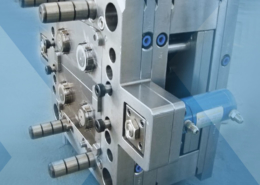
PTI Engineered Plastics Inc. | Plastic Molding Manufacturers - pti injection mol
Author:gly Date: 2024-10-15
When you get a quote, a DFM analysis is also given. Such analysis already identifies the nonmachinable parts, the draft angles, and other future problems due to the design.
During injection, the nozzle contacts the mold, and since mold temperature is generally lower than nozzle temperature, and the temperature difference is large, frequent contact cools the nozzle, freezing the melt at the nozzle.
When impurities in the melt block the nozzle or cold material blocks the gate and runner, clean the nozzle or enlarge the mold cold well and runner cross-section.
As to the manufacturing process, in-store injection molding companies can be more dependable. This is so since you have a physical store to check the phases of the manufacturing process.
A short shot refers to incomplete filling at the end of the material flow or incomplete filling in multi-cavity molds, especially in thin-walled areas or at the end of the flow path. It manifests as the melt solidifying before the cavity is fully filled, resulting in a shortage of material in the product.
If part thickness and length are disproportional, and the shape is complex with a large molding area, melt easily encounters flow resistance at the thin-wall entry, making cavity filling difficult. Design part shape considering the thickness and melt filling limit flow length.
The costs for the injected material depending on the type of materials themselves. This is quite the make or break for the entire computation since it depends on the quantity of the order.
With all the things that we have covered here, you might be wondering about some of the best injection molding companies out there.
For mold and injection molding factories, analyzing and perfectly resolving this short-shot problem is a fundamental skill. Every mold and injection molding practitioner has the responsibility and obligation to master all injection molding defects.
It is one thing that you know the type of costs that are covered in injection molding. But to have a more comprehensive view of the cost of injection molding, including how to reduce it and other handy information, here is an injection molding cost overview for your reference.
The common method to control feeding is volumetric feeding. Check whether the plastic particle size is uniform and if “bridging” occurs at the feed port. If the feed port temperature is too high, it will also hinder feeding. To address this, clear and cool the feed port.
Injection pressure is nearly proportional to the filling length. Low injection pressure shortens filling length and leaves the cavity unfilled. Address this by slowing injection speed, extending injection time, etc., to increase injection pressure.
The running and operations to manufacture detailed and custom injection molds make it all the pricier. Remember that molds always have two sides and it is the underside which really has those geometries and recesses.
Additionally, short holding time can also result in short shot. Control holding time within a suitable range, but note that excessive holding time can cause other faults. Adjust during molding based on the specific part.
Using raw materials with excessive moisture or volatile content will also produce large amounts of gas, leading to poor mold ventilation. In this case, dry the raw materials and remove volatiles.
If you are a start-up company, you need more expert heads to come up with a reliable design. Hence, for this matter, an online injection molding is the better choice because of the diversity of designs.
Generally, the cavity is that hollow or empty part of the injection mold or cast. The volume of the cavity in the mold means more pressing time.
If you want to know some of the best injection molding cost calculations online, with a full breakdown free quotation, here are the ones to check out:
This is connected with the manufacturing process and quality control. Time and again, you can be more at ease with in-store injection molding companies. You can visit anytime, demand as you deem fit, and have the designs modified at your own pace.
In multi-cavity molds, appearance defects often arise from unbalanced gate and runner designs. When designing the gating system, ensure gate balance and the weight of parts in each cavity should be proportional to the gate size, so that each cavity can be filled simultaneously. The gate should be positioned at the thick wall, and a balanced runner design can also be adopted. If the gate or runner is small, thin, and long, the pressure of the melt during flow will result in excessive pressure loss, leading to filling issues. To address this, enlarge the runner cross-section and gate area, and use multiple feeding points if necessary.
