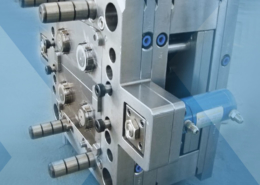
Prototyping Services with Injection Moulding - prototype plastic injection moldi
Author:gly Date: 2024-10-15
Techniques for polishing molds are crucial for making plastic molding tools. It greatly impacts the quality of the mold and the plastic component in addition to the mold itself.
Mold polishing is a method that involves several steps, starting with coarse polishing and moving toward increasingly fine polishing. More polishing procedures are necessary as the required finish level increases. As a result, every step is represented by its corresponding cost.
In procedures with high surface requirements, ultra-precision polishing methods are used. Abrasives are forced into the workpiece surface for high-speed rotation in this situation, together with special injection mold polishing tools. Ra 0.008 micrometer, the greatest value for polishing molds, is this technology’s surface roughness.
An approach that aids in obtaining smooth mold surfaces is plastic injection mold polishing. This is accomplished by cutting and deforming plastic to remove the convex portions of the mold. In most cases, manual polishing methods for molds employ sandpaper, wool wheels, and whetstone strips.
Want to learn more about injection molding? Sign up to receive a Design Cube. This physical aid demonstrates how to properly design features commonly found on molded parts.
In order to form a brush under the influence of the magnetic field, magnetic abrasive is used in magnetic polishing. With better processing efficiency, this technique grinds the workpiece. It is a straightforward procedure that produces high-caliber results. Surface roughness of roughly Ra 0.1 micrometer is achieved using the right abrasives.
Our digital factories create prototypes and low-volume parts fast, while our manufacturing network, offers advanced capabilities and volume pricing.
Get machined parts anodized and chromate plated with our quick-turn finishing option. Eligible materials include aluminum 6061/6082 and 7075.
There are a few crucial elements you need to think about before you attempt mold polishing. You can choose the best mold polishing method using this information. Major factors to take into account are
Nave ISK-8, Parque Industrial y Logístico Sky Plus, Avenida Mineral de Cinco Señores No.100, del Parque Industrial Santa Fe, Silao de la Victoria, Guanajuato, México
Proto Labs, Inc. 5540 Pioneer Creek Dr. Maple Plain, MN 55359 United States P: 877-479-3680 F: 763-479-2679 E: [email protected]
High polishing will be necessary for transparent injection molded items on both the cavity and core. Additionally, the price has increased as a result of this. According to some industry insiders, approximately 5% of the total mold cost goes into polishing the mold. For various injection molding businesses, this could be different.
Plastics that are strong and flexible can withstand unevenly polished surfaces. These substances consist of impact styrene, polypropylene, and ABS. Acrylics, however, are brittle and inflexible, and they cannot handle harsh finishes. For these types of materials, draw polishing is more advantageous. When choosing the perfect plastic material, you must be cautious enough to specify the appropriate mold finishing.
The primary method for polishing molds involves mechanically scraping away protruding (convex) elements from a workpiece’s surface to achieve a smooth one. Tools like oilstones, sandpaper, and wool wheels aid this laborious process.
The polishing of hard, fragile materials is accomplished using this method for plastic injection mold polishing. In this instance, the material is pretreated with the abrasive suspension before being exposed to an ultrasonic field. Ultrasonic waves are used by the suspension to hone and polish the workpiece’s surface. No workpiece deformation is a result of ultrasonic polishing because of its tiny macroscopic force.
The same principles that underlie chemical polishing also apply to electropolishing. To put it another way, it specifically dissolves the workpiece’s surface to provide a smooth finish. For even more notable effects, it does away with the cathode response influence.
The force required to draw the part out of the cavity and push it off the core will be less if the sidewalls of the part are drafted. There are situations, though, where the functional requirements for plastic parts do not account for draft angles. Smooth plastic injection mold polishing becomes increasingly crucial in these circumstances. Therefore It will be desirable to define the mold polishing specifications, especially for pieces that require little to no draft angles.
Additionally, manufacturers will employ super-precision polishing techniques when the material needs a high-quality surface finish. It is accomplished by applying solutions with abrasives firmly and quickly to the workpiece surface using specialized mold polishing equipment. As a result, this approach makes it possible to achieve a surface roughness of Ra 0.008 micrometers.
