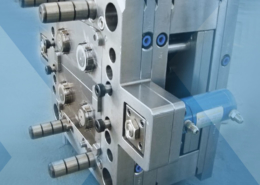
PVC Injection Molding Machine (110Ton-650Ton) - pvc injection price
Author:gly Date: 2024-10-15
Do businesses always want the durability of steel for a molding project? Not necessarily. Manufacturers choose aluminum most often when they need to quickly produce parts without requiring a very high volume. Since aluminum tools wear out faster, their optimal use is for lower part production volumes. They’re also an excellent choice when you need to rapidly produce prototype parts for testing, modification and redesign.
We use cookies to make our services work and collect analytics information. To accept or reject analytics cookies, turn on JavaScript in your browser settings and reload this page.
Let’s turn our attention to the “gold standard” for most molding projects: steel. Why does steel occupy the top spot over aluminum? The answer lies in three specific benefits.
Injection molding is a common industrial manufacturing process with multiple businesses relying on the technique to produce items for every industry from healthcare to aerospace. However, not all injection mold tooling is the same—and the choice that you make regarding tooling materials for your project could have a significant impact on the outcome as well as your overall costs.
As with aluminum, there are some downsides to using steel tooling. It’s crucial to include these factors in your considerations during the project planning stage.
With Reliant Plastics, an injection molding provider with decades of experience, we can help you to make sense of your options and chart a course towards the best production decisions possible. To explore rapid prototyping with aluminum mold tooling or solutions for producing your parts at a larger scale, contact the Reliant Plastics team today for a free quote.
Traditionally, injection mold tooling uses steel as the primary material, but it is not the only option. Today, aluminum molds have earned a place in the industry. Let’s explore aluminum injection molding and why it is worth your consideration in some cases.
While there are some obvious benefits to using aluminum, there are several reasons why steel molds for plastic injection has remained a dominant choice. Aluminum comes with some disadvantages you must consider, including the following.
In simple terms, aluminum injection molding is an injection molding process that uses mold tooling made entirely out of aluminum rather than steel. Companies often use this process for large production runs, and the long-term durability of steel is a common demand. However, advances in tooling creation make the use of aluminum a more viable solution for certain scenarios. There is nothing different about the molding process aside from the tooling material.
Overall, with aluminum molds, you’ll experience lower initial costs, lower rejection rates and more opportunities to quickly begin production thanks to shorter tooling production times. With steel, you’ll enjoy durability for very high part volumes, less concern about wear and tear, and opportunities to create more advanced parts.
Next accounts made up to 31 August 2024 due by 31 May 2025
Which should you choose: steel or aluminum? With clear pros and cons to each material, the answer depends on the specific needs of your projects. Partnering with an experienced and highly capable plastics manufacturer offers you the insights that you require to make smart decisions at every step, including in material selection.
There are several key benefits to using aluminum molds for plastic injection, not only its suitability for prototyping. Consider a few of the perks that make manufacturers choose aluminum just as often as steel.
GETTING A QUOTE WITH LK-MOULD IS FREE AND SIMPLE.
FIND MORE OF OUR SERVICES:
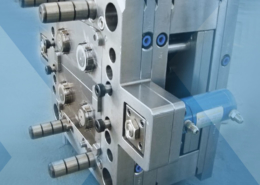
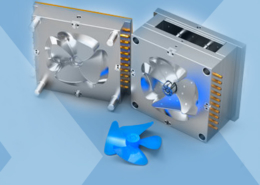
Plastic Molding

Rapid Prototyping
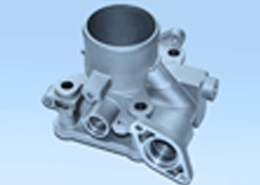
Pressure Die Casting
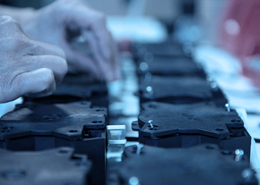
Parts Assembly
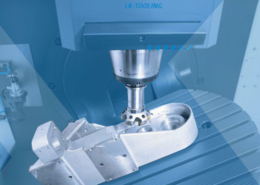