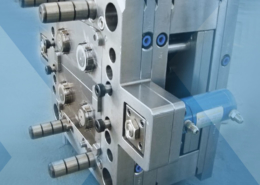
PVC Material Products Injection Molding - pvc injection molding
Author:gly Date: 2024-10-15
Blazing speed plus shrinking energy consumption supported the “green” theme at the big show. Smarter controls and growing connectivity were another key focus.
This month’s resin pricing report includes PT’s quarterly check-in on select engineering resins, including nylon 6 and 66.
While the major correction in PP prices was finally underway, generally stable pricing was anticipated for the other four commodity resins.
Mexico’s booming automotive industry inevitably became part of the conversation with exhibitors at the country’s largest plastics trade fair, Plastimagen.
It started in a garage and evolved into a multi-plant, $100 million operation that holds particular expertise in multi-shot molding.
Across all process types, sustainability was a big theme at NPE2024. But there was plenty to see in automation and artificial intelligence as well.
Of course, we are also always available to customers with in-house injection molds. In the preliminary stage, we express the expectations, on the day of arrival the molds are installed on the machine and by means of a trial injection the products are presented for approval. We ensure that this transition goes smoothly as if no transfer has taken place. Are you curious what Fleur Plastics can do for you? Feel free to contact us and we will discuss the possibilities!
Thousands of people visit our Supplier Guide every day to source equipment and materials. Get in front of them with a free company profile.
Join this webinar to explore the transformative benefits of retrofitting your existing injection molding machines (IMMs). Engel will guide you through upgrading your equipment to enhance monitoring, control and adaptability — all while integrating digital technologies. You'll learn about the latest trends in IMM retrofitting (including Euromap interfaces and plasticizing retrofits) and discover how to future-proof your machines for a competitive edge. With insights from industry experts, it'll walk you through the decision-making process, ensuring you make informed choices that drive your business forward. Agenda: Maximize the value of your current IMMs through strategic retrofitting Learn how to integrate digital technologies to enhance monitoring and control Explore the benefits of Euromap interfaces and plasticizing retrofits Understand how retrofitting can help meet new product demands and improve adaptability Discover how Engel can support your retrofitting needs, from free consultations to execution
In its 50th year, Matrix Tool applies moldmaking and injection molding expertise, plus a long family heritage, to high-precision jobs that many would deem impossible.
Discover how artifical intelligence is revolutionizing plastics processing. Hear from industry experts on the future impact of AI on your operations and envision a fully interconnected plant.
Exhibitors and presenters at the plastics show emphasized 3D printing as a complement and aid to more traditional production processes.
To compete in today’s market, you need good technology, but you also need to know what you stand for and what you’re good at.
The foundation only begin with a good product drawing that complies with the design rules: uniform wall thicknesses, part line, discharges, roundings, position of injection and undercuts, and the position of the injection of the die. No problem, we are happy to help you with the product design.Our first step is to analyze the product drawings and discuss with you the requirements the product must meet. Based on this, we also make an estimate of what the mold must meet and whether it fits within your budget.
There are five specific areas that designers and manufacturers need to consider to realize the potential of these unique materials.
The latest developments in all-electric and hybrid injection molding machines from several Japanese OEMs made their debut at Platex Osaka, a triennial show held in April in Osaka, Japan.
Joining metal and plastics to target some of today’s most dynamic industries, contract manufacturer Tenere reinvented itself—and its customer list—in 2016.
Resin drying is a crucial, but often-misunderstood area. This collection includes details on why and what you need to dry, how to specify a dryer, and best practices.
The diversity of electric machines will be on display at this year’s show, with several new all-electric versions in direct-drive and belt-driven versions.
Currier Plastics had a major stake in small hotel amenity bottles until state legislators banned them. Here’s how Currier adapted to that challenge.
Multiple speakers at Molding 2023 will address the ways simulation can impact material substitution decisions, process profitability and simplification of mold design.
The Plastics Industry Association (PLASTICS) has released final figures for NPE2024: The Plastics Show (May 6-10; Orlando) that officially make it the largest ever NPE in several key metrics.
If you’re interested in lightweight composites, IML, LSR, multi-shot, inmold assembly, barrier coinjection, micromolding, variotherm molding, foams, energy-saving presses, robots, hot runners, and tooling—they’re all here in force.
Despite price increase nominations going into second quarter, it appeared there was potential for generally flat pricing with the exception of a major downward correction for PP.
Nissei’s upcoming NEX-V Series will have OPC-UA protocol standard in its new controller, ready to integrate with auxiliaries.
