from a main channel to a side channel and back, creating a helix-like flow. This design enhances temperature distribution by increasing the surface area that coolant can reach. When dealing with laminar flows, bafflers introduce turbulence into the coolant’s path. Turbulence enhances heat dissipation by exposing more of the coolant’s surface to the hot injection mold.
Established and operated since 1987 Danbar is situated in regional Victoria and is easily accessible to Melbourne. Accessibility – Approachable management team with businesses or individuals. Quick mould or Toolmaking prototype modifications. Flexibility – Short lead toolmaking lead times, custom pricing, low setup costs, short run custom plastic injection moulding capabilities.
There are two primary types of cooling in injection mold — traditional cooling and conformal cooling. Each one is built on the general concept of cooling channels through which a cooling agent (such as coolant or water) can flow.
Injection molding cooling systems play a crucial role in the injection molding process, directly influencing both product quality and production efficiency. The cooling stage accounts for about 60-70% of the injection molding cycle. Reducing cooling time and improving cooling efficiency will make injection molding production more efficient. To achieve this goal, two crucial elements are needed: the right injection mold cooling systems design and the ideal cooling method. In this post, we’ll delve into the critical role of injection molding cooling systems, guiding you in selecting the best options for your projects.
We help "Create your Solutions" from idea to delivery to the customer we can manage the design of the product, manufacture it , pack it, store it, warehouse it then arrange and organise the distribution and delivery of your plastic products.
GETTING A QUOTE WITH LK-MOULD IS FREE AND SIMPLE.
FIND MORE OF OUR SERVICES:
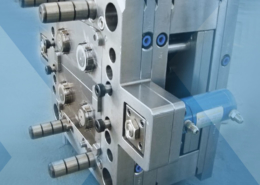
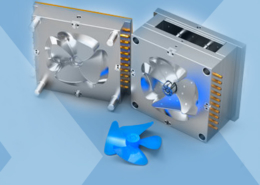
Plastic Molding

Rapid Prototyping
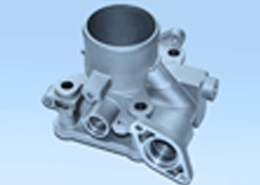
Pressure Die Casting
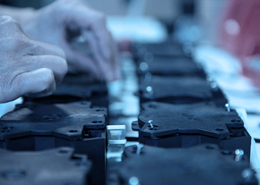
Parts Assembly
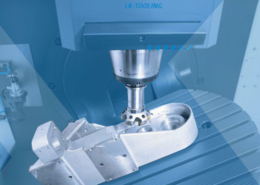