By considering the DFM analysis and employing the suggestions, you can lessen the design costs and future manufacturing costs.
As such, it adds to the price of the injection mold because interventions are incorporated in the machines to lessen pressing time for the cavities.
The main cause of short shots is excessive flow resistance, preventing the melt from continuing to flow. Factors affecting the flow length of the melt include part wall thickness, mold temperature, injection pressure, melt temperature, and material composition. Mishandling these factors can result in short shots.
Anent the first tip, it is best that you just focus on the basic yet necessary features of your injection mold design. If some of the features do not necessarily add market value, then it is best to just forego it.
As mentioned, the more detailed the design and the more geometrical it is, the pricier it gets. Custom injection molds take time and a lot of effort and consultation to be finalized.
If injection pressure can’t increase further, remedy by increasing material temperature, lowering melt viscosity, and improving melt flow performance. Note that excessive material temperature can cause melt thermal decomposition, affecting part performance.
When melt enters a low-temperature mold cavity, it cools too quickly, failing to fill all corners of the cavity. Preheat the mold to the process-required temperature before starting, and control the mold cooling water flow at startup. If mold temperature can’t rise, check if the mold cooling system design is reasonable.
If nozzle temperature is low and can’t rise, check if the nozzle heater is damaged and increase nozzle temperature accordingly. Otherwise, excessive pressure loss in the flow will also cause a short shot.
If you need injection mold calculations, quotations, or other information about injection molding, you can check out the injection molding products and services of Kemal Manufacturing.
If low-temperature injection is necessary to prevent melt decomposition, extend the injection cycle time to avoid short shots. For screw injection machines, increase the temperature in the front zone of the barrel.
Aside from this, the cost of having to use CNC, EDM, and 3D printers to aid injection molding for some projects also add up to the cost.
If the mold structure lacks a cold well, cold material entering the cavity solidifies immediately, preventing subsequent hot melt from filling the cavity. During mold opening, separate the nozzle from the mold, reducing mold temperature impact on the nozzle, and keep nozzle temperature within process requirements.
Instead of buying a new injection mold, why not design a mold which can be used multiple times. If there are excess molds from small parts, you can remold and reuse them for the same parts or re-machine such parts for other projects.
The most common materials are plastics and thermoplastics. Thermoplastic pellets on one hand costs $1-10 per kilogram depending on the grade. Higher-end plastics cost $7-20 per kilogram.
Note however, that this is not an exclusive list. There are other variables to consider and tips to employ in reducing the injection mold list. It is a good time to check other techniques that would reduce injection mold.
If the raw material formula has too much lubricant and the clearance between the injection screw check ring and the barrel is large, severe melt backflow in the barrel will result in insufficient feeding and a short shot. To address this, reduce lubricant usage and adjust the clearance between the barrel, injection screw, and check ring, as well as adjust the equipment.
The process of insert or overmolding basically involves placing the product in the injection mold and then further molding it in plastic. As such, you can both reuse the material and the mold itself for new mold products.
When raw material flowability is poor, the mold’s structural parameters affect short shots. Improve the gating system stagnation defect by reasonably positioning runners, enlarging gate, runner, and sprue sizes, and using a larger nozzle. Also, add appropriate additives to the raw material formula to improve resin flow performance.
Thus, if you are eyeing more cost-effective injection molding manufacturing, expect that Chinese companies would offer 35-50% less in cost compared to US injection molding companies.
For you to have a holistic view of what accounts for the total cost of injection molding, you need to know the type of costs in injection molding. Here are the most important injection molding costs which you must know of.
If a large amount of gas remains in the mold due to poor ventilation and is compressed by the material flow to a pressure greater than the injection pressure, it will hinder the melt from filling the cavity, causing a short shot. To address this, check if there are cold wells or if they are correctly positioned. For deep cavities, add vent grooves or vent holes at the short shot location; on the parting surface, create vent slots with a depth of 0.020.04 mm and a width of 510 mm, and position vent holes at the last filling point of the cavity.