This method employs a flowing fluid containing abrasive particles to erode the workpiece surface. The hydrodynamic grinding process is assisted by hydraulics. Low pressure allows the polymeric component in the medium to flow. Frequently, silicon carbide powder makes up the abrasive particles.
One of the last actions conducted by a mold maker is polishing the cavities and cores of a new mold tooling. People frequently forget to do this step. However, mold polishing is an essential operation to improve the quality of molds, so it’s important to comprehend the mold polishing procedure. These mold polishing processes will be explained in this article. Additionally, you will discover the best methods for maximizing the benefits of the mold polishing procedure.
Material made of plastic contracts as it cools. The shrinkage draws those components out from the cavity to assist them in grabbing the core more firmly. In this situation, the plastic item needs to be ejected from the core using the highest demolding power. Mold ejection forces and cycle duration considerably rise if the inside surfaces are not polished smoothly. Injection molding draft angles and mold polishing go hand in hand frequently.
Glossier surfaces are typically produced with plastic polymers. For instance, no matter what the mold finish, polystyrene pieces look glossier than low-density polyethylene ones. In addition, several thermoplastic elastomers, soft polyvinyl chlorides, polyethylenes, as well as polyurethanes have the propensity to stick to highly polished surfaces. Mold polishing with a gentle blast will work for these materials.
The polishing of molds is an essential step in the production of plastics. Thus, accuracy is crucial. You can maximize the effectiveness of your plastic injection mold polishing procedures by using the following advice:
Products made of plastic for industry and commerce are currently getting better and more varied. As a result, it is up to producers to raise the caliber of molds. It is due to the direct role that molds have in determining the quality of a product. Plastic injection mold polishing became necessary as a result of this.
Surface finishing for polishing purposes is very different from surface finishing for other sectors. Mirror processing is a common name for this kind of polishing. It adheres to strict requirements for geometric precision, smoothness, and polishing.
Regarding the ultimate quality of injection molded items, a mold’s quality is essential. Polishing plastic injection molds is a great way to enhance the look of molded products and guarantee high-quality manufacturing. Thus, to maximize the benefits of your injection molding, apply the advice mentioned above. Prototool’s mission is to quickly transform your billion-dollar concepts into marketable, approachable solutions that are valuable to consumers. For all of your demands, you can find the greatest solutions. They will take extra measures to guarantee that your interaction with their services is straightforward and reliable.
Polystyrene is an amorphous thermoplastic that offers transparency and heat resistance. It's commonly used in medical applications, packaging and containers, and appliances. The resin is also food contact compliant.
Tough Black (Loctite Henkel 3843) and Ceramic-Filled (BASF 3280) are two new advanced photopolymer materials now available for 3D printing.
Additionally, the aesthetics of the finished product are enhanced by a smooth mold surface. The wear and corrosion resistance of the plastic surface is simultaneously enhanced. Effective plastic mold polishing processes typically result in shorter injection cycle times.
Our helpful design aid demonstrates part features that are too thin or too thick, bad bosses, right and wrong ribs, and other considerations to be mindful of while designing parts for injection molding.
Two main goals are typically the focus of mold polishing. The plastic material is firstly ejected quickly and smoothly. Molders can quickly and simply remove and demould plastic components because of the smooth surface finish of the mold. Consequently, you can be confident that the plastic will not adhere to the mold. You can stop injection molding problems from happening with this method.
GETTING A QUOTE WITH LK-MOULD IS FREE AND SIMPLE.
FIND MORE OF OUR SERVICES:
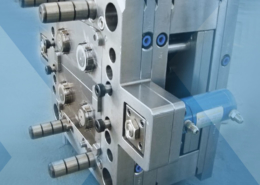
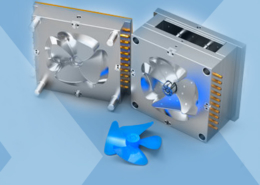
Plastic Molding

Rapid Prototyping
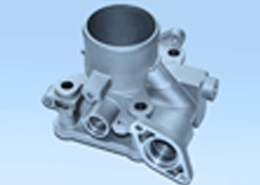
Pressure Die Casting
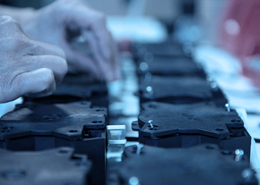
Parts Assembly
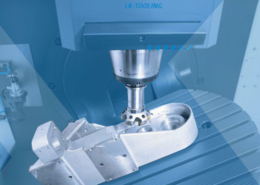