When the mold drawing fully meets your and our requirements, the production of the mold will be initiated. Beforehand we have already looked at your budget and based on this we have made a choice for the suitable mold manufacturer, also called toolmaker.We have been working with the same Dutch and Asian toolmakers for many years, where it is possible to make molds from different types of steel. This way we can always guarantee excellent quality.
Have you head of NISSEI? NISSEI is an injection molding machine company based in Nagano, Japan; the mountain area famous ...
When the mold is ready for production, it is extensively tested on one of our injection molding machines by means of a trial injection. You then receive the first samples (First Out of Tool) along with a dimensional report. This allows us to ensure that the products meet the product drawing and your requirements. Regardless of where the mold is made, production always takes place at our facility in Boxtel!
Join Engel in exploring the future of battery molding technology. Discover advancements in thermoplastic composites for battery housings, innovative automation solutions and the latest in large-tonnage equipment designed for e-mobility — all with a focus on cost-efficient solutions. Agenda: Learn about cutting-edge thermoplastic composites for durable, sustainable and cost-efficient battery housings Explore advanced automation concepts for efficient and scalable production See the latest large-tonnage equipment and technology innovations for e-mobility solutions
This 1-day technical conference and exhibition showcases innovative developments in materials, processing and equipment for the additive manufacturing industry. This conference is specifically designed to inform, update and educate plastic processors about implementing new additive manufacturing technologies. Hear technical presentations on the newest advances in additive manufacturing related to: design, materials development, processing equipment and enabling technologies, new applications and more. See exhibits from engineering plastic suppliers, compounders, molders, design and engineering firms and machinery suppliers. Experts will show you how to apply the latest technologies to your next project or program. The conference includes a full day of technical presentations, plenary and keynote presentations on business trends; breakfast, lunch and breaks; exhibits of advanced technologies and an evening networking reception. Note: Additive Manufacturing Media executive editor Stephanie Hendrixson will moderate the Supporting AM Adoption in Northeast Ohio panel at 11:20 a.m.
An inspired combination of automation, ISO certification, use of certified resins, and strict adherence to a rigorous set of time-honed manufacturing standards are among the chief factors giving the Rodon Group, a 54-year-old custom molding operation in Hatfield, Pa., the confidence to boast that it can beat the pants off of Chinese part pricing, and Mexican pricing, too.And it’s not an idle boast.
Clear, amber or red; headlights, taillights and turn signals: those are just some of the constantly changing jobs that custom automotive molder TASUS pulls in and out of its presses, requiring a flexible drying system to handle the ever-changing run list.
If a better machine can help your company beat challenging economic conditions, you’ll probably find it at NPE. And finding it will be easier, thanks to our editors’ efforts to sift out of some 2000 exhibits the most significant news in injection and blow molding, extrusion, compounding, and thermoforming.
Liquid silicone rubber is breaking out of its niche into a broader array of applications, helped by new developments in materials, machinery, and processing. Larger parts, micro-parts, foams, and multi-color or multi-material combinations are key areas of innovation.
BlueHalo’s Intense Eye UAS has replaced a machined aerospace-grade aluminum chassis with one molded from Alpine Advanced Materials’ HX5 multi-scale reinforced polymer for a stronger, lighter craft.
Good news was there if you knew where to look for it—in the pages of Plastics Technology magazine or right here on our website. Here’s a review of headlines you can feel good about.
At Prism Plastics, quality is baked into every step of the process. The result: 1 billion parts per year with a defect rate less than 1 ppm.
In this collection of articles, two of the industry’s foremost authorities on screw design — Jim Frankand and Mark Spalding — offer their sage advice on screw design...what works, what doesn’t, and what to look for when things start going wrong.
Gifted with extraordinary technical know how and an authoritative yet plain English writing style, in this collection of articles Fattori offers his insights on a variety of molding-related topics that are bound to make your days on the production floor go a little bit better.
The Japanese maker of injection molding machines has merged its Californian-based sales subsidiary into its Texas machine-production site.
Nissei America, Inc. (US branch of Nissei Plastic Industrial Co. Ltd.) is an injection molding machine company headquartered in San Antonio, Texas. We offer a wide variety of injection molding machines, and our large machines are assembled here in San Antonio, Texas.
Learn about sustainable scrap reprocessing—this resource offers a deep dive into everything from granulator types and options, to service tips, videos and technical articles.
Stress-free production of large car windows, in-mold painting, and an injection unit that applies pack and hold while accumulating the next shot were a few of the cutting-edge technologies on display.