Facing short shots in injection molding isn’t scary; what’s truly scary is when the factory doesn’t understand or can’t solve the issue. Familiarity with structural design, mold design, sample testing, problem analysis and resolution, appearance assurance, material characteristics, and more are essential skills for all injection molding practitioners.
If you want to cut cost in tooling, it is recommended that you use small injection molding machines especially for small to medium orders.
Having molds to reuse for other projects highly decreases operations cost. Aside from this, high-end injection molding companies would really recommend overmolding as a cost-effective approach to injection molding.
Knowing how an injection molding cost helps you in strategizing your operations if you are already using it in your manufacture or to make the change if you are thinking of switching to injection molding for your production.
The volume of production also dramatically raises the price of injection molding because in this phase, the different materials needed and the details are now all pressed. The larger the product bulk and the larger and more detailed the product bulk, the pricier the injection mold.
Given these, the average range for labor or service cost depends on the quantity of orders, the frequency of running, and the materials used for the injection mold.
What they do not know, however, is that injection modeling is way less costly when it comes to scaling, manufacture, and mass production in the long run.
As has been laid down, we can only lay down the average cost range of injection molding because it depends on various factors. To narrow them down, here are the most common variables which impact the cost of injection mold.
Non-experts in injection molding would tell you that CNC machining and 3D prototyping is more cost-efficient. Well, that is quite true, upfront.
Additionally, in mold system process operations, improve poor ventilation by increasing mold temperature, reducing injection speed, reducing gating system flow resistance, decreasing clamping force, and increasing mold clearance.
The core cavity approach has always been cost-efficient. In this process, the cavities are pressed down to the mold. Through this, surface finishes are smoothened and improves angles.
When selecting equipment, the maximum injection capacity of the injection machine must exceed 120% of the total weight of the part and the sprue, while the total injection weight should not exceed 85% of the machine’s plasticizing capacity.
The first thing which you can do is to simplify tooling designs. Limiting the complexity of molds shall lessen the costs because press time is lessened, tooling and equipment as well as labor costs are also lessened.
If you have already invested in in-demand small and large parts, it is best to consider on-demand production option. This allows you to control volatility of product demand and to equalize tooling costs.
At startup, barrel temperature is usually lower than the barrel heater gauge temperature. Ensure the barrel is heated to gauge temperature and then hold temperature for a while before starting.
As what is already covered in this post, there is no exact range for injection molding cost. Most if not all injection molding near you would compare their cost with Chinese and American injection molding companies.
https://jayconsystems.com/blog/2022/4/7/how-much-does-plastic-injection-molding-costhttps://www.protolabs.com/resources/design-tips/11-tips-to-reduce-injection-molding-costs/https://icomold.com/much-injection-molding-cost/https://makenica.com/in-house-and-outsourcing-in-injection-molding/https://www.protolabs.com/resources/design-tips/11-tips-to-reduce-injection-molding-costs/https://www.hubs.com/knowledge-base/how-much-does-injection-molding-cost/https://waykenrm.com/blogs/injection-molds-cost-in-plastic-prototyping/
Your house, your rule. Hence, you have a better rein on quality control and the pacing of the project if it is in-store. The internal quality control of in-store companies never misses.
Nonetheless, the final costing for the injected material depends on the final design of the injection mold, the material to be injected and the final choice of finish of the product.
Generally, within the appropriate molding range, the material temperature is nearly proportional to the filling length. Low-temperature melt flow performance decreases, shortening the filling length. If material temperature is below process requirements, check if the barrel heater is intact and raise the barrel temperature accordingly.
One thing to know about injection molding is that it is done automatedly. Nonetheless, for each stage, from start-up, to running, to cooling and removal, operations costs run up too.
If you are all for reducing injection molding costs, here are the tips which you should go for to reduce injection molding costs. Here are 11 injection molding design considerations to stretch your manufacturing dollar.