In this collection of content, we provide expert advice on welding from some of the leading authorities in the field, with tips on such matters as controls, as well as insights on how to solve common problems in welding.
Plastics Technology covers technical and business Information for Plastics Processors in Injection Molding, Extrusion, Blow Molding, Plastic Additives, Compounding, Plastic Materials, and Resin Pricing. About Us
In a time where sustainability is no longer just a buzzword, the food and beverage packaging industry is required to be at the forefront of this innovation. By adopting circular packaging processes and solutions, producers can meet regulatory requirements while also satisfying consumer demand and enhancing brand reputation. Join Husky to learn more about the broader implications of the circular economy — as well as how leading brands are leveraging this opportunity to reduce costs, increase design flexibility and boost product differentiation. Agenda: The cost and operational benefits of embracing circularity Key materials in circular packaging — including rPET and emerging bioplastics How to design a circular food and beverage package Strategies for selecting sustainable closures to future-proof packaging solutions Optimization and streamlining of production processes for enhanced efficiency How Husky Technologies can enable your sustainable success
3730 Global Way San Antonio, TX 78235 US 714-693-3000 info@nisseiamerica.com nisseiamerica.com
Formnext Chicago is an industrial additive manufacturing expo taking place April 8-10, 2025 at McCormick Place in Chicago, Illinois. Formnext Chicago is the second in a series of Formnext events in the U.S. being produced by Mesago Messe Frankfurt, AMT – The Association For Manufacturing Technology, and Gardner Business Media (our publisher).
Multi-shot and coinjection molding techniques are staking out new territory. Mach ines are getting larger and are combining more materials or colors in more sophisticated and imaginative ways.
“We love to tell our story.” That’s one way Mike Cartner, CFO of Currier Plastics, defines what separates this family-owned custom processor from its competitors.
“Every custom molder thinks he needs a proprietary product,” says John Currier, president and co-owner of the injection molding firm his father founded, Currier Plastics in upstate Auburn, N.Y.
Introduced by Zeiger and Spark Industries at the PTXPO, the nozzle is designed for maximum heat transfer and uniformity with a continuous taper for self cleaning.
Energy-saving all-electric machines will continue to be a big draw at NPE, where new designs or upgraded models will be found in virtually every press maker’s booth.
New injection machinery at the show ranged from all-electric units for high-speed packaging or bioplastic processing to hybrid presses ready for the cleanroom. Other units highlighted multi-component molding with LSR and thermoplastics or super-compact presses for small parts. Several new machines targeted specific applications such as caps and closures, PET preforms, LSR, or integrated long-glass compounding.
Allegheny Performance Plastics specializes in molding parts from high-temperature resins for demanding applications as part of its mission to take on jobs ‘no one else does.’
Ultradent's entry of its Umbrella cheek retractor took home the awards for Technical Sophistication and Achievement in Economics and Efficiency at PTXPO.
Join KraussMaffei for an insightful webinar designed for industry professionals, engineers and anyone interested in the manufacturing processes of PVC pipes. This session will provide a comprehensive understanding of the technology behind the production of high-quality PVC pipes: from raw material preparation to final product testing. Agenda: Introduction to PVC extrusion: overview of the basic principles of PVC pipe extrusion — including the process of melting and shaping PVC resin into pipe forms Equipment and machinery: detailed explanation of the key equipment involved — such as extruders, dies and cooling systems — and their roles in the extrusion process Process parameters: insight into the critical process parameters like temperature, pressure and cooling rates that influence the quality and consistency of the final PVC pipes Energy efficiency: examination of ways to save material and energy use when extruding PVC pipe products
technotrans says climate protection, energy efficiency and customization will be key discussion topics at PTXPO as it displays its protemp flow 6 ultrasonic eco and the teco cs 90t 9.1 TCUs.
Hundreds of tons of demonstration products will be created this week. Commercial Plastics Recycling is striving to recycle ALL of it.
While prices moved up for three of the five commodity resins, there was potential for a flat trajectory for the rest of the third quarter.
How small is small? How small is micro? How about parts weighing as little as 0.00012 g and measuring no more than 0.038 in. (1 mm) long?
The mold contains the shape of the part and is used in injection molding to inject the molten plastic. When the plastic then cures again, the product is ejected and the process repeats itself.
In this three-part collection, veteran molder and moldmaker Jim Fattori brings to bear his 40+ years of on-the-job experience and provides molders his “from the trenches” perspective on on the why, where and how of venting injection molds. Take the trial-and-error out of the molding venting process.
The company added all-electric Sumitomo (SHI) Demag, Niigata and Nissei molding machines to its Minnesota facility in support of medical device customers and other manufacturers.
Mixed in among thought leaders from leading suppliers to injection molders and mold makers at the 2023 Molding and MoldMaking conferences will be molders and toolmakers themselves.
After successfully introducing a combined conference for moldmakers and injection molders in 2022, Plastics Technology and MoldMaking Technology are once again joining forces for a tooling/molding two-for-one.
The October show in Dusseldorf saw an onslaught of new all-electric and hybrid-electric presses, with modular designs, new clamping styles, and new sizes available from an ever-growing range of suppliers.
Earlier this month, Nissei Plastic Industrial Co. Ltd. of Japan announced the official opening of its first U.S. assembly plant for injection molding machines in San Antonio, Texas.
For the first time since the largest Italian maker of injection molding machines joined with the Japanese firm, the joined companies will exhibit at a major show.
AIM Processing has parlayed small part molding expertise and aggressive automation, even for short run production, into a highly successful custom molding business.
Show goers will see an electric injection machine in nearly every press maker’s booth this year, and electric/hydraulic hybrids in several.
If you were buying an injection molding machine 20 years ago, you had to decide between a toggle or fully hydraulic clamp and that was pretty much it.
This CW Tech Days virtual event will explore the technologies, materials and strategies used by composites manufacturers working in the evolving space market. Presentations from industry experts will emphasize the use of composite materials in applications requiring the weight savings, structural benefits and ability to withstand extreme temperatures that only composites can provide.
Mold maintenance is critical, and with this collection of content we’ve bundled some of the very best advice we’ve published on repairing, maintaining, evaluating and even hanging molds on injection molding machines.
More than four years on, there are aspects of the COVID-19 pandemic that linger in their impacts to the plastics market and are made visible in our annual survey.
In many cases, decreasing the discharge temperature will improve product quality and perhaps even boost rate. Here are ways to do it.
I know I’m leaving myself wide open on this one. I was asked, “What are the 10 most interesting injection molding technologies of 2015?” I should have pleaded eggnog hangover and politely declined.
This Knowledge Center provides an overview of the considerations needed to understand the purchase, operation, and maintenance of a process cooling system.
Hot buttons at the show will be multi-component molding, in-mold labeling/decorating (IML/IMD), in-mold assembly, medical molding, liquid silicone rubber (LSR), micro-molding, and high-speed packaging.
Everything molders need to compete in markets from automotive to medical was on display in Orlando. Besides a huge number of new machine models, there was emphasis on cell integration and automation.
In this collection, which is part one of a series representing some of John’s finest work, we present you with five articles that we think you will refer to time and again as you look to solve problems, cut cycle times and improve the quality of the parts you mold.
It’s the power to run your plant and machines better and more profitably. Today’s process and production monitoring systems put that information in the palm of your hand.
For MDS Manufacturing, its first decade in business has been one of nearly constant change. But the two brothers who started it have never strayed from the company’s roots and the lessons about the molding business they learned from their father.
August 29-30 in Minneapolis all things injection molding and moldmaking will be happening at the Hyatt Regency — check out who’s speaking on what topics today.
When, how, what and why to automate — leading robotics suppliers and forward-thinking moldmakers will share their insights on automating manufacturing at collocated event.
During this process, a mold must be resistant to clamping forces as high as thousands of tons, for large parts such as crates. During injection, these pressures are released but heat is also generated from the molten plastic. Ideally, we also need the mold to withstand this more than 500,000 times!
The injection molder has added a 950-ton Nissei injection molding machine and a Zeiss O-Inspect 543 coordinate measuring machine (CMM) inspection system to its facility in Newton Falls, Ohio.
All-electric machines will be one of the biggest themes in injection molding machinery at this year’s K show, where at least nine firms will bring out their first models.
NPE2024: Nissei’s compact FWX Series combines a novel clamp design, low-pressure molding technology, and greater platen and tiebar spacing to enable large molds to run on lower tonnages.
It’s not easy being a custom injection molder in the NYC metro area. For Natech Plastics, the key is developing employees’ skills and commitment.
More speed, more power, more precision, and more automated functions accomplished in and out of the mold. That’s exactly what injection machinery suppliers were offering at NPE2012.
Second quarter started with price hikes in PE and the four volume engineering resins, but relatively stable pricing was largely expected by the quarter’s end.