Aside from the faster lead time, you are also reducing operations cost because you are making more products without buying another one.
Note that online injection molding companies are shipped from somewhere or shall be freighted locally. If you are tight on budget and cannot spend more than the cut, just go for an in-store injection molding company.
It is always best to invest on high demand small and large sizes if you have already established a product pattern from your stable clients. List down the minimum and maximum part sizes so that you can have them made before getting bulk orders.
Mid-level orders consisting of at least 1,500 small parts can cost you at least $10,000 in tooling while customized and complex geometries can go for up to $100,000 in tooling costs.
Luckily, you can now create universal parts where you can design parts that would fit in any direction. With just one mold that can fit everything, you can lessen production costs in injection molding.
Shiny and glossy finishes are beautiful but they require a lot of tooling and handwork, hence, spiked up prices. If the finish and appearance are not that necessary or do not add up to the product value, then just dispense them altogether to reduce cost.
The first thing to consider is equipment costs. The computation for this relies on the type, size, and function of the equipment.
Tooling costs greatly depend on the size of the parts and the intricacy of the geometries incorporated. Other than this, EDM, CNC machining and 3D printing are also a part of the tooling cost.
Below is a table of common injection molding defects and their detailed channels, which interested friends are welcome to click on for in-depth understanding:
Bigger or mid-tier to large injection molding equipment on the other hand, have an equipment cost ranging from $50-000 – 100,000. Larger injection molding equipment costs up to $200,000.
Regardless, you must still understand that the variables cited, affecting the cost of injection molding, are of much consideration no matter where you get the injection molding.
One of the more observable determinants of cost would be the size of the parts. Of course, the larger the part size, the more sizable the cost too. Part size is also significant in costing especially for projects which include large, small, and custom molds.
There is no steady answer to this because there are various points to consider. In this section, an overview of the strengths and drawbacks of ordering from in-store injection molding companies and online injection molding companies are laid down.
Yes, we have already covered this beforehand. But you must know that this is pricey. Some of the variables which really spike up tooling prices are hinges, inserts, textures, and details.
Injection molding defects are issues that every injection molding factory may encounter during the molding process. Short shot defects in Injection Molding are a common injection molding defect. However, unlike flash defects, most short-shot defects are resolved before mold testing.
The following must be considered if you are wondering as to the labor or service costs when it comes to injection molding:
Injection speed directly affects filling speed. If injection speed is slow, melt fills slowly, and low-speed flowing melt easily cools, further reducing flow performance and causing a short shot.
If you have a bulk project, it is best that you categorize molds with the same sizes, cavities, and designs. By joining them in the same hinge, you can make lead time faster using multi-cavity or family molds.
GETTING A QUOTE WITH LK-MOULD IS FREE AND SIMPLE.
FIND MORE OF OUR SERVICES:
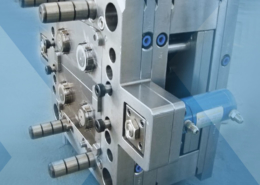
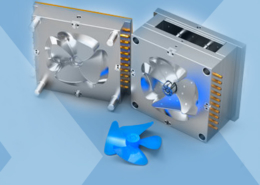
Plastic Molding

Rapid Prototyping
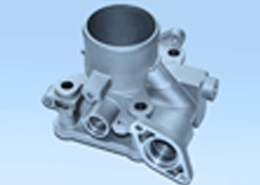
Pressure Die Casting
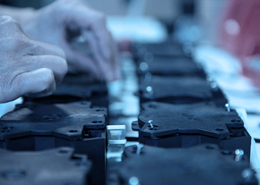
Parts Assembly
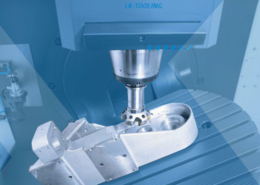