Because of these requirements, mold construction is expensive and complex. A mold is made up of mostly separate components manufactured from a high-quality steel. Each component is precisely machined to a tolerance three times smaller than the thickness of a piece of copy paper. These components must then work together in the mold to create your plastic product.
Across all process types, sustainability was a big theme at NPE2024. But there was plenty to see in automation and artificial intelligence as well.
Mike Sepe has authored more than 25 ANTEC papers and more than 250 articles illustrating the importance of this interdisciplanary approach. In this collection, we present some of his best work during the years he has been contributing for Plastics Technology Magazine.
Sustainability continues to dominate new additives technology, but upping performance is also evident. Most of the new additives have been targeted to commodity resins and particularly polyolefins.
What are the basic building blocks of plastics and how do they affect the processing of that material and its potential applications in the real world? Meet the repeat unit.
If the product drawing meets the various requirements, a mold drawing will be prepared. The mold drawing takes into account all the basic components. Here you can think of the mold cavities, location and geometry of the injection, the partial seam of the mold on the product, the cooling channels, placement of the ejectors and other technical components.
At the heart of the injection molding process is the mold, or casting mold into which the heated plastic raw material is injected under high pressure. You can provide us with your own molds for injection molding, or our engineer can use CAD software to design a mold for your product.
Plastics Technology’s Tech Days is back! Every Tuesday in October, a series of five online presentations will be given by industry supplier around the following topics: Injection Molding — New Technologies, Efficiencies Film Extrusion — New Technologies, Efficiencies Upstream/Downstream Operations Injection Molding — Sustainability Extrusion — Compounding Coming out of NPE2024, PT identified a variety of topics, technologies and trends that are driving and shaping the evolution of plastic products manufacturing — from recycling/recyclability and energy optimization to AI-based process control and automation implementation. PT Tech Days is designed to provide a robust, curated, accessible platform through which plastics professionals can explore these trends, have direct access to subject-matter experts and develop strategies for applying solutions in their operations.
An overview on the use of chemical foaming agents (CFAs) to successfully foam single and multilayered rotational molding parts, this webinar will illustrate the multiple benefits rotational molders can achieve, including reducing resin consumption, decreasing part weight, enhancing wall thickness and improving structural rigidity. Agenda: Charging the mold Dosing ratios Venting Optimal decomposition temperatures, cycle times and drop times for drop box applications Cooling considerations
Join Wittmann for an engaging webinar on the transformative impact of manufacturing execution systems (MES) in the plastic injection molding industry. Discover how MES enhances production efficiency, quality control and real-time monitoring while also reducing downtime. It will explore the integration of MES with existing systems, emphasizing compliance and traceability for automotive and medical sectors. Learn about the latest advancements in IoT and AI technologies and how they drive innovation and continuous improvement in MES. Agenda: Overview of MES benefits What is MES? Definition, role and brief history Historical perspective and evolution Longevity and analytics Connectivity: importance, standards and integration Advantages of MES: efficiency, real-time data, traceability and cost savings Emerging technologies: IoT and AI in MES
Take a deep dive into all of the various aspects of part quoting to ensure you’ve got all the bases—as in costs—covered before preparing your customer’s quote for services.
Plastics Technology Top Shops Benchmarking Survey provided both unanimous responses and divided results, but pervasive throughout is the sense of an industry still grappling with the aftermath of 2020’s global pandemic.
Three, four, five and six axes; high speed and high payload capacities; low-cost models; and collaborative robots made news at K. There were also QMC systems and AGVs.
GETTING A QUOTE WITH LK-MOULD IS FREE AND SIMPLE.
FIND MORE OF OUR SERVICES:
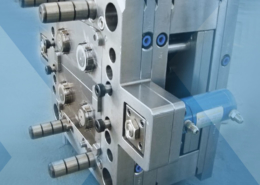
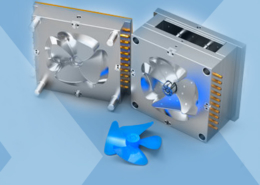
Plastic Molding

Rapid Prototyping
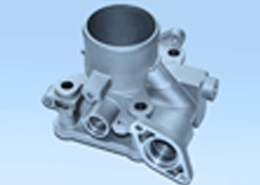
Pressure Die Casting
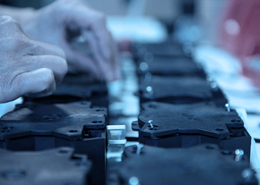
Parts Assembly
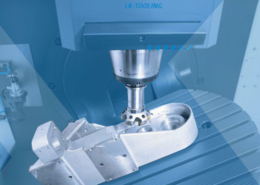